アイデア炸裂!「からくり」が生産現場を楽にする
日本の強みを鍛える、現場の創意工夫
てこやカム、クランク、ギヤなどを用い、ローコストでシンプルな設備や装置を製作して生産現場に適用する「からくり改善」への熱が高まっている。ヒューマンエラーによるポカミスを防いだり、身体負荷のきつい作業を楽にしたりするなど、現場の困りごとを現場が自ら解決していく改善活動のことだ。
日本の製造業の強みは、現場力の高さにあるのは紛れもない事実。そんな現場力を蓄える場として、からくり改善に取り組んでいる企業は決して少なくない。
住友理工は、製品に添える防錆紙を作業者が1枚ずつ箱から取り出す際、取り出しづらく作業時間にバラツキが出ることを課題に挙げた。そこで、箱のフタに粘着ローラーを取り付け、フタの開閉に合わせて粘着ローラーが1枚ずつ防錆紙を持ち上げ、確実に取れる装置を考案。「コロコロペッタン1ま~い、2ま~い」と名づけられたからくりが現場で活躍している。
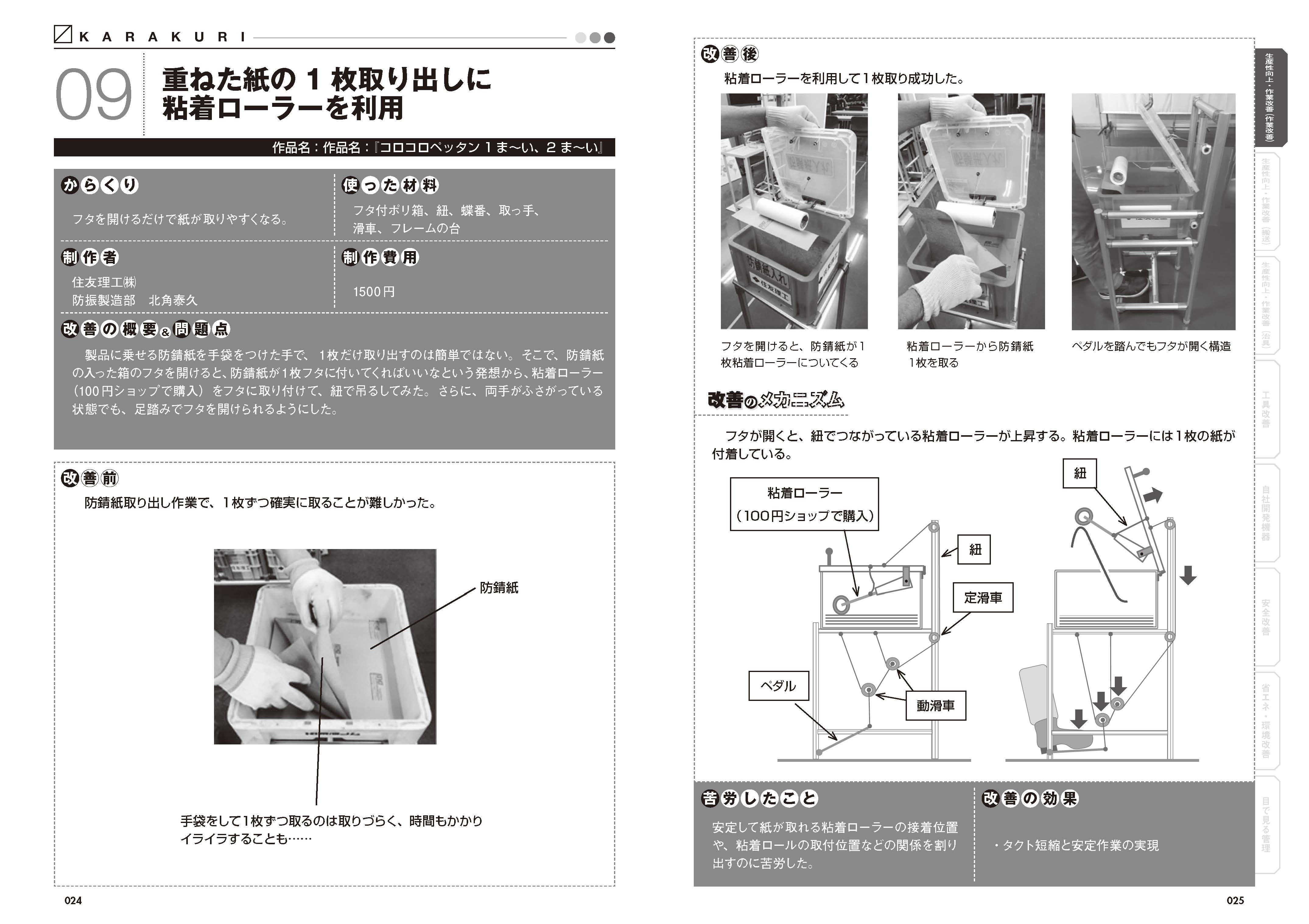
住友理工の「コロコロペッタン1ま~い、2ま~い」
マツダ防府工場のトランスミッション組立工程では、「反転じょ~ず」を開発し、重量8kgの部品を手で持って反転させる作業を廃止した。部品組み付けに使う治具に、ちょっとした細工を施したものだ。治具で部品をクランプする際、クランプ位置を部品の重心から10mmずらす設定としたことで、重力アンバランスにより反転する。このからくりのおかげで、反転作業による手首への負担がなくなったばかりでなく、反転・組み付け時間が半減した。
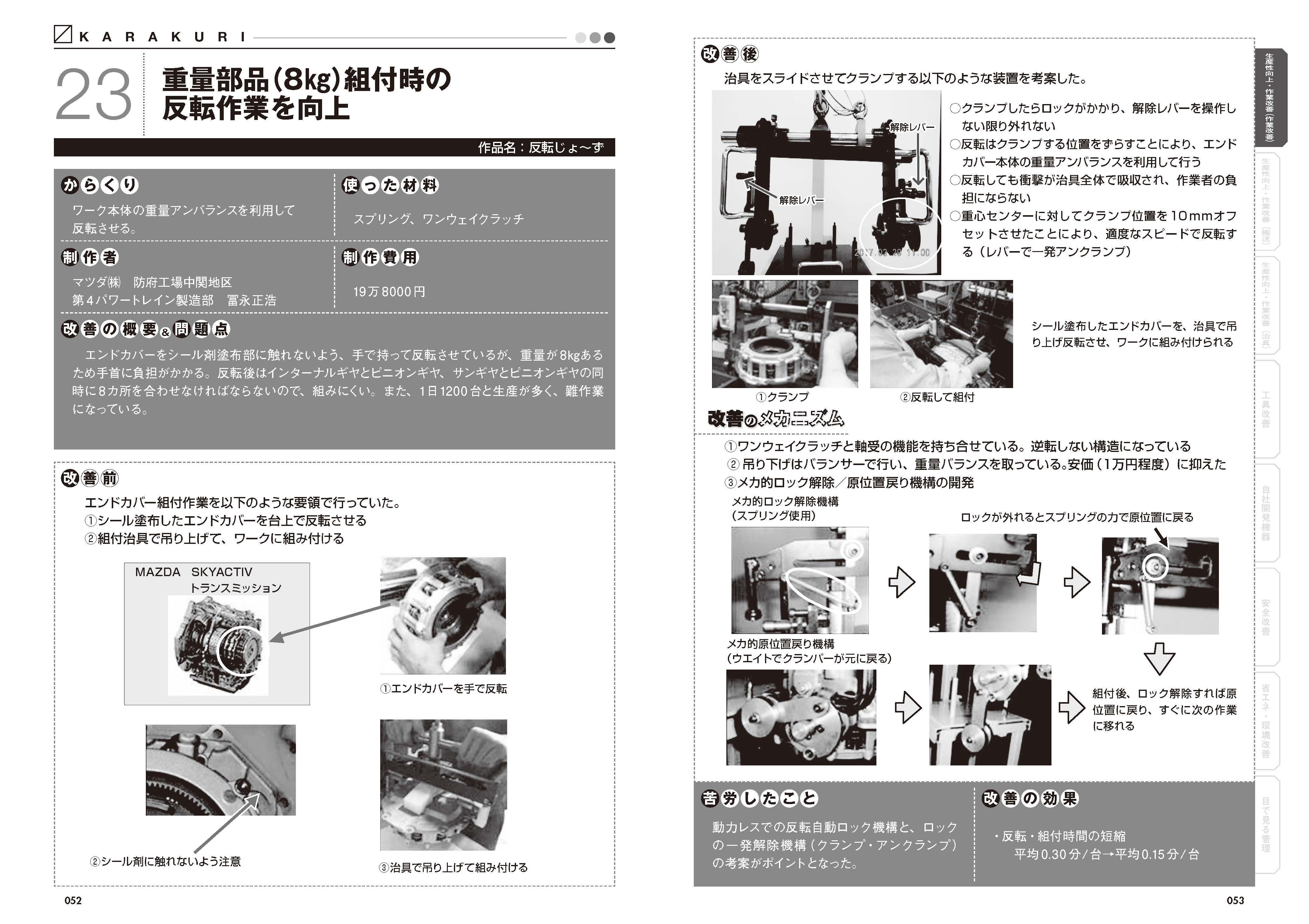
マツダの「反転じょ~ず」
トヨタ自動車は、工場内を駆け回る台車の車輪の動きに着目し、改善のヒントを得た。積載重量が重い台車は通常、旋回しやすさを考慮して前輪が固定されている。