日本が世界をけん引、パワーエレクトロニクス最新事情
**松波弘之氏(京都大学名誉教授)
《実用化が進むパワー半導体SiCの最新動向》
これまでパワーデバイスは、Siを材料にして作られてきたが、SiCは現用のSiに比べて、約3倍の禁制帯幅を持つなどの特性があり、電力の損失を?分の1程度に抑えられることができるほか、耐圧性にも優れている。また熱にも強く、大がかりな冷却装置も必要ないことから、機器の小型化にも貢献できる。
最近ではIoT(モノのインターネット)、インダストリー4.0が注目を集めているが、ネットにおける電力使用量の増大は無視できない。そういった中でSiCや窒化ガリウム(GaN)といったワイドギャップ半導体は省エネに有効である。
SiCはさまざまな場面で優位性が唱えられたが、高品質の結晶を成長させる技術が確立するまではパワー半導体としての注目度は低かった。
我々は「ステップ制御エピタキシー」という高品質のSiCエピタキシャル結晶を成長させる方法を1987年に見いだした。これをきっかけにSiCの優れた特性を産業界で生かせると思ったが、経済成長の時期でSiCには関心が薄かった。
材料開発だけでは相手にされないと考え、これまでの研究成果をもとに耐圧1kVを超えるショットキーバリアダイオード(SBD)を提示し、電界効果トランジスタ(MOSFET)に対する見通しを立てた。企業の参画を促すために、いくつかの国家プロジェクトにつなげていった。
国家プロジェクトの支援を基に、現在は自動車や鉄道などで電力損失低減の実績から実用化が進んでいる。基礎研究レベルであるが、電力インフラに使える超高耐圧パワーデバイスは、グリーンイノベーションの実現に寄与できるほか、国際競争力の高い新産業の創出につながると考えている。
最近は、科学技術振興機構による京都スーパークラスタプログラム事業において、SiCパワーデバイスを搭載した省エネシステムの製品化および社会実装を目指したプログラムの支援をしている。地元中小企業を中心にした産産学連携による取り組みだけでなく、長野県、福井県、滋賀県にあるサテライトクラスタとの連携も加速している。
課題として高品質バルク成長と低価格化があるが、個人的にはSiCでしかできない応用の発掘、さらには使い方を考える若手の育成などに取り組む必要があると考えている。
《パワーエレクトロニクス革新の意義―国内の現状と産総研の取り組み》
パワエレの守備範囲は広範にわたるが、では”マイクロエレクトロニクス”と”パワーエレクトロニクス”とどう違うのか。前者は主に「情報、信号」を扱うのに対して、後者は「エネルギー」を扱うという点で半導体デバイス構造も大きく変わってくる。
パワエレの場合、デバイス性能として高耐圧、低オン抵抗、大電流動作などの性能が求められるわけだが、SiCやGaNといったワイドギャップ半導体の材料物性がそれらに対応できる。
従来の半導体材料の構成元素は、周期律表の中で第3周期以降に位置するが、第2周期の炭素や窒素といった元素を含む物質にも半導体の性質を示すものが存在する。
SiCやGaNなどがそれで、結晶の格子定数が小さくバンドギャップが大きいという特徴を持つ。ただ、原子間の結合が強いので、融点が高く合成するのが難しいというのが材料面からの課題であった。バルク成長も薄膜成長も難しい。
