【日本の科学技術力#01】カーボンナノチューブ、見えてきた産業応用
材料を育ててくれる用途を見つけられるか、この2-3年が正念場
さまざまな分野でイノベーションの礎となってきた日本の科学技術。産業応用に加え、社会問題を解決する手段としての期待も高く、先進性や独創性に満ちあふれた研究テーマは数多い。こうしたテーマの背景や成果、今後の可能性にシリーズで迫る。初回は、「カーボンナノチューブ」(CNT)。
カーボンナノチューブは、直径が数ナノメートル(ナノは10億分の1)と微細な筒状の炭素分子。1991年の飯島澄男名城大学教授(当時NEC主席研究員)による発見から25年が経過し、産業応用へ大きな節目を迎えている。
高品質なCNTの量産が始まって安定供給が保証されたため、電子部品などのメーカーがCNTを使った製品を開発できるようになった。電子部品など最終製品として市場競争に勝てる商品に仕上げる技術開発が今後、本格化する。
理想的な単層CNTは、比重がアルミの半分で強度は鉄鋼の20倍、電子移動度はシリコンの約10倍。流せる電流量は銅の1000倍、熱伝導性も銅の5倍以上と画期的な性質を持つ。素材としての魅力は大きく、幅広い産業で実用化が試されてきた。
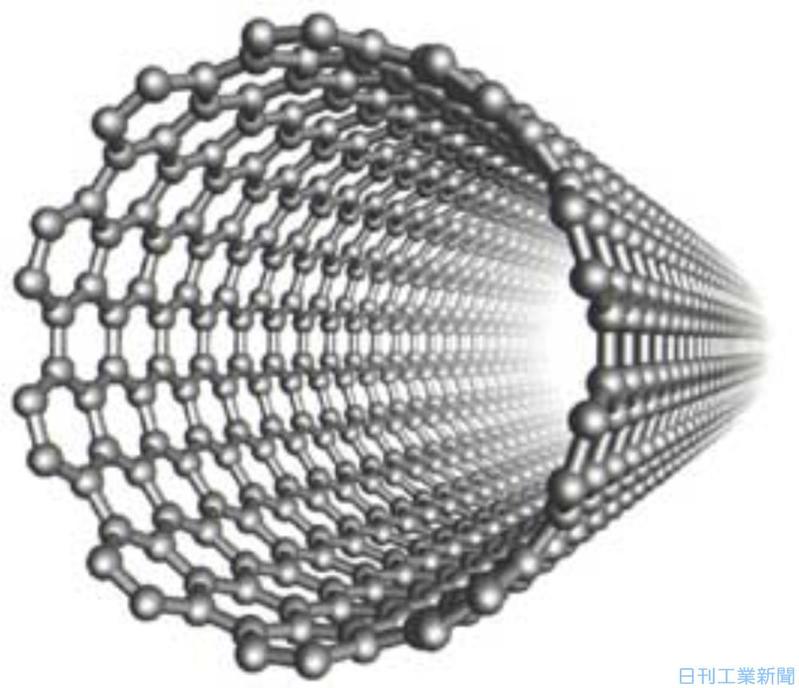
(CNTの構造図)
当初は薄型ディスプレーや医療への応用に期待が集まり、関連企業がCNT研究に投資した。これがCNTの物性研究や合成法などの基礎研究を支えた。欧米や中国では投資家から資金を集め、CNTの量産に挑戦したベンチャー(VB)は少なくない。飯島教授は「実はCNTを作るだけなら高校生でも可能だ」と指摘する。
ただ、半導体産業の求める品質や、自動車産業の求めるコストで作るとなると話は別だ。実際に応用CNT製品の開発に着手すると材料コストや安全検証コストがネックとなってきた。薄型ディスプレーは液晶ディスプレーの価格下落で開発が下火となった。多くのVBが廃業したことなども背景にあり、現在もCNTの用途開発が続いている。
飯島教授は「大学の研究者はデバイスを作れば論文になる。世界の一流科学雑誌の表紙を飾り、脚光を浴びることも可能だが、事業化は別だ。量産できるのか、採算は合うのかと問われ、応えられる研究者は大学にはいない」と説明する。
材料研究者の成果を実用化するには、材料メーカーの製造プロセスのノウハウと、最終製品の設計ノウハウが必要だった。そこで新エネルギー・産業技術総合開発機構(NEDO)はCNTの基礎研究者と材料メーカー、最終製品メーカーを巻き込んだ開発プロジェクトを進めている。
