9割以上の仕事が道外から!金型技術を武器に航空・宇宙分野へ
キメラは金型部品を中心とした精密機械加工を手がける。μm単位の高精度と短納期対応により、北海道室蘭市にありながら、9割以上の仕事を道外の顧客から受注。2004年には射出成形金型の設計・製作にも参入し、業務の幅を広げつつある。
同社が力を入れるのが新規顧客の開拓だ。2020年5月に航空・宇宙関係の品質マネジメントシステム「JISQ9100」の認証を取得し、金型部品の精密加工で培った技術やノウハウを航空・宇宙の分野でも活かそうと取り組み始めた。また、強みである短納期対応をより強化するため、加工現場でもさまざまな改善を続けている。新規顧客開拓を主導する髙田麻世さん、現場のレベルアップを推進するマシニングセンタ(MC)担当の藤原健吾さん、形彫り放電加工機担当の伝里雄士さんを取材した。

同社は創業者である前社長が研磨機1台で立ち上げた。超硬合金の研磨加工を得意とし、超硬が使われることの多いプレス金型部品を主に扱っていたが、2000年以降プレス金型部品加工の多くが中国に流れると、代わって射出成形金型部品の加工を手がけるように。それに伴い、研磨を主体とした加工から、MC や形彫り放電加工による3次元加工へと要素技術を変え、現在に至っている。国内2工場とマレーシア・クアラルンプールにある子会社の工場、協力会社を合わせて月産8,000点の部品を製作しており、その9割が金型部品である。
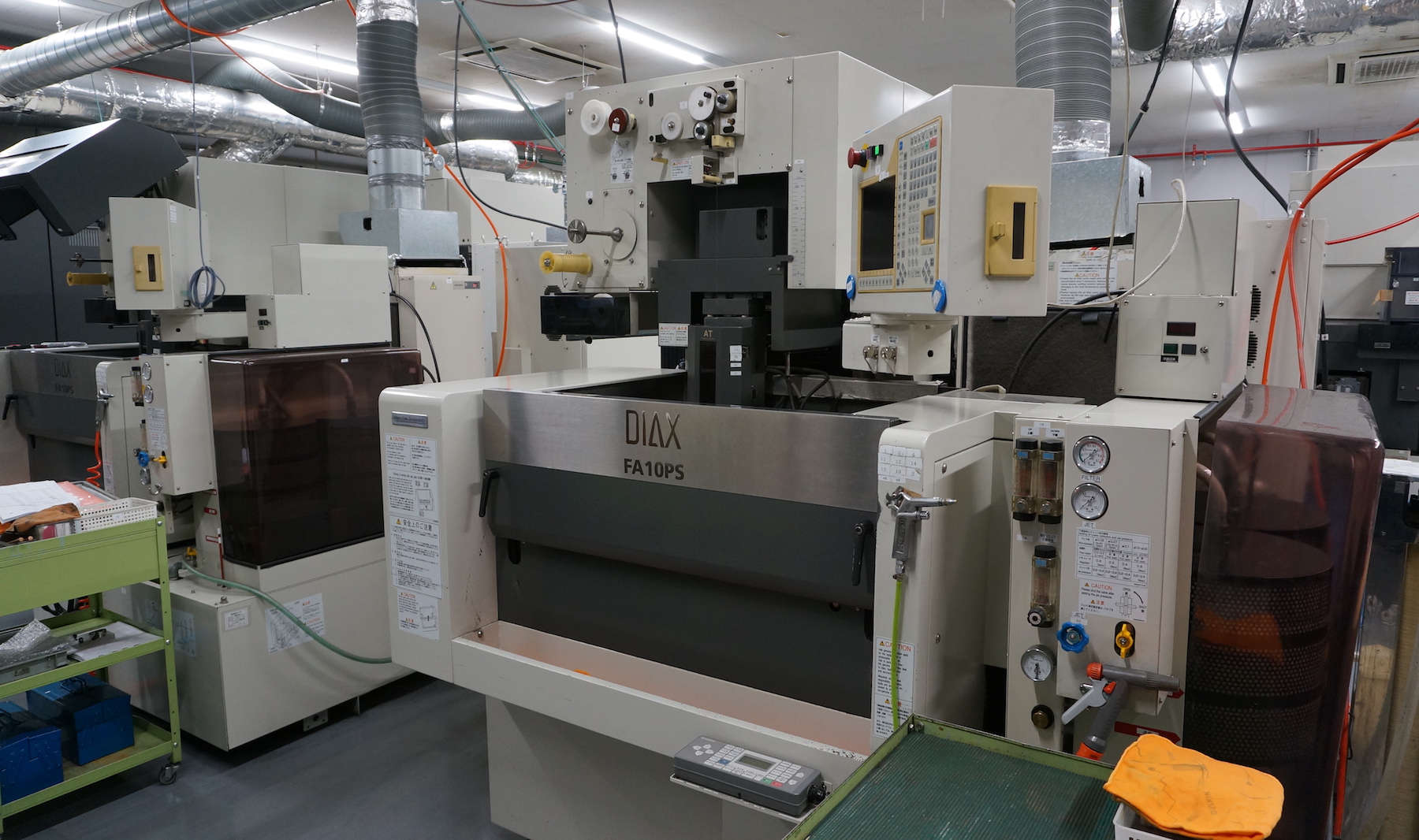
金型部品を主力とする同社だが、藤井徹也社長は「今後は金型にこだわらず、新しい分野を開拓したい」と話す。製作する射出成形金型部品の多くは車載コネクターといった自動車関連。業界の先行きを考えたとき、「現状と異なるターゲットに営業して、設備もそのターゲットに合わせていかないと生き残れない」(同)との危機感がある。そこで、①JIS Q9100の認証取得、②社内の原価管理の強化、③展示会でのアピールの強化、の3つを目的として2019年に「経営企画室」を立ち上げた。①はすでに達成しており、室長を務める髙田さんは主に展示会での自社技術のアピールに力を注いでいる。
