JSRやANAなどが樹脂製義足を共同開発。3Dプリンターでコスト7割減
来年の販売目指す
JSRと全日本空輸(ANA)、SHCデザイン(神奈川県茅ケ崎市)は29日、3Dプリンターで造形する樹脂製の義足を共同開発したと発表した。金属部品を含む一般の義足に比べ軽く、生産コストも20―30%程度に抑えられる。2017年の販売を目指す。
JSRが展開する糸状の樹脂材料(フィラメント)「ファブリアル」を使い、SHCデザインが仕上げた。義足を使用しているANAの社員が実際に装着もし、空港の保安検査場や各種サービスにおける使い勝手を検証。航空会社として可能なサポートを検討する。
義足は金属の部品を含むためサビが発生する懸念があり、海岸や温泉で使えない課題がある。また空港の保安検査でもセンサーが反応するため、改めて係員のチェックを受ける必要があった。
JSRが展開する糸状の樹脂材料(フィラメント)「ファブリアル」を使い、SHCデザインが仕上げた。義足を使用しているANAの社員が実際に装着もし、空港の保安検査場や各種サービスにおける使い勝手を検証。航空会社として可能なサポートを検討する。
義足は金属の部品を含むためサビが発生する懸念があり、海岸や温泉で使えない課題がある。また空港の保安検査でもセンサーが反応するため、改めて係員のチェックを受ける必要があった。
日刊工業新聞2016年8月30日
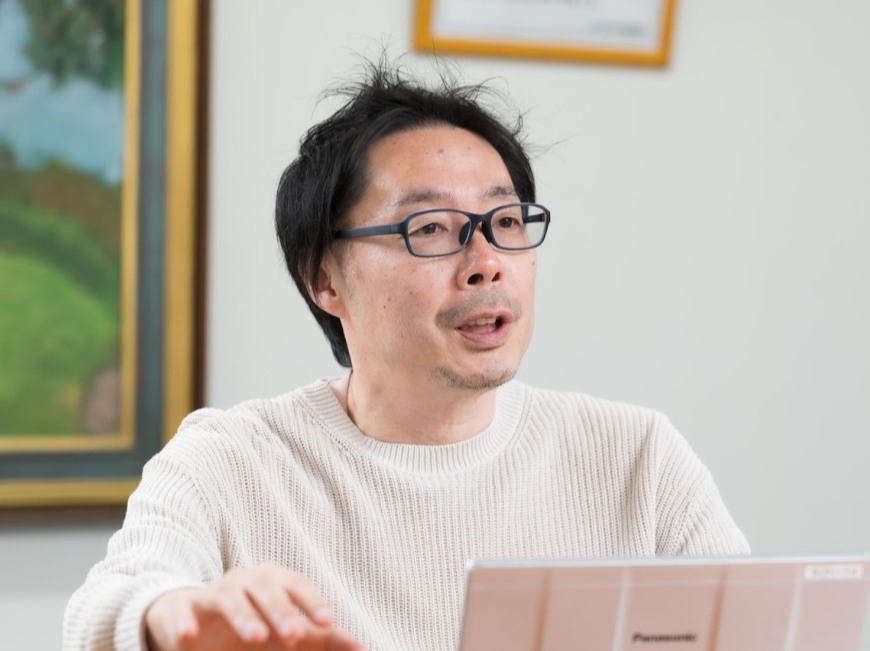