需要あるが導入に壁…「モバイルマニピュレーター」は市場をこじ開けられるか
無人搬送車(AGV)に協働ロボットを載せた「モバイルマニピュレーター」を製造現場で活用したいというニーズが人手不足で高まっている。部材を搬送するだけではなく、装置に部材を投入したり工具を交換したり、届けた後の作業も自動化できる。一方、シンプルな搬送だけなら、協働ロボを固定しAGVを周回させる方が簡単だ。複数の場所や装置を巡回することで強みが生きるが、スケジューリングや連携機器との協調制御が複雑になる。モバイルマニピュレーターは走り出せるか。(取材・小寺貴之)
「ポテンシャルはある。あとは市場をどう作っていくか」。デンマーク・ユニバーサルロボット(UR)の山根剛日本支社長はモバイルマニピュレーターを普及させるために知恵を絞る。移動も作業もできるモバイルマニピュレーターは、ニーズはあるものの実際の導入には時間がかかっているロボットだ。協働ロボが働き出せば、人と同じように移動して作業の場を変えながら働けないのかと要望が上がる。だが技術やコスト面で課題があった。
URは同じく米テラダイン傘下のデンマーク・モバイルインダストリアルロボッツ(MiR)のAGVとインターフェースを整え、URの協働ロボとMiRのAGVを組み合わせたモバイルマニピュレーターの構築環境を整えた。協働ロボは直流電源で駆動し、AGVと電池を二重に抱える必要がない。AGV側から協働ロボに指令を出して実行させるなど、上下で協調制御できる。山根支社長は「半導体のウエハーカセット搬送や計測器を持たせた大型部材の検査などの用途を開拓したい」と意気込む。
【カンタム・ウシカタ/ワーク投入・回収自動化】
システムインテグレーターのカンタム・ウシカタ(横浜市都筑区)は工作機械へのワーク投入や回収の自動化を提案する。松井重憲ロボティクス事業部統括部長は「協働ロボを固定すると工作機械2台しかカバーできない。移動できれば順番に交換していける」と説明する。URとMiRのモバイルマニピュレーターの費用は約1000万円。3台以上の工作機械をめぐれば、協働ロボを並べるよりもメリットが出てくるとそろばんを弾く。
