海外で「日本製は壊れない」と言われる所以? 知られざる、設計審査会議の内容とは
前回の連載では、設計者がイラストを描くことから始まり、3次元データを作成し、またシミュレーションを用いて効率良く設計することをお伝えした。製品化プロセスにおいて、次のステップは試作となる。ここでいう試作とは、試作部品の作製とその部品を用いての組立てである。その試作に入る前には設計審査を行う必要があり、その目的は、設計のアウトプットである3次元/2次元データおよび部品表(BOM)が下記の4つの項目を 満たしているかの妥当性を確認することだ。
①製品仕様②製品、部品コスト
③品質レベル
④試作コスト
①と②は、第3回連載で詳細をお伝えしているのでそれを参照してほしい。③は、製品化を行う企業の定めている品質レベルのことである。その詳細は第4回連載にある“設計で押さえるべき7つの規制”を参照してほしい。④は、本来は設計審査で行うものではないが、製品化を行う企業としては押さえておくべきことであるため、あえてここに記載した。製品化を行う企業は、その製品化プロセスのどのステップで審査を行い、何の項目を審査するかを決める。上記は一般的な4つを示した。
設計審査の会議
各項目は設計審査の会議の前までに確認を行い、その確認結果を会議で提示する。①の“製品仕 様”に関しては、実際に試作部品で組立てを行って検証してみなければ判断できない項目が多いため、製品仕様を満足できる既製のデバイスや部品の提示、3次元データやシミュレーション、計算結果から問題がないことを示す。②のコストに関しては、既存部品からの類推や購買部からのアドバイス、部品メーカーへの見積もりなどで確認し計算することになる。
試作部品の作製には多額の費用がかかる。試作部品は一般的に10個くらいから多くても100個くらいの1回きりの生産であり、その段取り費用をその少ない試作数個で案分するため、部品は高額となる(図1)。その高価な試作部品を何の確認もなく発注してはならないため、設計審査のときに試作部品の合計コストが予算内に収まるかどうかの確認も行う必要がある。予算をオーバーしそうであれば、試作個数の削減や塗装品の塗装削除などで試作費用を削減する。これは設計審査とは別に行っても問題はない。設計審査で一番大切な項目は、次項でお伝えする品質レベルの確認である。
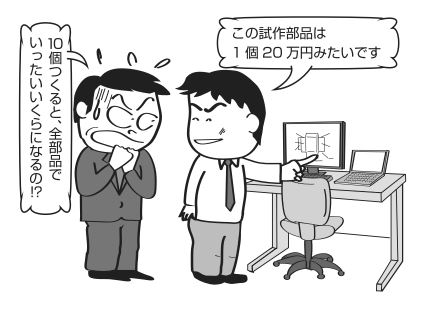
設計審査での品質レベル確認の意義
製品化を行う企業には、その企業独自の品質レベルがある。設計審査における品質レベルの確認項目の数とその内容がその企業の品質レベルとなる。しかし、一般的に品質レベルの確認といってもその項目は非常に多岐にわたり、それらをすべて完璧に確認するには際限なく時間がかかる。何の項目をどのように確認するか、というのも製品化を行う企業のノウハウなのだ。
