「無人搬送車」が自律走行。日立が実用化へ
倉庫など壁は「動かない領域」、商品棚は「動く領域」に分けて管理
日立製作所は4日、物流倉庫などで商品を棚ごと搬送する「無人搬送車」を自律的に走行させる技術を開発したと発表した。センサーの情報をもとに自ら登録された商品棚などの配置図をリアルタイムに更新し、車の位置を認識。床面マーカーなどの走行ガイドを使わずに走行する。日立が販売する小型・低床式無人搬送車に同技術を適用し、実用化を目指す。
無人搬送車へ事前に登録する配置図を、倉庫の壁や柱などの「動かない領域」と、商品棚などの「動く領域」に分けて管理する。この配置図と、距離センサーで計測した柱や商品棚の位置情報を照合し、車の位置を認識する。その後、動く領域にある商品棚の配置だけを更新する仕組み。
これにより配置図を更新する時間を短縮し、その精度も向上。マーカーが不要になったことで敷設・保守コストが減り、走行経路や設備レイアウトの設計自由度も高まった。
一般的な無人搬送車の利用環境である70メートル四方の建屋内で、1メートル四方の商品棚が搬送によって入れ替わる状況をコンピューター上で模擬した。その結果、平均誤差10ミリメートルで車の位置を認識できた。
9月に東京電機大学で開かれる「第33回日本ロボット学会学術講演会」で発表する。
日立製作所は部品や商品が保管された棚を自動で集めて回るピッキング用無人搬送車を開発した。棚そのものを持ち上げ、ピッキングの作業スペースに搬送する。作業者は工場や倉庫を歩き回らずに収集でき、一般的な人力での手法に比べてピッキング効率は3倍強になるという。導入コストは、品物を自動で出し入れする自動倉庫に比べて約3割抑制できる。9月1日に販売を開始し、2015年度に30億円の売り上げを目指す。
開発した無人搬送車は「Racrew(ラックル)」。搬送車と制御システム、ラックル専用の部品・商品棚、充電装置で構成する。価格は個別見積もりだが、搬送車10台規模のシステムで1億―1億5000万円程度を想定する。
大きさは幅900ミリ×長さ960ミリ×高さ380ミリメートルで、小型・低床式を実現した。指示に従って部品・商品棚に向かい、棚の下に潜り込んで持ち上げ、指定位置まで搬送する。作業者が部品や商品を探し回る必要がなく、省人化を図れる。部材や半製品を生産工程に運ぶ搬送車はあるが、棚そのものを運び出してピッキングを支援する搬送車は珍しい。
導入時に搬送能力が決まる自動倉庫に比べて拡張性が高い。工場の立ち上げ時は小規模で対応し、フル操業時に増車することが可能だ。少量多品種生産や工場のレイアウト変更にも対応する。実際の運用データを分析し、利用頻度の高い棚を運びやすい位置に配置したり、渋滞の少ないルートを選ぶなど、搬送効率を高める機能を有する。
積載荷重は最大500キログラム。負荷のない時は最大で毎時80メートルで走行する。工場内の部品組み立てラインや医薬品・食品の製造ライン、倉庫・配送センターでの利用を見込む。15年1月から中国や東南アジアなど海外でも販売を始める。「人件費が上昇する中国では需要がある」(インフラシステム社)としている。14年度は10億円の売り上げを見込む。