これを前輪も回転車輪とし、車輪ベースと荷台ベースの間に取っ手ベースを設け、取っ手が左右90°スライドする台車を製作。カニ歩きのように横移動できることから「たまにクラブ」と命名された。
以前の台車では、ラインのそばや作業台へ寄せる際に切り返しが何度も発生していた。そのせいで設備に身体をぶつけたり、指をはさんだりする災害の恐れがあったという。ワイヤーやスプリング、軸受など製作に要した費用は15,000円。DIYの感覚で気軽に挑戦できる点がウケているようだ。
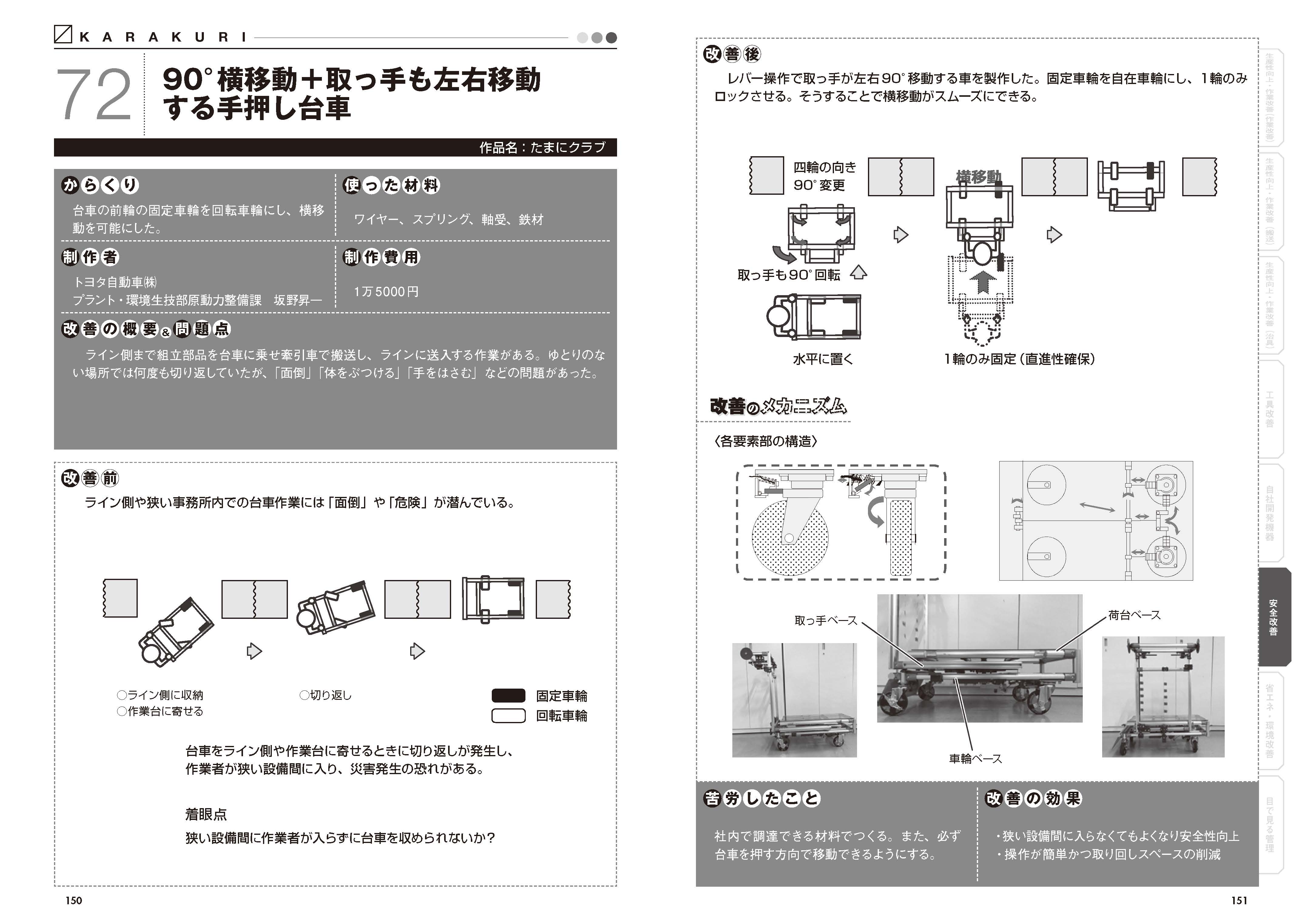
トヨタ自動車の「たまにクラブ」
3つの例の通り、創意工夫を活かして製作されたからくりには、どれも愛情に満ちたネーミングが付されている。それは、現場で真に必要とされるものをカタチにした証と言えないだろうか。
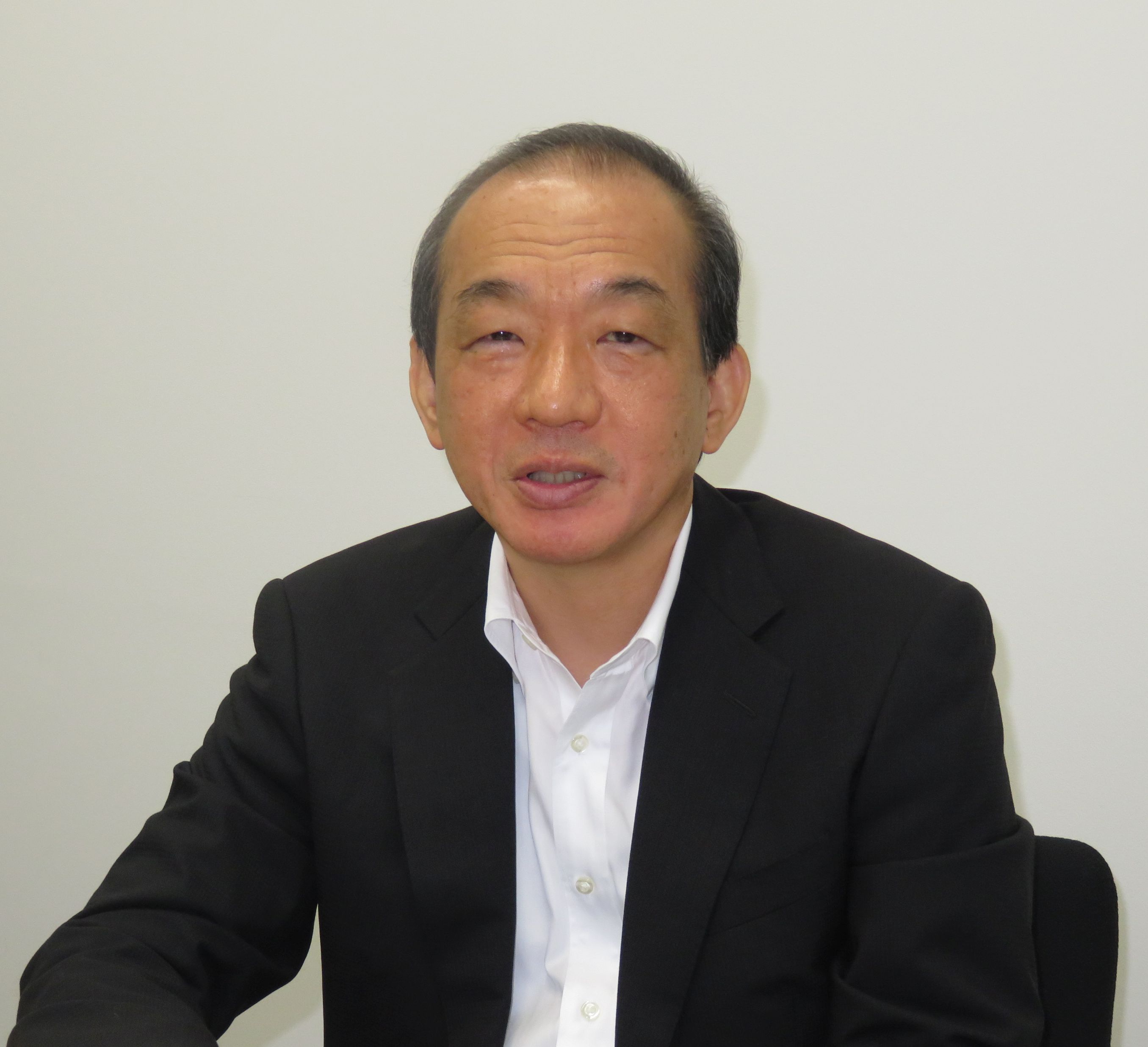
