ユーザー視点で使いやすい製品を開発し微細加工の進化を支える
小物・精密部品向け微細加工機の分野で業界を牽引する碌々スマートテクノロジー(旧・碌々産業)。1996 年に微細加工機「MEGA」を発表して以来、「Android」や「Vision」など市場の要望に合わせてラインナップを拡大してきた。近年は、「微細加工はオペレータがいてこそ成立する」との考えから、オペレータを支援する機能の開発に注力。ワークの自動交換や追加工の自動化など、人手の足りない現場をサポートするシステムも充実させている。今年創立120 周年を迎えた同社は、10 月1 日に社名を碌々スマートテクノロジーへ変更した。ユーザーの課題解決につながる提案をこれまで以上に強化していく中で、どのような製品開発を目指すのか。設計を担当する3 人に話を聞いた。
御社が微細加工機の分野に参入した経緯を教えてください
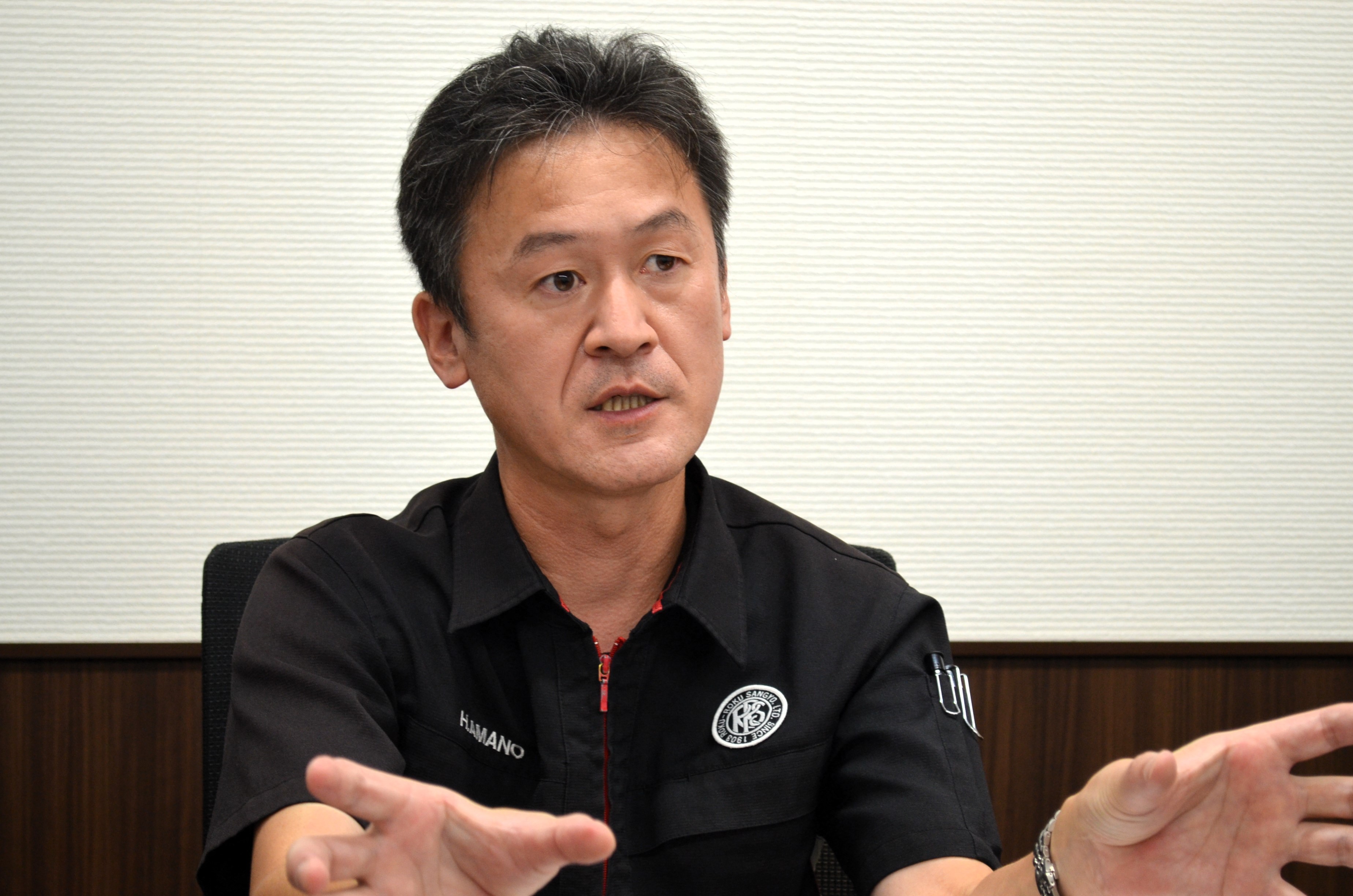
天野 1996 年のJIMTOF でMEGA-360 を発表、そしてリリースしたのが当社の微細加工機の始まりです。それ以前は、太くて高剛性なBT40 番のシャンクでバリバリ鉄を削るようなマシニングセンタ(MC)をつくっていたのですが、競合が多く、 大手との販売競争が厳しかったこともあり打開策が必要でした。そこで目を付けたのが微細加工分野です。当時、MC と並ぶ主力製品だったプリント配線基板向けの穴あけ機や外形加工機を手掛ける中で、電子機器分野が伸びていくとわかってい ました。コンピュータやモバイルフォンが小型化し、金型や部品が小さくなることも予見できた。この分野で新たな市場を切り開こうと微細加工機を開発したのです。
