FAオープン化の波、国内王者の三菱電機が考えていること
担当役員に聞く。
プログラマブルロジックコントローラー(PLC)、サーボモーターなど工場自動化(FA)機器で高いシェアを誇る三菱電機。FA機器と管理ソフトウエアなどを一括提供し製造革新に導く「e―ファクトリー」を展開している。IoT(モノのインターネット)の普及でFAにさらなる進化が求められる中、業界大手として新時代にどう向き合うのか。漆間啓常務執行役FAシステム事業担当に戦略を聞いた。
―IoTの時代に向けe―ファクトリーをどう進化させますか。
「すでに300社近くと組み、多様な機器、ソフトを製造現場に提供できるようになっている。だが今後は製造だけでなく、設計、調達、販売、サービスなども支援できるようにしていく必要がある。このため、協業の幅をもっと広げていきたい」
―調達などサプライチェーンの領域に踏み込むとなると、競合他社の製品と連携する必要も出てきます。
「ドイツなどで構想される第4次産業革命は基本的にオープンな世界。オープン化に対応できなければ、流れに乗り遅れる。従って将来には(e―ファクトリーと競合製品が)つながるようにするべきだと思う」
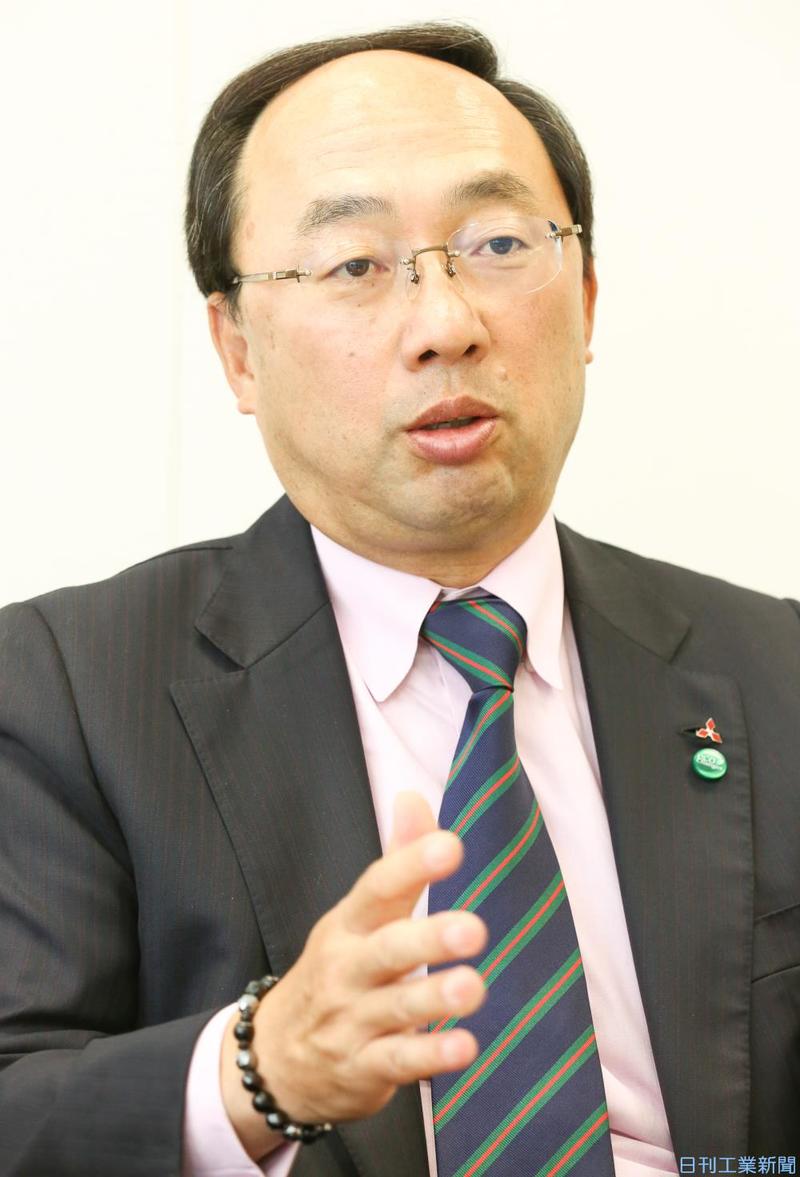
(漆間氏)
―競合他社が提唱し始めたオープン型のIoT基盤に参加するつもりはありますか。
「可能性はある。ただ、まずはe―ファクトリーのオープン化を目指したい。順番として(競合のシステムに参画するのは)その後になる」
―4月にレーザー加工機向けIoTサービス「iQケアリモート4U」を始めました。
「加工機の遠隔診断を可能にし、稼働停止時間の低減に貢献することが目的。まだ始めたばかりなので未知数だが、興味を持っているユーザーが非常に多いのは確かだ。今後は故障の予知なども可能にしていきたい」
―IoTの普及でFA業界はどう変化していくのでしょう。
「ここ1年ほど、IoTに対するユーザーの関心度は驚くほど高い。ユーザー側も大きく変わろうとしている。その中で、他の一歩先を行くことが大事だ。e―ファクトリーをベースに課題解決型の事業形態にしていくべきだと思う」