顧客の目を引く展示品を考案
髙田さんは通っていた商業高校で「性格的に製造業が向いているのでは」とキメラの工場見学を勧められたのをきっかけに2008年入社。製造管理部門に配属され、工程管理システムを使って機械加工現場に図面を受け渡す業務を受けもった。
金型部品加工はMC 加工や放電加工、研磨など複数の工程があり、その順序を決めるのは製造管理部門の役目。図面を渡す順序を間違えると現場で待ち時間が発生してしまうため、図面を見ながら、「次はMC」、「次は形彫り放電加工」と頭の中で工程を必死に組み立てながら仕事にあたった。「すべての工程を把握しないと仕事にならないため、最初は工場内をぐるぐる回りながらいろいろな人に質問していました」(髙田さん)。その後、マレーシア工場との調整業務を経て現在の部署に配属された。
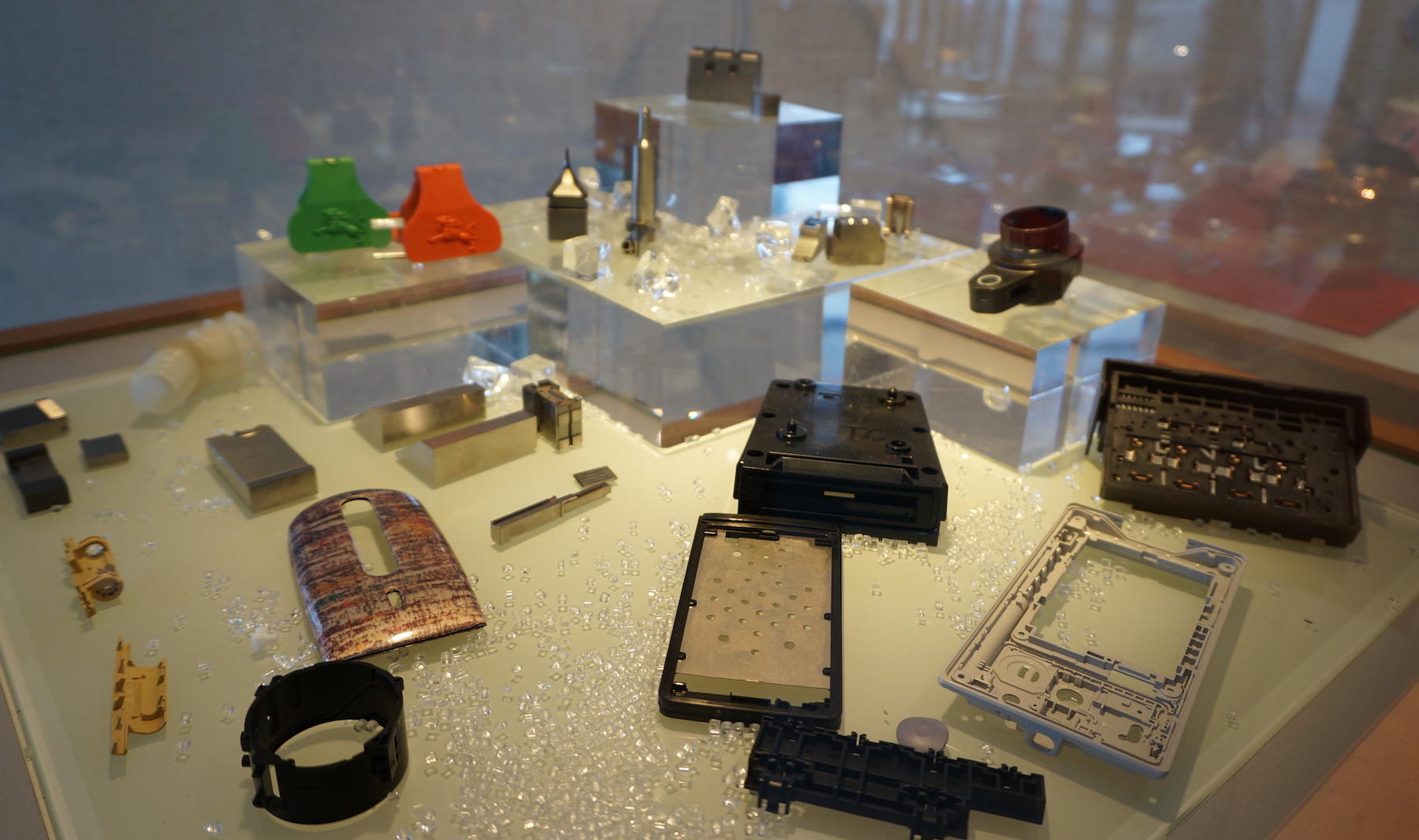
展示会への出展は自社技術をアピールして、新規顧客の獲得につなげる絶好のチャンスだ。半面、同社では展示する加工サンプルやその見せ方がワンパターンになっており、顧客の目を引きつける展示が課題だった。「展示会場を歩くお客さまに足を止めてもらうには、『なに?コレ』と驚いてもらうことが大事。足を止めてもらえれば、『こういう加工ができる会社です』と話しを続けられます」(髙田さん)。そこで、新しい加工サンプルのアイデアを出し、加工部門の協力を得て展示品に加えている。