「からくり改善」を通じて設備に詳しい人づくりを進めたいと語る鈴置専務理事
1994年に「からくり改善」を提唱し、生産性向上や設備の低コスト化を普及・啓蒙する日本プラントメンテナンス協会の鈴置智専務理事は、「設備投資を積極的に行いにくい状況の中で、モノづくり強化と国内生産存続のために、こうした全員参加型の改善活動が改めて注目されている」と手応えを口にする。9月28・29日には名古屋で「第22回からくり改善くふう展」を開催。日本中から改善アイデアを一堂に集めて披露する。第4次産業革命の時代といえども、働く1人ひとりの活力と主体性を発揮する仕掛けがますます重要になるに違いない。
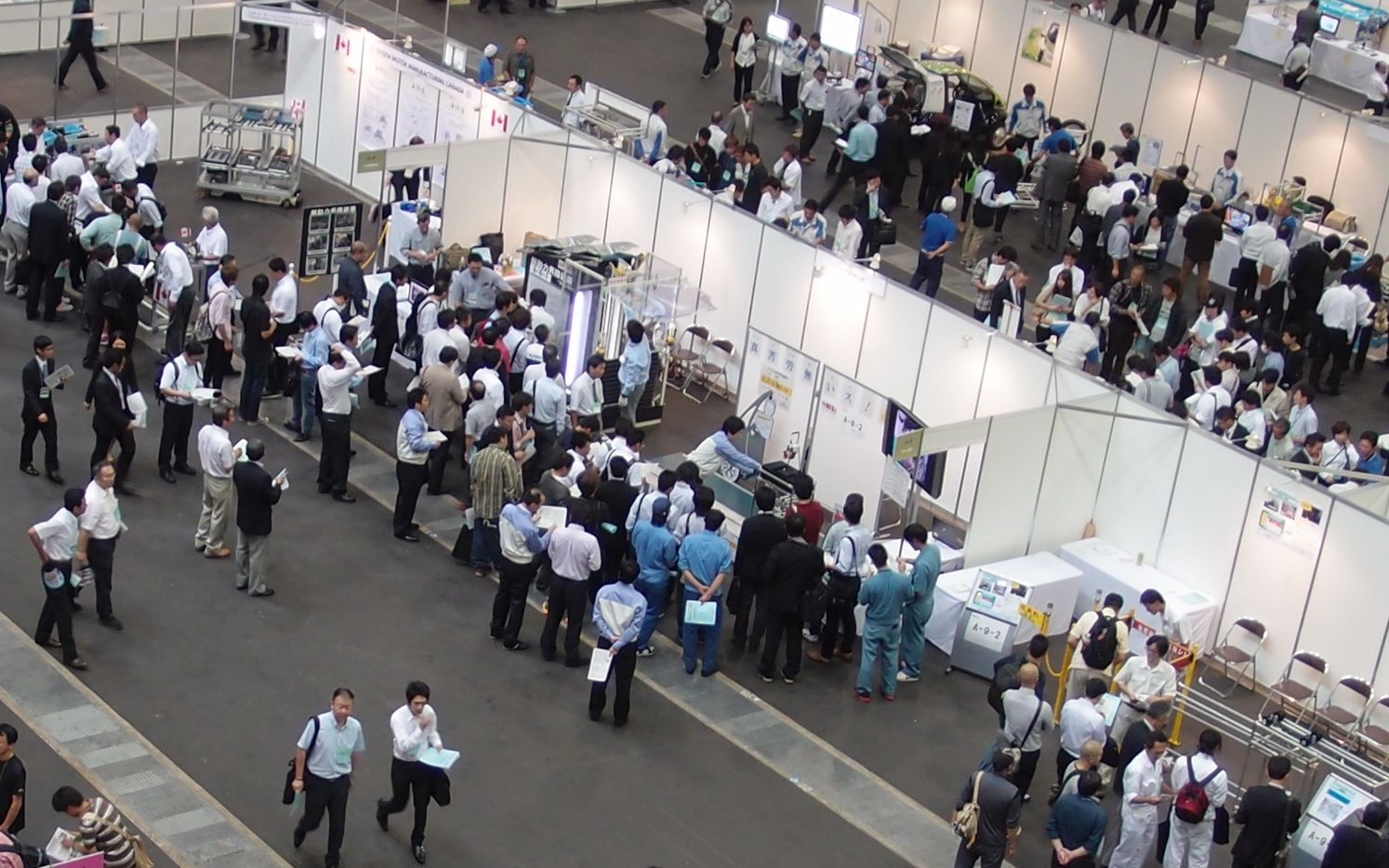
「からくり改善くふう展」での展示模様(今年は9/28・29名古屋で開催)
「金を掛けずに知恵を出す からくり改善事例集Part3」