設計審査は3次元/2次元データおよび部品表の確認であり、3次元データでのシミュレーション結果があれば、さらに確認できる項目は増える。この確認はほかの項目と同じく、設計審査の前に確認会を開催して実施しておく。そして確認した結果を設計審査で提示する。筆者は機構設計者であるため、ここからは機構設計に関する内容でお伝えする。
品質レベルの確認は、3次元データと2次元データが作成し終わった後、試作部品を発注する前の段階で行うことが望ましいが、指摘事項が多いと設計の手戻りが発生する場合がある。確認会後に設計修正を行い、再度3次元データと2次元データを作成し直すとなると非常に多くの時間を費やしてしまう。筆者は、3次元データの完成度が9割方の段階で、まだ2次元データを作成する前で確認会を開催するのが望ましいと考える。9割方の意味は、確認会で確認すべき項目にかかわる設計はすべて完了しているが、それには関係しない細部の設計までは完了していない、という意味合いがある。
確認会で問題点を指摘する方も、2次元データまで完成した後で大きな変更になり得る指摘をすることに忍びなさを感じ、指摘のちゅうちょや、「その変更は日程もないことだから、次回の試作で修正することにしましょう」という判断が出てしまうことがあるからだ。この品質レベルの確認は非常に多くの項目があるため、確認会を数日に分けて行い、2次元データの確認はその日程の最終日が適切と考える。
製品化プロセスでの最初の品質レベルの確認会では、いかに多くの問題点を見つけ出すかが重要となる。その理由は以下の2つである。
まず1つは、製品仕様がいくら細かく決まっていても、設計内容のパターンは無限にあるものだ。筆者は、前職で製品の設計を幾度と行う中で、「もう一度最初から設計し直させてもらえれば、もっと良い設計ができるのに」と思うことが何度もあった。しかし、設計が進む過程では多くの検証を実施しており、その検証結果を元に設計修正をして設計の完成度を少しずつ上げているため、検証をゼロからやり直すような大きな設計変更はできないのである。設計は一度進めてしまえば、大きな手戻りは避け、無限にある設計内容のパターンの中の一つを、企業で定めた品質レベルを満足できるように設計修正を加えながら製品にしていく(図2)。設計者の選択した設計内容に大きな問題があれば、早い段階でそれを指摘してもらい、設計初期の段階で改善しておきたい。
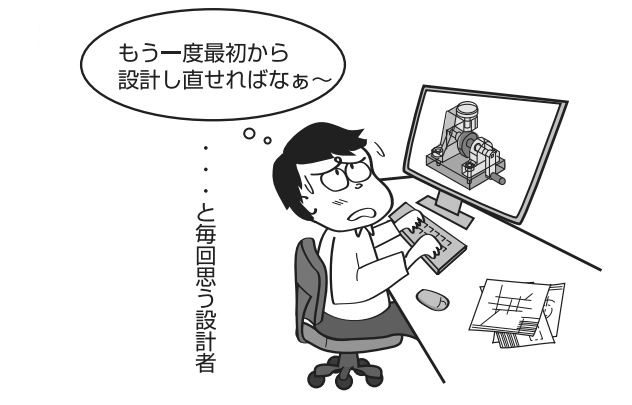
もう1つの理由は、たとえ大きな手戻りが発生しない問題点でも、製品化プロセスが進むにつれ、その変更にかかるコストは増えていくからだ。3次元データのみの修正であれば、その修正に時間を費やすだけであるが、試作部品をつくっていればその追加工のコストが必要になる。試作部品の組立てを終えていれば、その組直しの時間が必要になり、もし金型の作製が進んでいれば、金型修正にコストが発生する。製品が市場に出てからの修正は市場改修となり、昨今の大手製造業の品質問題で報道されたものでは、数百億円の改修コストになっている。このようなことから設計審査前の品質レベルの確認会は、決して形式的な会議にしてはならない。
