自動車エンジン部品、金属表面に特殊加工で摩擦エネ損失35%減
東京都市大など実証。ピストンリングなどの他の部品にも適用
東京都市大学や東北大学、九州大学など10大学の研究グループは、ピストンなど自動車のエンジン部品に摩擦を少なくする技術を適用し、摩擦で生じるエネルギー損失を35%減らせることを実証した。金属表面への特殊な加工技術などを利用した。早ければ4月にも乗用車用エンジンの実証実験を始める予定で、エンジン全体で摩擦損失を半分にすることを目指し、投入したエネルギーを動力に変換する効率「熱効率」を向上させる。
今後、ピストンリングなどの他の部品にも低摩耗技術を適用する。研究グループの責任者である東京都市大の三原雄司教授は、「エンジン全体で摩擦損失を半減できれば、自動車全体の熱効率を2%程度押し上げられるのではないか」と期待する。
摩擦低減技術の一つとして、名城大学が開発した金属表面への特殊な加工技術を適用した。エンジンのピストン表面が薄い潤滑剤の膜で覆われるように加工してある。部品同士が直接接触した場合の摩擦を減らした。
近年、部品の動きを良くするための潤滑油の粘度を下げ、摩擦を減らす試みがなされている。だが粘度が低い潤滑油では部品同士の接触部分から潤滑油が逃げる場合があり、そのため部品同士がこすれ、かえって摩擦が大きくなることがあった。
今後、ピストンリングなどの他の部品にも低摩耗技術を適用する。研究グループの責任者である東京都市大の三原雄司教授は、「エンジン全体で摩擦損失を半減できれば、自動車全体の熱効率を2%程度押し上げられるのではないか」と期待する。
摩擦低減技術の一つとして、名城大学が開発した金属表面への特殊な加工技術を適用した。エンジンのピストン表面が薄い潤滑剤の膜で覆われるように加工してある。部品同士が直接接触した場合の摩擦を減らした。
近年、部品の動きを良くするための潤滑油の粘度を下げ、摩擦を減らす試みがなされている。だが粘度が低い潤滑油では部品同士の接触部分から潤滑油が逃げる場合があり、そのため部品同士がこすれ、かえって摩擦が大きくなることがあった。
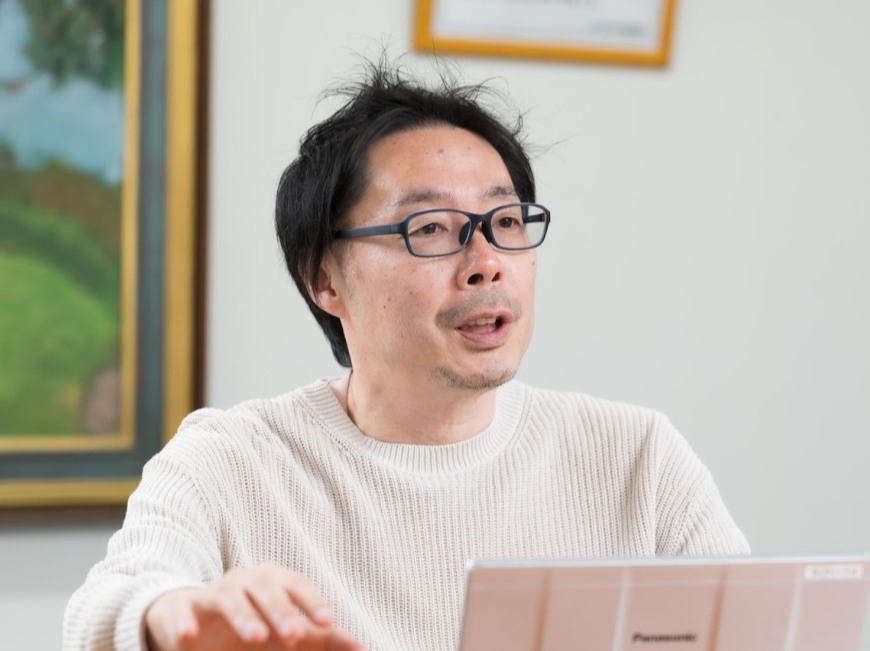