それまで手掛けていたMC とはかなり違っていた?
天野 ええ。部品が微細化するのに伴い、工具の小径化が予想されました。小径工具で加工するには周速を速めないといけない。そこで、MEGA-360 では主軸を36,000 回転にしました。当時手掛けていたMC が8,000~12,000 回転程度だったので一気に3 倍に速めたことになります。また、テーブルを動かすガイドレールには、当時主流だった滑りガイドに代わり、転がりガイドを採用し、ま たボールねじはショートリードを採用して位置決め精度を高めました。現在当社の代名詞となっている門型の機械構造や箱型ベッドもMEGA-360で初採用しています。いろいろな面で大胆にチャレンジした機械だったと言えるでしょう。
それらの要素技術は96 年以前から蓄積していたのですか
天野 転がりガイドは、MEGA-360 以前のMCやボール盤でもすでに採用実績がありました。位置決め精度の向上には低摩擦化が重要で、滑りガイドよりも転がりガイドの方が優れていると考えていたからです。また、プリント配線基板用穴あけ機はエアースピンドルを120,000 回で回転させていたので、「速く回転させるために、どんな設計をすればいいのか」の知見もありました。
主軸の振れ抑制を重視
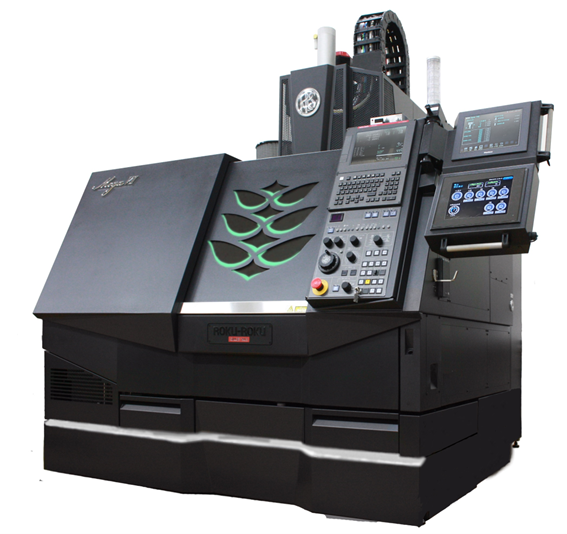
御社の微細加工機で使える最小の工具径は?