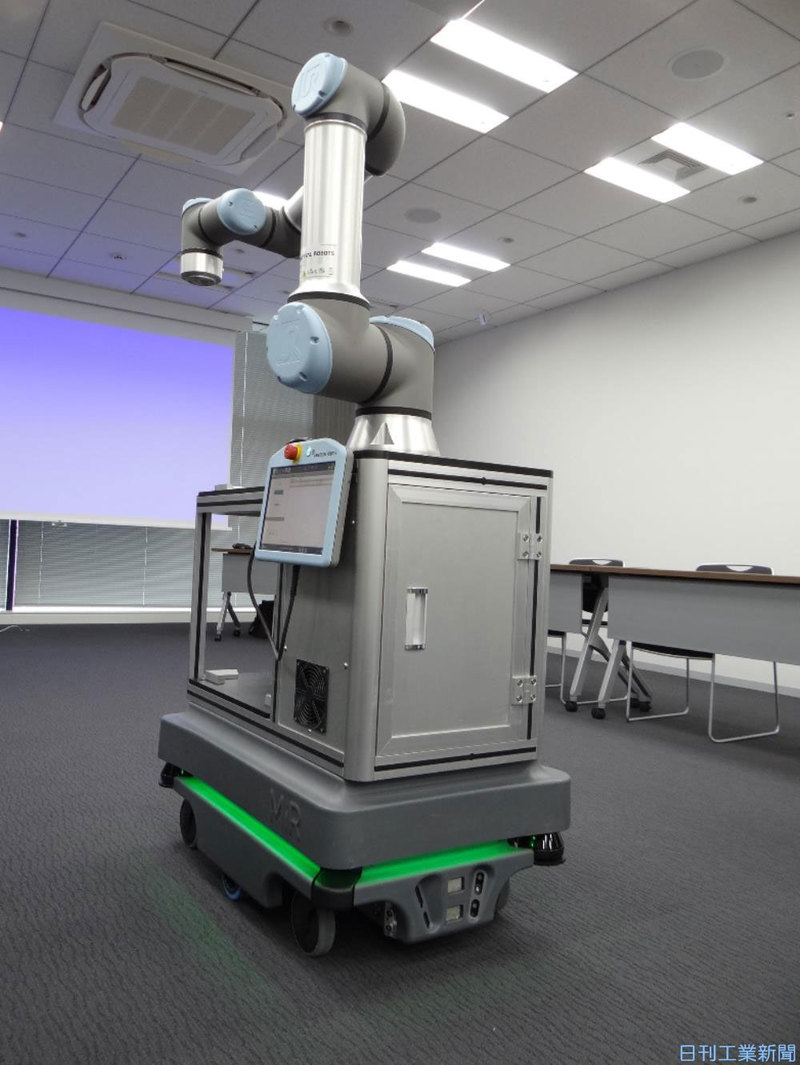
【オムロン/複数セットを同時搬送】
オムロンは組み立てラインや半導体製造ライン向けにモバイルマニピュレーターの利用を提案する。経営基幹職の越智直哉氏は「コンベヤーから受け取るAGVだと1セットしか運べない。可搬重量をフル活用できていなかった」と指摘する。アームでAGV内に収納すれば複数のセットを同時に運べ、搬送を効率化できる。
東芝インフラシステムズ(川崎市幸区)はコンベヤーからパレットに積み替える用途を想定する。荷を受けるパレットを回転テーブルで回し、ロボットの移動距離を短縮する。
【明電舎/数cmずれ 手元計測で補正】
明電舎はファナックの小型協働ロボを載せた「RocoMo―V」を発売し、工作機械へのワーク投入などでの活用を勧める。開発担当の山中和之氏は「AGVの位置ずれが数センチメートル程度残るため、協働ロボの手元計測でずれを補正する。機構で吸収できればより安く抑えられる」と説明する。
製造業のモバイルマニピュレーター活用はスペースと位置精度の問題に苦しんできた。中小規模の工場ではロボ専用の走行スペースを取りづらく、作業者とすれ違う前提で安全を確保する必要があった。AGVの障害物回避などの自律走行機能が向上し、協働ロボを載せることで人と共存しやすくなった。
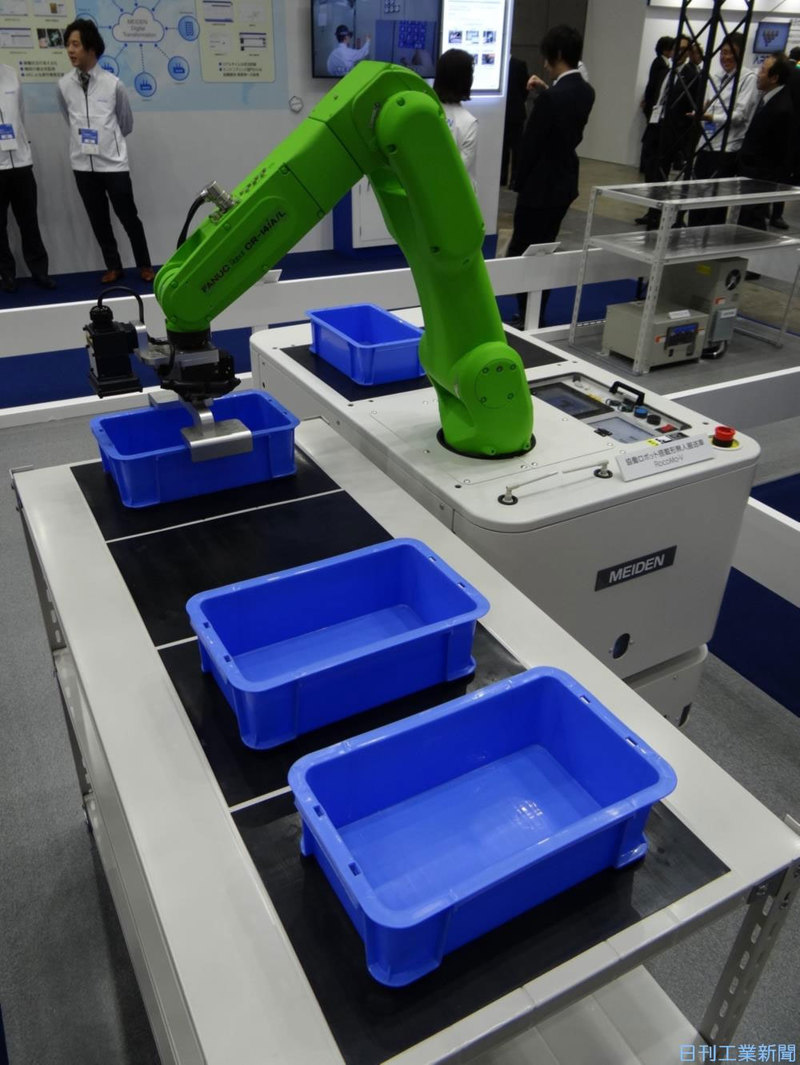
AGVの位置ずれは協働ロボに求められる位置精度と比べると桁違いに大きい。移動する度に測り直すため、この計測システムに予算とタクトタイムが費やされてしまう。しかし現在はアームの先に載る3次元(3D)センサーが進化している。2年前に200万円程度だった3Dセンサーの価格が数十万円になった。FA・ロボットシステムインテグレータ協会(SIer協会、東京都港区)の久保田和雄会長(三明機工社長)は「数万円の距離カメラでもできることは多い。モバイルマニピュレーターの提案は増えていく」と期待する。
