売却も噂されるGEの鉄道事業、工場はデジタル化で生まれ変わっていた!
収益性は高いが、機関車は中長期の成長性に…
機関車を手がけているGEトランスポーテーションの工場でスーパーバイザーを務めるダスティン・カストル氏は、先日、長年勤務する作業員たちに彼らの業務がロボットに代替されようとしていることを伝えた。少なくとも、作業員たちはそうとだけ告げられたと思っていた。
カストル氏はペンシルバニア州グローブシティにあるGEトランスポーテーションの工場に勤めるようになってまだ2年しか経っていなかったのに、昨年、何十年もこの組立ラインで働いてきた作業員たちに、業務手法が劇的に変わろうとしていることを伝える必要があった。
重さ4万ポンド(約18トン)の機関車のディーゼル・エンジンのボルトを正確な強度で締める際には、全長3フィート(約0.9m)の油圧トルクレンチを作動させる反復的なプロセスが必要。しかしカストル氏は作業員たちに「今後はそんな複雑な定石に基づく手作業は必要なくなるんだ」と説明した。
今後、こうした作業はロボットが代替し、作業員はその進捗を監視するようになる。「僕がそう伝えたとき、現場からは“このやり方を20年も続けてきたし、作業方法は熟知している!”という反論が噴出した」とカストル氏。
敷地面積240,000平方フィート(約22,297m²)、400人近い社員を抱える工場の未来にとって、この変革は重要な意味をもつことをカストル氏は認識してした。
それはこの工場を「ブリリアント」ファクトリーにするというGEの決断の重要な側面でもあった。GEのブリリアント・ファクトリーは、より効果的に業務を遂行できるよう、リーン手法とソフトウェア、センサー、リアルタイムデータなどのデジタルソリューションを活用している。
GEは新設工場、既設工場を含め、世界に7つの工場拠点を「ブリリアント・ファクトリー」にすることを決め、2015年2月、その第1弾をインドのプネーにオープンさせた。
この7拠点には、カストル氏が管理するグローブシティの工場、そして東京都日野市にあるGEヘルスケア・ジャパンの工場も含まる。今では、世界中に広がるさらに多くの工場で「ブリリアント・マニュファチャリング」の考え方が取り入れられるようになった。
カストル氏がこの動きを歓迎したのは、こうした変革によって工場はコスト競争力を維持し、長期的存続が可能になることを知っていたからだ。
GEは最近、グローブシティの事業に1億5,000万ドルを超える投資を行った。これには新しいエンジンを組み立てるための2つ目の工場建設も含まれている。
「ここはGEが成功させたいと願っている場所なんだと認識できて、雇用が保障されていると実感できる」(カストロ氏)。それでもやはり、作業員たちはしばしばオートメーション化に不安を抱いていることに、彼は気付いた。
新たなシステムに適合できないと思い込んでいる者もいれば、仕事量が減って全員に行きわたらないのではないかと心配する者もいる。
しかし、オートメーション化は一部の業務を減らす一方で、他の業務のニーズを増やしてもいる。実際、1982年~2012年の米国の労働人口に関するある調査によると、コンピューターに依拠する割合が高い業務分野の方が、雇用増加のスピードははるかに速いという結果も示されている。
作業員たちの不安を和らげるため、カストルはそれぞれの生産ライン・チームのミーティングに頻繁に参加し、工場デジタル化が進むことによって日常業務がどう変わっていくのかを作業員たちに説明した。
ボルトのトルク作業の自動化は、ケガを減らしながらも精度を高めることができること。「ブリリアント」ファクトリーのプロセスは業務を減らすために設計されているわけではなく、工場の効率や柔軟性を向上させるためのものであって、製品のさらなる多様化を図れること。
