ZARAがスペインでも生産を続ける現場力
【東大大学院教授・新宅純二郎】小回りがきく国内生産でブランド力維持
日本と中国の現場力を比較すると、日本の「9勝1敗」。2013年から14年にかけ、電機連合と共同調査した結果だ。日本の電機メーカーなどを対象に、国内工場と中国の自社工場で競争力を比較した。
電機産業では生産拠点の海外移転の流れに加え、大手企業の相次ぐ経営不振もあり、国内工場の規模が縮小してきた。そんな状況の中、日本の製造現場が本当に競争力を失ったのか、それを確かめるために調査した。
10項目中、製造技術や納期など9項目で日本工場の方が優れていた。負けたのは製造コストのみだ。
過去、中国の賃金の安さに圧倒され、「国内工場の維持は無理」という声もあった。00年代半ばまでは中国の賃金は日本の10分の1以下だったが、国際協力銀行の調査によれば、15年にはその差は約半分に縮小した。中国で作る方が安い時代は終わりを迎えた。
スキャナーを製造している企業を例に挙げると、以前は普及価格帯の製品を中国で生産し、日本では高級品などを小ロット生産していた。
東日本大震災を機に製造拠点を分散化するため、日本でも一部の普及品を生産することにした。当初は久しぶりの量産に戸惑っていたが、すぐに生産性を大きく高め、1年後には製造コストでも中国に追いついた。
賃金が高騰している今、中国の工場では生産性を高めないと生き残れない。アパレル産業などは設備移転が楽なので、中国からバングラデシュ、アフリカと、渡り鳥のように工場を移す生き方もできる。
