半導体「後工程」に脚光、次世代技術開発が活発化
半導体の性能向上に向け、製造プロセスの「後工程」の重要性が高まっている。回路を形成する「前工程」の技術進化はハードルが上がっており、複数チップを積み重ねて性能を高める3次元積層など後工程の次世代技術の開発が活発化する。それに伴って後工程製造装置の需要が高まる見通し。成長市場で商機を捉えようと、装置メーカー各社も技術開発などを活発化している。(山田邦和)
【専門展示会、日本で初開催】装置・材料アピール
「半導体の後工程に光を当てたい。後工程の進化を支える製造装置メーカーや材料メーカーをアピールし、認知度の向上や業界の活性化につなげたい」。半導体の業界団体、SEMIジャパンは後工程に特化した国際展示会「アドバンストパッケージング・アンド・チップレット・サミット(APCS)」を12月に日本で初めて開催する。SEMIジャパンの浜島雅彦代表は8月末に行った記者会見でAPCS開催の意図をそう説明した。
70―80社の出展を見込み、アジアを中心としたOSAT(後工程専業の製造受託会社)などに向けて装置や材料をアピールする。実行委員会にはアドバンテストやディスコ、東京精密など10の企業・大学が参加。経済産業省もオブザーバーとして加わった。同時開催する半導体関連の国際展示会、セミコン・ジャパンとの相乗効果を見込み、合計の入場者数で「(セミコン・ジャパン単体の開催だった時の2倍近い)10万人規模を早期に目指したい」(浜島代表)と意気込む。
半導体の製造工程はシリコンウエハーに回路を形成する前工程と、ウエハーからチップを一つずつ切り分けて完成品に仕上げる後工程に分けられる。市場が大きいのは前工程。SEMIの予測でも2022年の世界の半導体製造装置の販売額1175億ドル(約16兆8052億円)のうち、後工程の比率は約15%(165億ドル)にとどまり、80%以上を前工程が占める。
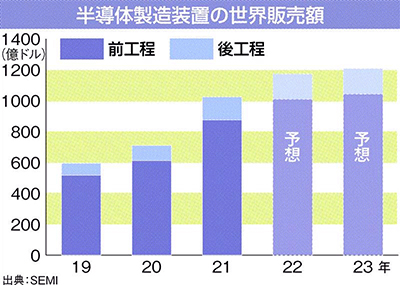
近年の半導体の性能の進化は電子回路の線幅を狭め、集積度を高める微細化と軌を一にしてきた。この微細化を支えたのが前工程で、装置市場の規模も大きかった。だが回路の寸法はすでにウイルスの10分の1以下に極小化。原子の大きさという制約もあり、微細化のハードルは年々高まっている。開発や量産コストも大きく膨らみ、性能向上に対し価格が高くなり過ぎる事態が生じつつある。
【量産へ装置各社に期待】チップレット技術カギ
一方でスマートフォンなどの最終製品は半導体の更なる能力向上を求める。このため近年注目を集めているのが集積度を平面方向に高めるだけでなく、縦方向に増していく方法だ。中でも現在トレンドとなっている技術の一つがチップレット。従来は一つのチップ上に混載していたさまざまな機能を、別々のチップで作り分け、ブロック玩具のように組み合わせて、あたかも一つのチップのように動かす。中核部分には最新世代、周辺部分には旧世代のチップを用いれば、微細化に頼らずに半導体の機能向上をより安価に実現できる可能性がある。
チップレット技術の成功には、チップを造る後工程がカギになる。重要性の高まりに比例して市場も拡大する見通しだ。「約10年後には装置の販売額に占める後工程向けの比率は約30%と、現在から倍増する」と英調査会社オムディアの南川明氏は予測する。
【前工程各社も商機探る】他社にない強み生かす
チップレットは新たな技術なだけに、接続スピードの向上や放熱性の改善、コスト削減など本格的な量産までに越えなくてはならないハードルは多い。その分、製造工程を支える装置メーカーへの期待も高くなる。「例えばチップを切り分けるダイシング工程では、加工速度を速めながら、生じる切り粉をいかに少なくするかがポイント。目に見えないほどの切り粉やゴミでもその後の工程の歩留まりに影響するためだ」。APCS実行推進委員会の委員長を務める、長瀬産業の折井靖光執行役員はそう話す。
