アイシンが不可能を乗り越える、軟体部品の組み立て自動化
アイシンがゴム製チューブやワイヤなど軟体部品の組み立て工程の自動化に乗り出している。持ち上げた際に揺れたり、形状が変化したりしやすい軟体部品は自動化できないとの認識が大半だが、同社は製品自体の構造の変更や自社でロボットハンドを開発するなど、創意工夫によりこれを実現した。不可能を改善や挑戦で乗り越える。(名古屋・川口拓洋)
軟体部品組み立ての自動化を実現したのはアイシンの新豊工場(愛知県豊田市)。同工場では車のスライドドアやバックドア、シートなどを電動で動かすための駆動ユニットを生産している。このうちパワーバックドアシステムに搭載し、挟み込みなどを検知するセンサー「タッチセンサー」の組み立て工程で自動化を取り入れた。
同センサーは長さ1メートルにもなるゴム部品であり、持ち上げると曲がる。これを樹脂製の「ブラケット」に正確に沿わせながら取り付ける必要がある。従来はセンサーに両面テープを取り付け、ブラケットにはわせながら貼り付けるという手間がかかる作業だった。
自動化への課題は軟体部品の位置の制御と、はめ込む際の人間の指の感覚をロボットでどう再現するかだった。これを解決するために、はめ込む際に必要とされる圧力や角度についてセンシングにより最適な条件を模索したり、軟体部品の位置を安定して保持させる機構を考えたりした。「人は『良い具合』や『何となく』の感触で組み立てられる。一方でロボットは決められた力や場所にしか行かない」と話すのは、グループ生産技術本部生技統括室の柴田幸治室長だ。車体カンパニー新豊工場の永田兼広工場長も「軟体部品は自動車メーカーも『最後のカン・コツ作業』と言っている。製造業が苦しんでいるところだ」と難しさを語る。
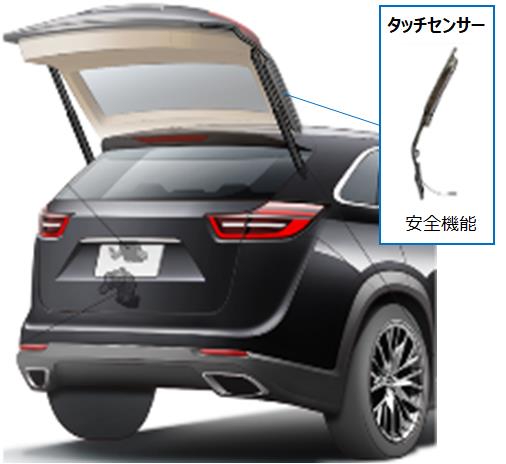
行き着いたのは製品構造の見直しだ。ブラケットにへこむ部分を設け、センサーを押し込むことで挟み込めるように変更した。産業用ロボットがブラケットの40―50カ所あるへこみ部に移動しながら正確にセンサーをはめ込むことが可能になった。車両のボディーやブラケットの形状が変更しても対応できるようにロボットハンドを自社で開発する。将来の変更や改善を行えるように柔軟性(フレキシビリティー)を持たせる工夫も施した。困難はあったが乗り越えたことで得られる成果も大きい。構造変更も加えることで、人による作業に比べ生産性を2・6倍に向上した。
同工場では2017年ごろから自動化を本格的に進めてきた。シート向け機構部品はプレス加工した硬質部品が多く、自動化率は高い。一方、バックドアなど軟体部品を使用する作業については人手が大半を占めていた。徐々に改善を進めており、22年には工程の半分以上を自動化した。25年にはシート向け部品と同程度の高水準の自動化率を目指す。永田工場長は「今後は(軟体部品の自動化に関する)ノウハウを国内外の他ラインや工場にも広げたい」とさらなる改善に意欲を燃やす。
【関連記事】 トヨタグループも頼りにする異能の変革集団
【関連記事】 デンソーも注目、岐阜の「改革マスター」とは?