天野 ドリルならφ0.01mm(=10μm) です。ただ、中にはφ5μm での穴あけ加工に挑戦しているユーザーもいるようです。
加工精度を高めるために、微細加工機の設計では何を重視していますか
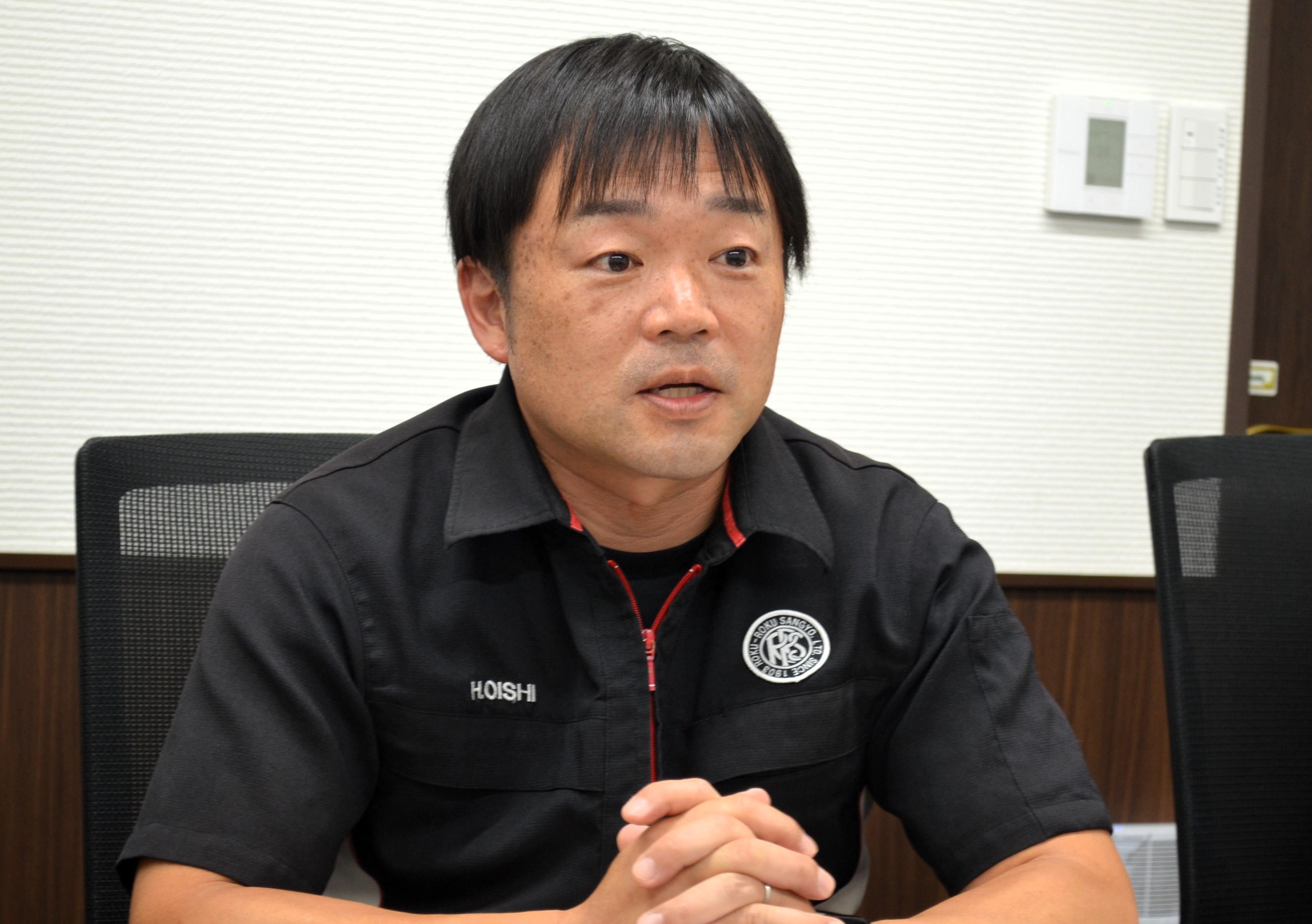
大石 3 つあります。1 つ目は主軸の振れをなくすことです。たとえば、φ0.05mm のボールエンドミルの加工では、数μm レベルの微小な切込み量が必要とされますが、主軸が振れていると、 工具設計から理想とされる微小な切込みができません。2 つ目は駆動軸をいかに指令通りに、つまりプログラム通りに動かすか。指令通りに動かないと加工形状に大きく影響するばかりでなく、工 具の寿命低下や折損につながります。3 つ目は熱変位対策です。主軸やサーボモータ、リニアモータから発生する熱が機械に伝わると、機械が姿勢変形を起こして主軸の位置が変わってしまいます。これも切込み量の変化や加工誤差を生じさせる原因になります。この3 つに加えて、「精度と生産性の両立」も常に心がけています。ナノマシンと呼ばれる研究用途のMC と違い、微細加工機には生産性も求められるからです。
量産現場で使える機械を目指しているのですね。現在の製品ラインナップを教えてください
大石 当社のラインナップはMEGA を基準に考えていただけるとよくわかります。まず、2022年のJIMTOFで発表したMEGAの7代目「MEGA-Ⅶ」があり、これを微細加工機のエントリーモデルと位置付けています。次にMEGA-Ⅶと同じ加工エリアをもち、より高精度を目指した機種が2つ。ボールねじ駆動のMEGA-Ⅶに対し、リニアモータ駆動で精度を高めた「AndroidⅡ」、そしてリニアモータ駆動に加えて油静圧案内面を採用した「P12-C genesis」です。