品質レベルの確認会では企業で定めた品質レベルを満足していても、設計アドバイス的な指摘事項も多く得られる。設計者のスキルにもよるが、設計の問題点がゼロであることはほとんどあり得ず、たとえ品質レベルを満足していても、より品質を上げるための改善点は必ずあるものだ。問題点の指摘が多くあればあるほどより品質の高い製品となり、設計者自身の設計スキル向上にもなるため、この確認会を有意義なものとして活用したい。指摘事項が少なかった際は安心するのではなく、確認が足りていなかったと考えた方が良い。
品質レベルの確認
品質レベルの確認項目は主に次のとおりである。
1)安全性(一部は法規制)2)信頼性
3)製品の製造性(組立性)
4)部品の製造性(例えば金型に対応すること)
5)サービス性
1.安全性
安全性とは、製品を使用する人やその使用環境にある財産(家など)に危害や損害を与えてはならないことだ。身近な製品ではスマートフォンやパソコンのバッテリーの破裂や発火がある。このような問題を3次元データなどで見つけ出すことは難しいが、3次元データだけで判断できる項目も多い。傘のフレームの先端が目に刺さるとか、折り畳み机に指が挟まる、などである。
安全性の一部は法規制になっていて、電気製品ではPSE(電気用品安全法)、医療用機器では薬事法、食器などでは食品衛生法がある。前述で、品質レベルは企業が定めるものとお伝えしたが、法規制になっているものはそれを順守した設計をしなければならず、当局から認証を受けて市場に出す必要がある。法規制になっているものはその規格書に則った設計をしなければならないが、一般的に規格書は多くの製品に通用するように汎用的に書かれているため、企業のオリジナル製品に当てはめて考えることが難しい場合が多い。法規制の専門機関に、できれば3次元データを描き始める段階から相談するのが賢明だ。
2.信頼性信頼性とは、製品が想定した環境で製品仕様を果たすことを指す。JIS(日本産業規格)で定められているものや、企業が社内の品質規格として独自に定めるものもある。また、製品のカタログに記載するもの、しないものがある。JISに記載され、カタログにも記載するものとしては、iPhoneの防水の保護等級がある。JISに記載され、カタログに記載しないものには、輸送包装試験規格がある。製品としてこの規格を満足しているのは当たり前であるため、カタログには記載しない。JISに記載はなく、カタログに記載 するものとして、「◯◯気圧の高地で使用可能」や、「騒音◯◯dB以下」がある。JISに記載がなくカタログにも記載しないものは、パソコンの開閉における耐久性がある。企業が定めた製品寿命に対し、十分な耐久性を持っているかどうかだ。よく「日本製は壊れない」と言われる要因の一つは、この信頼性の基準を製品の多くの箇所に定めていて、さらにその安全率を高く設定しているからであると考える(図3)。