現在は樹脂複合材料や電子部品などの企業が、実用化の推進役になっている。日本ゼオンは材料メーカーとして製造ノウハウを提供し、産業技術総合研究所が開発した合成技術を工場での量産プロセスとして確立した。並行して樹脂とCNTの複合材を開発し、高機能複合材として商品化を進めている。
日信工業は耐熱性ゴムを開発。日本ケミコンはCNTの表面積の大きさを利用した大容量キャパシターを開発している。NEDO材料・ナノテクノロジー部の小久保研主査は「16年度はCNTの応用製品を開発するための基盤技術を発表できる。17年度にはCNTを使った中間部材製品の供給を始める。その後、CNT応用製品が世に出ていく予定だ」と説明する。
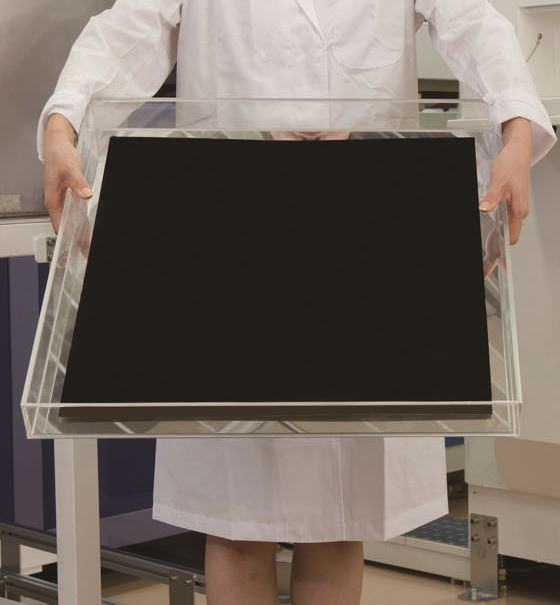
(産総研が開発したCNT合成法のCNT基板=産総研提供)
CNTの分散技術や樹脂との混合技術などの基盤技術は、最終製品メーカーが製品を開発する上で必須の技術だ。例えば添加剤は、その後の製造工程に大きく影響するが、一般には材料メーカーが製造ノウハウとして囲い込んでしまう。
産総研はこの基盤技術を体系化した。基盤技術を広く提供して最終製品の開発を促すことや、ノウハウとして隠して材料メーカーの競争力とすることが可能になる。17年度に中間部材が提供されれば「CNT応用製品の開発は目に見える形で加速する」(小久保主査)と期待する。
CNTの発見には電子顕微鏡の進化が大きな役割を果たしている。飯島教授は電子顕微鏡のスペシャリストで、71年にはニオブ酸化物結晶中の金属原子を直接観察することに成功。73年には結晶中の点欠陥を原子レベルの分解能で撮影した。結晶欠陥構造の解析法は半導体産業で欠かせない手法となった。
電子顕微鏡の技術開発は、半導体産業の興隆を下支えした。70年代以前は独シーメンスと蘭フィリップスが開発を主導しており、日立製作所や日本電子などの日本勢が食い込もうとしていた。
日本から世界最高性能の装置が出始めたタイミングで、飯島教授の計測技術が登場し、材料研究や半導体の開発を加速させた。飯島教授は「91年にCNTを見つけるまで20年以上の蓄積がある。技術がそろっていたところに幸運にもCNTと出合った」と振り返る。
一方、半導体産業の発展を後押ししたのは、電子顕微鏡だけではない。シリコン(ケイ素)の材料開発も切り開いた。シリコンの製造プロセスは幅広く、コスト競争力も高い。
CNTの実用化に向けて、シリコンは巨大の壁として立ちはだかっている。飯島教授は「シリコンと比べればCNTまだ未熟。研究の厚みが違う。CNTの実用化には泥臭い研究に打ち込める挑戦者が求められている」と話す。
