4時間かかっていた段取りを3分にまで短縮したひらめきとは?
10分以内で段取りを行う「シングル段取り」、ヒューマンエラーを未然に防ぐ仕組み「ポカヨケ」。生産現場の改善で用いられるおなじみの手法だ。これらの手法を築いたのは、新郷重夫氏。戦後、コンサルタントとして多くの製造業の現場改善に取り組み、トヨタ生産方式の源流を形作ったともいわれる人物である。画期的な改善手法が生まれた背景には、現場の事実を正しく捉えて、真の問題を探求する粘り強さと熱意があった。
月刊誌『工場管理』4月号特別企画「“カイゼンの職人”新郷重夫に学ぶ 改善の原点的思考」への寄稿「IEを現場のものにし、卓越した改善の功績を残す『新郷重夫』を知る~その思いと思考、改善の手法を紐解く~」(日本能率協会コンサルティング・石田秀夫著)を一部編集の上、4回にわたって紹介する。新郷氏の功績を振り返り、現場改善に向き合う姿勢や思いに迫る。
変種変量に対応した「シングル段取り」とは
シングル段取りのシングルは、ゴルフをやっている人にはなじみがあるかもしれないが、1桁分(=10分未満)で、プレス型などの段取り切替えを行うことである。
英語では、“Single Minute Exchange of Die“と言い、略してSMEDと言わることもあり、生産工場では、KAIZEN同様、世界でも語られる日本発の言葉である。
「シングル段取り」を発案した背景
大量生産のビッグスリーに対して、変種変量生産をより効率的に生産を行おうとした場合、プレスの型段取りは1950年代では4時間程度を要しており、プレス機の可動率を悪化させていた。その段取り時間を圧倒的に短縮することが求められ、取り組んだのである。発案まで少々時間を要し、発案まで3段階あったとされている。
▶はじまりと気づき
1950(昭和25)年、東洋工業にて800 tプレスの稼働分析を行った際、段取り替えで「型の取付けボルトが紛失していたため長時間のロスが発生した」とのことである。それを新郷さんが見て、
『段取り替えには、
・内側の段取り(内段取り)…機械をどうしても止めて行わなければならぬ段取り
・外側の段取り(外段取り)…機械の回転中にあらかじめ、あるいは後で行うことのできる段取り
の2つの性格がある、ということを悟った』
とのことである。
▶実は実施していた外段取り
『1957年(昭和32年)三菱重工業広島造船所で、エンジン・ベッドを「大型の片持プレーナー」で、切削する作業があった。この機械の能力不足を解消しよう、と散々苦心した結果、段取替え時間が長くかかっているので、機械のテーブルをもう1つ製作して、「エンジン・ベッドをプレーナーで切削中に、次のエンジン・ベッドを“予備の機械のテーブル上で、芯出し、取付け等の段取り”を行い、加工が終ったら“機械のテーブルと共に、次のエンジン・ベッド”をプレーナーに取付ける」というようにして、大幅に機械の稼働率を向上させることができたのである。