アイデアを実現するための要!「志」を明確にし、関係者を巻き込む
製品化において志を持つことは大切である。「この技術とアイデアは素晴らしいから一緒につくろう、買ってほしい」と触れ込んだところで、誰にも協力してもらえず、また買ってもくれない。カラーテレビが登場した時代であれば、まだ世の中には技術的に優れた製品がそれほど出回っていなかったので、それでも売れたかもしれない。しかし、現代はそうはいかない。
製品化における志とは「この製品でどのような世界をつくりたいか」である。iPhoneでいえば「外で電話ができて音楽が聴け、Webで検索ができるような世界をつくりたい」ということになるであろう。そこから次のステップで「携帯電話と ウォークマンと PC を一体化しよう」となり、iPhoneは考え出された(図1)。
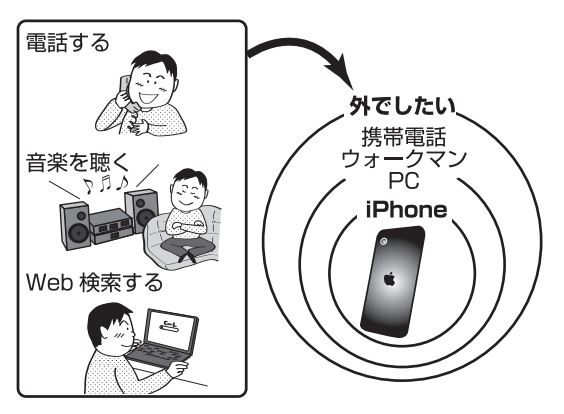
技術先行でも、後付けで志を考える
現実には、素晴らしい技術やアイデアが先行し製品化を開始する場合が多くある。以前放映されたNHK連続テレビ小説の「まんぷく」は、その典型的な例だ。カップラーメンを発明したが、当初は売れ行きが良くなかった。新技術とアイデアを 麺とそれを入れるカップに詰め込んだ画期的な製品がなぜ売れないのか、主人公の福子が悩み続ける。製品に問題はないはずだ。製品に対する自分 たちの思いに何かが欠けていて、それが顧客に伝 わっていないと福子は考え始める。しかし、その何かをなかなか見つけられないのだ。悩みに悩んだ末、自分たちには“志”がないという事実に行き着く。その後、その志を持って販売をしたところ、爆発的なヒット商品になっていったというストーリーである。志が何であるかは、ビデオオンデマンドで見てほしい。
このように、技術やアイデアが先行してしまうことはよくある。しかし、後付けでも志を見つけることによって大ヒットとなった製品は多い。ソニーのウォークマンも同様であった。
志というと大げさな気もするが、次のような例もある。それはiPodである。アップルがiPodを販売する以前に、他社からポータブルのデジタルオーディオプレーヤーは販売されていたが、ヒット商品にはなっていなかった。まだその頃はフラッシュメモリの容量が小さかったため、デジタルオーディオプレーヤーには100曲程度しか入らなかった。100曲だと週に1回程度の曲の入替えが必要となるが、パソコンに接続して曲を選択しiPodの中身を入れ替える作業は面倒であった。