【記者の目・新時代の旗手へ変容期待】
ハードウエアの信頼性を強みに発展してきた日本のFA機器業界。だが欧米などで構想されるIoT革命は、ハードよりソフトに重きを置いたものだ。競合のファナックは、情報系企業と組み独自のIoT基盤を提唱し始めた。三菱電機もハード主体から課題解決型への転換を目指すという。巨大な既存ビジネスを抱える中、どれだけ劇的に変わり、時代の変化をリードできるかが見どころだ。
(聞き手=藤崎竜介)
三菱電機は2016年度から国内の自社工場を対象に、モノのインターネット(IoT)技術を使った生産革新を本格的に始める。データを収集・分析する生産システム「e―ファクトリー」を中核に据え、発電機やパワー半導体の工場など少なくとも10―20程度の工場で着手する。1年かけてコスト削減などの効果を実証し、17年度から生産革新の仕組みを外販する。
すでにFA機器を生産する名古屋製作所と、ブレーカーを作る福山製作所でIoTを採用し生産革新を進めていた。自動化しやすい量産品の工場ではIoTとの親和性が高いためだ。今後は発電機など受注生産品の工場でも採用し、国内で全面的に展開する。
事業領域を絞らずに各工場からIoT活用の立候補を募り、生産革新の具体案を提出させて年度内に決める計画。コスト削減や品質・歩留まり改善、製造期間の短縮など目的に応じ、各種センサーやe―ファクトリーなどを導入する。
e―ファクトリーは工場の各種設備からデータを収集・分析する。課題を”見える化“し、生産効率や品質の向上に結びつける。e―ファクトリーを中心にIoTの仕組みを導入し「自社工場で高い生産性を示す」(同社)。さらに蓄積したノウハウを生かし、製造業の顧客にシステムとして提供する。
同業では日立製作所が16年度にサーバーやストレージ(外部記憶装置)の工場でIoT技術を採用する。生産ラインにセンサーを設置して稼働状況を把握し、多品種少量生産の効率を高める意向だ。NECも16年度から国内外の主要生産拠点でIoT活用の標準システムを導入する。
