自動車部品の金属から樹脂への流れに乗れ!“スーパー繊維”向け抜き型
ハガタ屋、厚み10cm対応。歯車のメーカーなどに提案
ハガタ屋(香川県東かがわ市、喜岡達社長)は、高強度・高弾性の特性を持つスーパー繊維の単一厚物素材を打ち抜く専用抜き型を開発、受注を始めた。厚み10センチメートルまでの積層しない単一素材を打ち抜くことができる。価格は個別見積もりの対応となるが、直径10センチ×高さ5センチメートルの抜き型で約100万円(消費税抜き)からを想定する。
ハガタ屋は自動車用トランスミッションなどで今後、スーパー繊維を用いた樹脂歯車の利用が広がると判断し、専用抜き型を開発した。自動車用歯車のメーカーなどに提案していく。
現在、一部の自動車の部品にスーパー繊維織物の積層素材を使った樹脂が使用されている。ただ、より強度が必要なトランスミッションの歯車での使用は、積層素材の層間剥離が起こるなどの課題があり、単一で肉厚の素材を抜く型が求められている。
同社は鍛造抜き型のメーカー。炭素繊維強化プラスチック(CFRP)の打ち抜き型を手がけるほか、アラミドやポリパラフェニレンベンズオキサゾール(PBO)など各種スーパー繊維の素材に応じた刃先を製作。重ね抜きや積層素材に対応した抜き型を製造している。
ハガタ屋は自動車用トランスミッションなどで今後、スーパー繊維を用いた樹脂歯車の利用が広がると判断し、専用抜き型を開発した。自動車用歯車のメーカーなどに提案していく。
現在、一部の自動車の部品にスーパー繊維織物の積層素材を使った樹脂が使用されている。ただ、より強度が必要なトランスミッションの歯車での使用は、積層素材の層間剥離が起こるなどの課題があり、単一で肉厚の素材を抜く型が求められている。
同社は鍛造抜き型のメーカー。炭素繊維強化プラスチック(CFRP)の打ち抜き型を手がけるほか、アラミドやポリパラフェニレンベンズオキサゾール(PBO)など各種スーパー繊維の素材に応じた刃先を製作。重ね抜きや積層素材に対応した抜き型を製造している。
日刊工業新聞2017年1月12日
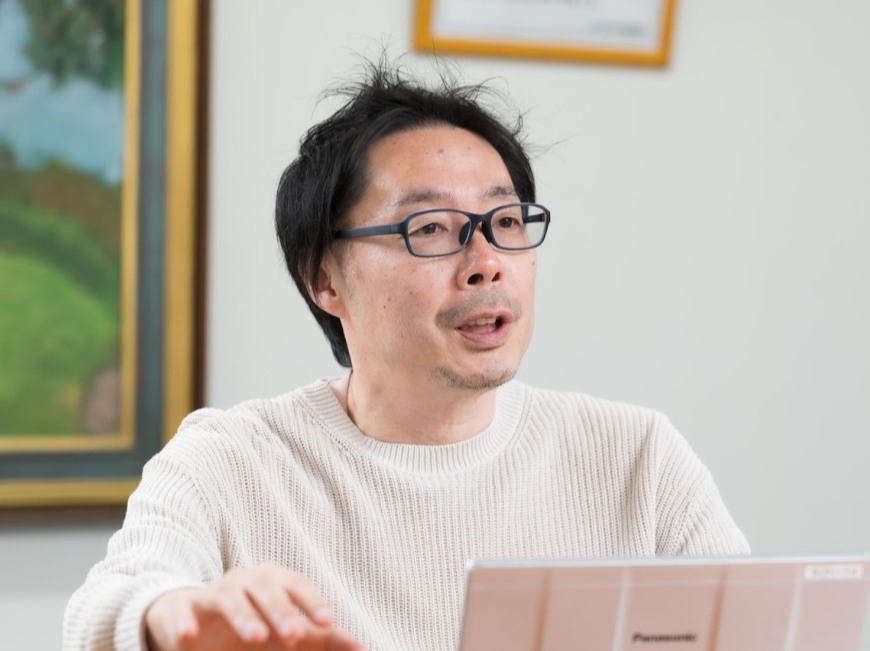