一例が、厚み0.05mm の卵の殻に切削加工で獅子の絵を削り出したサンプルである。ソディック製の高速リニアMC「HS430L」と半径R 0.1mm の工具を使用。卵の殻をスキャニングして曲面をデータ化し、そのデータをCAMに取り込んで加工軌跡を生成した。卵の殻のMCへの固定方法にも独自の工夫がある。こうしたサンプルを展示することで、アクセサリーメーカーのような金型以外の業種から声がかかるケースも出始めた。
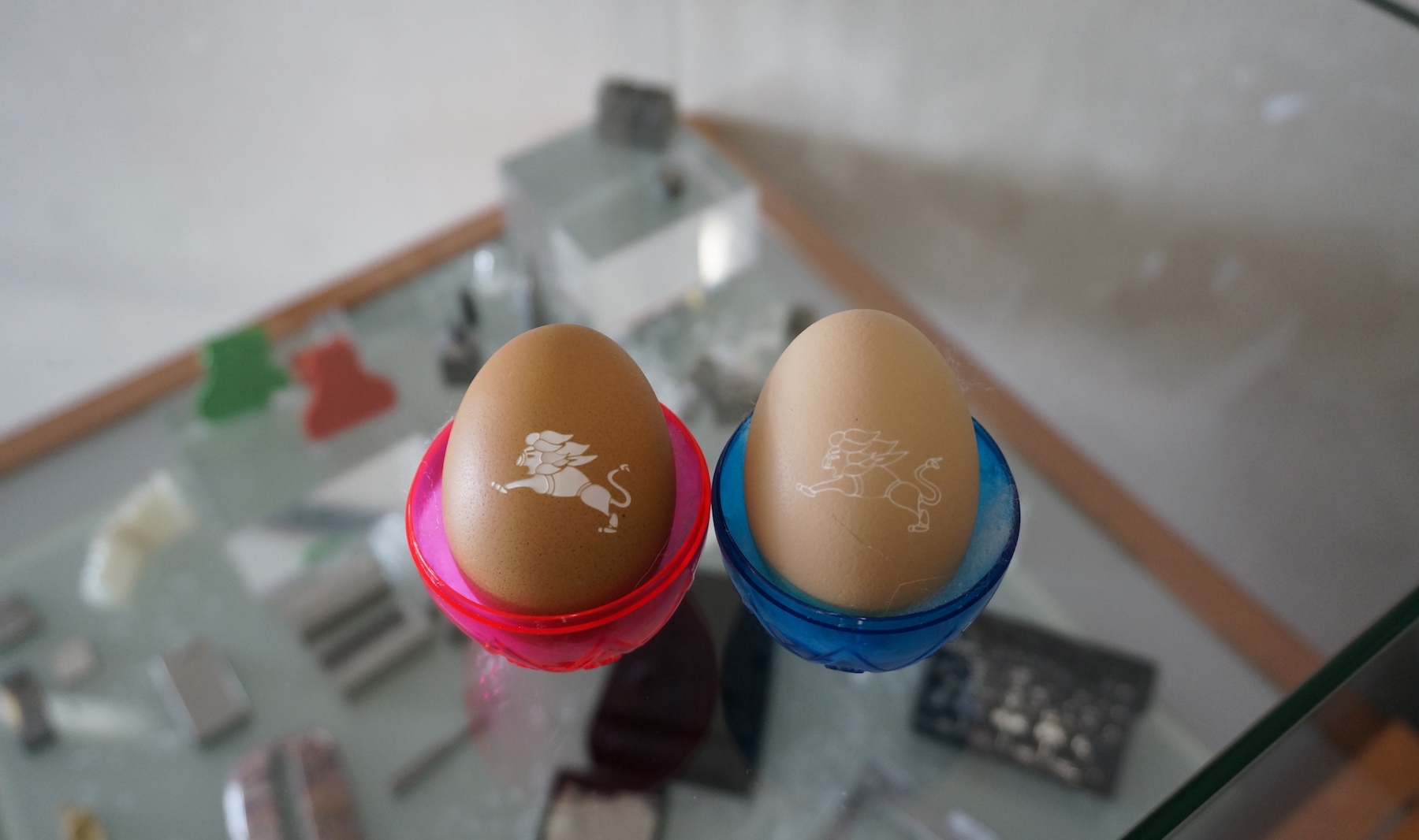
今の課題は、JIS Q9100認証を活かした航空機関連での受注獲得だ。小物部品を主に扱ってきた同社にとって、大物・長尺部品のイメージが強い航空機関連の仕事を受注するのは容易ではない。それでも髙田さんは「業界のニーズを勉強して、当社からアピールしていきたい」と意欲的だ。北海道では、室蘭市に製造拠点を置く日本製鋼所が航空機構造部材用製品の新工場を竣工したことを受け、室蘭市や道経済産業局などが航空機産業を後押ししている。精密加工で培った技術やノウハウを活かせる仕事を見つけられるか。これからが正念場だ。
自衛隊からモノづくりへ
同社の国内2工場はいずれも室蘭市内にある。本社工場はワイヤおよび形彫り放電加工と研削加工を、第二工場はMC加工や旋盤加工のほか金型設計、成形トライを担う。同社は自動化ロボットや工程管理システムなどを活用した短納期対応を強みとしているが、さらに磨きをかけようと取り組んでいる。
藤原さんは2011年に中途入社した。兵庫県出身で、陸上自衛隊員として東千歳駐屯地(北海道千歳市)に勤務していたときに転職を考え、もともと興味のあったモノづくり企業に応募した。夏涼しい北海道の気候が気に入り、地元に戻ることは考えなかったという。
入社後は一貫してMC加工を担当している。最初は右も左もわからず、先輩社員について図面の読み方からセット方法、MCの操作方法、測定機の使い方などを学んだ。今では7人いるMCオペレーターの中で2番目に長い経験者となり、後輩に教える機会も増えている。「自分のようにまったくの畑違いから来る方もいるので、どう説明すれば理解してもらえるか悩みながら教えています。ただ、自分も苦労したので、『ここでつまずくだろう』と気づける点は利点ですね」(藤原さん)。