日本プラントメンテナンス協会編、日刊工業新聞社 9/25発売
※Part1・Part2も好評発売中
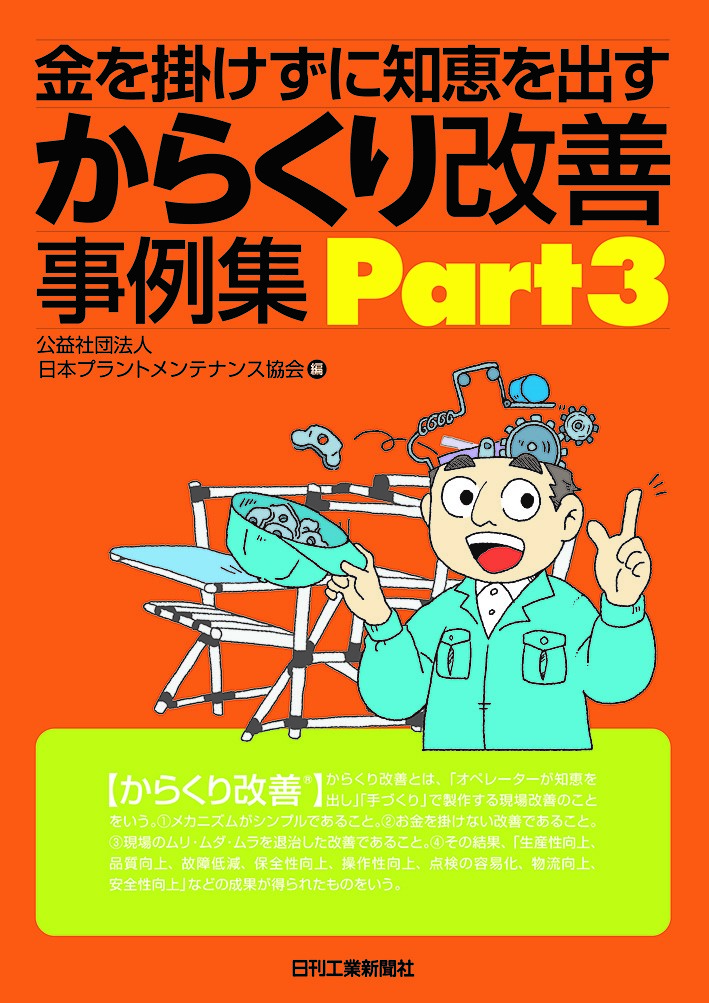
からくり改善事例集Part3
Amazonからの購入はこちら
日本の製造業の強みは、現場力の高さにあるのは紛れもない事実。そんな現場力を蓄える場として、からくり改善に取り組んでいる企業は決して少なくない。
面倒でイライラする作業を解消
住友理工は、製品に添える防錆紙を作業者が1枚ずつ箱から取り出す際、取り出しづらく作業時間にバラツキが出ることを課題に挙げた。そこで、箱のフタに粘着ローラーを取り付け、フタの開閉に合わせて粘着ローラーが1枚ずつ防錆紙を持ち上げ、確実に取れる装置を考案。「コロコロペッタン1ま~い、2ま~い」と名づけられたからくりが現場で活躍している。