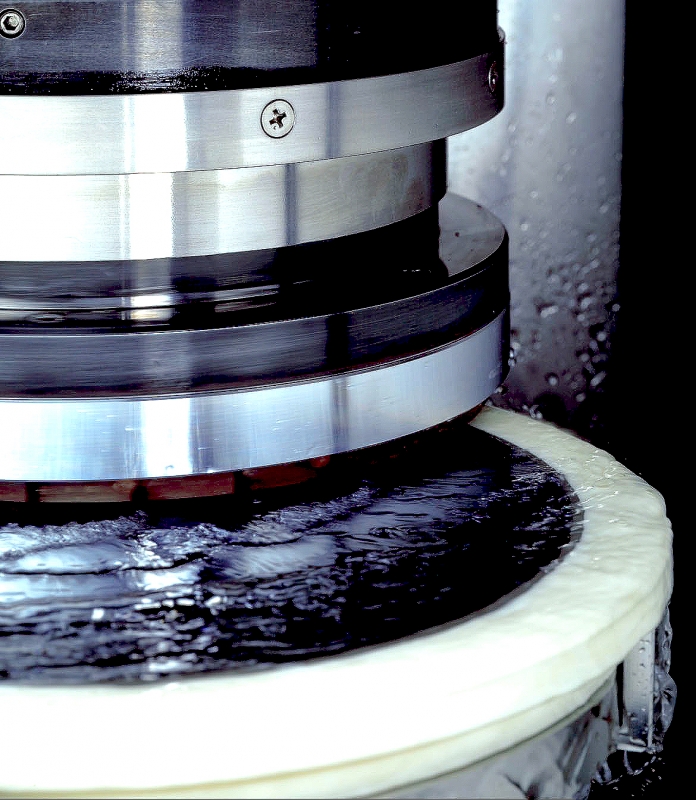
現状で高いシェアを持つ後工程装置メーカーも対応が欠かせない。ダイシング工程で使われるダイシングソーで約7割と、世界シェア首位を握るディスコ。同社の川合章仁営業技術部長は「チップレットに限らないが」とした上で「求める加工結果を実現するために、レーザーを含めた新しい加工方法を活用していく可能性がある」と説明する。同社は砥石(といし)を使った切断や切削装置で知られるが、「レーザーの中にはパルス発振レーザーのように非熱加工(瞬時に加熱し気化する)が可能で、砥石とは異なる加工結果が得られるものもある。応用することでこれまでとは全く違う加工スピードや品質に到達するポテンシャルはあると思っている」として、開発に注力していく考えだ。
できあがったチップが設計通りに動作するか、電気信号を流して確認するテスト工程でも「積層化で複雑になる配線をより早く、正確に検査できる装置の需要が今後高まる」(業界関係者)との見方が多い。
後工程市場の拡大を見据えて、前工程の製造装置メーカーも相次ぎ参入を目指す。東京エレクトロンの河合利樹社長は、6月の中期経営計画の発表会見でウエハーボンディング装置の見通しについて問われ「量産に移行すれば大きな市場となる」と見通しを語った。「東京エレクトロンには前工程で培ったスーパークリーン技術や洗浄技術などがあり、競合他社にはない強みだ」として、事業拡大に意欲を示した。
前工程と後工程の融合もすでに始まっている。一例がインターポーザ(複数の半導体チップと基板を接続するための中継部材)向けの露光装置だ。インターポーザ上に配線を形成する際は特殊な露光装置を用いる。シリコン基板上に回路を転写する通常の露光装置とは異なる特性が必要で、先端パッケージ向けではキヤノンが市場シェアの大半を握る。「今後も露光面積の大型化や解像度の向上などさまざまな取り組みで顧客の要望に応え、シェアの維持・拡大に努める」と武石洋明専務執行役員兼光学機器事業本部長は話す。
【複数の課題】OSAT誘致の要望も
既存の装置にこれまでになかった商機が生まれ、新たな装置の需要も期待できる後工程市場。日本の半導体産業全体が浮揚する転機にもなり得るだけに、関係者の期待は高い。長瀬産業の折井執行役員は「たくさんの部品を細かい配線でつなげ、小さくまとめるのは日本の得意な技術。国内の装置や材料企業が今まで培ってきた技術を世界に見せる時が来たと思っている」と力を込める。
一方で課題もある。複数の業界関係者が指摘するのが、日本国内には海外にあるようなOSATが存在しないことだ。前工程はトランジスタの集積度が約2年で倍増するという「ムーアの法則」に代表される標準化された技術ロードマップが存在し、開発するべき基本的な技術を世界中で共有できている。
これに対して後工程にはそうしたロードマップが存在せず、スマホメーカーは小型化や消費電力の削減、自動車メーカーは信頼性や耐熱性など、ユーザーごとに要求項目が異なる。ユーザーの潜在ニーズを素早く、的確に汲み取り、製品に反映させる必要がある。
ディスコのように試作や商談のための施設を世界中に展開する企業、東京エレクトロンのように今後5年間で1兆円以上の研究開発費を投入する企業は問題ないものの、中小企業にとっては、物理的な距離がユーザーニーズの汲み取りを難しくする可能性もある。台湾積体電路製造(TSMC)が茨城県つくば市に研究開発拠点を設けたが、業界関係者は「今後は海外大手OSATの製造拠点の誘致なども政府には期待したい」と話す。
【関連記事】 世界の半導体工場で、揺るぎない信頼を集めるクリーン搬送装置