これらのほとんどは3次元データを見るだけでは判断できないものが多く、計算やシミュレーションの結果で判断することになる。
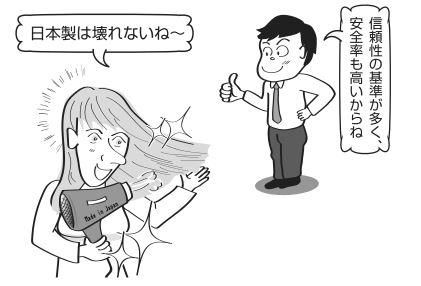
製品の製造性とは、組み立てやすさのことだ。組み立てやすいということは、組立ミスが生じにくく品質向上につながる。また、組立作業のタクトタイムが短くなりコストダウンのメリットもある。
組み立てやすさは、現物の試作部品がないと判断しにくいが、3次元データで判断ができるところも多くある。部品の3次元データを組み立てる順番にディスプレイ上に映し出し、設計者の想定した組立順に問題がないかを見ていくと良い。同時に、部品同士の嵌合具合(公差など)や勘合方法、接合方法(ビスや溶接)が適切であるかの確認も行うことができ、ある部品が間違った向きに取り付いてしまうことがないか、また別の部品が取り付いてしまう可能性はないかの確認もできる。
4.部品の製造性部品の製造性とは、設計した部品が量産可能であるかの確認である。試作で部品を数個作製するのは、あの手この手を使えばどんな形状でもほとんどは可能であるが、量産となるとそうはいかない。板金部品をタレパンもしくは金型で作製する場合、どの順番で板金を曲げるかを考えながら設計する必要があり、樹脂の成形部品であればテーパやパーティングラインなどを考えながら設計する必要がある(図4)。それをつい忘れると、量産することが不可能な部品になってしまう。3次元データでは、それを確認することができる。
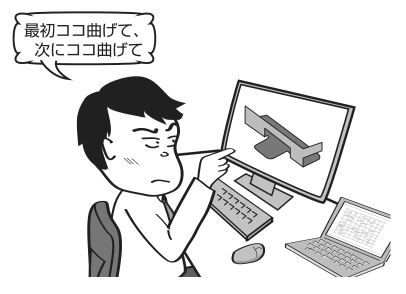
部品の製造性を考えた形状は、熟練の設計者でもわからないことが多い。また、量産する部品メーカーによっても、そのメーカーの得意分野や保 持している設備などで異なる場合がある。よって、3次元データの作成中であっても量産メーカーが 決まっていれば、相談しながら設計を進めるのが、手戻りのない設計を進めるコツである。タレパンと金型の両方で製造を行っている板金メーカーでは、試作部品を作製してくれると同時に、金型で作製するときの設計アドバイスをしてくれるところもある。
5.サービス性サービス性は、製品の販売後の修理のしやすさのことだ。交換する部品の取外しと取付けなどが、容易にできることを確認する。ほかの多くの部品を取り外さないと部品交換できない、ドライバーが届かない、交換部品以外の部品を変形/破損させてしまう、サービスマンに危険が伴うなどがあってはならない。これらは、もちろん組み立てた現物で確認する方が確実であるが、3次元データでも確認できる。