同じ100曲のみを聴き続けることになり飽きがきてしまい、デジタルオーディオプレーヤーを使わなくってしまった。そこで、アップルは容量を十分 に増やして「曲を入れ替える必要がないようにしよう」と考えたのだ。ストレージをハードディスクにして容量を5GBとし、1000曲以上が入るようにした。しかし、そのiPodはやや大きめのサイズであったため、次に小型にしたいと考えた。小型にすると容量を小さくするしかなく、曲の入替えが面倒になる。そこでPCに接続するだけで、勝手に曲が入れ替わる方法を考えた。そうして生まれたのがiPod shuffleである。これら2つはシンプルな志であるが、その志が市場をつくってきたと理解してもらえるのではないだろうか(図2)。
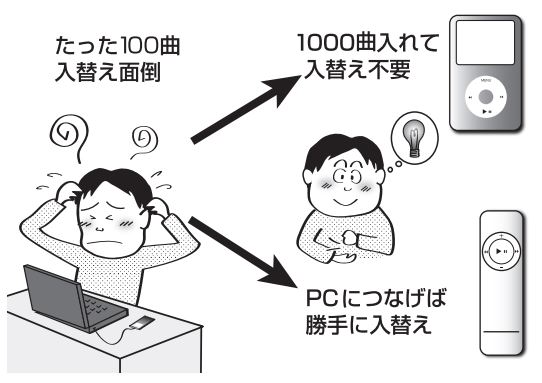
志がない製品
では、志がないとどうなるであろうか。製品化をするうえでは、複数の設計者や品質保証部/購買部などの関連部署、部品や製品を製造してくれる協力会社などの多くの関係者から協力を得なければならない。志がないと、これらの人々の製品化に協力するモチベーションが上がることはない。
仕様が決まると、製品の設計が開始される。しかし、設計内容がすべて企画書や設計構想書に記載されるわけではなく、設計者に一任されている 内容は非常に多い。志が明確になっていないと、多くの設計者の設計に対するベクトルが揃わず、結果としてポリシーの感じられない製品が設計されてしまうのだ。
設計途中で競合製品が出てきたり、市場が変わったりということがある。そうした際、仕様や設計を見直すか、そのまま設計を継続するか。志が明確になっていればその選択は難しいものではない。ところが、志がないと判断を誤ってしまうことになる。
仕様を決める
製品の志が決まったところで、次にその志を満足する仕様を考える。製品の仕様には次のような項目がある。
・一般的な仕様・取得する規格
・信頼性
・デザイン
一般的な仕様とは、例えばテレビの場合「4K 800万画素」のようなものだ。このように数値や言葉で表すものや、キッチン用品で「側面カバーを外して洗浄可能」など、図をもって表すも のもある。そのほか、使用するキーデバイスの名称(例:○◯社製レンズ搭載)や、切替えモード(例:おやすみモード)などもある。取得する規格とは、iPhoneの防水性能IP68やマスクのN95などのことだ。JIS(日本産業規格)で定められているものや、業界標準となっているものがある。信頼性とは、「連続◯◯時間使用可能」や「温度◯◯で使用可能」などを指す。これらの内容の多くは、製品のセールスポイントとなる。