一方、MEGA-Ⅶと同じボールねじ駆動で、加工エリアを広げたのが「CEGA-SSS」です。軸移動量はMEGA-Ⅶの410×330×200mm に対し、510×410×310mmとなっています。そしてCEGA-SSSよりもやや大きな650×550×300mmの軸移動量をもち、AndroidⅡと同じリニアモータ駆動を採用したのが「Vision」です。MEGA-Ⅶを中心に5機種を揃えることで、お客様のニーズに応えています。
これらの微細加工機の中で転換点になった機種はありますか
天野 リニアモータを搭載した微細加工機としてユーザーに受け入れられたという意味で、Androidが転換点だったと思います。実はAndroidを発売する10年ほど前にも、リニアモータ駆動の機械をリリースしたことがあったのですが、MEGAよりも加工範囲が狭く、リニアモータに対する信頼性もまだ低かったため受け入れられませんでした。一方、それからしばらく経つとボールねじ駆動の機械の耐久性が問われるようになり、金型分野でリニアモータ駆動への需要が高まります。そこにジャストフィットする形で2010年にAndroid、2015年にAndroidⅡをリリースしたことで、金型分野のユーザーにも使っていただけるようになりました。特殊な転がりガイドを採用したため、適した工具、適した加工パスを選べば、エンドミル加工でも研削加工に近い鏡面が得られるようになったという面でも重要な機種だったと言えます。
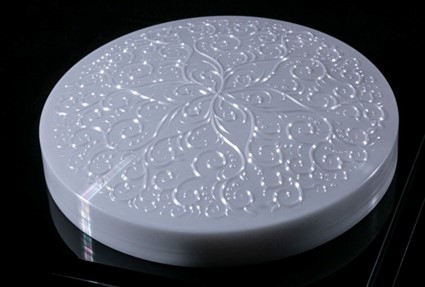
Visionは荒加工から微細加工までを1台に集約したいというユーザーの声で開発したと聞いています。最近はどんなニーズが強まっていますか
里中 自動化のニーズが増えてきたと感じます。当社は10年以上前から自動ホルダ交換システム(AHC)を提供していますが、最近はオプションでAHCを組み込むユーザーが目立つようになりました。もとは形彫り放電加工用の電極の加工で主に使われていたもので、最近は金型部品や医療機器部品などにも広がっています。
