40年以上ロボットと働く自動車部品メーカー、長い経験が築き上げた強み
経験生かし外販積極化
ヒロテックがロボットを初めて導入したのは1980年頃。スポット溶接用のロボットで「大きくて取り回しが悪かった」(鵜野政人会長)という苦い経験が、ロボットを自社開発するきっかけになった。
90年代には、多軸アーム型ロボットや自動搬送装置を開発。ただ、7軸のロボットは量産化を目指した時期もあったが、価格面などで断念した。その後、研究を継続しつつ、単純作業や重労働現場を自動化し、「現在、重労働は、ほぼロボットに代替できている」(同)と話す。
15年1月、オンリーワン技術の開発や、生産現場の課題解決を担う生産技術研究所を設立。「別角度による発想や視点が工程の見直しにつながり、職場が活性化して社員も前向きになった」(同)とその効果を説く。
最近の事例では、19年5月、自動車用ドアのアウター(外装部)とインナー(内装部)の端を押し曲げて接合するヘミング加工にロボットを導入した。
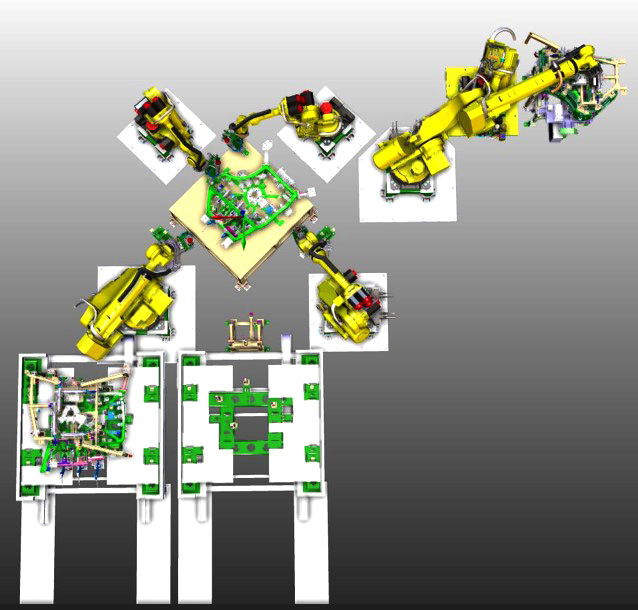
以前は、車種別に作ったヘミング用金型をダイチェンジャー(金型交換台車)でプレス機にセットし、アウターとインナーを2台のロボットでプレス機に出し入れして加工していた。ドア1点当たり48秒かかり、5人の人員が必要だった。
この作業をすべてロボットに置換した。まず導入に向け、ロボットでつかめるほど軽量で、ヘミング加工にも歪まないアウターとインナーを固定するアンビル(治具)や、ロボットの先に付けてヘミング加工するローラーヘッドを開発した。
二つのアンビルを2台のロボットで上下を合わせて作業台にセットし、4台のローラーヘミング用ロボットで加工する。
結果、ドア1点の加工時間は同等だが、最終検査員以外の4人の作業を自動化。さらに高価で場所を取るダイチェンジャーやプレス機が不要となり、48%の省スペース化につなげた。
現在、生産技術研究所は五つの研究室を抱え、生産システムの開発やロボットを構成する頭、目、手の研究にまい進している。
外販製品では、18年2月に箱積みロボットシステムを完成。箱の大きさをカメラで認識し、つかむと同時に箱の重さを計り、良否を判断、約100通りに積める。そのほか、部品の整列、フタ締めなどのロボットシステムも開発した。20年7月に外販部門を設け、分野を問わず販売を強化。足元で海外も含め、10数社に納入した。
鵜野会長は「24時間365日働く無人工場が目標だが、永遠の課題」と話すが、意欲満々、士気も高い。