製品購入時の選定基準になるようなセールスポイントは、カタログやメーカーのホームページ、そして製品に同梱される取扱説明書に記載されるため、簡単には変更できない。その記載内容はメーカーに責任があるため、製品化プロセスにおける検証は確実かつ適切に行われなければならない。
デザインも仕様の一つである。デザインは格好良くきれいであれば良いものではなく、そのメーカーのポリシーや製品化の志の意をくんで考えられる。また、製品の仕様や使い勝手も考慮されてデザインが行われるため、多くのデザインの中でもプロダクトデザインは最も難易度が高いとされている。
設計構想は仕様とは別に、設計者のチャレンジを盛り込みたい。その内容は「競合製品から20%軽量化」や「従来製品の3部品を一体化し組立性改善」などがある。これらはカタログなどに記載はされないが、設計者のモチベーションを上げるには重要だ。また、社内の技術レベルを継続的に向上させるうえでも、必要不可欠な内容である。
生産台数(ロット)と生産年数を決める
筆者の知る中には、生産台数と生産年数を決めないで設計を進めているベンチャー企業が多くある。しかし、それではビジネスは成り立たない。理由は、生産台数と生産年数が製品コストを決めるからである。製品コストは製造原価に利益と販売費/一般管理費を上乗せして決まり、製造原価の中でも部品コスト、金型コストの2つは、設計者が管理すべきものである。
部品コストを部品メーカーに見積依頼するときには生産台数と生産年数の提示が必要であり、これらの値によってコストは変動する。板金部品は、金型を作製するか否かを生産台数で判断する必要があり、部品コストは大きく異なる。
目標の部品コストを決める
製品化は限られた資金で行われる。生産台数と生産年数を決めずに製品化を行うことは、資金がいくら出ていくら入ってくるかを計画できていないということだ。製品化を中断したり、倒産したりするベンチャーが多いのは、生産台数と生産年数を決めずに製品化を進めていることにも原因があると考える。
設計コスト、試作コスト、経費(出張費など)の3つは販売費/一般管理費となり、製造原価には含まれないが、最終的には製品のコストに上乗せされる。
