IoTで海外工場を一括管理。三菱製鋼が自動車用バネで遠隔監視を導入する狙い
高性能の評価試験装置などを活用し生産状況を把握
三菱製鋼はIoT(モノのインターネット)や高性能の評価試験装置などを活用し、海外工場の操業を支援する。主に自動車用バネ製品において、海外工場に設置したセンサーや監視カメラなどの情報から国内で生産状況を常時監視し、品質や安全性の向上を図る。さらに高精度顕微鏡や特殊な測定機を導入し、海外製の材料を試験・評価することで、現地調達比率の向上につなげる。
いずれもバネの主力製造拠点である千葉製作所(千葉県市原市)内の技術開発センターが主体を担う。現在、自動車メーカーのグローバル化に合わせ、海外生産を急速に展開中。
米国、カナダ、メキシコ(工場建設中)、中国(同増設中)、インドに加え、近く欧州にも工場を新設する。海外に供給する国内の人材が追いつかないこともあり、IoTによって日本から遠隔で海外工場を一括管理できる体制を敷く。
具体的には、生産ラインの稼働状況を常時監視し、生産計画に沿って操業しているかどうかを日本から確認できるようにする。センサーとカメラで設備の振動や音の変化などを監視し、予防保全につなげる。
また、製造品目をすべてデータ管理し、不良品が出た場合は生産工程までさかのぼり、映像などで原因を確認できるようにする。「ユーザーからクレームが入ったら、すぐにひも付けされたデータで照会し、映像を交えてその生産状況を説明できる」(技術開発センター)という。
一方、海外工場では基本的に部材の現地調達率100%を目指している。現地の部材の評価試験を国内の最新鋭装置で集中的かつ効率的に行うことで、ユーザー認証の取得などをサポートする。
技術開発センターでは2018年までの3年間に約21億円を投じ、レーザー顕微鏡やねじり試験機、高温クリープ試験装置などを順次導入する予定。人員も現在の31人から20年には55人まで増やす。これらを海外の材料の分析・評価にも活用する。
このほか、海外工場向けに巻きバネのコンパクトラインを開発。設置面積を3分の1に縮小したもので、投資額も3分の1から4分の1に抑えられる。これまでより生産量が見込めない比較的、小規模な国・地域にも進出しやすくなる。
生産能力は5分の1程度のため、生産効率はやや悪いが、「IoTで補完することで人員など固定費は減らせる」(同)という。スタビライザーのコンパクトラインも年度内に開発を終える予定だ。
いずれもバネの主力製造拠点である千葉製作所(千葉県市原市)内の技術開発センターが主体を担う。現在、自動車メーカーのグローバル化に合わせ、海外生産を急速に展開中。
米国、カナダ、メキシコ(工場建設中)、中国(同増設中)、インドに加え、近く欧州にも工場を新設する。海外に供給する国内の人材が追いつかないこともあり、IoTによって日本から遠隔で海外工場を一括管理できる体制を敷く。
具体的には、生産ラインの稼働状況を常時監視し、生産計画に沿って操業しているかどうかを日本から確認できるようにする。センサーとカメラで設備の振動や音の変化などを監視し、予防保全につなげる。
また、製造品目をすべてデータ管理し、不良品が出た場合は生産工程までさかのぼり、映像などで原因を確認できるようにする。「ユーザーからクレームが入ったら、すぐにひも付けされたデータで照会し、映像を交えてその生産状況を説明できる」(技術開発センター)という。
一方、海外工場では基本的に部材の現地調達率100%を目指している。現地の部材の評価試験を国内の最新鋭装置で集中的かつ効率的に行うことで、ユーザー認証の取得などをサポートする。
技術開発センターでは2018年までの3年間に約21億円を投じ、レーザー顕微鏡やねじり試験機、高温クリープ試験装置などを順次導入する予定。人員も現在の31人から20年には55人まで増やす。これらを海外の材料の分析・評価にも活用する。
このほか、海外工場向けに巻きバネのコンパクトラインを開発。設置面積を3分の1に縮小したもので、投資額も3分の1から4分の1に抑えられる。これまでより生産量が見込めない比較的、小規模な国・地域にも進出しやすくなる。
生産能力は5分の1程度のため、生産効率はやや悪いが、「IoTで補完することで人員など固定費は減らせる」(同)という。スタビライザーのコンパクトラインも年度内に開発を終える予定だ。
日刊工業新聞2016年9月26日
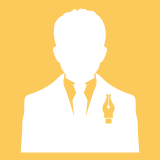