(文=小寺貴之)
※随時掲載
カーボンナノチューブは、直径が数ナノメートル(ナノは10億分の1)と微細な筒状の炭素分子。1991年の飯島澄男名城大学教授(当時NEC主席研究員)による発見から25年が経過し、産業応用へ大きな節目を迎えている。
高品質なCNTの量産が始まって安定供給が保証されたため、電子部品などのメーカーがCNTを使った製品を開発できるようになった。電子部品など最終製品として市場競争に勝てる商品に仕上げる技術開発が今後、本格化する。
理想的な単層CNTは、比重がアルミの半分で強度は鉄鋼の20倍、電子移動度はシリコンの約10倍。流せる電流量は銅の1000倍、熱伝導性も銅の5倍以上と画期的な性質を持つ。素材としての魅力は大きく、幅広い産業で実用化が試されてきた。
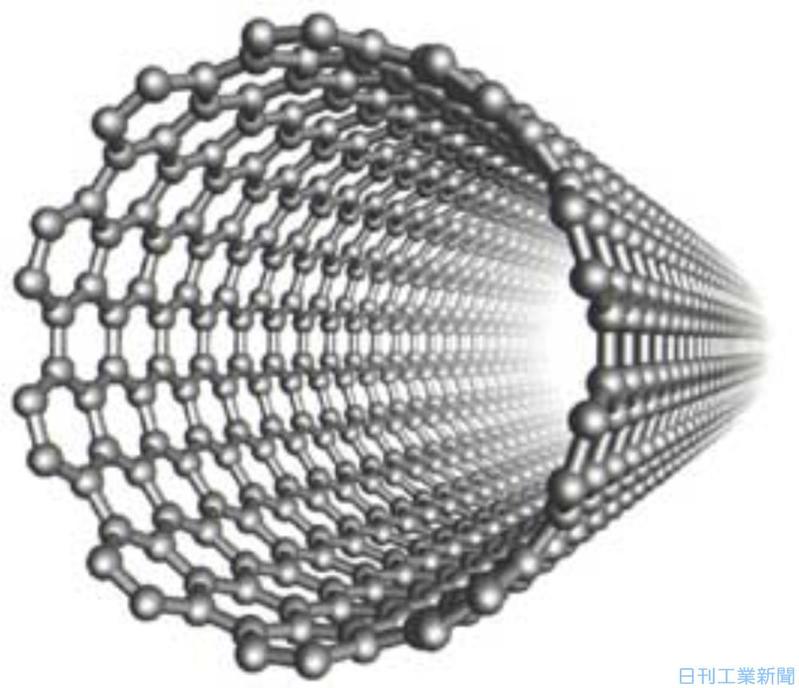
(CNTの構造図)
材料や安全検証のコストがネックに
当初は薄型ディスプレーや医療への応用に期待が集まり、関連企業がCNT研究に投資した。これがCNTの物性研究や合成法などの基礎研究を支えた。欧米や中国では投資家から資金を集め、CNTの量産に挑戦したベンチャー(VB)は少なくない。飯島教授は「実はCNTを作るだけなら高校生でも可能だ」と指摘する。
ただ、半導体産業の求める品質や、自動車産業の求めるコストで作るとなると話は別だ。実際に応用CNT製品の開発に着手すると材料コストや安全検証コストがネックとなってきた。薄型ディスプレーは液晶ディスプレーの価格下落で開発が下火となった。多くのVBが廃業したことなども背景にあり、現在もCNTの用途開発が続いている。
飯島教授は「大学の研究者はデバイスを作れば論文になる。世界の一流科学雑誌の表紙を飾り、脚光を浴びることも可能だが、事業化は別だ。量産できるのか、採算は合うのかと問われ、応えられる研究者は大学にはいない」と説明する。
NEDOが背中を押す開発プロジェクト
材料研究者の成果を実用化するには、材料メーカーの製造プロセスのノウハウと、最終製品の設計ノウハウが必要だった。そこで新エネルギー・産業技術総合開発機構(NEDO)はCNTの基礎研究者と材料メーカー、最終製品メーカーを巻き込んだ開発プロジェクトを進めている。
現在は樹脂複合材料や電子部品などの企業が、実用化の推進役になっている。日本ゼオンは材料メーカーとして製造ノウハウを提供し、産業技術総合研究所が開発した合成技術を工場での量産プロセスとして確立した。並行して樹脂とCNTの複合材を開発し、高機能複合材として商品化を進めている。