「作業員の中にはそれでも昔ながらのやり方に固執する者もいた」ものの、大部分のメンバーは「これによって誰もがもっとスマートに働けるようになる、ということをしっかり理解してくれた」とカストロは話す。
工場のオペレーションがデジタル化される以前は、作業員が不具合を起こしたすべてのエンジンを完全に分解し、組み立て直していた。
今では、各機関車に設置された何百個ものセンサーからエンジンの健康状態を仔細に把握できるようになったので、エンジンを再発送するまでに、簡単な修理だけで済むような場合もある。
2014年からグローブシティの工場で働いているジェイミー・モイヤー氏は、追跡しやすいようにエンジン部品にバーコードを刻むチームに所属している。
「覚えるまでに少し時間はかかったけど、それだけの価値が絶対にある。『ブリリアント』ファクトリーの取り組みが始まってから、工場は以前よりずっと整備された。探し物のために走り回ることも、今はあまりない」
カストル氏自身の仕事の生産性も大いに高まっていている。「作業場で起こっていることを自分のデスクから正確に把握できるようになった」という。
かつては情報を見つけるのに多くの時間を費やし、時にはエンジン部品の書類を探すのにいくつもの箱をしらみつぶしに調べることもあった。
しかし、今では自身のPCや作業場のステーションの上にある大型スクリーンを眺めれば、工場が目標を達成できているかどうかや、メンテナンスが必要なラインがあるかどうかを確認できる。それゆえ、安全課題や優先順位の高いプロジェクトに注力することが可能になった。
グローブシティで電車のおもちゃで遊びながら育ち、この地で働きたいと願ってきた者としては、GEがものづくりの未来に備えてこの工場を進化させていく過程を目の当たりにできるのはとても嬉しい、とカストル氏は話す。
それでもなお不安を捨てきれないメンバーに向けて、カストル氏はこうアドバイスする。「この変革のチャンスを活用しよう。少し変化を受け入れてみれば、この変革が本当に多くの時間の節約につながることを認識できるはずだ。僕自身も毎日、とても大きな恩恵を受けているよ」ー。
カストル氏はペンシルバニア州グローブシティにあるGEトランスポーテーションの工場に勤めるようになってまだ2年しか経っていなかったのに、昨年、何十年もこの組立ラインで働いてきた作業員たちに、業務手法が劇的に変わろうとしていることを伝える必要があった。
重さ4万ポンド(約18トン)の機関車のディーゼル・エンジンのボルトを正確な強度で締める際には、全長3フィート(約0.9m)の油圧トルクレンチを作動させる反復的なプロセスが必要。しかしカストル氏は作業員たちに「今後はそんな複雑な定石に基づく手作業は必要なくなるんだ」と説明した。
今後、こうした作業はロボットが代替し、作業員はその進捗を監視するようになる。「僕がそう伝えたとき、現場からは“このやり方を20年も続けてきたし、作業方法は熟知している!”という反論が噴出した」とカストル氏。
敷地面積240,000平方フィート(約22,297m²)、400人近い社員を抱える工場の未来にとって、この変革は重要な意味をもつことをカストル氏は認識してした。
それはこの工場を「ブリリアント」ファクトリーにするというGEの決断の重要な側面でもあった。GEのブリリアント・ファクトリーは、より効果的に業務を遂行できるよう、リーン手法とソフトウェア、センサー、リアルタイムデータなどのデジタルソリューションを活用している。
GEは新設工場、既設工場を含め、世界に7つの工場拠点を「ブリリアント・ファクトリー」にすることを決め、2015年2月、その第1弾をインドのプネーにオープンさせた。
この7拠点には、カストル氏が管理するグローブシティの工場、そして東京都日野市にあるGEヘルスケア・ジャパンの工場も含まる。今では、世界中に広がるさらに多くの工場で「ブリリアント・マニュファチャリング」の考え方が取り入れられるようになった。