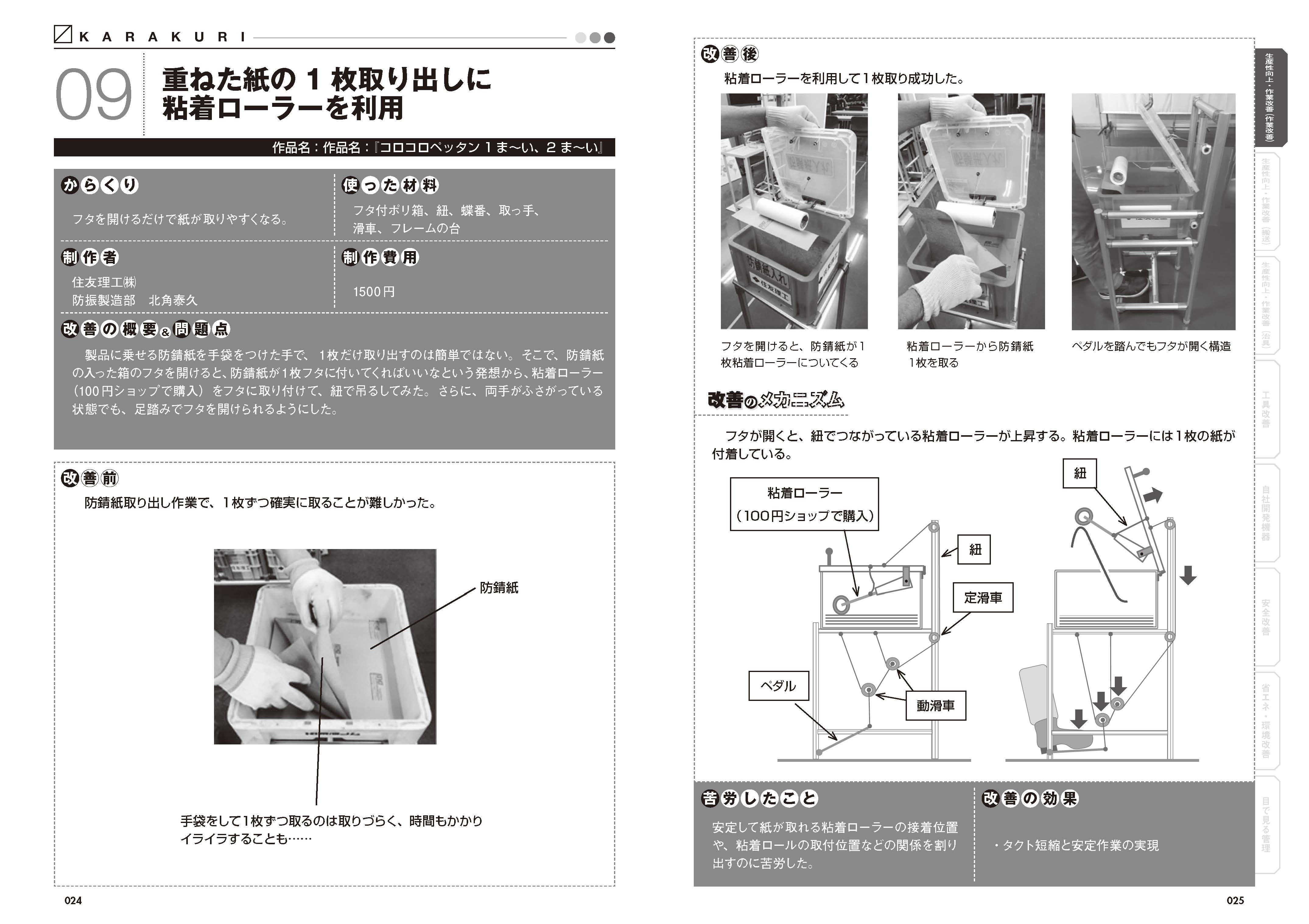
マツダ防府工場のトランスミッション組立工程では、「反転じょ~ず」を開発し、重量8kgの部品を手で持って反転させる作業を廃止した。部品組み付けに使う治具に、ちょっとした細工を施したものだ。治具で部品をクランプする際、クランプ位置を部品の重心から10mmずらす設定としたことで、重力アンバランスにより反転する。このからくりのおかげで、反転作業による手首への負担がなくなったばかりでなく、反転・組み付け時間が半減した。
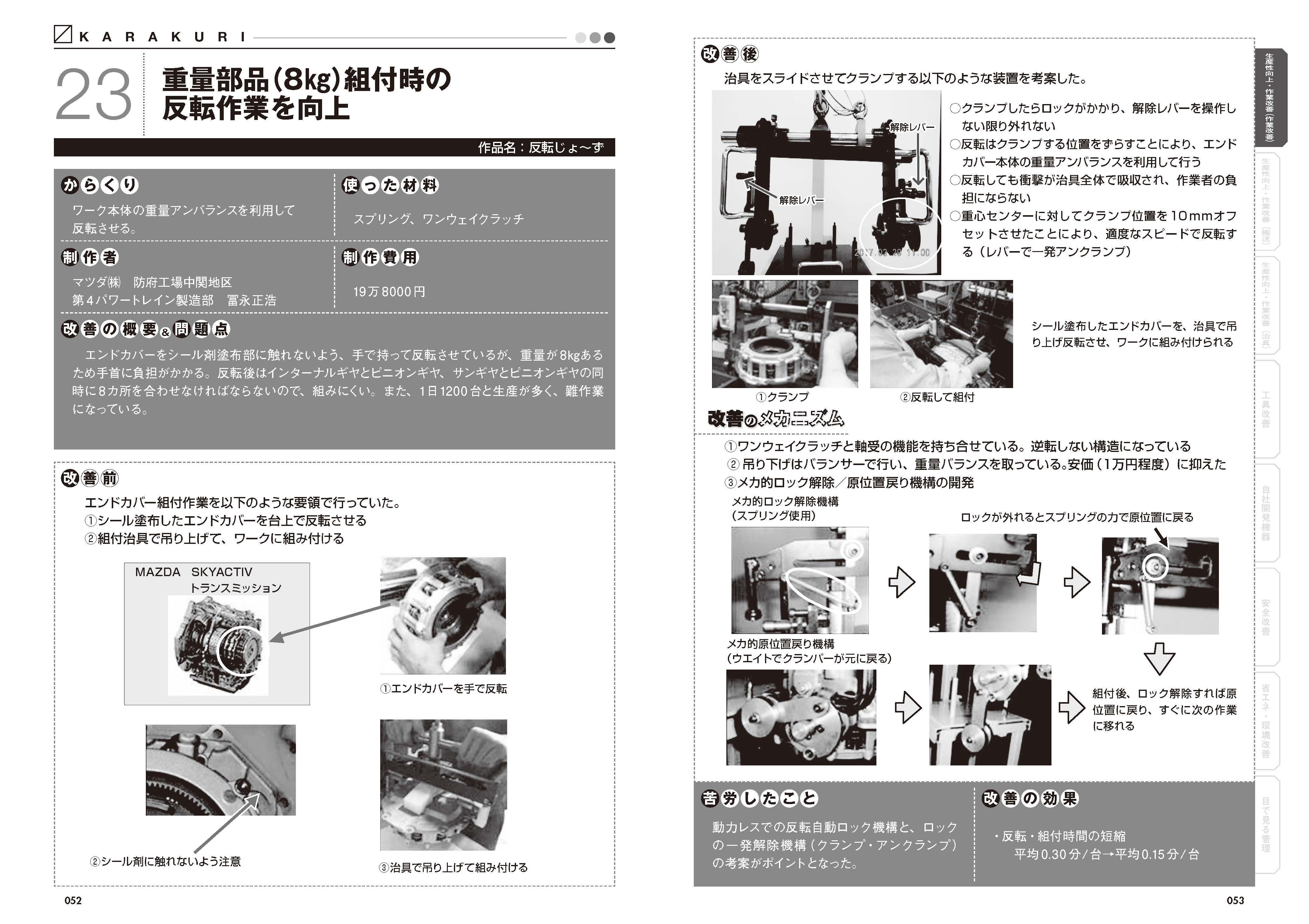
安全に作業できることが一番
トヨタ自動車は、工場内を駆け回る台車の車輪の動きに着目し、改善のヒントを得た。積載重量が重い台車は通常、旋回しやすさを考慮して前輪が固定されている。これを前輪も回転車輪とし、車輪ベースと荷台ベースの間に取っ手ベースを設け、取っ手が左右90°スライドする台車を製作。カニ歩きのように横移動できることから「たまにクラブ」と命名された。