日信工業は耐熱性ゴムを開発。日本ケミコンはCNTの表面積の大きさを利用した大容量キャパシターを開発している。NEDO材料・ナノテクノロジー部の小久保研主査は「16年度はCNTの応用製品を開発するための基盤技術を発表できる。17年度にはCNTを使った中間部材製品の供給を始める。その後、CNT応用製品が世に出ていく予定だ」と説明する。
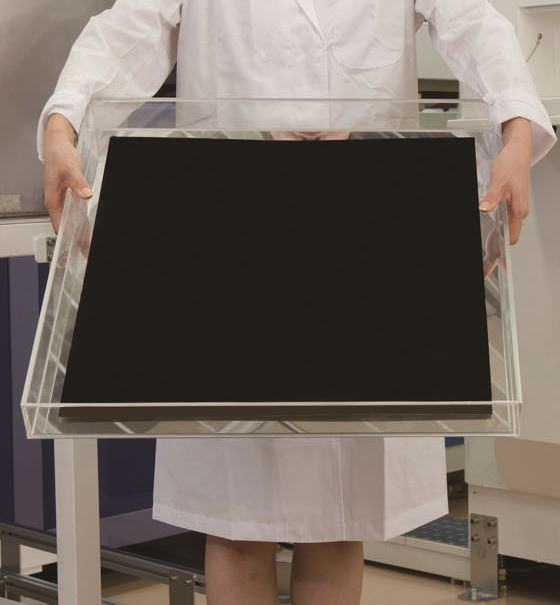
(産総研が開発したCNT合成法のCNT基板=産総研提供)
製造ノウハウを囲い込まないよう体系化
CNTの分散技術や樹脂との混合技術などの基盤技術は、最終製品メーカーが製品を開発する上で必須の技術だ。例えば添加剤は、その後の製造工程に大きく影響するが、一般には材料メーカーが製造ノウハウとして囲い込んでしまう。
産総研はこの基盤技術を体系化した。基盤技術を広く提供して最終製品の開発を促すことや、ノウハウとして隠して材料メーカーの競争力とすることが可能になる。17年度に中間部材が提供されれば「CNT応用製品の開発は目に見える形で加速する」(小久保主査)と期待する。
CNTの発見には電子顕微鏡の進化が大きな役割を果たしている。飯島教授は電子顕微鏡のスペシャリストで、71年にはニオブ酸化物結晶中の金属原子を直接観察することに成功。73年には結晶中の点欠陥を原子レベルの分解能で撮影した。結晶欠陥構造の解析法は半導体産業で欠かせない手法となった。
電子顕微鏡の技術開発は、半導体産業の興隆を下支えした。70年代以前は独シーメンスと蘭フィリップスが開発を主導しており、日立製作所や日本電子などの日本勢が食い込もうとしていた。
「シリコンと比べればCNTまだ未熟」
日本から世界最高性能の装置が出始めたタイミングで、飯島教授の計測技術が登場し、材料研究や半導体の開発を加速させた。飯島教授は「91年にCNTを見つけるまで20年以上の蓄積がある。技術がそろっていたところに幸運にもCNTと出合った」と振り返る。
一方、半導体産業の発展を後押ししたのは、電子顕微鏡だけではない。シリコン(ケイ素)の材料開発も切り開いた。シリコンの製造プロセスは幅広く、コスト競争力も高い。
CNTの実用化に向けて、シリコンは巨大の壁として立ちはだかっている。飯島教授は「シリコンと比べればCNTまだ未熟。研究の厚みが違う。CNTの実用化には泥臭い研究に打ち込める挑戦者が求められている」と話す。
(文=小寺貴之)
※随時掲載
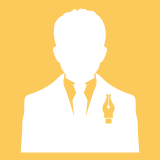