6.品質レベルの確認シート品質レベルの確認項目は非常に多岐におよぶため、項目を列挙した一覧表を確認シートにつくっておくと良い。大項目として前述した1)~5)の5項目があり、そのそれぞれの項目がさらに細分化される。そして、その各項目を満足しているか否かを確認会で判断する。設計審査は一般的に最低2回ある。初めての試作のときと量産と同等の部品での試作のときである。量産試作の方が、確認できる項目は多いので、それは一覧表で区別できるようにしておく。「製造性の問題は何があるかな~」と3次元データを漠然と眺めるような確認会はやめておきたい。この確認項目の数とその内容がその企業の品質レベルになるので、細分化された確認項目は基本的に1つの企業のどの製品も同じであるはずだ。しかし、製品が大きく異なれば、使用する言葉や内容も異なる場合があるため、あらかじめ製品ごとに確認シートはつくっておくのも良い。
確認結果は基本的には「OK」もしくは「NG」であり、設計審査ではすべて「OK」になっていなければ、次のステップには進めない。よく、重要度A、B、Cとランクを付け、「A:必ず修正」、「B:次回の試作までに修正」、「C:修正は設計に一任」などとする場合もあるが、筆者はおすすめしない。理由は、ユーザーにとってはどんなに軽微な不良であっても不良には変わりなく、そこに重要度は存在しない。また、設計者にとっても設計修正をするかしないかの2通りしかないからだ(図5)。A、B、Cに持たせる意味は、企業によってさまざまであると思うが、それをつけることによって、企業の定めた品質レベルにブレが生じ、設計者もそれに甘んじてしまうことは避けたい。
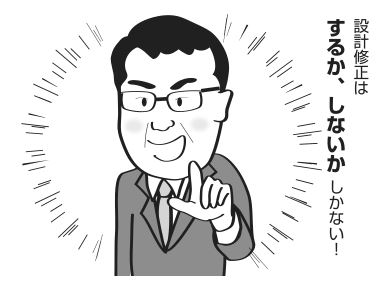
著者略歴
ロジ 小田 淳(おだ あつし)
製品化のイロハコンサルタント。上智大学理工学部機械工学科卒。ソニーに29年在籍し、プロジェクタなど15モデルを製品化。ベンチャーを支援する中で、材料費が高すぎ売っても損する、輸送中に壊れる、法規制がわからないなど、製品化のハードルを越えられない企業に出会う。企画から設計〜試作〜検証〜量産の全プロセスにおける、安全性(法規制)・信頼性・製造性・コスト管理などの手法をコンサルと研修で伝える。
雑誌紹介
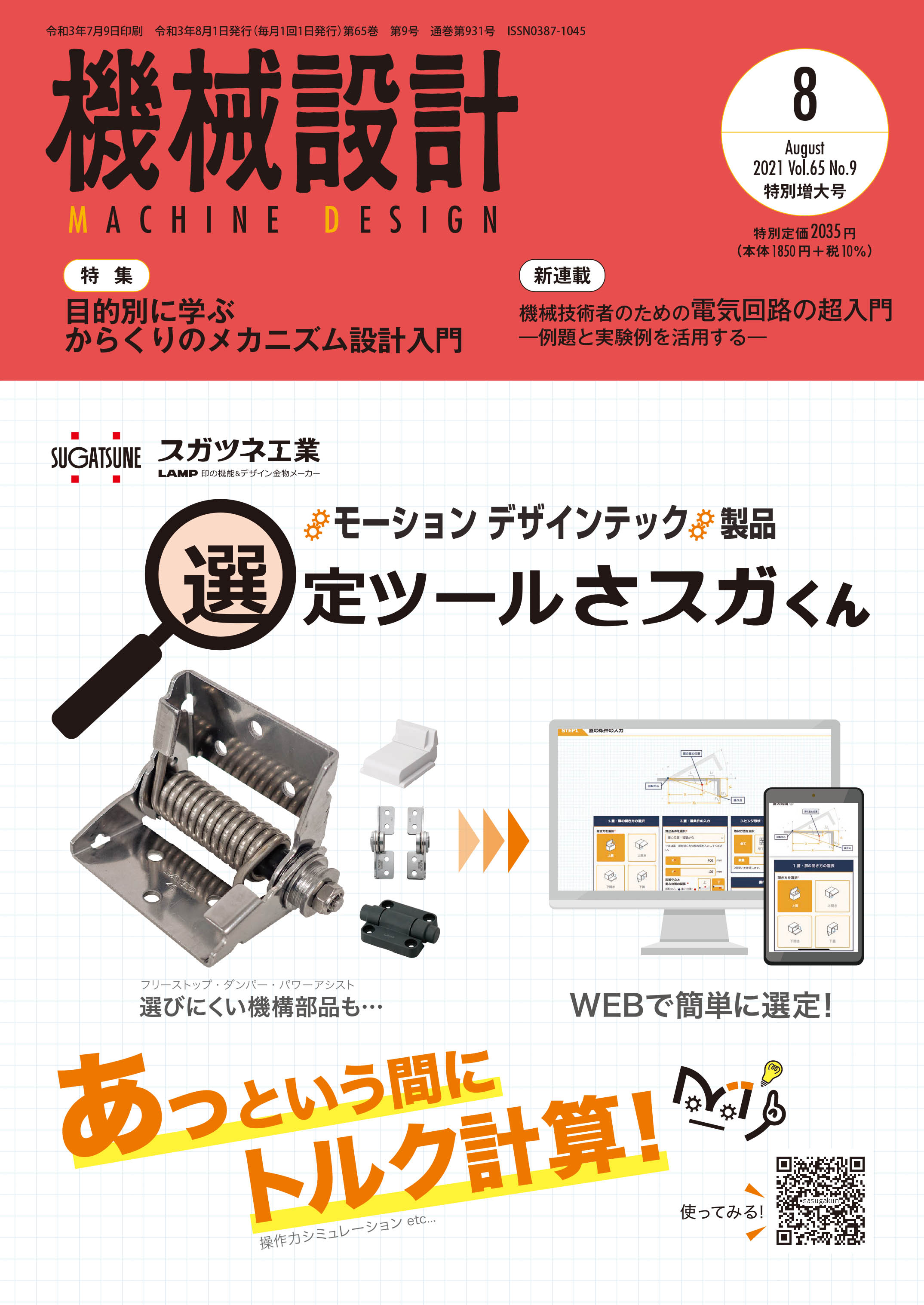
雑誌名:機械設計2021年8月号
判型:B5判
税込み価格:1,540円
内容紹介
機械設計 2021年8月号 Vol.65 No.9 【特集】目的別に学ぶからくりのメカニズム設計入門各種部品の加工・搬送・組立てなどにおいて、ワークの単純な送りや上下・回転移動、把持、配置、往復動作などを自動化するにあたっては、複雑な電気制御を用いなくても、リンク類や基本的な機械要素部品を工夫して組み合わせて用いることで、低予算で効果的な動きを実現するシステムを構築できます。本特集ではそのような「からくりのメカニズム設計」に焦点を当てます。製造現場で使用されることの多い動作を取り上げ、それらをからくりのメカニズムでどのように実現するかをやさしく解説します。