だが、そのアパレル業界でもスペインのZARAは、定番商品をバングラデシュや中国など低賃金国で製造する一方、流行の移り変わりが速い商品はスペイン国内で製造している。企画商品などを売り切るには、小回りがきく国内生産が適していると判断したようだ。
エアコンなど季節性の高い家電も同様で、売れ残ると量販店でたたき売りされ、ブランドを傷つけかねない。そこで、初期ロットは中国などで量産するが、追加発注分は国内工場で少ロット生産し、売り切ることに徹する会社もある。
製造コストを決めるのは生産性と原単位、為替レートだ。生産性は工場の現場力を表しているが、原単位を構成する賃金や材料および光熱費、為替レートは工場の実力と無関係だ。経営者は賃金や為替レートばかり見るのでなく、現場力にも目を向けるべきである。
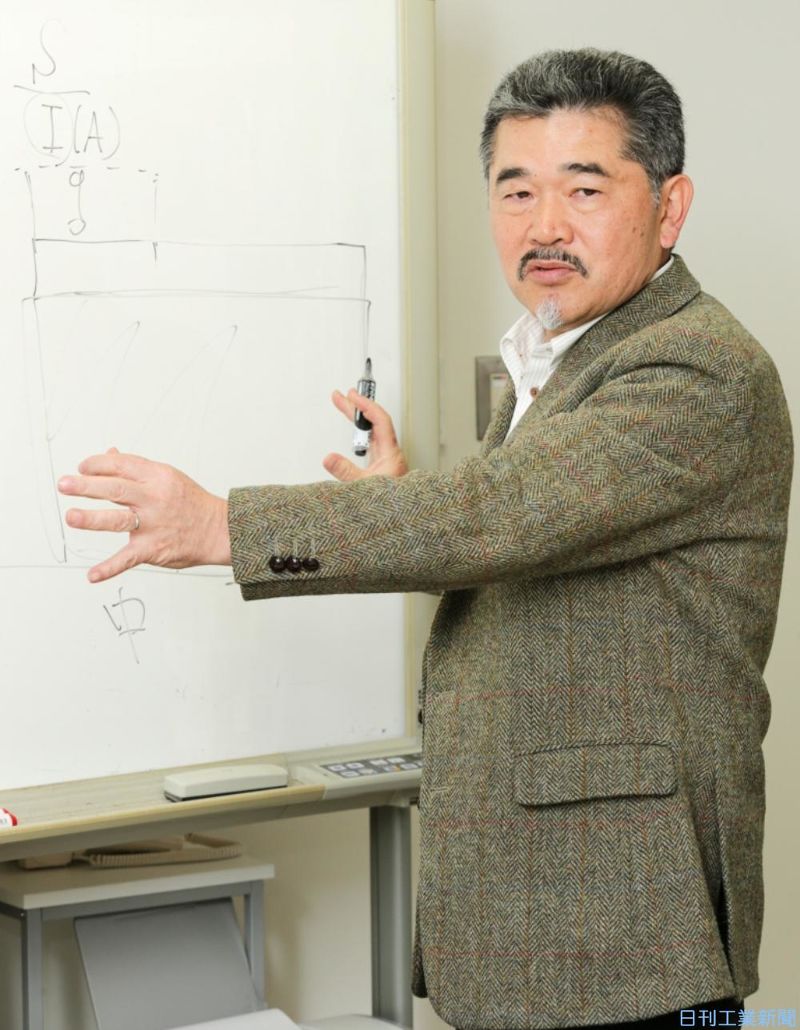
電機産業では生産拠点の海外移転の流れに加え、大手企業の相次ぐ経営不振もあり、国内工場の規模が縮小してきた。そんな状況の中、日本の製造現場が本当に競争力を失ったのか、それを確かめるために調査した。
10項目中、製造技術や納期など9項目で日本工場の方が優れていた。負けたのは製造コストのみだ。
過去、中国の賃金の安さに圧倒され、「国内工場の維持は無理」という声もあった。00年代半ばまでは中国の賃金は日本の10分の1以下だったが、国際協力銀行の調査によれば、15年にはその差は約半分に縮小した。中国で作る方が安い時代は終わりを迎えた。
スキャナーを製造している企業を例に挙げると、以前は普及価格帯の製品を中国で生産し、日本では高級品などを小ロット生産していた。