近年、結晶成長法の進展で高品質な結晶が安定的に得られ、実用的な半導体デバイスが試作できるようになった。ワイドギャップ半導体パワーデバイスの技術進展の観点から眺めてみると、第1世代と定義できる耐圧1kV級において、現在までにエアコンなどの民生品で実用化が進んでいる。
第2世代と言われる5kV級の領域においては産業機器や自動車、運輸インフラを適用先とした高耐圧高信頼性デバイス、第3世代である10kV以上の領域においては電力系統インフラなどに使われる超高耐圧バイポーラデバイスの研究開発が加速している。
産総研では、SiCウエハの低コスト化につながる新規結晶成長法として溶液成長法の開発を進めているほか、大口径結晶の高効率ウエハ化一貫プロセスを目指して、切断・研削・研磨および化学的機械平坦化(CMP)の各工程の効率向上と最適化で、従来の方法に比べ加工時間を大幅に短縮できるウエハ加工技術を開発した。
高耐圧トレンチMOSFETや絶縁ゲートバイポーラトランジスタ(IGBT)といった新構造の高耐圧・超高耐圧パワーデバイスも開発している。
今後は、高効率性や小型軽量化を通した利便性向上による普及促進の面と、”何にでも使いたい”という要望に対応して耐電圧や容量の増大という適用領域拡大に向けた取り組みが開発の方向性となる。これらの要求に応えるため、オープンイノベーション拠点として、最先端技術に基づく迅速な量産化レベル開発を可能とする開発環境の整備を今後進めていく予定である。
《実用化が進むパワー半導体SiCの最新動向》
これまでパワーデバイスは、Siを材料にして作られてきたが、SiCは現用のSiに比べて、約3倍の禁制帯幅を持つなどの特性があり、電力の損失を?分の1程度に抑えられることができるほか、耐圧性にも優れている。また熱にも強く、大がかりな冷却装置も必要ないことから、機器の小型化にも貢献できる。
最近ではIoT(モノのインターネット)、インダストリー4.0が注目を集めているが、ネットにおける電力使用量の増大は無視できない。そういった中でSiCや窒化ガリウム(GaN)といったワイドギャップ半導体は省エネに有効である。
SiCはさまざまな場面で優位性が唱えられたが、高品質の結晶を成長させる技術が確立するまではパワー半導体としての注目度は低かった。
我々は「ステップ制御エピタキシー」という高品質のSiCエピタキシャル結晶を成長させる方法を1987年に見いだした。これをきっかけにSiCの優れた特性を産業界で生かせると思ったが、経済成長の時期でSiCには関心が薄かった。
材料開発だけでは相手にされないと考え、これまでの研究成果をもとに耐圧1kVを超えるショットキーバリアダイオード(SBD)を提示し、電界効果トランジスタ(MOSFET)に対する見通しを立てた。企業の参画を促すために、いくつかの国家プロジェクトにつなげていった。
国家プロジェクトの支援を基に、現在は自動車や鉄道などで電力損失低減の実績から実用化が進んでいる。基礎研究レベルであるが、電力インフラに使える超高耐圧パワーデバイスは、グリーンイノベーションの実現に寄与できるほか、国際競争力の高い新産業の創出につながると考えている。
