トヨタは「ホワイトカラーの無駄取り」をこうやって実践している
実務責任者が語る抑えておきたいポイント
トヨタ自動車の「トヨタ生産システム(TPS)」をご存じの方は多いだろう。この生産方式は「徹底して無駄を出さない」「段取りをしっかりと組むんで合理性を追求する」ことがキモだ。
同社は生産現場だけでなく、それ以外のいわゆるホワイトカラーの職場でも「無駄取りと段取り」を徹底した「自工程完結型」の仕事の進め方に取り組んでいる。
事業のグローバル化や技術の進展で、以前にも増して無駄の削減や人材育成、士気向上が難しくなっている中でも、それらの題をクリアする一つの切り札になるとしている。
TPSは「必要なものを必要な時に必要なだけつくって運ぶ」という仕組み。部品がどこでどれだけ使われたかが書いてある「かんばん」を駆使して生産性を高める「ジャスト・イン・タイム」と、生産工程内で異常が発生したら設備がそれを検知して自ら止まり、不良品づくりを未然に防ぐ「自働化」という二つの概念を組み合わせている。これらにより、無駄を徹底的に排除して、求められる分の製品を確実に届ける体制を実現させている。
そこで必要となるのが「段取りをしっかりと組む」ことだ。作業に入る前に入念に作戦を立てることで、建てた通りに作業を進めれば良い結果を出すことができるし、作業自体が行き当たりばったりにならない。
もし途中でミスがあっても、振り返って原因を探せて、改善につなげられる。仕事の質が上がるだけでなく、作業の無駄や、やり直しが減るため仕事に自信が持て、モチベーションも高まる。
段取りを徹底する方法は、同社は営業や広報など、生産現場以外の職場でも拡大している。「部品を取ってくる」「工具を使って組み付ける」といった生産現場と異なり、ホワイトカラーの職場は工程がなかなか目に見えにくく、自分の仕事の進捗(しんちょく)状況も見えづらい。
その状況に「段取り」を導入し、充実させることで、目に見える形にするのだ。業務品質改善部自工程完結推進グループ長の江口真氏は「ホワイトカラー職場の仕事は『意思決定の連鎖』。自分の取り組んでいる仕事の善しあしが自分でわかるようになる(自工程完結させる)ことで、無駄がなくなり質も高まる」としている。
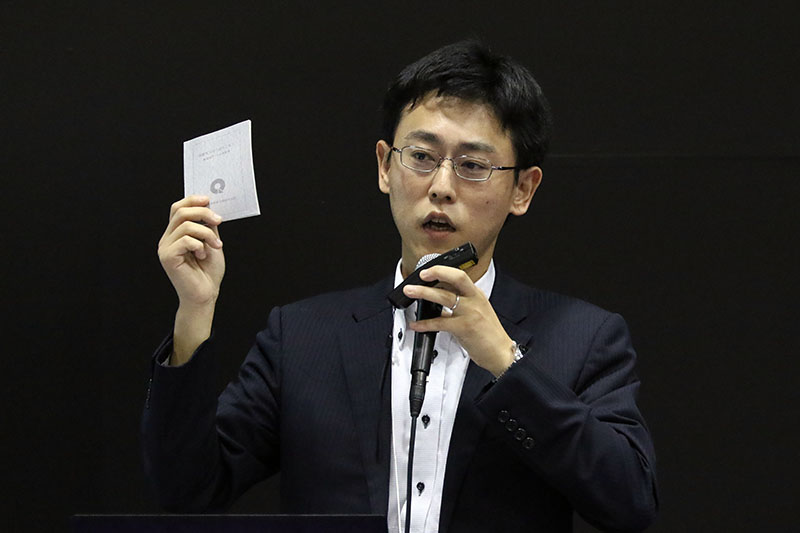
江口氏
仕事の進め方で「PDCAサイクル」というモノがあるのはご存じの方も良いだろう。Plan(計画)を建て、Do(判断して実行)し、Check(進め方のどこに問題があるか振り返り)をし、Act(振り返りを伝承)する一連の流れのうち、最も重要なのが「P」で、「目的」「目標」「アウトプット」の三つに注意を払うべきだと江口氏は力説する。
「あらゆる業務で失敗する人は、ゴールから逆算せず、どんな方法を使うかをまず考えがちだ」。ゴールを設定してから、そこに至るまでの道筋を考え、やるべき仕事や携わってほしい関係者、必要な作業時間を洗い出す。必要となる情報や判断基準を事前に集め、取り組む。