カストル氏がこの動きを歓迎したのは、こうした変革によって工場はコスト競争力を維持し、長期的存続が可能になることを知っていたからだ。
GEは最近、グローブシティの事業に1億5,000万ドルを超える投資を行った。これには新しいエンジンを組み立てるための2つ目の工場建設も含まれている。
「ここはGEが成功させたいと願っている場所なんだと認識できて、雇用が保障されていると実感できる」(カストロ氏)。それでもやはり、作業員たちはしばしばオートメーション化に不安を抱いていることに、彼は気付いた。
新たなシステムに適合できないと思い込んでいる者もいれば、仕事量が減って全員に行きわたらないのではないかと心配する者もいる。
しかし、オートメーション化は一部の業務を減らす一方で、他の業務のニーズを増やしてもいる。実際、1982年~2012年の米国の労働人口に関するある調査によると、コンピューターに依拠する割合が高い業務分野の方が、雇用増加のスピードははるかに速いという結果も示されている。
作業員たちの不安を和らげるため、カストルはそれぞれの生産ライン・チームのミーティングに頻繁に参加し、工場デジタル化が進むことによって日常業務がどう変わっていくのかを作業員たちに説明した。
ボルトのトルク作業の自動化は、ケガを減らしながらも精度を高めることができること。「ブリリアント」ファクトリーのプロセスは業務を減らすために設計されているわけではなく、工場の効率や柔軟性を向上させるためのものであって、製品のさらなる多様化を図れること。
「作業員の中にはそれでも昔ながらのやり方に固執する者もいた」ものの、大部分のメンバーは「これによって誰もがもっとスマートに働けるようになる、ということをしっかり理解してくれた」とカストロは話す。
工場のオペレーションがデジタル化される以前は、作業員が不具合を起こしたすべてのエンジンを完全に分解し、組み立て直していた。
今では、各機関車に設置された何百個ものセンサーからエンジンの健康状態を仔細に把握できるようになったので、エンジンを再発送するまでに、簡単な修理だけで済むような場合もある。
2014年からグローブシティの工場で働いているジェイミー・モイヤー氏は、追跡しやすいようにエンジン部品にバーコードを刻むチームに所属している。
「覚えるまでに少し時間はかかったけど、それだけの価値が絶対にある。『ブリリアント』ファクトリーの取り組みが始まってから、工場は以前よりずっと整備された。探し物のために走り回ることも、今はあまりない」
カストル氏自身の仕事の生産性も大いに高まっていている。「作業場で起こっていることを自分のデスクから正確に把握できるようになった」という。
かつては情報を見つけるのに多くの時間を費やし、時にはエンジン部品の書類を探すのにいくつもの箱をしらみつぶしに調べることもあった。
しかし、今では自身のPCや作業場のステーションの上にある大型スクリーンを眺めれば、工場が目標を達成できているかどうかや、メンテナンスが必要なラインがあるかどうかを確認できる。それゆえ、安全課題や優先順位の高いプロジェクトに注力することが可能になった。
グローブシティで電車のおもちゃで遊びながら育ち、この地で働きたいと願ってきた者としては、GEがものづくりの未来に備えてこの工場を進化させていく過程を目の当たりにできるのはとても嬉しい、とカストル氏は話す。
それでもなお不安を捨てきれないメンバーに向けて、カストル氏はこうアドバイスする。「この変革のチャンスを活用しよう。少し変化を受け入れてみれば、この変革が本当に多くの時間の節約につながることを認識できるはずだ。僕自身も毎日、とても大きな恩恵を受けているよ」ー。
GE REPORTS JAPAN
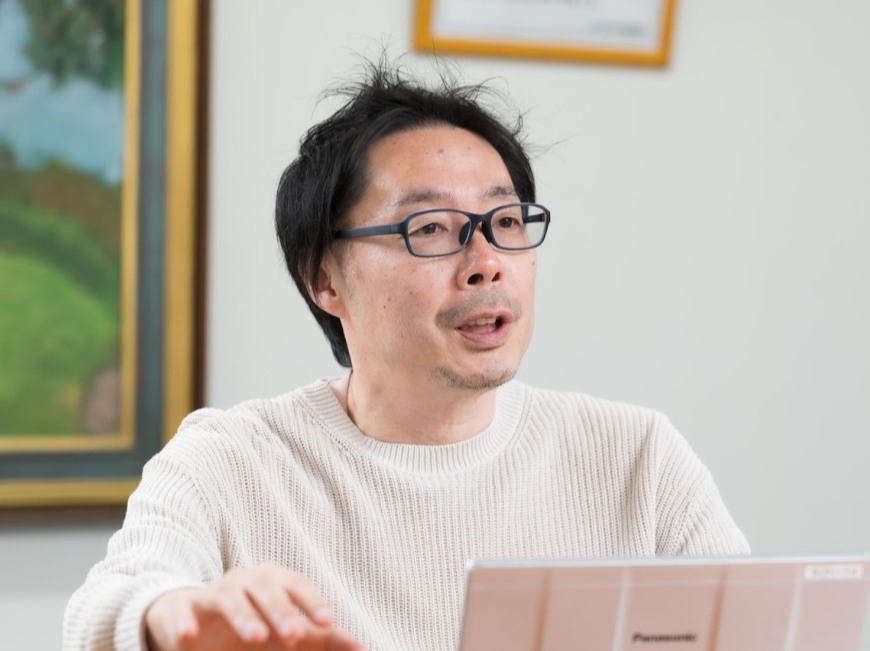