その名は「月光ドリル」 鳥取の中小企業が挑む逆転の物語
三日月状の刃先
「月光ドリル」という変わった名前のドリルがある。ドリルの刃先を三日月の独自形状にすることで、切れ味に優れ、切削性能を向上させた。極めて加工の難しいステンレス鋼などの難加工材に容易に孔を空けることができる。この月光ドリルを開発したのが1980年創業のビック・ツール(鳥取県日吉津村)。2012年の開発以来、引き合いは国内外で広がり、同社を代表する製品に育て上げた。創業者の新井高一社長は、「ステンレス鋼に孔は空きにくいという常識を覆しました。簡単に空けられるので、摩擦抵抗が少なくて済み、電力消費量も約30%抑えられます。二酸化炭素の排出量削減に貢献し、国連の『持続可能な開発目標(SDGs)』の実現にも合致するはずです」と自信を見せる。(取材・小川淳)
ステンレス鋼が簡単に
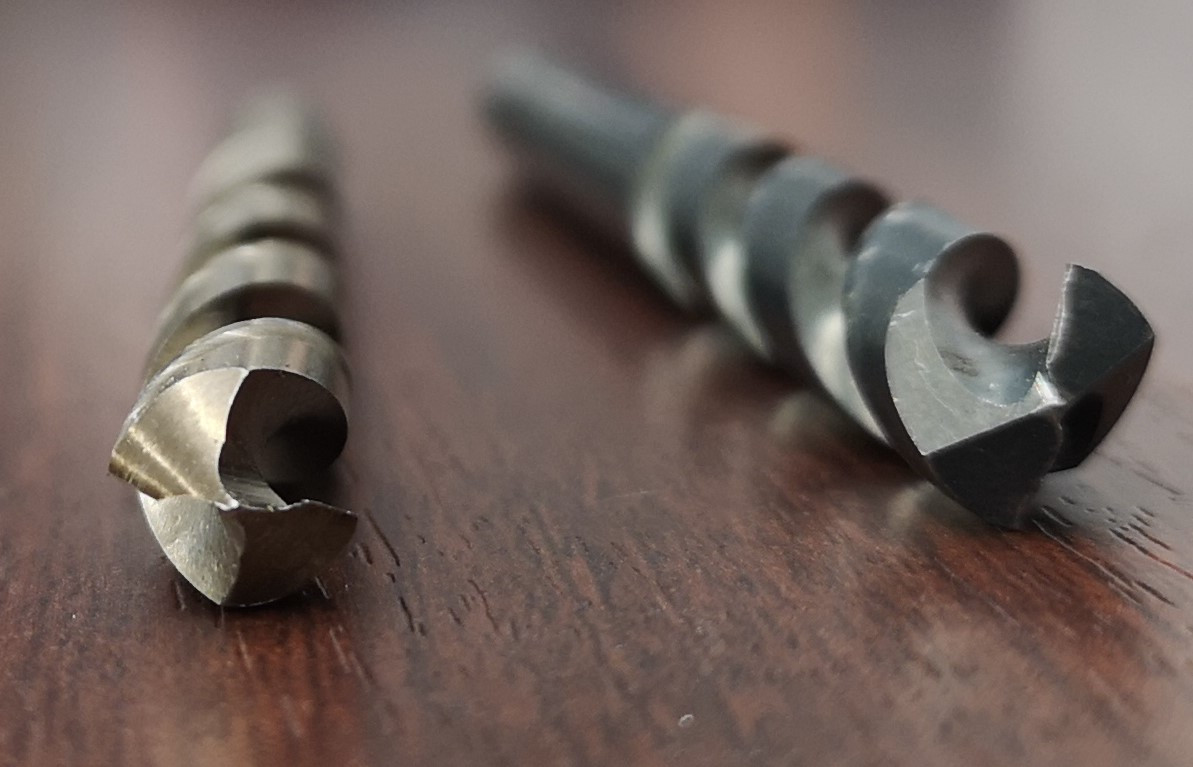
月光ドリルと一般的なドリルと材質は同じだという。違いは、刃先だけだ。ステンレス鋼と接地するドリル先端の刃先形状が三日月のように反っている。普通のドリルはここがほとんどまっすぐになっている。また、普通のドリルが材料を「削る」のに対し、月光ドリルは「切る」感覚に近い。
その証拠に木をカンナで削った時と同様に、切りくずがつながりながら連続して出るようになっており、その切れ味が伝わる。「草を刈る鎌がドリルの先端にあると思ってください」と新井社長は説明する。
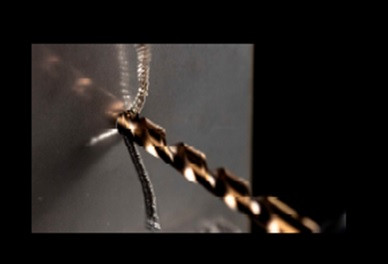
ステンレス鋼への孔空けの比較試験では、切削時間は10分の1程度で済むという。また、加工した際に生じる出っ張り、いわゆる「バリ」がほとんど出ず、真円に近い孔を空けられることも現場で重宝される理由のひとつである。
新井社長は、「モノづくりの基本の一つは孔を空けることです。一つの孔を空けるのにどれだけのコストを削減できるのか問われています。月光ドリルが普及すれば、日本のモノづくり現場で、現在大きな課題になっている生産性がきっと向上するはずです」と力を込める。事実、月光ドリルはその優れた技術が認められ、2019年の科学技術分野の文部科学大臣表彰を受賞した。