AHCとはどのようなものですか
里中 ワークをセットしたホルダごとワーク交換ができる、長時間の無人運転をサポートするシステムです。あらかじめ複数のホルダにワークをセットし、スケジュールを組んでおけば、24時間、無人で加工とワーク交換を繰り返します。位置決めのためのチャックはエロワ社とシステム 3R 社の製品に対応し、交換精度は実測値で±1μmです。作業者の足りない現場で重宝されています。
天野 半面、人が介入しないので、加工現場の温度環境を最初にきちんと整えることが重要になります。工具も適切なタイミングで交換しないと、加工が進むにつれて不良発生のリスクが高まるので、あらかじめ工具寿命のデータを集めておくなど事前の準備が必要です。
新OSでオペレータを支援
微細加工を実現するにはオペレータの能力も重要です。オペレータの能力向上や気づきにつながる機能にはどのようなものがありますか
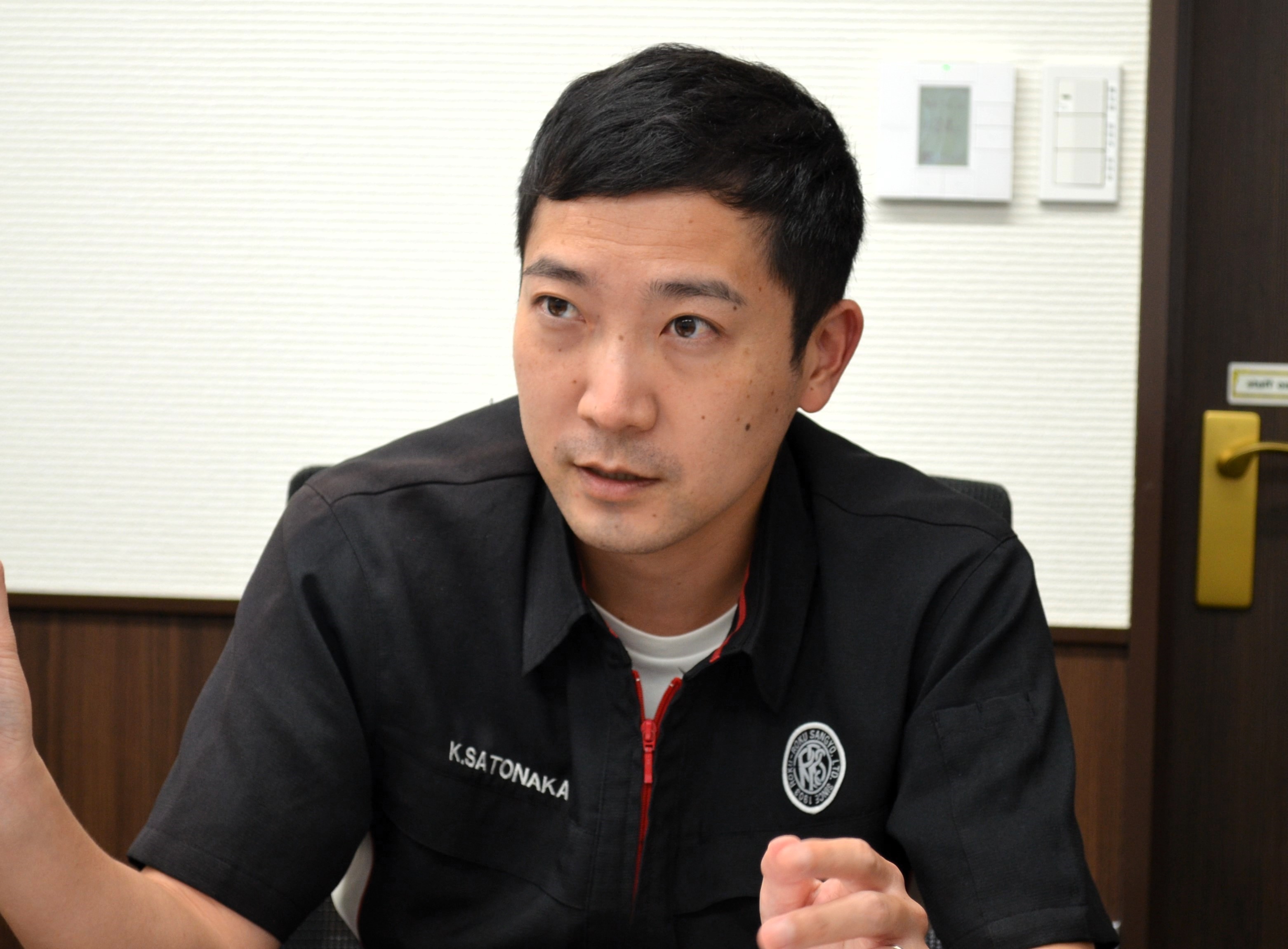
里中 代表例を2つ挙げます。1つ目は「MA-OS1(マシニングアーティスト・オペレーティングシステム)」です。従来のOSでも、CNCメーカーが提供する標準的な画面とは別に、自動心出し機能や機上工具測定機能のためのカスタマイズ画面がありましたが、文字や数値が並んでいるだけの簡素なものでした。それに対して、アニメーションを加えたグラフィカルな画面にして、直感的に操作しやすく、必要な情報を一目でわかるように開発したのがMA-OS1です。
マルチ画面を採用した点も特徴です。他メーカーが大きなメインモニタに情報を集約しているのに対し、メインモニタの横にサブモニタを配置し、サブモニタに当社のカスタマイズ画面を表示することで画面の切替えに伴うオペレータのストレスを軽減しました。MA-OS1はMEGA-ⅦとCEGA-SSSに標準搭載されており、2024年1月からAndroidⅡやVisionにも展開予定です。
もう1つの機能は?