「この三つがズレていなければ、大きなミスは起きにくい」とし、以降のDCAは、Pで立てた段取りに沿って動けば生産性の向上が見込めるというわけだ。段取りを重視するのには、激変し続けるビジネス環境の下でもしっかりと結果を残すためだ。
トヨタは2000年代以降世界での生産台数が拡大し、事業のグローバル化が進んだ。それに伴い、海外との人の往来も活発になった。でも業務の拡大に比例するように人材を増やし続けるのは非現実的であり、業務の引き継ぎや情報共有などを通して各個人の知見をどのように残していくかが課題となっていた。
加えて、仕事のそのものの環境変化も見過ごせなかった。ITの進展などに代表される技術の高度化や仕事の高速化、デジタルツール化などが進み、10年前とは仕事の質も環境も異なっている。業務が複雑化する中で、仕事の無駄を増やすわけにも、質を落とすわけにもいかない。
そこで、自工程完結の考え方がホワイトカラーにも波及されるようになった。江口氏は「自分の仕事の状況が分かると、クオリティーを保つことにもつながる。なぜ今自分がこの仕事をしているかが分かるとやる気も出るようになる」としている。
考え方を徹底させようと、同社は、日常生活のワンシーンを題材にした四コママンガを通じての自工程完結に取り組むきっかけ作りなどの啓発活動、方法論を学ぶ研修活動、組織的に工程実践を支援する活動、それらの活動ができる体制整備を進めている。絶えず改善しながら、生産性向上のための取り組みを今後も続ける。
(文=山田諒)
同社は生産現場だけでなく、それ以外のいわゆるホワイトカラーの職場でも「無駄取りと段取り」を徹底した「自工程完結型」の仕事の進め方に取り組んでいる。
事業のグローバル化や技術の進展で、以前にも増して無駄の削減や人材育成、士気向上が難しくなっている中でも、それらの題をクリアする一つの切り札になるとしている。
TPSは「必要なものを必要な時に必要なだけつくって運ぶ」という仕組み。部品がどこでどれだけ使われたかが書いてある「かんばん」を駆使して生産性を高める「ジャスト・イン・タイム」と、生産工程内で異常が発生したら設備がそれを検知して自ら止まり、不良品づくりを未然に防ぐ「自働化」という二つの概念を組み合わせている。これらにより、無駄を徹底的に排除して、求められる分の製品を確実に届ける体制を実現させている。
そこで必要となるのが「段取りをしっかりと組む」ことだ。作業に入る前に入念に作戦を立てることで、建てた通りに作業を進めれば良い結果を出すことができるし、作業自体が行き当たりばったりにならない。
もし途中でミスがあっても、振り返って原因を探せて、改善につなげられる。仕事の質が上がるだけでなく、作業の無駄や、やり直しが減るため仕事に自信が持て、モチベーションも高まる。
生産現場と違って仕事の進捗が見えにくい
段取りを徹底する方法は、同社は営業や広報など、生産現場以外の職場でも拡大している。「部品を取ってくる」「工具を使って組み付ける」といった生産現場と異なり、ホワイトカラーの職場は工程がなかなか目に見えにくく、自分の仕事の進捗(しんちょく)状況も見えづらい。