金型コストや試作コスト、経費は予算を立て、その範囲内で設計を進めることになる。設計コストは設計人数と設計期間で決まってくるので、決められた人数と日程で設計を進めることが大切だ。設計者にとって最も注意が必要なのは部品コストである。理由は、新規に作製する部品であれば、どのような材質と形状にしてどのように加工するか、カタログ品であれば何を選定するか、また部品点数をいくつにするかなどが、設計次第でいかようにもなるからである。よって、設計者は製品化プロセスの全期間にわたって部品コストを管理しなければならない。部品コストは、一般的に製品コスト(図3)の中で30%以上を占めているため、その管理はとても重要だ。また、それを管理できるのは設計者しかいない。
筆者が以前にかかわったベンチャー企業で、製品が売れれば売れるほど損をしてしまう企業があった。部品コストが高すぎたのだ。設計担当者に部品コストをいつ決めたのか聞いたところ、「いくらになるかわからなかったので、決めないで設計をスタートした。最後の試作の部品仕様で見積もりを取ったらとても高くなっていたが、その時点で設計変更はできなかった」との回答であった。
部品は高価にも安価にも設計できる。部品コストに制約をつけずに設計を進めると、設計者は製品の安全率を高く見込み、高価な部品を設計してしまうのが普通である。例えば、厚み0.5mmの板金で強度が十分なペンケースを設計する際、絶対に壊れないようにと安全率を高めにして厚み1mmで設計する。材料費の高い1mm厚を選んで設計を進め、強度試験などで問題がないことを確認してしまうと、その後にコストダウンで0.5mm厚にすることはできない。もし、次の試作で0.5mmに変更して強度試験を行い問題が発生したら、設計の後戻りになるからだ。よって、部品それぞれの目標コストを最初に決め、そのコストの範囲内で問題が発生しない板金の厚みを選択し、設計しなければならない(図4)。
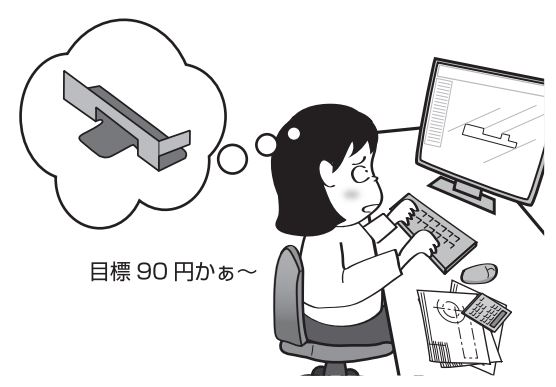
部品コストを管理する
では、いつの時点で部品の目標コストを決めるか。それは企画の後の設計構想のときである。企 画で提示された仕様に沿って設計者は設計構想を考える。筆者の場合は、そのときにイラストを描き、部品構成/部品点数/部品形状/材質を決める。そして、設計者仲間に相談しながら、そのイラストを使って既製の類似部品から部品コストを類推する。それでもわからない場合は購買部や、なじみの部品メーカーにも相談する。