現在、月光ドリルは機械加工用だけでなく、整形外科用やインプラントの歯科医療用へと種類を広げている。骨に孔を空ける医療用ドリルは、普通のドリルなら骨の表面ですべってしまい、斜めに孔を空けることができなかったが、切れ味の鋭い月光ドリルなら斜めの孔空けも可能だ。また、摩擦熱が少ないため、熱で骨が壊死する懸念もない。
アイデアは日本海の荒波を見て
ビック・ツールは、板金加工の職人だった新井社長が「自分の手でモノづくりをしてみたい」との念願を叶え、起業した。もともとは自動車用の修理工具を製造しており、その後、自動車の修理工具のメンテナンスに使うドリル研磨機などの製造に乗り出した。一方、2010年頃から自動車の車体に衝突安全性の高いボディーの導入が進み、車体用鋼板が一層硬くなってきた。鋼板に孔を空ける需要の拡大を見越し、新しいドリルの開発に着手した経緯がある。
月光ドリルが完成したのは2012年。刃先が反る三日月状にするアイデアは、新井社長が「日本海を見ながら砂浜を歩いているとき、打ち寄せる波の形状を見て、『これを刃先につけてみよう』思いついた」という。
最初はまったく売れず
ただ、実際に製品化をしてみたものの、当初はまったく売れなかったという。新井社長と二人三脚で月光ドリルを育て上げてきた新井義一専務は、「地道などぶ板営業の連続です」と振り返る。性能には絶対の自信があったが、価格は普通のドリルより、「1.3倍ほど高くなる」(新井社長)。さらに東南アジアなどの製造現場では中国産のドリルが市場を席巻しており、月光ドリルはそれらの安価なドリルに比べさらに5倍から10倍も割高となる。
耐久性の高い月光ドリルならランニングコストの差で導入コストの差は十分補えるのだが、「納入実績のないところは厳しい」(新井専務)。国内外の展示会に出かけたり、客先に現物を持ち込んで実際に孔を空けることを繰り返した。ホームセンターでの実演も数え切れないほど足を運んだという。「切るという行為を目の前で見せないと、お客さんは信じてくれませんから」と新井専務。