MC加工では、加工のスピードアップが課題だ。同社のような部品加工を主力とする業種では、短い時間でどれだけの仕事をこなせるかが利益を左右する。そこで藤原さんは、「可能な限り1度の加工で狙いの寸法を出す」ことを目標にしている。寸法精度の要求が厳しいほど、少しずつ狙いの寸法に近づける「追込み加工」をするのが一般的。だが、それでは加工にかかる時間が長くなる。藤原さんは工具メーカーの協力を得て工具1本1本の工具径データを取得。補正値として加工に反映させ、厳しい寸法精度でも1度の加工で仕上げられるよう取り組んでいる。これにより、20時間超の加工であれば2~3時間の短縮が可能だ。「今は±10μmの寸法精度であれば1度で狙いにいきます。より厳しい精度でも実現できるよう、取り組んでいます」(藤原さん)。
段取り時間の圧縮に挑む
旭川市出身の伝里さんは、スマートフォンやパソコンのディスプレイに使われる材料や部品を製造する企業での勤務を経て2017年に入社した。工業系の高等専門学校で学んだものの、任された形彫り放電加工は見るのも聞くのも初めてだった。「油の中でどんな風に加工が進み、どういう原理で加工しているのか?」を知ろうと、専門書を漁ったり、上司を質問攻めにしたりしていたという。形彫り放電加工機は夜間や休日に長時間動かすことが多く、加工機を動作させるためのプログラムの入力を間違えても、その間違いに気づきにくい。「朝出社して、加工されたものを見て真っ青になったこともあります。数値をたくさん入力するので、とにかく入力ミスをしないように心がけています」(伝里さん)。