このようにして全部の部品コストの見積もりを行い、作成した部品表でそれらの合計を計算する。このとき、製品本体以外の部品の存在を忘れてはならない。取扱説明書や付属品、そして梱包材などである。これらも合算して製品の合計コストを計算する。ビスなど数のわからないものは100本 など大まかに部品表に入れておく。
部品コストは一般的に、設計を進めるにつれて増えていくものである。理由は、対策部品が発生するからだ。法規制や規格など、製品化にあたって必ず越えなければならないハードルが存在する。製品化の終盤でそれを越えることが難しくなった場合、暫定的に部品を追加することになる。もちろん、それが恒久になることもある。そのような部品が発生する場合に備え、10%程度の余裕は必要だ。
最初の企画の段階で目標コストを提示するが、設計構想でその目標に入らなかった場合は、目標コストを上げるか、コスト調整をする。コスト調整の方法は、仕様を満足しながら部品コストを下げることから考えていく。塗装レスや印刷を刻印にする、安価な材料の選定、複数部品の一体化(組み立てにくくなる場合もある)、などといった方法がある(図5)。
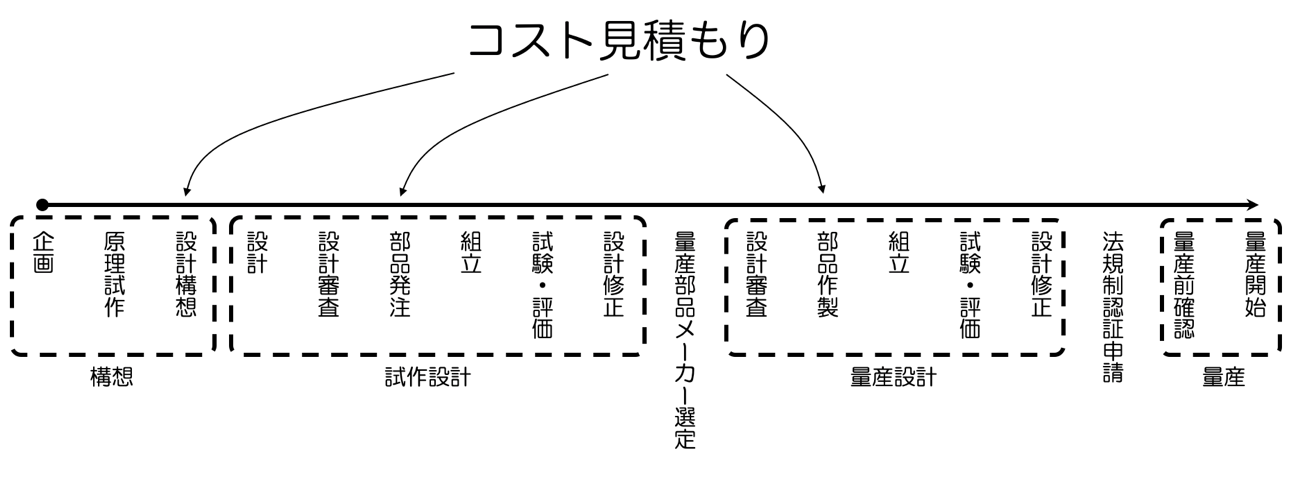
部品コストは設計を進めるにつれて変わるものだ。よって、試作のための3次元データや図面が出来上がるたびに見積もりをして、部品表のコストを更新していく必要がある。これは設計者の大切な業務の一つだ。
ビジネスの成否は志を元に、いかに綿密に作戦を立てるかで決まってくると考える。だからこそ、市場の変化に柔軟に対応ができる。製品化においては、この作戦が企画・設計構想になるのだ。
著者略歴
ロジ 小田 淳(おだ あつし)
製品化のイロハコンサルタント。上智大学理工学部機械工学科卒。ソニーに29年在籍し、プロジェクタなど15モデルを製品化。ベンチャーを支援する中で、材料費が高すぎ売っても損する、輸送中に壊れる、法規制がわからないなど、製品化のハードルを越えられない企業に出会う。企画から設計〜試作〜検証〜量産の全プロセスにおける、安全性(法規制)・信頼性・製造性・コスト管理などの手法をコンサルと研修で伝える。
雑誌紹介
機械設計 2021年6月号 Vol.65 No.7 【特集】これだけは押さえておきたい!手戻りをなくすプラスチック製品設計の勘所
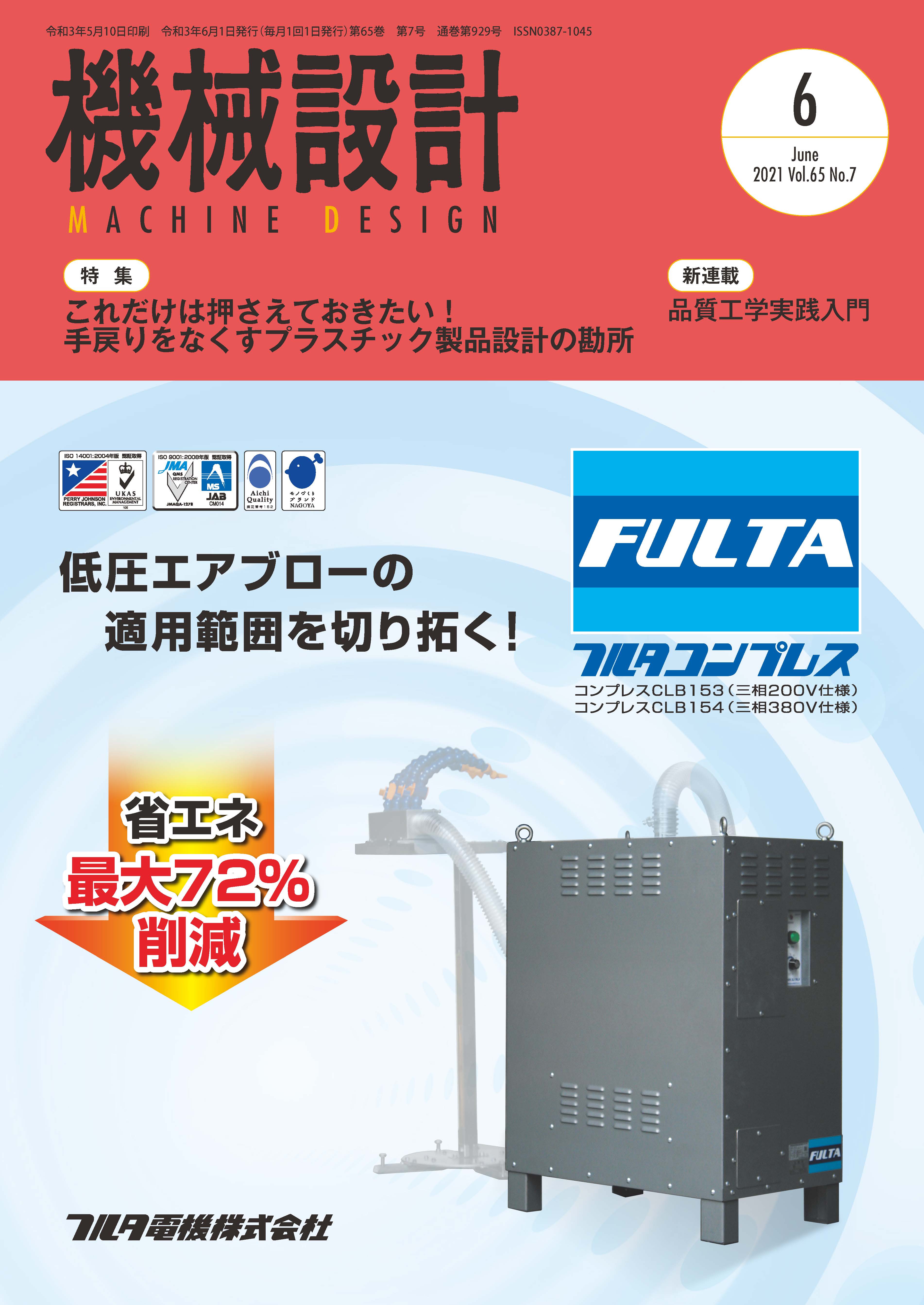
雑誌名:機械設計2021年6月号
判型:B5判
税込み価格:1,540円