無人搬送車へ事前に登録する配置図を、倉庫の壁や柱などの「動かない領域」と、商品棚などの「動く領域」に分けて管理する。この配置図と、距離センサーで計測した柱や商品棚の位置情報を照合し、車の位置を認識する。その後、動く領域にある商品棚の配置だけを更新する仕組み。
これにより配置図を更新する時間を短縮し、その精度も向上。マーカーが不要になったことで敷設・保守コストが減り、走行経路や設備レイアウトの設計自由度も高まった。
一般的な無人搬送車の利用環境である70メートル四方の建屋内で、1メートル四方の商品棚が搬送によって入れ替わる状況をコンピューター上で模擬した。その結果、平均誤差10ミリメートルで車の位置を認識できた。
9月に東京電機大学で開かれる「第33回日本ロボット学会学術講演会」で発表する。
昨年発売された「ラックル」-15年度に売上高目標が30億円だったが
2014年8月29日付
日立製作所は部品や商品が保管された棚を自動で集めて回るピッキング用無人搬送車を開発した。棚そのものを持ち上げ、ピッキングの作業スペースに搬送する。作業者は工場や倉庫を歩き回らずに収集でき、一般的な人力での手法に比べてピッキング効率は3倍強になるという。導入コストは、品物を自動で出し入れする自動倉庫に比べて約3割抑制できる。9月1日に販売を開始し、2015年度に30億円の売り上げを目指す。
開発した無人搬送車は「Racrew(ラックル)」。搬送車と制御システム、ラックル専用の部品・商品棚、充電装置で構成する。価格は個別見積もりだが、搬送車10台規模のシステムで1億―1億5000万円程度を想定する。
大きさは幅900ミリ×長さ960ミリ×高さ380ミリメートルで、小型・低床式を実現した。指示に従って部品・商品棚に向かい、棚の下に潜り込んで持ち上げ、指定位置まで搬送する。作業者が部品や商品を探し回る必要がなく、省人化を図れる。部材や半製品を生産工程に運ぶ搬送車はあるが、棚そのものを運び出してピッキングを支援する搬送車は珍しい。
導入時に搬送能力が決まる自動倉庫に比べて拡張性が高い。工場の立ち上げ時は小規模で対応し、フル操業時に増車することが可能だ。少量多品種生産や工場のレイアウト変更にも対応する。実際の運用データを分析し、利用頻度の高い棚を運びやすい位置に配置したり、渋滞の少ないルートを選ぶなど、搬送効率を高める機能を有する。
積載荷重は最大500キログラム。負荷のない時は最大で毎時80メートルで走行する。工場内の部品組み立てラインや医薬品・食品の製造ライン、倉庫・配送センターでの利用を見込む。15年1月から中国や東南アジアなど海外でも販売を始める。「人件費が上昇する中国では需要がある」(インフラシステム社)としている。14年度は10億円の売り上げを見込む。
日刊工業新聞2015年08月05日 科学技術・大学面
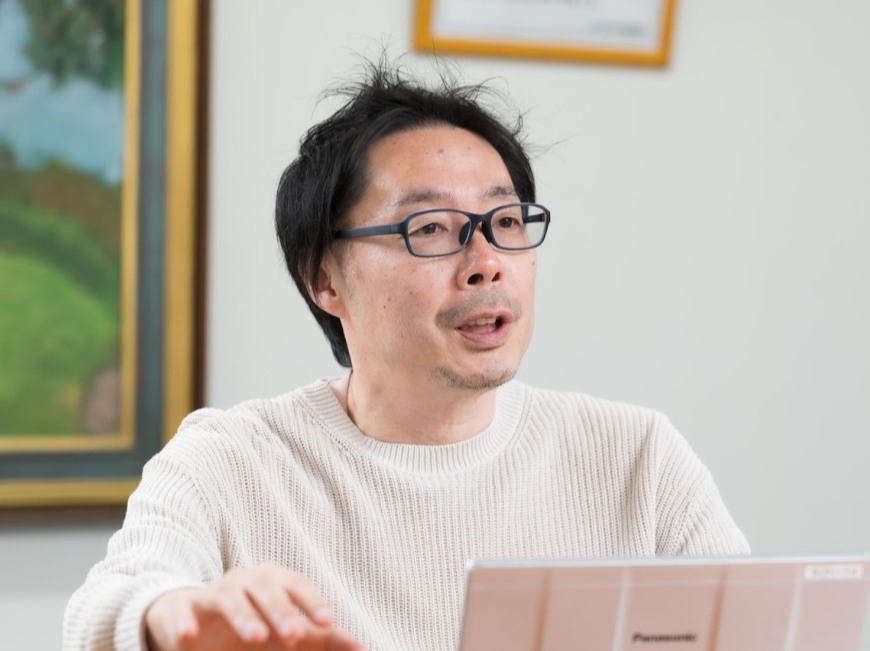