IoTの活用は米国やドイツが先行しているが、日本の主要メーカーでも工場で使う動きが広がってきた。
―IoTの時代に向けe―ファクトリーをどう進化させますか。
「すでに300社近くと組み、多様な機器、ソフトを製造現場に提供できるようになっている。だが今後は製造だけでなく、設計、調達、販売、サービスなども支援できるようにしていく必要がある。このため、協業の幅をもっと広げていきたい」
―調達などサプライチェーンの領域に踏み込むとなると、競合他社の製品と連携する必要も出てきます。
「ドイツなどで構想される第4次産業革命は基本的にオープンな世界。オープン化に対応できなければ、流れに乗り遅れる。従って将来には(e―ファクトリーと競合製品が)つながるようにするべきだと思う」
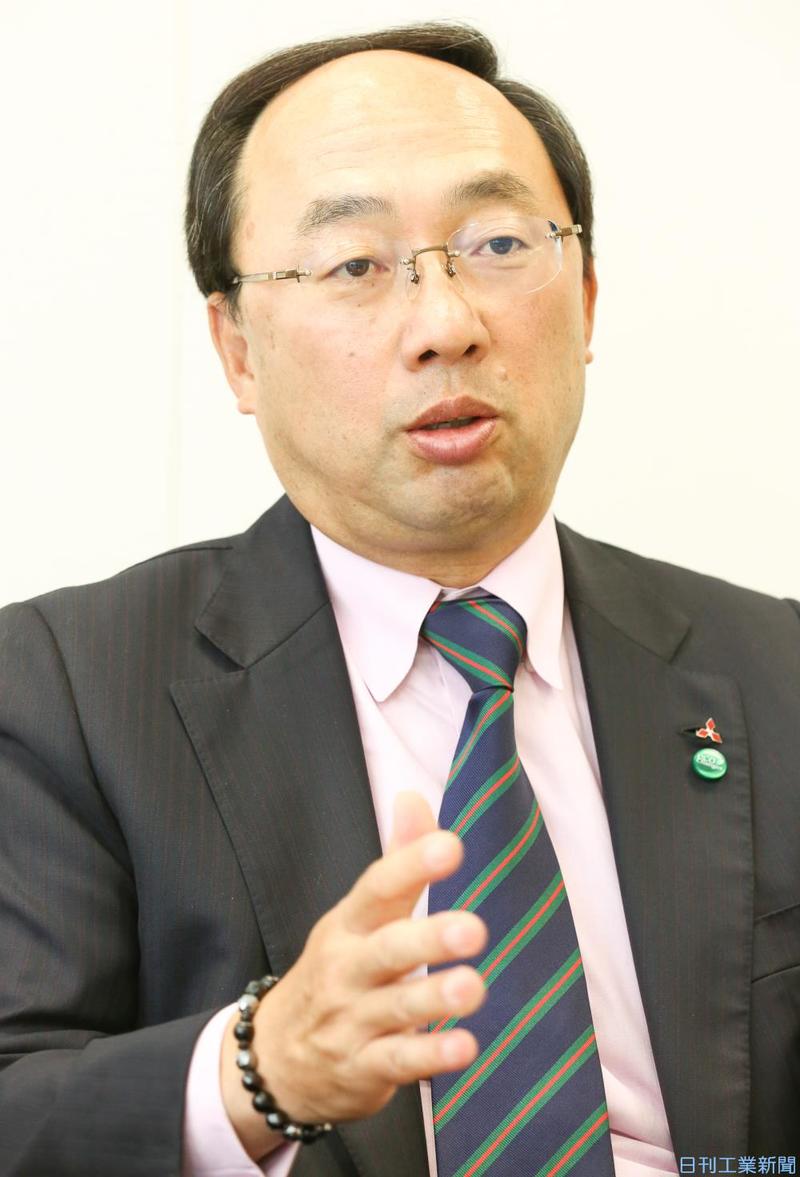
(漆間氏)
―競合他社が提唱し始めたオープン型のIoT基盤に参加するつもりはありますか。
「可能性はある。ただ、まずはe―ファクトリーのオープン化を目指したい。順番として(競合のシステムに参画するのは)その後になる」
―4月にレーザー加工機向けIoTサービス「iQケアリモート4U」を始めました。
「加工機の遠隔診断を可能にし、稼働停止時間の低減に貢献することが目的。まだ始めたばかりなので未知数だが、興味を持っているユーザーが非常に多いのは確かだ。今後は故障の予知なども可能にしていきたい」
―IoTの普及でFA業界はどう変化していくのでしょう。
「ここ1年ほど、IoTに対するユーザーの関心度は驚くほど高い。ユーザー側も大きく変わろうとしている。その中で、他の一歩先を行くことが大事だ。e―ファクトリーをベースに課題解決型の事業形態にしていくべきだと思う」
【記者の目・新時代の旗手へ変容期待】
ハードウエアの信頼性を強みに発展してきた日本のFA機器業界。だが欧米などで構想されるIoT革命は、ハードよりソフトに重きを置いたものだ。競合のファナックは、情報系企業と組み独自のIoT基盤を提唱し始めた。三菱電機もハード主体から課題解決型への転換を目指すという。巨大な既存ビジネスを抱える中、どれだけ劇的に変わり、時代の変化をリードできるかが見どころだ。