そして、素晴らしい“作業改善を行った”と工場長と共に喜んだことであったが、これは今から考えると、正に「内段取りを、外段取りに転化した」ということであり、私が、この改善を「単なる“作業改善”としてではなく“思想的な改善”と悟っていれば、わが国の“シングル段取り”は、もう13年、早く生れたことになったであろう」と、実に残念に考えている次第である』とある。
(『トヨタ生産方式のIE 的考察―ノン・ストック生産への展開―』新郷重夫著より転載)
▶トヨタ生産方式の追求のために
『1970年(昭和45年)トヨタ自工において1000tプレスの段取替えに“4時間”を要していた。ところが、西独のVW社が“2時間”で行っている。というので、何としても、それを追い越そうと半年余り努力して、とのことである。
・内段取りと外段取りをハッキリ分けて、外段取りでできることは、一切外段取りで行う
・内段取り、外段取りの方法そのものを改善する
ということを熱心にやって“1時間半”に短縮することに成功したのであった。<中略>
部長さんから「あの1000tプレスの段取替えを“3分”にせよ」、トップから命令されたが、どうしたらよいだろうか?と相談をもちかけられて、4時間の段取替え時間を1時間半まで改善するのに、あれだけの苦心をしたのに、それを更に“3分にする”ということは大変なことだ。むしろ「不可能だ」と思ったトタンに「“ハツ”と、インスピレーションが閃めいた」<中略>
「ソウダ、内段取りを外段取りに追い出せばよいのではないか!」と考えて、その場で黒板にスラスラと手法を書いて、列席の杉浦車体部長、地視主担当員、太田職長さん等に説明した』
(『トヨタ生産方式のIE 的考察―ノン・ストック生産への展開―』新郷重夫著より転載)
シングル段取りの概要および解説
型や治工具などの段取り切替え時、通常は生産活動を止めて、段取りを行う。その間、可動率としては低下することになり、可動率を下げないため、大ロットで生産し、段取り切替えを最小限にしたくなるのが、変種変量かつ必要な特に必要なだけつくることを考えると、段取り切替えの圧倒的短縮が必要である。そのレベルを10分未満にすることがシングル段取りである。
段取りには内段取りと外段取りがあり、ほとんどの内段取りを外段取りに追い込むことで、可能になってくる。
・内段取り:設備を止める必要がある段取り
・外段取り: 設備を止めなくてもできる段取り(段取り前か後にできる段取り作業)
改善のステップ
段取り改善においては、まずは徹底して外段取り化し、その次にワンタッチ化、一発化などで内段取りを短縮していく。
