MBD・AI・部品共通化…自動車部品サプライヤーが製品開発に新手法
自動車部品サプライヤーが新たな製品開発手法の採用を急いでいる。電気自動車(EV)やコネクテッドカー(つながる車)の普及拡大が見込まれ、高機能と環境性能の両立が求められる中、開発期間短縮やコスト低減を実現しながら、効率的に製品化に結びつける狙いだ。「部品共通化」「人工知能(AI)」「モデルベース開発(MBD)」「ベンチマーキング」の四つのテーマで部品各社の取り組みを追った。(名古屋・増田晴香)
部品共通化 期間短縮、コストダウン
ブリヂストンは部品共通化を積極化する。タイヤを構成するカーカス(骨組み)とベルト(補強帯)を異なる商品間で共通化する。一方、タイヤの表面であるトレッド部分は各商品で切り替えて性能を差別化する。この技術を「ブリヂストン・コモナリティ・モジュラリティ・アーキテクチャ(BCMA)」と呼称し取り組みを推進する。モジュールを共用する設計により開発期間を短縮し、コストを低減する狙いだ。
多様化する顧客ニーズに応じた製品をアジャイル(機敏)に開発できる体制を構築し“究極のカスタマイズ”を実現する。モジュール化によって開発だけでなく生産工程での段取り替えを削減できるため生産も効率化できる。2024―26年の中期事業計画期間内にBCMAの効果を見える化し、実際にコストダウンにつなげる狙い。国内の拠点では現在扱っている30―40商品を最終的には5モジュールに集約する。
同じ工場に生産難易度が高い製品とシンプルな製品が混在しているとうまくモジュール化の効果を発揮できない。まずは「生産品目の見直しなど各工場の役割を明確化し、生産計画とも連動したBCMAを展開する」(石橋秀一最高経営責任者〈CEO〉)。
シートメーカーのタチエスも同様の取り組みを推進する。フレーム構造を共通化し、開発や設備導入、生産準備、購入部品における効率化でコスト低減を図っている。開発ではそれぞれフロントフレーム、リアフレームで同一設計を採用し、地域個別開発を廃止する方向。さらに共通フレームに搭載されているコア部品である機構部品、電装部品の現地化を推進し、競争力を向上する。
同社は21―24年度の中期経営計画における重点活動として「モノづくり競争力の強化」を掲げている。フレーム構造の共通化や内製化、部品現地化、購入部品合理化など開発や製造でのコスト低減を進め、24年度には営業利益で55億円の押し上げ効果を創出したい考え。
A I 大量データと連携・進化
住友ゴム工業はスーパーコンピューターで材料シミュレーションを行う「アドバンスド4Dナノデザイン」や、タイヤの性能持続技術開発を加速させる「タイヤリープAIアナリシス」などの技術で開発を高度化してきた。現在はそれらに加え、タイヤのライフサイクル全体から収集したデータを開発に生かす取り組みを進めている。原材料のデータやタイヤの使用データといったライフサイクルを通して収集したビッグデータ(大量データ)を連携させ、シミュレーションやAI技術をさらに進化させる。
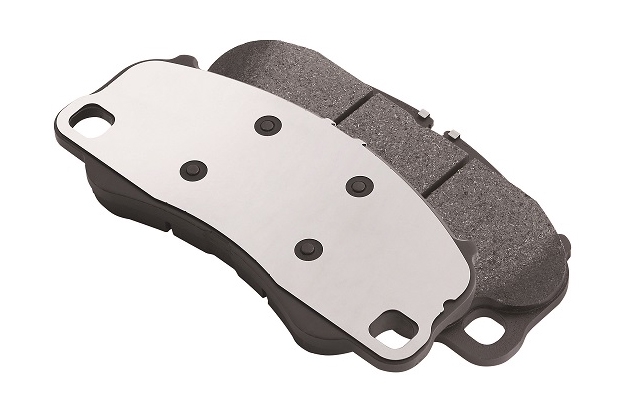
横浜ゴムは独自のAI利活用プラットフォーム「ハイコラボ」を展開。人が設定する仮説に沿ってデータを生成・収集し、AIにより予測・分析・探索する。人間のひらめきや発想力とAIの処理能力を組み合わせ、AIが苦手とするデータの存在しない領域も含めた知見の探索も可能にする。
