オムロンの製造現場からIoT導入のヒントを得る
草津事業所、最適な加工条件に自動制御する仕組み
**金型加工の情報分析で加工精度を高度化
オムロン草津事業所(滋賀県草津市)は、4,000種を手がける超多品種少量生産の現場で、1日の段取り替えは500回にものぼる。そのうち90%以上が20台以下という。製品の多品種少量化に伴い、コストダウンは避けて通れなくなっている。そこで草津事業所ではIoTを活用した、金型加工の生産性向上の実証実験を行った。
その結果、金型加工速度を従来比で40%も向上させ、工具の摩耗量を従来比で20%低減させた。17年9月からは同社の製品であるリレーやスイッチ用のプレス金型や樹脂成形金型の作製に活用している。
金型製造コストを下げるには加工時間の短縮が必須で、工具の折損による加工停止時間などは最小に抑えなければならない。工具は折損させず、加工速度は向上させるという難易度の高い取組みになる。
今回の取組みでは、金型作製に使用している3軸のマシニングセンタ(MC)を使い金型加工時のデータ収集、見える化・分析し、制御フィードバックした。結果として、熟練工の判断を超える最適な加工条件に自動制御する仕組みを構築している。
データ取得のため、MCのチャックに振動センサを取り付けた。エンドミルで金型材料を加工する際に発生する振動を捉え、振動から微細な加工抵抗を数値化する。振動センサで捉えたデータは同社製のプログラマブルロジックコントローラ(PLC)「NJ」に送られ、最適な送り速度に調整される。
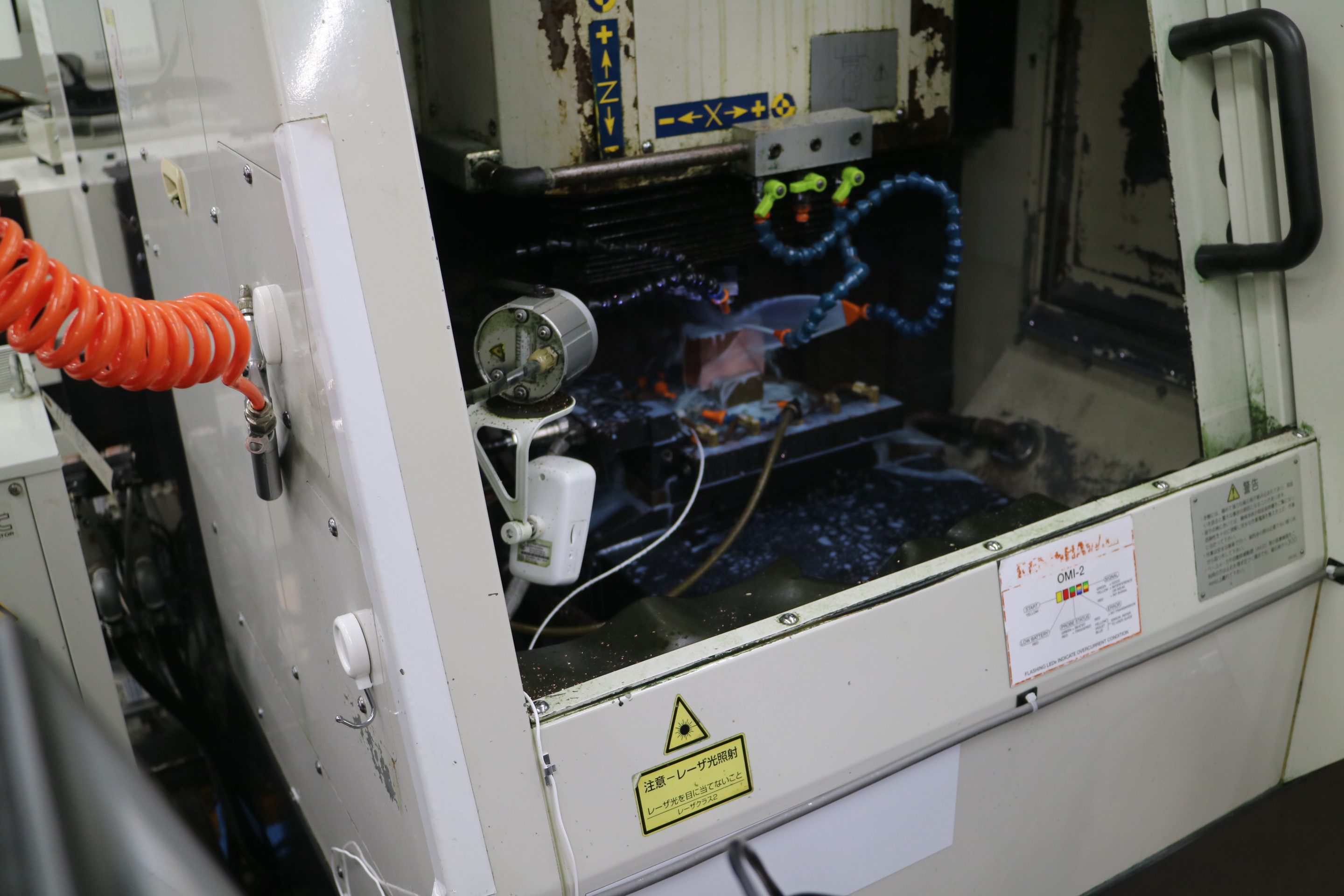
MCによる金型加工
振動が大きいと工具にかかる加工抵抗値は大きくなる。ワークを加工する際に、設定した加工抵抗の閾値を上回っている場合は、工具にかかる加工抵抗値を下げるため、工具の送り速度を落とす。加工抵抗が高いままだと工具の摩耗が早くなるほか、工具の折損につながる。ワークの材料にも余計な力がかかっており、いいことはない。加工抵抗値が閾値より、低い場合には工具の送り速度を上げる。これは加工速度が遅く、加工時間が長くなるためだ。
振動センサからは3秒に1回データが送信され、MCはPLCのNJから10秒に1回フィードバックし、最適な送り速度を保つ仕組みだ。従来、工具の送り速度は熟練工が判断し高めていたが、工具メーカー推奨値の1.3倍止まりだったという。オムロンのグローバルものづくり革新本部の山崎雄司主査は「データ取得後は送り速度を3〜5倍まで高められた」という。送り速度を制御することで、金型加工時間を従来比で40%も短縮でき、工具摩耗量も20%削減できた。