以前の台車では、ラインのそばや作業台へ寄せる際に切り返しが何度も発生していた。そのせいで設備に身体をぶつけたり、指をはさんだりする災害の恐れがあったという。ワイヤーやスプリング、軸受など製作に要した費用は15,000円。DIYの感覚で気軽に挑戦できる点がウケているようだ。
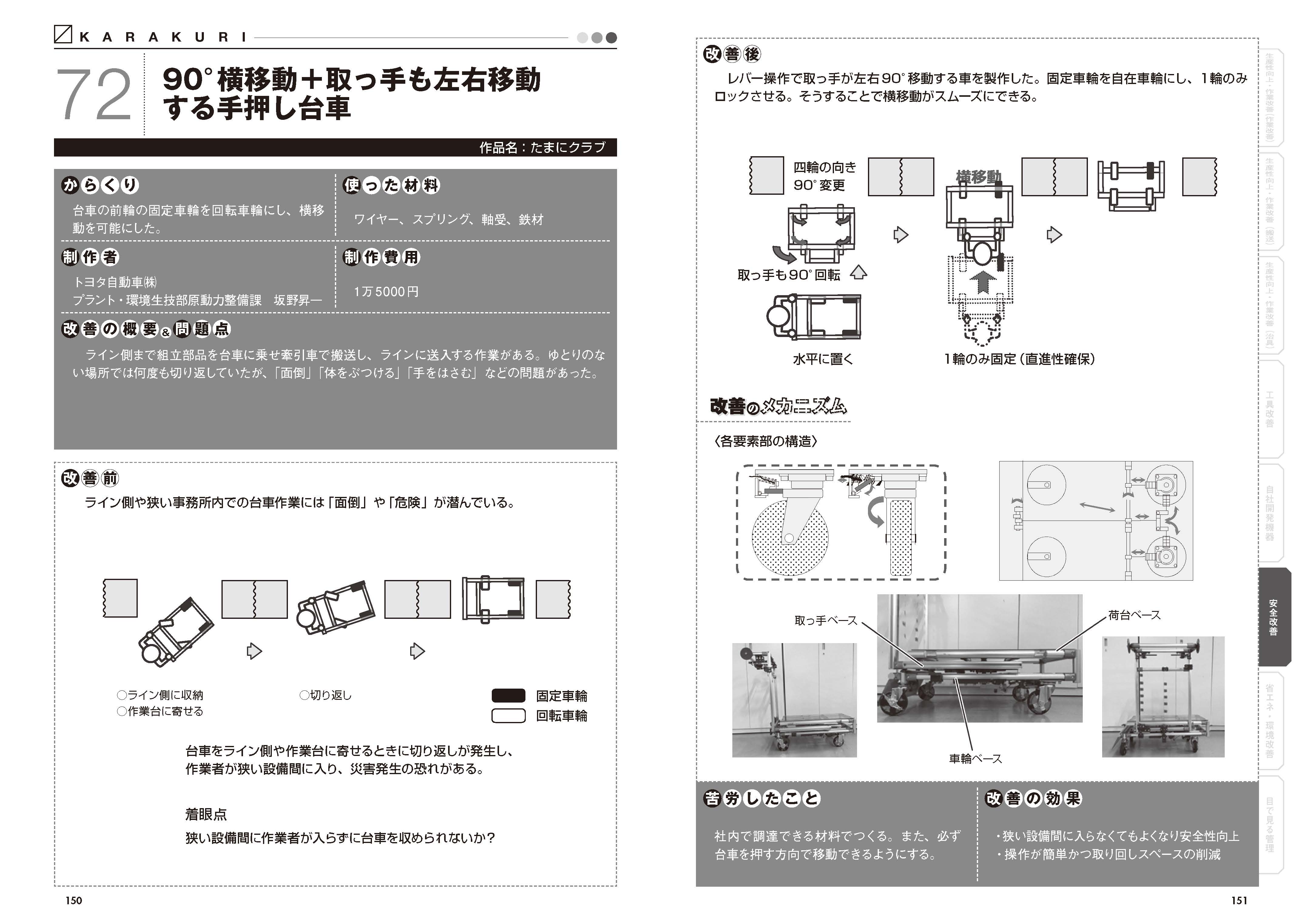
愛着を込めて呼ばれるからくり設備たち
3つの例の通り、創意工夫を活かして製作されたからくりには、どれも愛情に満ちたネーミングが付されている。それは、現場で真に必要とされるものをカタチにした証と言えないだろうか。
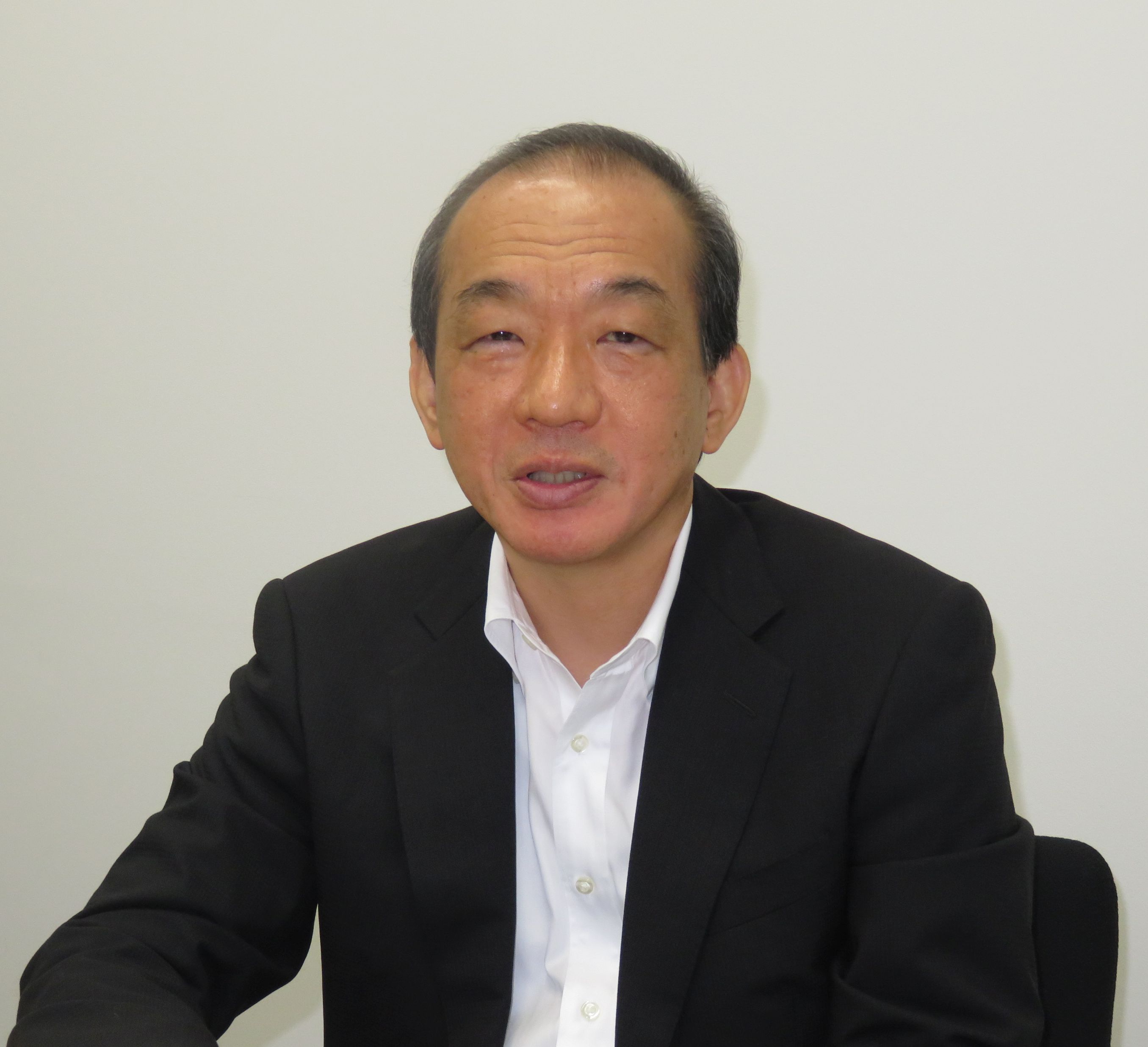