モバイルマニピュレーターと周囲をつなぐ技術も進化している。オムロンは0・5秒でバラ積み部品を計測し把持点を割り出す技術を開発した。3Dカメラの1回の撮影でバラ積みの立体形状を求め、部品の形と照合して拾う箇所を特定する。従来は1―2秒程度かかっていた。次工程に必要な部品をバラ積みから配膳トレーに並べるキッティングが速くなる。同時に工作機械やトレーの位置を2次元マーカーで把握する技術も開発した。協働ロボが移動する度に、工作機械やワークとの相対位置がずれても2次元マーカーを読んで修正できる。
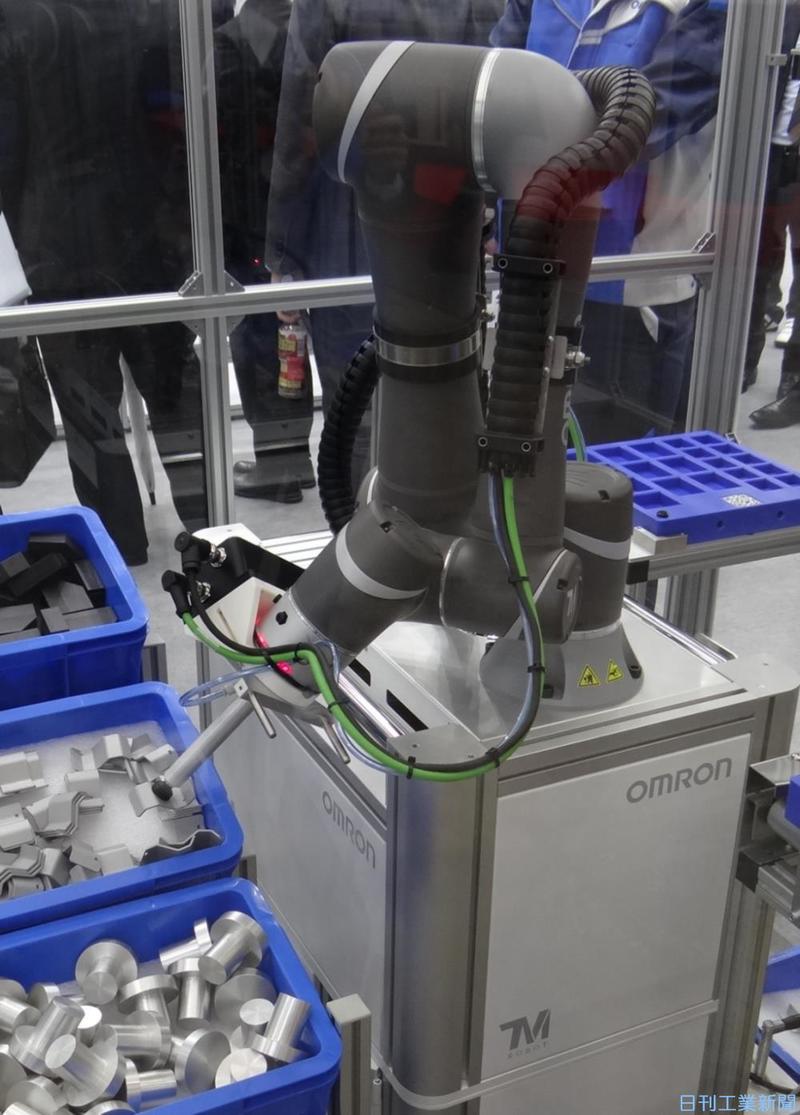
これらの技術がモバイルマニピュレーターに統合されれば、昼間にキッティングでワークを準備し、夜はロボットで工作機械を稼働させることも可能になる。早朝や午前は作業者向けのキッティングを担うこともできる。
オムロンの越智氏は「欧州の中小企業が夜はロボットで工作機械を稼働させて量産仕事をこなし、昼間に人手で多品種少量や特急品に応えている」と指摘する。夜間稼働で工作機械の償却期間を短縮し、人は付加価値の高い非量産品に割り当てる。人件費勝負ではない、顧客に近い工場の戦い方を展開できる。
【日立/強化学習で最適化】
課題は制御管理システムの肥大化だ。工作機械の加工終わりのタイミングとAGVの到着タイミングの調整や搬送ルート、作業者とロボの交差防止など、機械とロボ、人のデータを取って最適化する必要がある。ただトラブルやチョコ停など、日々現場は変化し、全てのデータを集めることは難しい。事前に計画を立てても実行できない可能性もある。そこで日立製作所は強化学習を用いた運用最適化を研究する。荒宏視主任研究員は「欠けたデータでもリアルタイムに最適化したい。事前計画よりもデータから強化学習した方が有効」と展望する。作業者500人、2万オーダーの加工物流センターをモデルとして運用最適化に取り組む。
