リサイクル炭素繊維、標準化へ入った議論の新たな段階
リサイクル炭素繊維に関する標準化に向けた議論が新たな段階に入る。国際標準化機構(ISO)で標準化を議論するワーキンググループ(WG)の設置が認められた。炭素繊維強化プラスチック(CFRP)の廃材から炭素繊維を抽出して再生する技術は確立しているものの、性能評価について標準化規格がない。このためリサイクル炭素繊維の使用用途が限定される。日系メーカーが世界の炭素繊維の約65%を生産しているだけに、標準化議論での主導的役割が求められる。(井上雅太郎)
新WGはISO専門委員会(TC)61(プラスチック)の分科委員会(SC)13(複合材および強化繊維)の傘下に設置される。日本から日本プラスチック工業連盟が事務局を務めるほか、日本化学繊維協会(化繊協)や経済産業省などがメンバーに加わるとみられる。化繊協の富吉賢一専任副会長は「評価方法が規格化できれば、リサイクル炭素繊維の出口が見えてくる」と期待する。
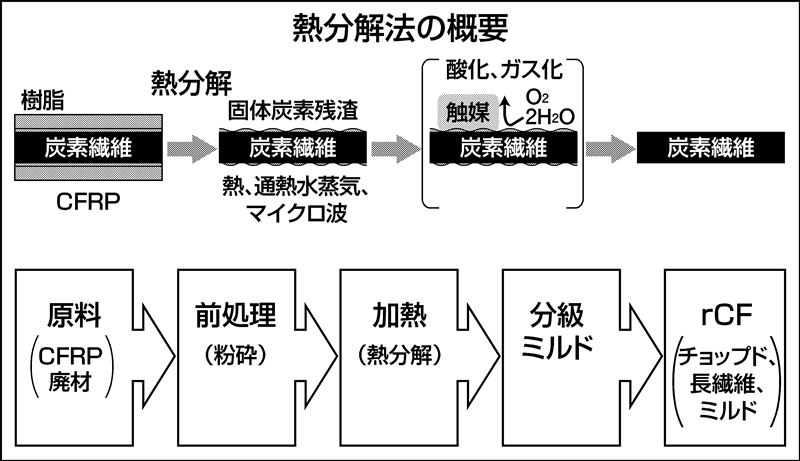
再生される炭素繊維は、CFRP製造工程から排出される工程廃材と、航空機などでの耐用年数を終えた使用済みCFRP廃材とで品質が大きく分かれる。さらに廃材の発生由来により炭素繊維の状態の品質が異なるため、化繊協は「これらバラつきのある素材を再生して、安定した品質を確保できるかどうかが大きな論点の一つ」と指摘する。
また、回収した炭素繊維廃材は繊維長さや太さ、方向性、含有率が異なるため、性能を評価する場合、連続繊維で製造するバージン素材と同様の引っ張り強度と弾性率など以外にも指標が必要になりそうだ。繊維の長さや分布、傷繊維の状態といった評価のほか、トレーサビリティー(製造履歴管理)の確保なども検討されるとみられる。
バージン炭素繊維を1キログラム製造するのに焼成工程などで約20キログラムの二酸化炭素(CO2)排出を伴う。軽くて強度が高いため航空機などの機体に採用すると燃費向上により環境負荷低減に寄与できる。さらにリサイクル炭素繊維を製造する場合ではCO2排出量をバージンに比べ8―10分の1程度に抑制できる。ただ性能はバージンに比べ劣化してしまうため、水平リサイクルが困難なのが実情だ。
経済産業省の調査などによると、2020年時点の使用済みCFRP廃材4万6500トン、CFRP製造工程廃材1万500トンが排出されたと推計。このうちマテリアルリサイクルしたのは1割未満で、ほとんどがサーマルリサイクルや埋め立て処理されている。
パソコン筐体(きょうたい)に採用される事例はあるが、主要用途として期待される自動車部品向けには品質保証の問題から採用が進んでいない。リサイクル炭素繊維の性能に関して標準化できれば、品質保証の問題を解消できるようになる。化繊協は「物性に問題はなく、標準化により自動車部品や風力発電向けなどに市場開拓ができる」と見通す。
その一方で、CFRPは不可逆性があるため熱可塑性の樹脂に比べ加工スピードが遅くなる。このため自動車部品として採用が進まない問題がある。「自動車部品として普及させるには熱可塑性のCFRPといった開発も必要になる」と合わせて指摘する。