曙ブレーキ工業は、AIを応用した新たな材料開発手法を検証している。試作や評価を減らし、新材料の開発リードタイム短縮を目指す。同社は18年ごろからAI活用に着手しており、これまでは過去に使ったことがある原材料について、配合や組み合わせを変え、改良を行う場合の摩擦材の性能予測を行ってきた。
さらに情報科学を用いて材料開発を効率化するマテリアルズ・インフォマティクス(MI)の手法を適用する。MIは製薬分野などでの導入が先行してきたが、近年は材料分野でも広まっている。過去に得られたデータを学習するだけでなく、未学習の原材料に関しては粒径や硬度などの情報を入れることで、それを配合した摩擦材の性能予測ができるようになる。また、目標性能を満たす材料を効率的に探索できる。
M B D 業界底上げ、中小に普及促進
コンピューター上のシミュレーションモデルを軸に開発を行う手法「MBD」は自動車メーカーや1次サプライヤー(ティア1)にとって必須になりつつある。
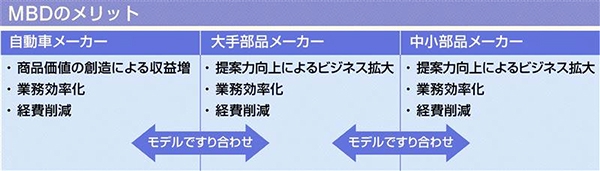
MBDではサプライヤーの部品の設計開発から、自動車メーカーの車両・システム開発までを一貫してシミュレーションモデルでやりとりし、開発の初期段階からデジタルですり合わせることが可能。実機テストや試作を削減でき、低コストで手戻りの少ない高効率な開発ができる。
10年ほど前からMBDを製品設計に導入している日本ピストンリングの高橋輝夫社長は「先行開発で実際にエンジンを回してテストする回数は減っており、開発期間も短縮している」という。
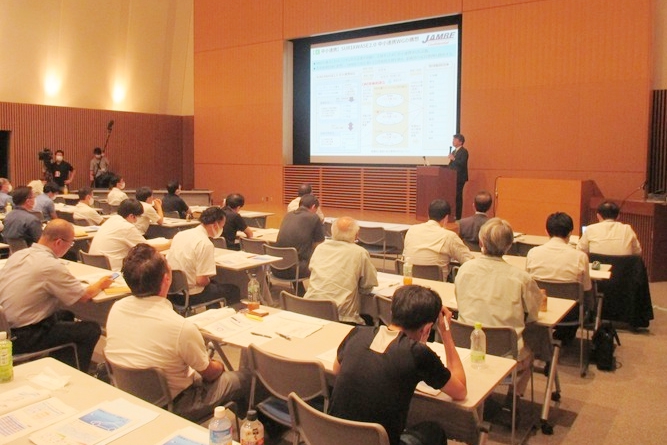
自動車業界全体の国際競争力を底上げするため、将来的には中堅・中小も含めたサプライチェーン(供給網)全体の開発最適化が理想だ。
自動車メーカーなどが運営する組織「MBD推進センター」は4月に一般社団法人化し、普及活動を拡大している。23年度は主に地域の産業振興団体との連携を強化し、中小企業へのセミナーや相談会などを実施している。
企画統括委員会の足立智彦委員長(マツダ技監)は「導入にはコストもかかる。まずは重要性を理解してもらうため成功事例を紹介し周知を図る」と話す。MBDはマツダが業界に先駆けて導入していたことから、広島県が先行して中小の育成に取り組んできた。広島の事例を全国の各地域に横展開する。
ベンチマーキング 調査委託拡大、高度・迅速化
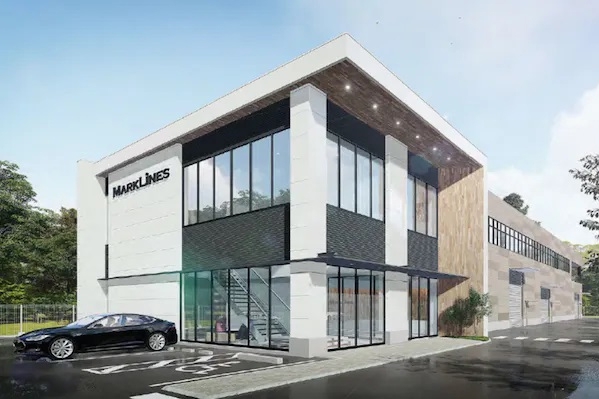
電動車をめぐる競争が激しくなる中、先行する米国や中国の新興メーカーなどの車両や部品を分解・分析する「ベンチマーキング」を実施して情報を得て、開発スピードを上げる取り組みの重要度が増している。従来、自動車メーカーは自社でベンチマーキング活動をしてきたが、近年は人材の不足や労力の大きさもあり、独立系企業に委託する例が増えている。受託企業は分解調査データやCADデータ、コスト分析データなどを提供し、次世代車の開発を後押しする。
マークラインズは24年にベンチマーキングの新たな専用施設を神奈川県厚木市に開設する。海外製EVの分解や計測、CADデータ取得などが新施設で可能になる。
これまで同社は国内外のエンジニアリング会社が作成した分析調査データの販売を行ってきた。加えて近年はEVのコア部品を分解して自社で得たデータの販売も拡大している。一連のベンチマーキング支援で開発の高度化や迅速化を下支えする。
【関連記事】 デンソーも注目、岐阜の「改革マスター」とは?