MCと同様に放電加工でもスピードアップが課題。伝里さんが目をつけているのは段取り時間だ。形彫り放電加工では、加工したものを加工機から外して寸法を測定し、寸法を満たしていなければ、再び加工機に載せて修正するという作業がある。この作業にかかる時間を測定したところ、ベテランに比べて若手は4~5倍と大きな差が出た。そこで、定期的にベテランから技術やノウハウについての教えを受け、形彫り放電加工チーム全体のレベルアップを図っている。
伝里さん自身も経験5年未満で、ベテランとのレベルの差を痛感している。段取りを効率化するために意識しているのは「加工内容をあらかじめしっかり把握すること」。求める形状が複雑になると、1つのワークに対して100本もの電極を使う。当然、どの電極でどの形状を加工するのかを事前に把握しておかなければ、修正が必要になったときもすぐに対応ができなくなる。「例えば、『組み合わさる相手部品が狙いに対して残り気味だから、こちらは逃がし気味に加工しないと』とか。細かいことですが、頭の中であらかじめシミュレートしておくことで、必要なときに素早く動ける。大事なのは、普段の業務の中でこうした“考える時間”を確保できるよう、効率良く動くことです」(伝里さん)。
力を合わせて技術力をアピール
展示会での「アイキャッチ(人の注意を引きつけること)」に力を入れる髙田さんは、現場に無理難題を頼むことも多い。新しく考案した加工サンプルには、0.1mmの薄肉をMCとワイヤ放電加工機で削り出した「クモの巣」、MCで形をつくり精密研磨で刃をつけた「極小ハサミ」などがあり、藤原さんは、「『なんだコレ?』と思うときもある(笑)」と話す。
中空のピンを複数立てた微細形状サンプルを担当した伝里さんは、「普段は手がけない加工で挑戦し甲斐があった」と振り返る。忙しいときに頼まれると負担に感じることもあるが、2人とも「会社のアピールにつながるなら」と前向きに捉えている。