地道な活動が功を奏し、今では医療・歯科用も併せて年間約100万本を製造する規模までになった。国内の大手重工メーカーに納入したほか、全国のホームセンター約2500店舗で取り扱い実績がある。韓国、台湾、タイなどにも輸出を果たしており、海外での展示会での出展を機に、大手航空機メーカーに試作品を納入するまでになったという。「日本のモノづくりの強さを認めてもらった」(新井専務)。
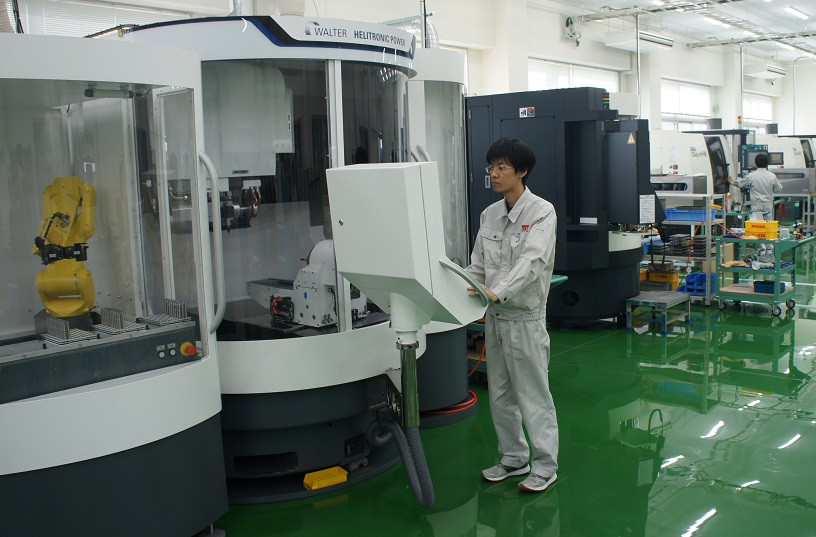
医師との出会いがきっかけに
今年7月には本社隣接地で医療用ドリルの製造や歯科用ドリルの研究開発をする第2工場の稼働を始めた。医療用ドリルが成功するきっかけになったのは、ある著名な整形外科医との出会いだったという。医療用の展示会で整形外科用のドリルの実演をしていたところ、その外科医の目にとまった。性能の高さを気に入ったその外科医は、自らの執刀でも使用し、業界での売り込みを後押ししてくれたという。新井専務は「その先生からは『これでたくさんの命が救われる。開発を続けてください』とエールを送られた」と嬉しそうに語る。
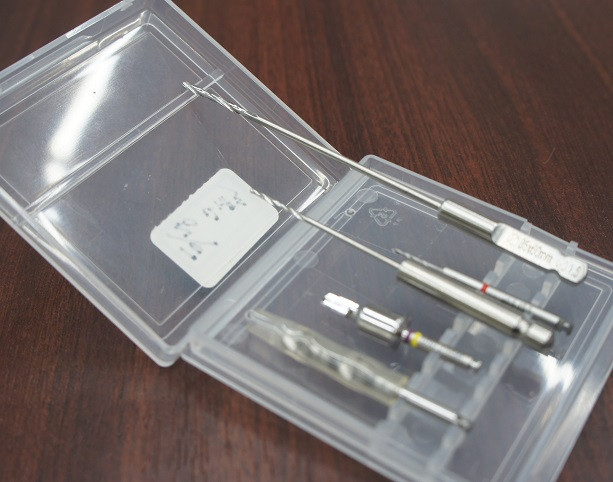
ビッグではなく「ビック」のこだわり
順調に成長してきた同社だが、「成長の速度はまだまだ遅い。認知度、ブランド力がまだ足りないのがネック」(新井社長)と自認する。大手企業への納入で着実に実績を挙げているものの、ドリルに対する固定観念を覆すのは容易でない。
社名に冠した「ビック」は「BIG(ビッグ)」ではなく「BIC(ビック)」と表記することにもこだわりがある。新井専務は「ビッグになるには濁点が一つ足りません。そういう謙虚で常に挑戦し続ける姿勢がこの『ク』には込められています」と明かす。
オンリーワンの技術を翼に、鳥取から全国、そして世界へと羽ばたこうとしているビック・ツール。生産現場や医療の世界を大きく変える日はそう遠くない。
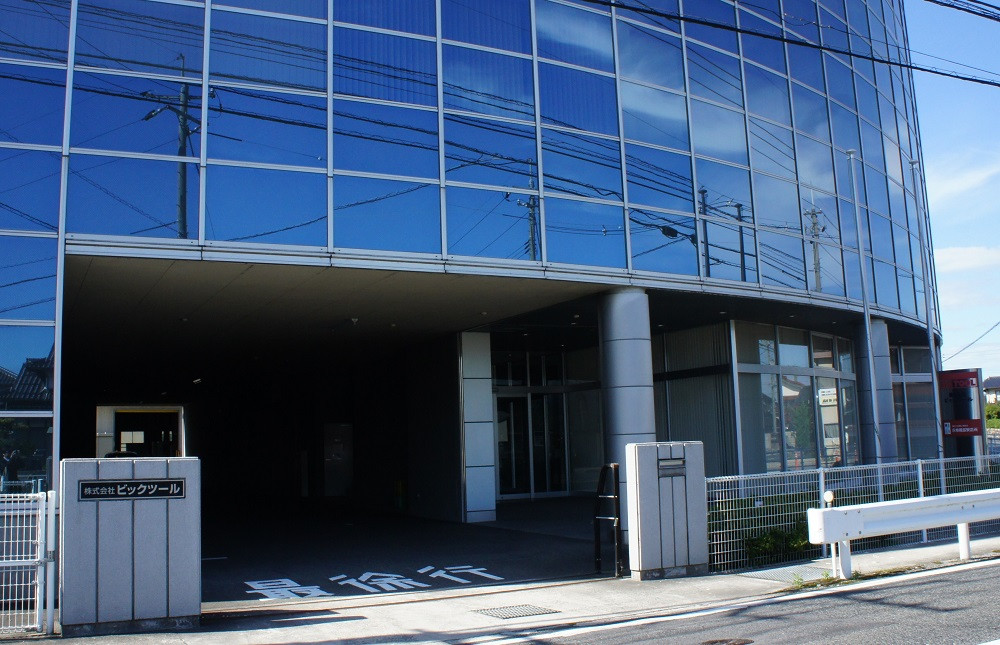
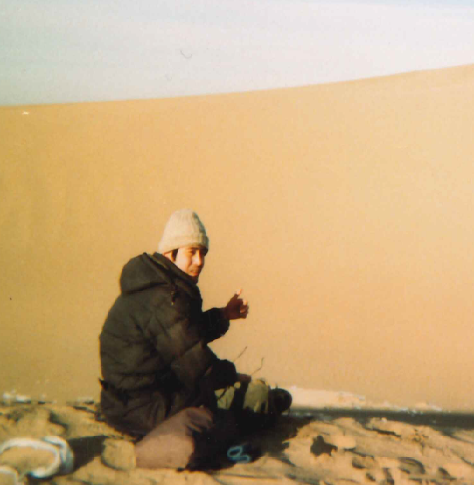