その状況に「段取り」を導入し、充実させることで、目に見える形にするのだ。業務品質改善部自工程完結推進グループ長の江口真氏は「ホワイトカラー職場の仕事は『意思決定の連鎖』。自分の取り組んでいる仕事の善しあしが自分でわかるようになる(自工程完結させる)ことで、無駄がなくなり質も高まる」としている。
Pで大事な「目的」「目標」「アウトプット」
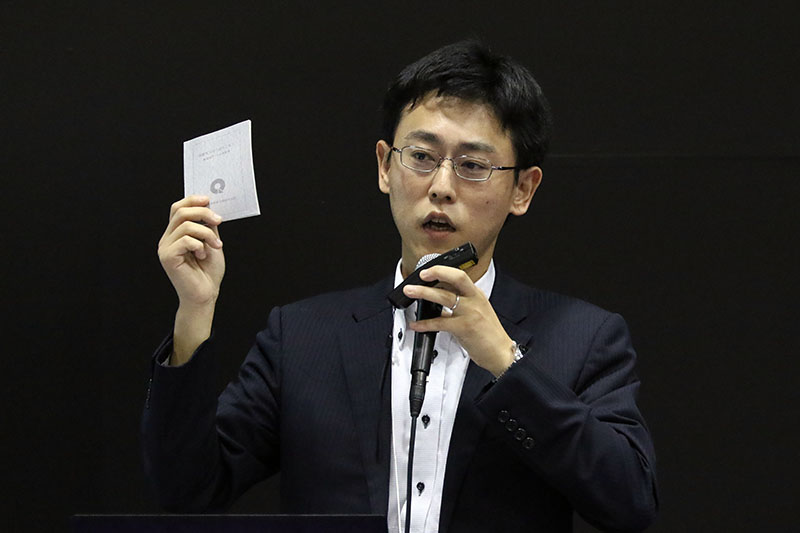
仕事の進め方で「PDCAサイクル」というモノがあるのはご存じの方も良いだろう。Plan(計画)を建て、Do(判断して実行)し、Check(進め方のどこに問題があるか振り返り)をし、Act(振り返りを伝承)する一連の流れのうち、最も重要なのが「P」で、「目的」「目標」「アウトプット」の三つに注意を払うべきだと江口氏は力説する。
「あらゆる業務で失敗する人は、ゴールから逆算せず、どんな方法を使うかをまず考えがちだ」。ゴールを設定してから、そこに至るまでの道筋を考え、やるべき仕事や携わってほしい関係者、必要な作業時間を洗い出す。必要となる情報や判断基準を事前に集め、取り組む。
「この三つがズレていなければ、大きなミスは起きにくい」とし、以降のDCAは、Pで立てた段取りに沿って動けば生産性の向上が見込めるというわけだ。段取りを重視するのには、激変し続けるビジネス環境の下でもしっかりと結果を残すためだ。
自工程完結の考え方が波及
トヨタは2000年代以降世界での生産台数が拡大し、事業のグローバル化が進んだ。それに伴い、海外との人の往来も活発になった。でも業務の拡大に比例するように人材を増やし続けるのは非現実的であり、業務の引き継ぎや情報共有などを通して各個人の知見をどのように残していくかが課題となっていた。
加えて、仕事のそのものの環境変化も見過ごせなかった。ITの進展などに代表される技術の高度化や仕事の高速化、デジタルツール化などが進み、10年前とは仕事の質も環境も異なっている。業務が複雑化する中で、仕事の無駄を増やすわけにも、質を落とすわけにもいかない。
そこで、自工程完結の考え方がホワイトカラーにも波及されるようになった。江口氏は「自分の仕事の状況が分かると、クオリティーを保つことにもつながる。なぜ今自分がこの仕事をしているかが分かるとやる気も出るようになる」としている。
考え方を徹底させようと、同社は、日常生活のワンシーンを題材にした四コママンガを通じての自工程完結に取り組むきっかけ作りなどの啓発活動、方法論を学ぶ研修活動、組織的に工程実践を支援する活動、それらの活動ができる体制整備を進めている。絶えず改善しながら、生産性向上のための取り組みを今後も続ける。
(文=山田諒)
ニュースイッチオリジナル
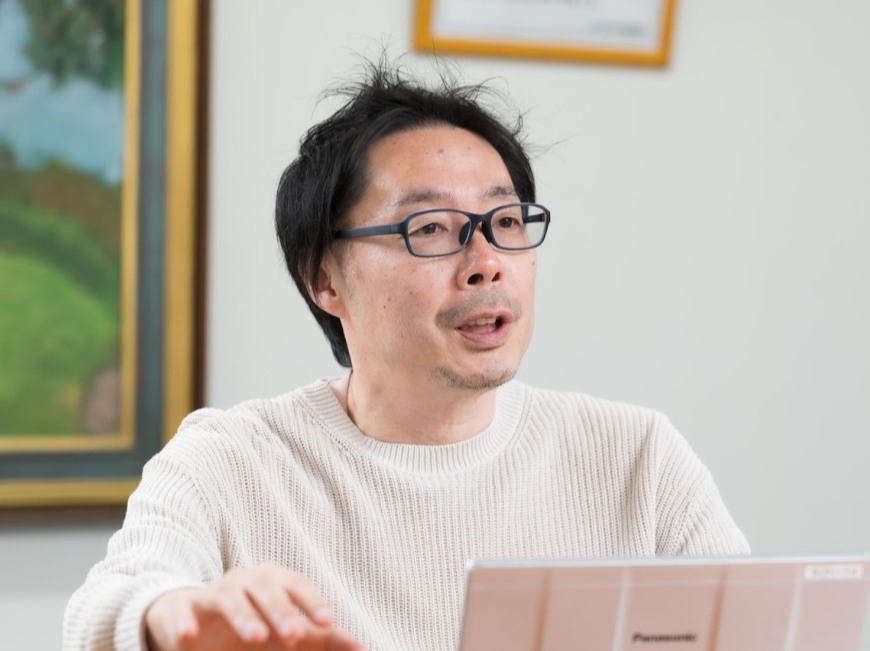