データ取得前は、熟練工の判断で早めた工具の送り速度でも、まだ加工速度を高められる余地があったわけで、データ取得、分析により最適な加工を行えるアルゴリズムを構築し、加工時間を短縮できたことになる。
今回のリレーやスイッチ用の金型加工に使用している、エンドミルは径が0.2〜6mmと細い。工具が加工中に折れてしまうと工具費用、工具交換時間、金型加工が中断するロスが発生するが、送り速度を調整することで、こうした突発的な事態も防げる。
もっとも、最初から振動センサを取り付けて活用したわけではない。当初は、MCの主軸モータの電流値から振動を捉えようとしたが、あまりに小さくノイズに埋もれてしまったという。今後は振動以外にも、放射温度計を用い工具寿命に関わる工具の温度データの取得なども検討する。
今回開発した金型加工で最適な加工条件に自動制御する仕組みは、機械が変わっても使える。次は1チャックで、さまざまな角度から加工ができる5軸MCでの実証を進める。ただし、機械が変わると、それぞれ最適な加工条件を出す実験は必要になる。山崎主査は「材料の材質や工具の直径が変わった場合、新たに閾値を設けるときに、今は人が実験している。今後はAIで推論して条件を出せれば」と話す。
オムロンの綾部事業所(京都府綾部市)では、近接スイッチモジュールの組立工程がある。近接スイッチは、非接触で近傍の物体の有無を検出するセンサだ。使用している組立装置は15年以上稼働しているが、国内の製造業では、同様に老朽化した設備を使っている工場も多く典型的な例だという。ここでは、ロボットを使い製品の組立を行っているが、不定期に発生するチョコ停の予兆を把握する仕組みを構築し生産性向上に取り組んでいる。
たとえば、ロボットを使い部品を上から下の部品に挿入し組み合わせる工程では、作業を行っている間にロボットにずれが発生し組付に失敗し、チョコ停が発生する。
調べていくと、ロボットの先端部分のずれが0.4mm以上になると、設備トラブルとなってしまう。人間の目では正常だが、ハイスピードカメラで捉えると、軸がわずかにずれていることがわかる(図1)。そこで、ずれの予兆を捉えるために、レーザー変位センサを用いて、3つの生産ラインでロボットの先端位置を測定している。
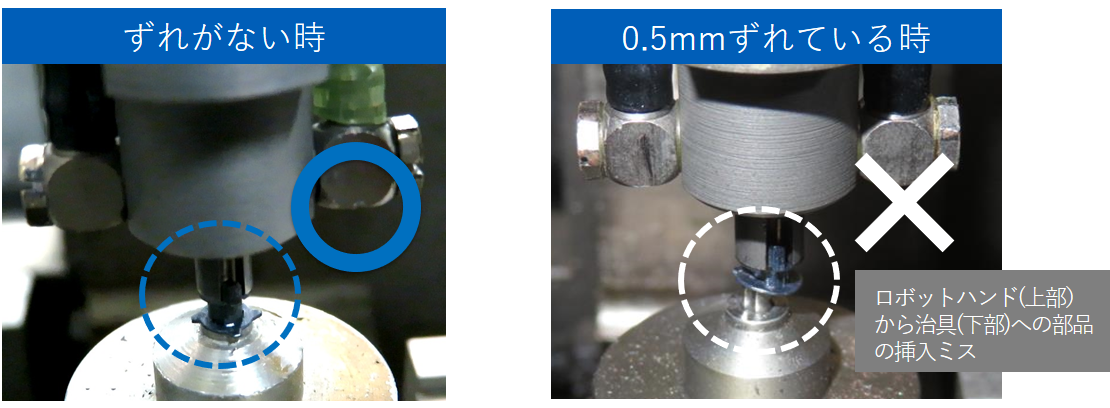
図1
