ホンダ、鋼板の高速切断をプレスからレーザーに置換え<追記あり>
業界で初めて寄居工場に導入。投資の抑制に直結
ホンダはレーザーで鋼板を高速切断する技術を開発した。小型車「フィット」などを生産する寄居工場(埼玉県寄居町)に昨年4月から導入。ボディーを形作る鋼板の型抜きをする工程に活用している。主流のプレスからレーザーに置き換えるのは業界初の試み。その技術や狙いを追った。
ホンダが開発したのは「レーザーブランキング」。鋼板の型抜きはよくある工程だが普通使われるのは「プレスブランキング」だ。鋼板はトイレットペーパーのようなコイル状態で工場に納入される。
寄居工場主幹の岡明男氏はトイレットペーパーを例えにプレスとレーザーの違いをこう説明する。「紙のミシン目ごとにいったん停止して型抜きをするのがプレスで、紙を引き出し続けながら型抜きをするのがレーザーだ」。
レーザーブランキングは家電製品の筐体など小物では実用化されているが、車のような大物には不向きとされてきた。切り取り線が長くなると時間がかかるためだ。
したがって車に応用するにはレーザー加工の高速化がポイントになる。ホンダはレーザーヘッドを軽量化しヘッドが縦横に素早く移動できるシステムを開発。従来の4倍の毎分120メートルという世界最速の加工スピードを実現した。
もう一つのポイントがコンベヤー。鋼板はコンベヤーに乗って流れる。そのままレーザーを当てると鋼板と一緒にコンベヤーも切断してしまう。対策としてコンベヤーを折り畳んでくぼみを作り、鋼板にだけレーザーが当たるようにした。このくぼみは加工で生じる鉄粉を受けるゴミ箱の役割も担う。
レーザーヘッドが縦横無尽に動くのと同時に鋼板の下ではゴミ箱が動く。さらにその下ではコンベヤーが一定速度で動いて鋼板を流し続けるという仕組みだ。エイチアンドエフと開発した。
加工スピードはプレスに比べて7―8割にまでなった。はんこをポンと押すようなプレスのスピードには及ばないが応用できるレベルにした。加工精度も社内基準を満たした。
「高速でヘッドが動くからレーザーの焦点がぶれないように制御することが大変だった」とホンダエンジニアリング技術主任の奥中啓之氏。5年の開発期間の苦労を振り返る。
そこまでしてレーザーを導入したのは投資の抑制や省スペースにつながるからだ。プレスがないと金型が不要になり金型を置くスペースもいらない。重いプレス機がないと基礎工事が浮かせる。
コイルから引き出す際に鋼板をたわませて待機する「ルーピング」という深さ5メートルの空間も不要だ。このため初期投資は「装置自体はプレス機と同等だが基礎工事を含めた全体では安くできる」と長谷川清一技師は言う。
次の課題はランニングコストの検証。特にメンテナンスのしやすさだ。「鉄粉の掃除などプレスとはまったく別の世界」(奥中氏)という新たな課題に挑む。
レーザーブランキングは鉄だけでなくアルミやハイテン材にも適用できるといい、メンテナンス性をクリアできれば汎用的な技術になる可能性がある。
(文=池田勝敏)
ホンダが開発したのは「レーザーブランキング」。鋼板の型抜きはよくある工程だが普通使われるのは「プレスブランキング」だ。鋼板はトイレットペーパーのようなコイル状態で工場に納入される。
寄居工場主幹の岡明男氏はトイレットペーパーを例えにプレスとレーザーの違いをこう説明する。「紙のミシン目ごとにいったん停止して型抜きをするのがプレスで、紙を引き出し続けながら型抜きをするのがレーザーだ」。
レーザーブランキングは家電製品の筐体など小物では実用化されているが、車のような大物には不向きとされてきた。切り取り線が長くなると時間がかかるためだ。
加工スピードは毎分120メートル
したがって車に応用するにはレーザー加工の高速化がポイントになる。ホンダはレーザーヘッドを軽量化しヘッドが縦横に素早く移動できるシステムを開発。従来の4倍の毎分120メートルという世界最速の加工スピードを実現した。
もう一つのポイントがコンベヤー。鋼板はコンベヤーに乗って流れる。そのままレーザーを当てると鋼板と一緒にコンベヤーも切断してしまう。対策としてコンベヤーを折り畳んでくぼみを作り、鋼板にだけレーザーが当たるようにした。このくぼみは加工で生じる鉄粉を受けるゴミ箱の役割も担う。
レーザーヘッドが縦横無尽に動くのと同時に鋼板の下ではゴミ箱が動く。さらにその下ではコンベヤーが一定速度で動いて鋼板を流し続けるという仕組みだ。エイチアンドエフと開発した。
加工スピードはプレスに比べて7―8割にまでなった。はんこをポンと押すようなプレスのスピードには及ばないが応用できるレベルにした。加工精度も社内基準を満たした。
開発期間5年、レーザー焦点のブレ克服
「高速でヘッドが動くからレーザーの焦点がぶれないように制御することが大変だった」とホンダエンジニアリング技術主任の奥中啓之氏。5年の開発期間の苦労を振り返る。
そこまでしてレーザーを導入したのは投資の抑制や省スペースにつながるからだ。プレスがないと金型が不要になり金型を置くスペースもいらない。重いプレス機がないと基礎工事が浮かせる。
コイルから引き出す際に鋼板をたわませて待機する「ルーピング」という深さ5メートルの空間も不要だ。このため初期投資は「装置自体はプレス機と同等だが基礎工事を含めた全体では安くできる」と長谷川清一技師は言う。
メンテナンスのしやすさは段違い
次の課題はランニングコストの検証。特にメンテナンスのしやすさだ。「鉄粉の掃除などプレスとはまったく別の世界」(奥中氏)という新たな課題に挑む。
レーザーブランキングは鉄だけでなくアルミやハイテン材にも適用できるといい、メンテナンス性をクリアできれば汎用的な技術になる可能性がある。
(文=池田勝敏)
日刊工業新聞2016年4月1日
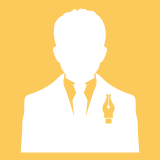