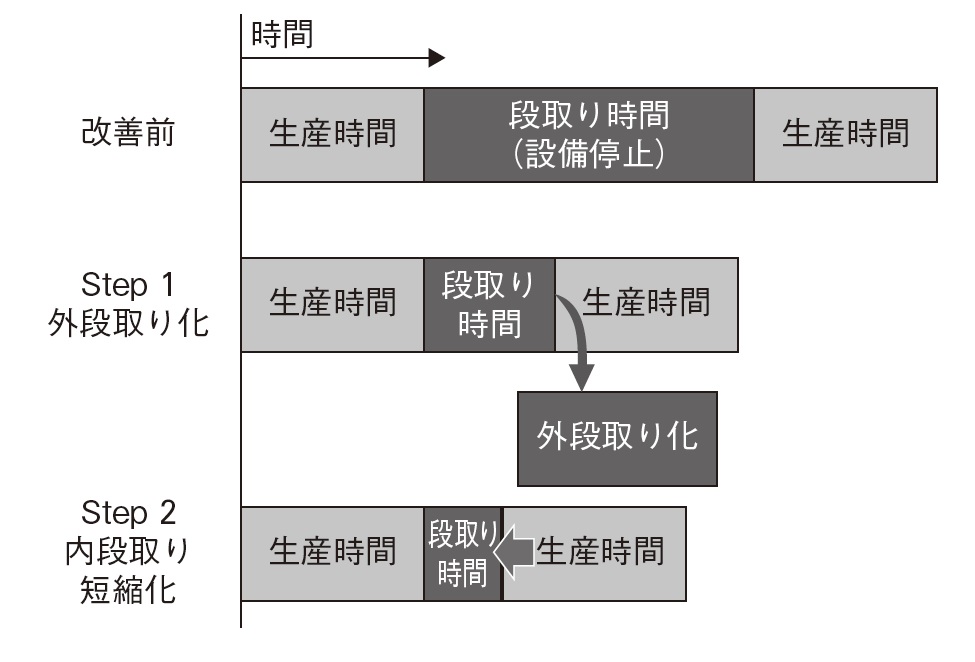
改善の効果
例:大型プレスの段取り
4時間→1時間→10分→3分
現在トップクラスは3分程度で段取り替えを行う。圧倒的な成果と言えるのではなかろうか。
この手法の本質
徹底的な外段取り化と内段取り化で、段取り替え時間は短縮できるが、材料や生産品種を切り替えた際に、1発目から良品が生産できることが大切である。そのために、製品の良品品質条件の蓄積が必要な技術と技能となってくる。
筆者:石田 秀夫
株式会社日本能率協会コンサルティング
取締役 生産コンサルティング事業本部 本部長 シニアコンサルタント
URL:https://www.jmac.co.jp/
(『工場管理』2023年4月号 特別企画「“カイゼンの職人”新郷重夫に学ぶ 改善の原点的思考」解説より抜粋)
雑誌・書籍紹介
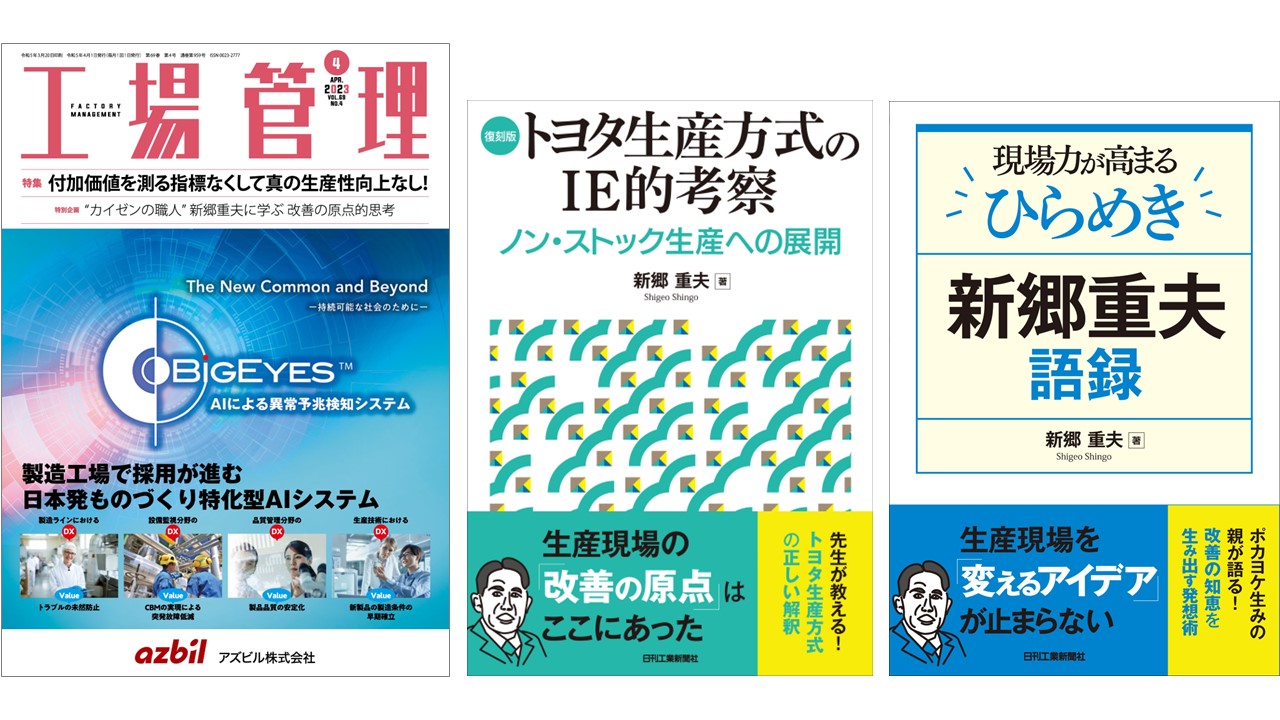
書名:『工場管理』2023年4月号
税込み価格:1,540円
<販売サイト>
Amazon
Rakuten ブックス
日刊工業新聞ブックストア
書名:復刻版 トヨタ生産方式のIE的考察 ノン・ストック生産への展開
著者名:新郷重夫
判型:A5判
総頁数:368頁
税込み価格:3,850円
<販売サイト>
Amazon
Rakuten ブックス
日刊工業新聞ブックストア
<目次>
<第1部>工場改善の原点的志向
第1章 生産の構造
第2章 工程の改善
第3章 作業の改善
第4章 ノン・ストック生産への展開
<第2部>トヨタ生産方式のIE的考察
第1章 トヨタ生産方式の理解
第2章 トヨタ生産方式の構成
第3章 トヨタ生産方式のIE的構成
第4章 カンバン制度の展開
第5章 トヨタ生産方式の周辺
第6章 トヨタ生産方式の進路
第7章 トヨタ生産方式の導入と展開
第8章 トヨタ生産方式の総括
書名:現場力が高まるひらめき 新郷重夫語録
著者名:新郷重夫
判型:四六判
総頁数:192頁
税込み価格:1,980円
<販売サイト>
Amazon
Rakuten ブックス
日刊工業新聞ブックストア
<目次>
第1章 改善を始めるために
第2章 改善するべき問題を見つけよう
第3章 なぜ改善するのか、その目的を理解しよう
第4章 改善案を作ってみよう
第5章 改善を実現していこう
特集・連載情報
月刊誌『工場管理』4月号特別企画「“カイゼンの職人”新郷重夫に学ぶ 改善の原点的思考」への寄稿「IEを現場のものにし、卓越した改善の功績を残す『新郷重夫』を知る~その思いと思考、改善の手法を紐解く~」(日本能率協会コンサルティング・石田秀夫著)を一部編集の上、4回にわたって紹介する。新郷氏の功績を振り返り、現場改善に向き合う姿勢や思いに迫る。