1994年に「からくり改善」を提唱し、生産性向上や設備の低コスト化を普及・啓蒙する日本プラントメンテナンス協会の鈴置智専務理事は、「設備投資を積極的に行いにくい状況の中で、モノづくり強化と国内生産存続のために、こうした全員参加型の改善活動が改めて注目されている」と手応えを口にする。9月28・29日には名古屋で「第22回からくり改善くふう展」を開催。日本中から改善アイデアを一堂に集めて披露する。第4次産業革命の時代といえども、働く1人ひとりの活力と主体性を発揮する仕掛けがますます重要になるに違いない。
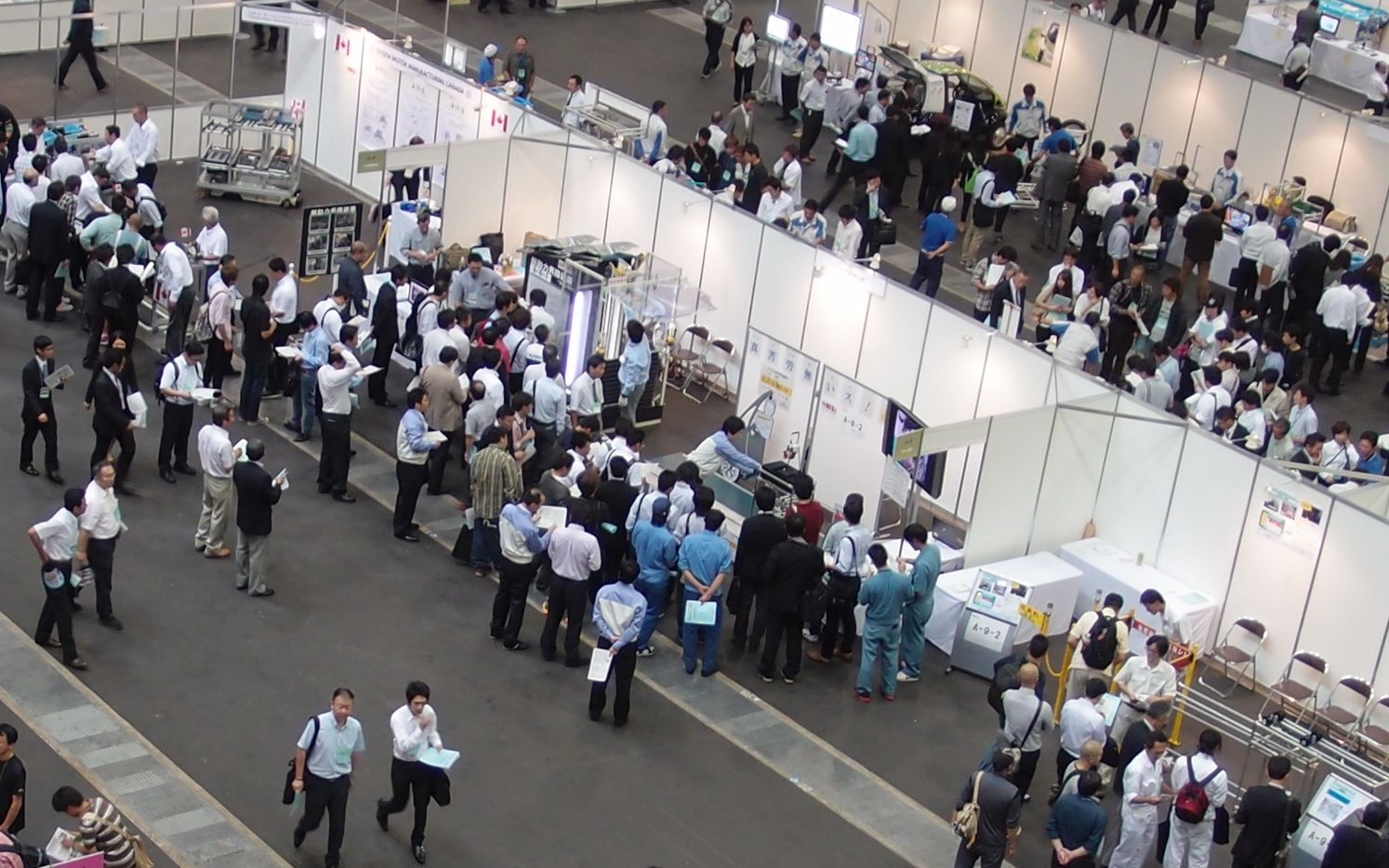
「金を掛けずに知恵を出す からくり改善事例集Part3」
日本プラントメンテナンス協会編、日刊工業新聞社 9/25発売
※Part1・Part2も好評発売中
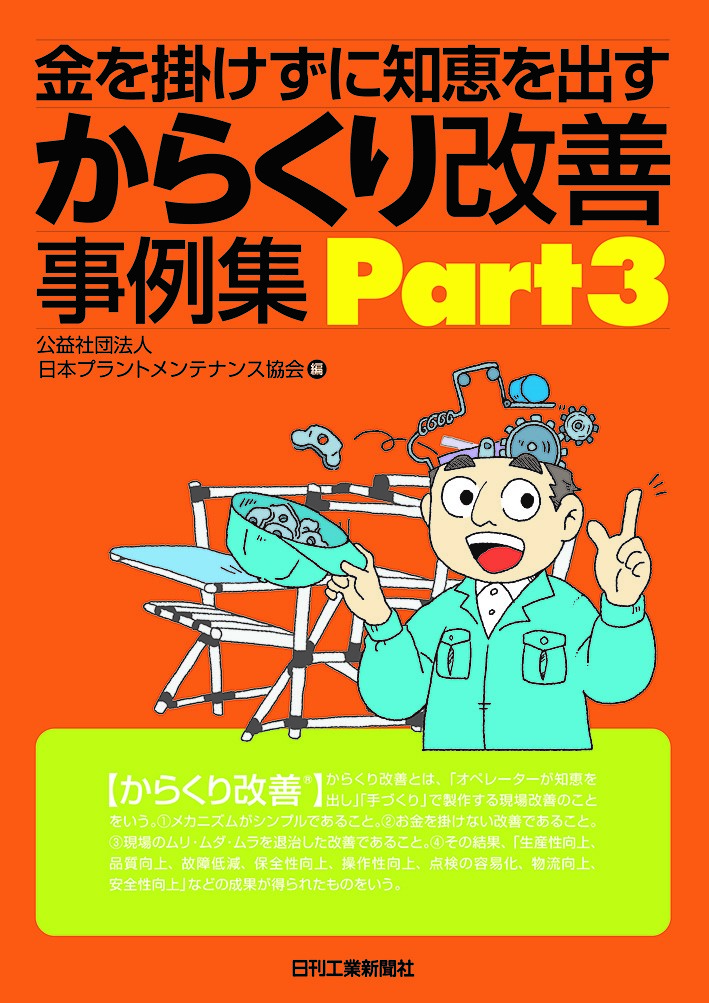
Amazonからの購入はこちら
ニュースイッチオリジナル