ロボットの先端位置の2ミリ秒ごとの波形データを収集し、任意に設定できるサイクルで、波形の中からずれたときに出る数値である特徴量をトレンドグラフとして表示する。ロボットの先端位置がずれて設定した閾値を超えると、生産ラインの状態を一覧できるオーバービューの画面上で「正常」から「予報」「警報」へと切り替わる仕組みだ(図2)。
たとえば予報の段階では、すぐに対応しなければならないレベルではないが、チョコ停が発生する前に、段取り替えのときに、ずれを調整するなど事前の準備ができる。突発的なトラブルで設備が止まってしまうと、すぐに対応しなければならないが、作業者の心理的な負担も減り、生産性の向上にもつながる。
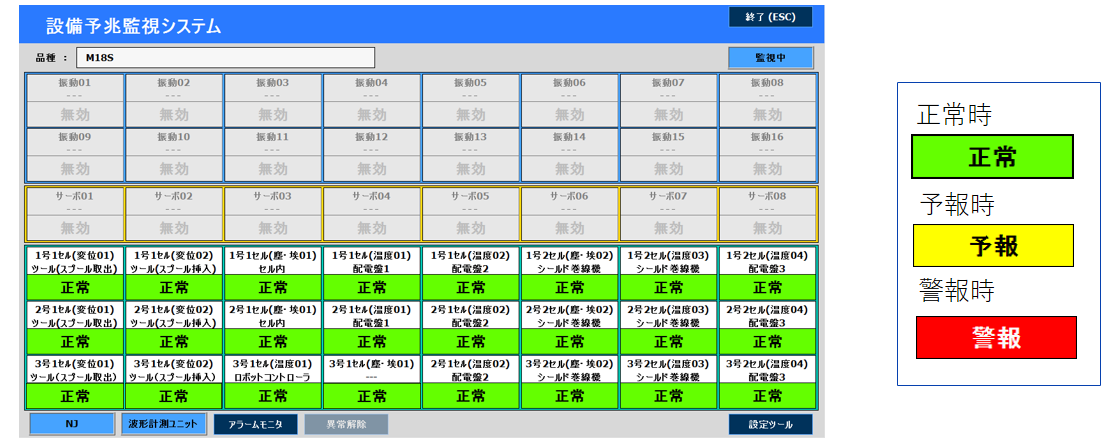
図2
予兆保全システムの実証実験はオフラインで17年4月から始め、9月からは実際の生産ラインで活用を始めた。チョコ停の低減の効果はまとまっていないが、1ライン当たりチョコ停は月4.5時間の低減、チョコ停に伴い発生する部品ロスが月1万3,000円低減すると見込んでいる。
従来の保全は、定期保全の考え方だが、予兆保全はムダな交換をやめて、設備をムダなく使いたいという考え方だ。大切なことは、予兆保全システムを使い最適な管理基準を決めるための知見を現場で蓄積していくことだ。
オムロンの製造現場においてIoT導入、得られたビッグデータをどのように活用していくのか、AIをデータ解析に役立てるのかという取組みは、まだ始まったばかり。草津事業所には年間2,000人以上の見学者が訪れるが、「身の丈にあったIoTは、どこから始めたら良いのか」という経営者や担当者が多いのも実情だ。
金型加工、ロボットを使った組立などオムロンの製造現場で行った生産性向上や設備の変化を捉える設備の予兆監視の取組みは、非常にベーシックだ。製造現場にIoTをどう活用すればいいのかと考える企業にとっては、導入費用、効果検討する上で示唆に富む実例になりそうだ。
オムロン草津事業所(滋賀県草津市)は、4,000種を手がける超多品種少量生産の現場で、1日の段取り替えは500回にものぼる。そのうち90%以上が20台以下という。製品の多品種少量化に伴い、コストダウンは避けて通れなくなっている。そこで草津事業所ではIoTを活用した、金型加工の生産性向上の実証実験を行った。
その結果、金型加工速度を従来比で40%も向上させ、工具の摩耗量を従来比で20%低減させた。17年9月からは同社の製品であるリレーやスイッチ用のプレス金型や樹脂成形金型の作製に活用している。