里中 「見える化」のための「M-kit」です。「究極の加工精度を実現するための重要なポイントの1 つは、オペレータが機械情報を事前に掴むこと」との考えで開発しました。室温や主軸の温度、サーボモータ温度やテーブル温度、エアー消費量などのデータを集め、サブモニタの下にある専用モニタに表示します。これらの情報を把握することで、オペレータは必要な補正をかけることができます。データを蓄積する機能もあるので、トラブルが起きたときの状況を後から確認することも可能です。またM-kit で得た主軸温度データと機上工具測定機能を利用することで、機械の熱サチレートの判断が可能となります。主軸温度の変化と主軸の伸びの測定結果を踏まえて暖機運転の終了を自動で判断できれば、オペレータが機械の前に張り付いている必要がありません。オペレータに機械の状況を知らせるだけでなく、作業負担の軽減にもつながるのです。
縦割り廃し顧客の声を取り込む
これまでさまざまな市場の変化に対応してきた御社ですが、10 年後はどんな工作機械が求められると思いますか
大石 やはり、自動化、無人化が求められるのではないかと思います。一方、「微細加工はオペレータがいてこそ成立する」が当社のスタンスです。どうやってオペレータをサポートするかを考えたとき、「使う側の視点に立って設計する」ことが重要になります。当社には、お客様のニーズを最もよく把握している営業担当者がいて、NCプログラムの作成や工具の選定など微細加工機の使い方をサポートする営業技術部隊、長年使った機械を修理するサービス部隊もいる。彼らがもっているお客様視点の情報にわれわれ設計部隊が真摯に向き合い、製品開発に活かしていくことが大切です。
天野 他部門が把握しているお客様のニーズを汲み取ると言うと簡単に聞こえますが、それを実行できている会社は少ないのではないでしょうか。会社はどうしても部門で区切られていますし、10個あるニーズのうち、2、3個だけを聞き入れて、ほかは聞き流していたりする。だからこそ、本当の意味で社内の風通しを良くして、細かなニーズを汲み取っていくことが、当社のような中小企業の生き残り戦略になるはずです。
10月1日に社名が碌々スマートテクノロジーに変わりました。新社名の下でどんな製品開発を目指しますか
天野 微細加工機を開発した当初は、適した機械をつくりさえすれば微細加工ができるようになると考えていました。でも、違いました。工具やCAM、機械の設置環境まで丸ごとサポートしないと、顧客の現場で微細加工を提供できないとわかってきたのです。そこで、2020年のOnline JIMTOFでは加工と自動洗浄、機上計測、CADデータとの比較、差分の追い込み加工を自動でできるシステム「COSMOS」を発表し、2022年のJIMTOFにおいては、実際のワークを展示しながら「COSMOS」システムの具体的な提案をしました。こうした微細加工機のみならず総合的な取組みが新社名の“スマートテクノロジー”につながっています。
今回、会社のスローガンも「微細加工機のリーディングカンパニーへ」から「微細加工のソリューションカンパニーへ」と変えました。あえて「機」を除いたことで、微細加工機はもとより、ソフト、周辺機器を含めて総合的のお客様の困りごとに対応していく姿勢を鮮明にした。製品開発でも、総合的なシステムづくりを加速させていきます。