航空・宇宙分野を含む「夢のある仕事」(藤井社長)の獲得を目指す同社。その基盤となる精密加工のブラッシュアップに向けて、藤原さんは「部門の底上げにつながるよう若手を育成したい」、伝里さんは「ボトルネック工程をサポートできるマルチな技術者を目指したい」と力強く話す。また、新型コロナウイルス感染症拡大の影響で予定されていた展示会が軒並み中止となる中、髙田さんはWeb展示会への出展準備を進めている。掲載できる写真や動画の点数に制限があり、どれだけ顧客にアピールできるかは未知数だ。それでも、「お客さまとのつながりを保つために何ができるかを考えて、中心となって実行に移したい」と話している。
会社概要株式会社キメラ
所在地:北海道室蘭市香川町24-16
電話番号:0143-55-5293
代表取締役:藤井徹也
資本金:2,800万円
創業:1988年
従業員数:116名
事業内容:各種金型部品加工、精密金属機械加工、射出成形金型の設計・製作・試作
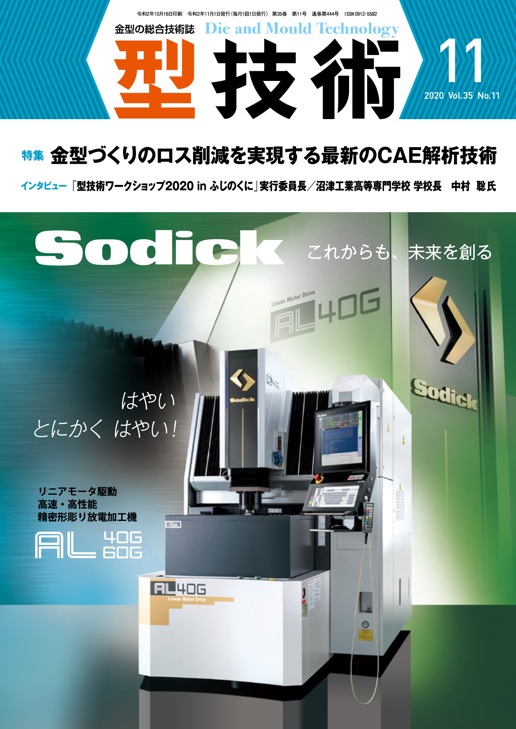
雑誌名:型技術 2020年11月号
判型:B5判
税込み価格:1,540円
内容紹介
型技術 2020年11月号 Vol.35 No.11
【特集】
金型づくりのロス削減を実現する最新のCAE解析技術
コンピュータを用いて仮想の試作・試験を行うCAE解析は、難易度の高い部品成形をサポートする重要なツールです。一方、CAE解析はソフトを導入したからといってすぐに効果を出せるわけではありません。CAE解析を使った事前予測により、試作回数の削減や不良発生の防止を実現するには、解析結果をいかに現実と近いものにできるかがポイントとなります。
本特集では、高精度な事前予測を可能にするCAE解析の最新技術動向と、CAE解析ソフトを使いこなして金型づくりや部品成形のロス削減につなげているユーザーの事例を紹介します。
Amazon
Rakutenブックス
Yahoo!ショッピング
日刊工業新聞ブックストア