モバイルマニピュレーターの研究は歴史が長く、これまで製品も提案されてきた。ただ小規模なら台車に載せるよりもアームを並べた方が安定し、大規模になると制御管理システムが膨らむ。モバイルマニピュレーター単体の能力が向上すると、この中間の用途が生まれる。市場をこじ開けられるか注目される。
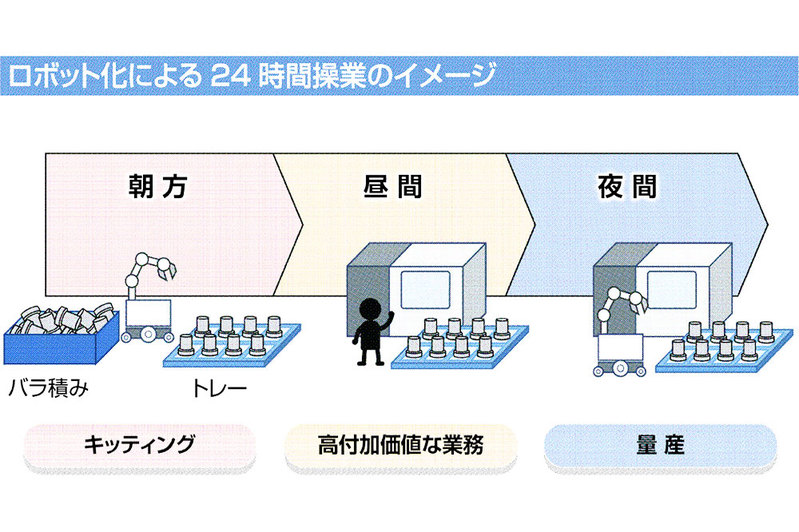
【追記】
工作機械にワークを投入するオートローダーは後付けが難しく、また要らなくなったら外せる協働ロボが使い勝手が良いと判断されて採用が増えているとのことです。ですがワーク投入や工具交換だけしている人はいないので空いた時間には別の作業をして欲しいところです。MCで20分間削るとして、その間ただ待っていると、人間なら怒られます。一方で20分ごとに協働ロボを人手で移動させていたら本末転倒なので、ロボが自動で移動し、違う工作機械もお世話してよと思ってしまいます。
またバラ積みピッキングも、特定の場所でバラ積みだけやってる人間はそんなにいません。ロボットアームの届く範囲に部品箱を並べるのも限界があるので、多少は移動してピックしてよと思ってしまいます。倉庫を巡ってピックするのは難しくても、部品棚のセルを作ったらセル間を移動してほしいところです。オムロンの0・5秒ピックはモバイルマニピュレーターに載せられるそうなので実現可能ではあります。モバイルマニピュレーターがバラ積みとワーク投入を一台でできたら人間の倍の時間がかかったとしても売れると思います。要素技術はできてきているので、統合してパッケージ化して良心価格でお願いできませんかと思ってしまいます。導入した後は、追加機械を含めたスケジュール再調整やルート最適化、新しいワークの登録・更新など、継続的に仕事が発生するので、サービスで稼げばいいのではないかと思ってしまいます。この人手不足の中で工作機械を24時間稼働させられるなら、工場のレイアウトを変えてもいいと考える工場長は少なくないはずです。
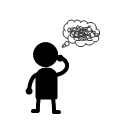