東日本大震災を機に製造拠点を分散化するため、日本でも一部の普及品を生産することにした。当初は久しぶりの量産に戸惑っていたが、すぐに生産性を大きく高め、1年後には製造コストでも中国に追いついた。
賃金が高騰している今、中国の工場では生産性を高めないと生き残れない。アパレル産業などは設備移転が楽なので、中国からバングラデシュ、アフリカと、渡り鳥のように工場を移す生き方もできる。
だが、そのアパレル業界でもスペインのZARAは、定番商品をバングラデシュや中国など低賃金国で製造する一方、流行の移り変わりが速い商品はスペイン国内で製造している。企画商品などを売り切るには、小回りがきく国内生産が適していると判断したようだ。
エアコンなど季節性の高い家電も同様で、売れ残ると量販店でたたき売りされ、ブランドを傷つけかねない。そこで、初期ロットは中国などで量産するが、追加発注分は国内工場で少ロット生産し、売り切ることに徹する会社もある。
製造コストを決めるのは生産性と原単位、為替レートだ。生産性は工場の現場力を表しているが、原単位を構成する賃金や材料および光熱費、為替レートは工場の実力と無関係だ。経営者は賃金や為替レートばかり見るのでなく、現場力にも目を向けるべきである。
【略歴】新宅純二郎(しんたく・じゅんじろう)82年(昭57)東大経卒、93年東大院経済学博士取得。96年東大院経済学研究科助教授、07年准教授、12年教授。福岡県出身、59歳。
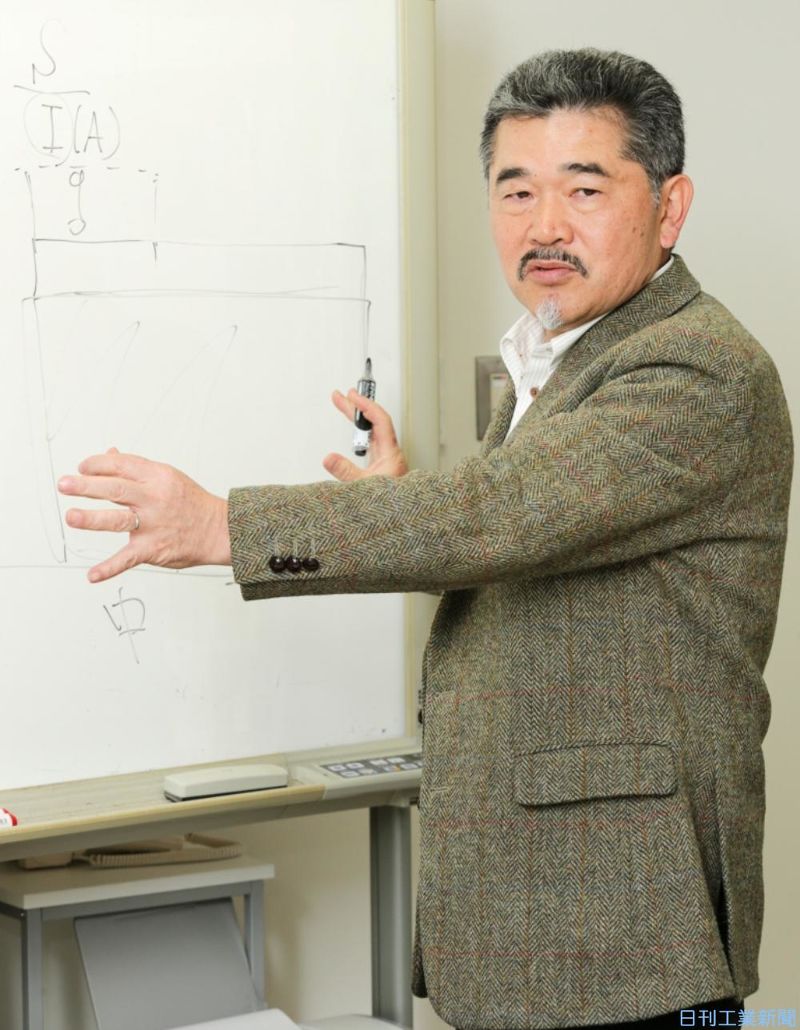
日刊工業新聞2018年5月14日
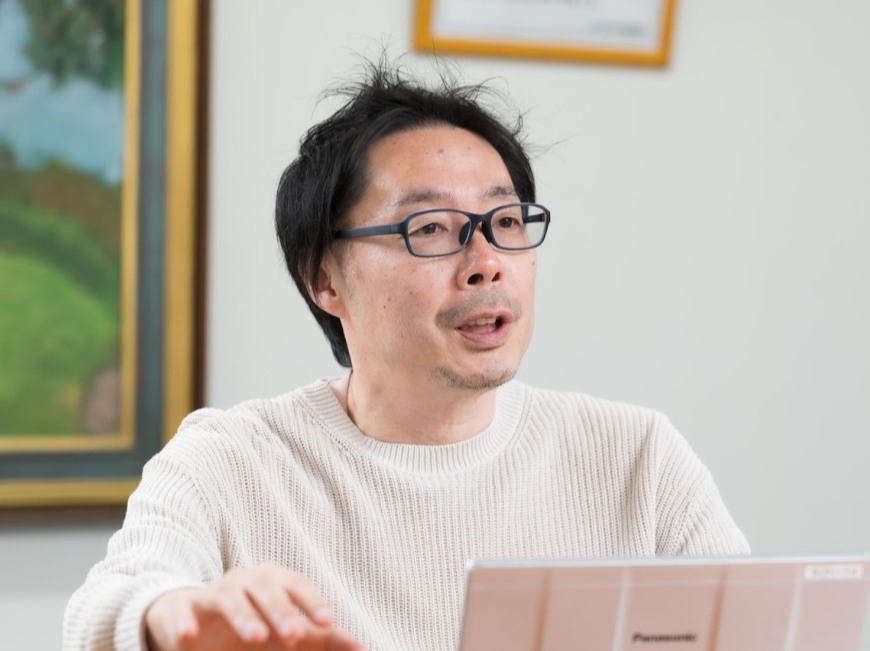