ボーイングのコスト削減要求に日本の航空機メーカーが出す答え
川重、新工場はIoTで武装。検査工程などを簡略化
「QCD(品質・コスト・納期)にもっと磨きをかけよう」。2016年4月に航空機部門のトップに就いた常務執行役員の並木祐之は、現場にこう語りかけた。民間航空機向け機体部品を手がける川崎重工業。メーン顧客の米ボーイングは欧エアバスと激しい受注競争を繰り広げ、コストダウン要求は年々厳しさを増している。
「単なるプライスダウンはできない」(並木)。川重には乾いたぞうきんを絞るような生産改善を進めてきた自負がある。「あとはボーイングと一緒になった取り組みが不可欠になる」と強調する。
例えば検査工程。一度も不具合が発生していない工程での検査を、簡便化するといった取り組みだ。並木は「ボーイングの決め事だから、当社では判断できない」とした上で、「さらにコストダウンを進めるにはこれしかない」と続ける。
民間航空機の胴体などを手がける名古屋第一工場(愛知県弥富市)。ボーイングの次世代大型機「777X」向け胴体の量産開始や、中・大型機「787」の増産対応など大イベントを控える。
17年2月、第一工場内で建設していた「777X」向け胴体の新工場が完成。6月の製造開始に向け、生産設備の設置作業を始めた。新工場の完成は航空機部門に留まらず、川重グループ全体への波及効果が期待できる。
並木は新工場を「IoT(モノのインターネット)などを活用したスマート工場のとっかかり」と表現する。自動で穿孔(せんこう)位置を認識する自社製ロボット、画像センシング技術や制御技術を駆使した新規開発設備を導入。IoTに必要な通信インフラも整備する。
技術開発本部とも連携し「ここで得た知見やノウハウを他部門の工場に広げたい」と並木。副社長の井城讓治は「自社で試して形になれば外販できる」とその先を見通す。スマート化の進捗(しんちょく)次第では、ボーイングの高い要求に応えられるかもしれない。生産改善に終わりはなく、これは製造業の宿命でもある。
(敬称略)
「単なるプライスダウンはできない」(並木)。川重には乾いたぞうきんを絞るような生産改善を進めてきた自負がある。「あとはボーイングと一緒になった取り組みが不可欠になる」と強調する。
例えば検査工程。一度も不具合が発生していない工程での検査を、簡便化するといった取り組みだ。並木は「ボーイングの決め事だから、当社では判断できない」とした上で、「さらにコストダウンを進めるにはこれしかない」と続ける。
民間航空機の胴体などを手がける名古屋第一工場(愛知県弥富市)。ボーイングの次世代大型機「777X」向け胴体の量産開始や、中・大型機「787」の増産対応など大イベントを控える。
17年2月、第一工場内で建設していた「777X」向け胴体の新工場が完成。6月の製造開始に向け、生産設備の設置作業を始めた。新工場の完成は航空機部門に留まらず、川重グループ全体への波及効果が期待できる。
並木は新工場を「IoT(モノのインターネット)などを活用したスマート工場のとっかかり」と表現する。自動で穿孔(せんこう)位置を認識する自社製ロボット、画像センシング技術や制御技術を駆使した新規開発設備を導入。IoTに必要な通信インフラも整備する。
技術開発本部とも連携し「ここで得た知見やノウハウを他部門の工場に広げたい」と並木。副社長の井城讓治は「自社で試して形になれば外販できる」とその先を見通す。スマート化の進捗(しんちょく)次第では、ボーイングの高い要求に応えられるかもしれない。生産改善に終わりはなく、これは製造業の宿命でもある。
(敬称略)
日刊工業新聞2017年3月6日
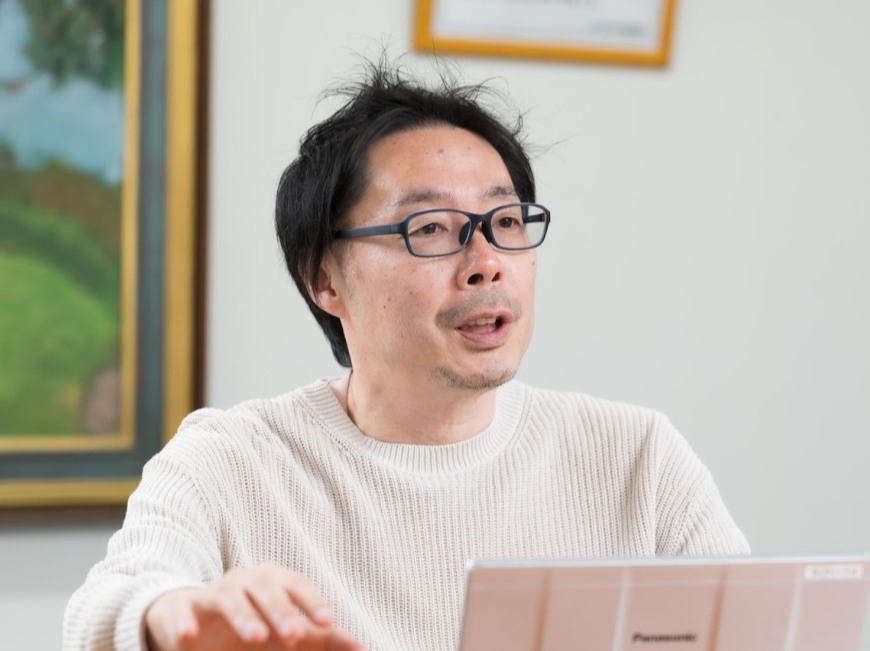