(聞き手=藤崎竜介)
IoT使い生産革新、20工場で実証
日刊工業新聞2016年1月12日
三菱電機は2016年度から国内の自社工場を対象に、モノのインターネット(IoT)技術を使った生産革新を本格的に始める。データを収集・分析する生産システム「e―ファクトリー」を中核に据え、発電機やパワー半導体の工場など少なくとも10―20程度の工場で着手する。1年かけてコスト削減などの効果を実証し、17年度から生産革新の仕組みを外販する。
すでにFA機器を生産する名古屋製作所と、ブレーカーを作る福山製作所でIoTを採用し生産革新を進めていた。自動化しやすい量産品の工場ではIoTとの親和性が高いためだ。今後は発電機など受注生産品の工場でも採用し、国内で全面的に展開する。
事業領域を絞らずに各工場からIoT活用の立候補を募り、生産革新の具体案を提出させて年度内に決める計画。コスト削減や品質・歩留まり改善、製造期間の短縮など目的に応じ、各種センサーやe―ファクトリーなどを導入する。
e―ファクトリーは工場の各種設備からデータを収集・分析する。課題を”見える化“し、生産効率や品質の向上に結びつける。e―ファクトリーを中心にIoTの仕組みを導入し「自社工場で高い生産性を示す」(同社)。さらに蓄積したノウハウを生かし、製造業の顧客にシステムとして提供する。
同業では日立製作所が16年度にサーバーやストレージ(外部記憶装置)の工場でIoT技術を採用する。生産ラインにセンサーを設置して稼働状況を把握し、多品種少量生産の効率を高める意向だ。NECも16年度から国内外の主要生産拠点でIoT活用の標準システムを導入する。
IoTの活用は米国やドイツが先行しているが、日本の主要メーカーでも工場で使う動きが広がってきた。
日刊工業新聞2016年5月25日
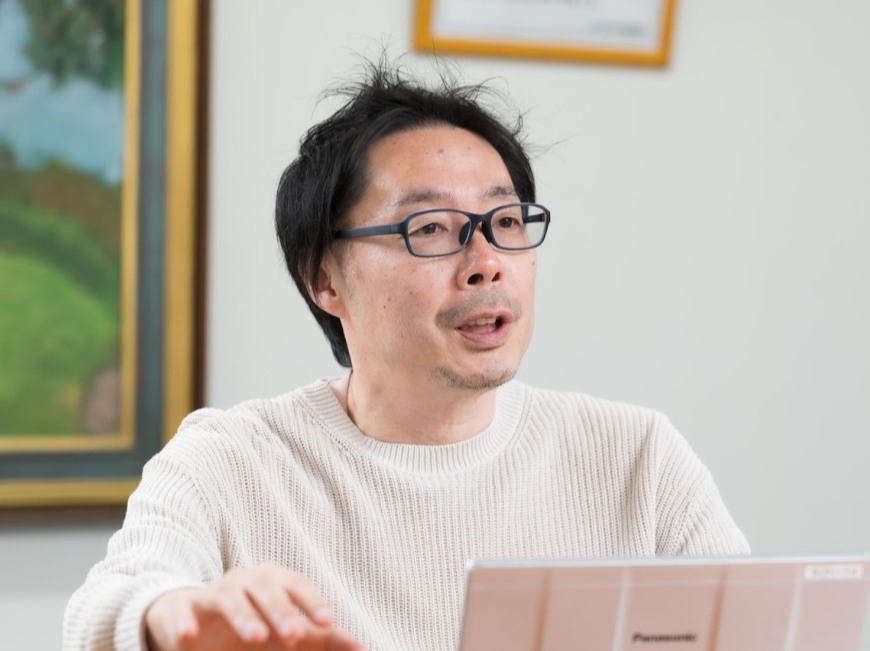