最近は、科学技術振興機構による京都スーパークラスタプログラム事業において、SiCパワーデバイスを搭載した省エネシステムの製品化および社会実装を目指したプログラムの支援をしている。地元中小企業を中心にした産産学連携による取り組みだけでなく、長野県、福井県、滋賀県にあるサテライトクラスタとの連携も加速している。
課題として高品質バルク成長と低価格化があるが、個人的にはSiCでしかできない応用の発掘、さらには使い方を考える若手の育成などに取り組む必要があると考えている。
奥村元氏(産業技術総合 研究所先進パワーエレクトロニクス研究センター 研究センター長)
《パワーエレクトロニクス革新の意義―国内の現状と産総研の取り組み》
パワエレの守備範囲は広範にわたるが、では”マイクロエレクトロニクス”と”パワーエレクトロニクス”とどう違うのか。前者は主に「情報、信号」を扱うのに対して、後者は「エネルギー」を扱うという点で半導体デバイス構造も大きく変わってくる。
パワエレの場合、デバイス性能として高耐圧、低オン抵抗、大電流動作などの性能が求められるわけだが、SiCやGaNといったワイドギャップ半導体の材料物性がそれらに対応できる。
従来の半導体材料の構成元素は、周期律表の中で第3周期以降に位置するが、第2周期の炭素や窒素といった元素を含む物質にも半導体の性質を示すものが存在する。
SiCやGaNなどがそれで、結晶の格子定数が小さくバンドギャップが大きいという特徴を持つ。ただ、原子間の結合が強いので、融点が高く合成するのが難しいというのが材料面からの課題であった。バルク成長も薄膜成長も難しい。
近年、結晶成長法の進展で高品質な結晶が安定的に得られ、実用的な半導体デバイスが試作できるようになった。ワイドギャップ半導体パワーデバイスの技術進展の観点から眺めてみると、第1世代と定義できる耐圧1kV級において、現在までにエアコンなどの民生品で実用化が進んでいる。
第2世代と言われる5kV級の領域においては産業機器や自動車、運輸インフラを適用先とした高耐圧高信頼性デバイス、第3世代である10kV以上の領域においては電力系統インフラなどに使われる超高耐圧バイポーラデバイスの研究開発が加速している。
産総研では、SiCウエハの低コスト化につながる新規結晶成長法として溶液成長法の開発を進めているほか、大口径結晶の高効率ウエハ化一貫プロセスを目指して、切断・研削・研磨および化学的機械平坦化(CMP)の各工程の効率向上と最適化で、従来の方法に比べ加工時間を大幅に短縮できるウエハ加工技術を開発した。
高耐圧トレンチMOSFETや絶縁ゲートバイポーラトランジスタ(IGBT)といった新構造の高耐圧・超高耐圧パワーデバイスも開発している。
今後は、高効率性や小型軽量化を通した利便性向上による普及促進の面と、”何にでも使いたい”という要望に対応して耐電圧や容量の増大という適用領域拡大に向けた取り組みが開発の方向性となる。これらの要求に応えるため、オープンイノベーション拠点として、最先端技術に基づく迅速な量産化レベル開発を可能とする開発環境の整備を今後進めていく予定である。
日刊工業新聞2016年3月11日付
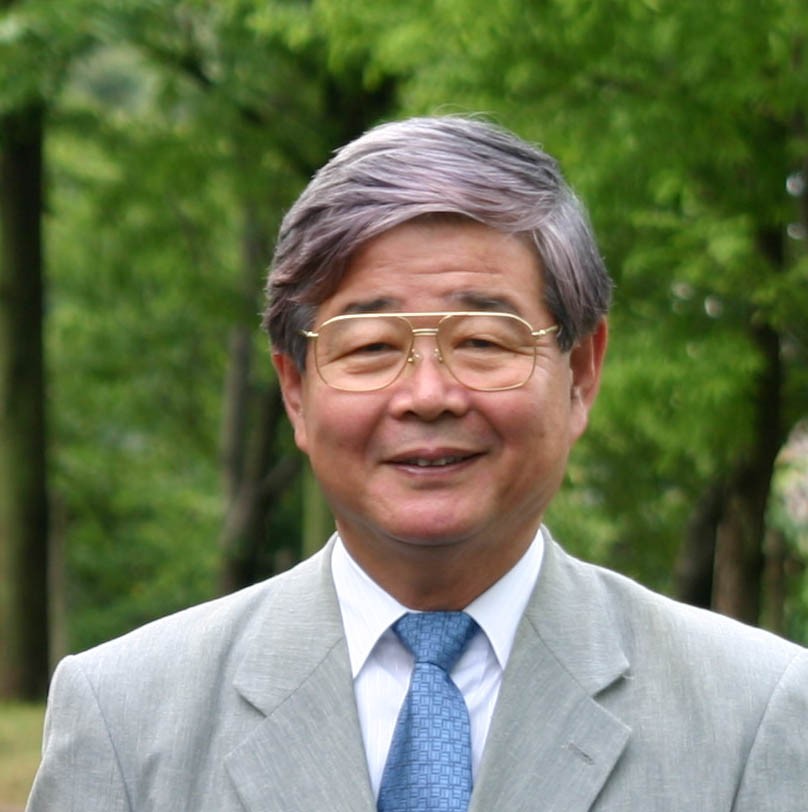