金型製造コストを下げるには加工時間の短縮が必須で、工具の折損による加工停止時間などは最小に抑えなければならない。工具は折損させず、加工速度は向上させるという難易度の高い取組みになる。
今回の取組みでは、金型作製に使用している3軸のマシニングセンタ(MC)を使い金型加工時のデータ収集、見える化・分析し、制御フィードバックした。結果として、熟練工の判断を超える最適な加工条件に自動制御する仕組みを構築している。
データ取得のため、MCのチャックに振動センサを取り付けた。エンドミルで金型材料を加工する際に発生する振動を捉え、振動から微細な加工抵抗を数値化する。振動センサで捉えたデータは同社製のプログラマブルロジックコントローラ(PLC)「NJ」に送られ、最適な送り速度に調整される。
振動が大きいと工具にかかる加工抵抗値は大きくなる。ワークを加工する際に、設定した加工抵抗の閾値を上回っている場合は、工具にかかる加工抵抗値を下げるため、工具の送り速度を落とす。加工抵抗が高いままだと工具の摩耗が早くなるほか、工具の折損につながる。ワークの材料にも余計な力がかかっており、いいことはない。加工抵抗値が閾値より、低い場合には工具の送り速度を上げる。これは加工速度が遅く、加工時間が長くなるためだ。
振動センサからは3秒に1回データが送信され、MCはPLCのNJから10秒に1回フィードバックし、最適な送り速度を保つ仕組みだ。従来、工具の送り速度は熟練工が判断し高めていたが、工具メーカー推奨値の1.3倍止まりだったという。オムロンのグローバルものづくり革新本部の山崎雄司主査は「データ取得後は送り速度を3〜5倍まで高められた」という。送り速度を制御することで、金型加工時間を従来比で40%も短縮でき、工具摩耗量も20%削減できた。
データ取得前は、熟練工の判断で早めた工具の送り速度でも、まだ加工速度を高められる余地があったわけで、データ取得、分析により最適な加工を行えるアルゴリズムを構築し、加工時間を短縮できたことになる。
今回のリレーやスイッチ用の金型加工に使用している、エンドミルは径が0.2〜6mmと細い。工具が加工中に折れてしまうと工具費用、工具交換時間、金型加工が中断するロスが発生するが、送り速度を調整することで、こうした突発的な事態も防げる。
もっとも、最初から振動センサを取り付けて活用したわけではない。当初は、MCの主軸モータの電流値から振動を捉えようとしたが、あまりに小さくノイズに埋もれてしまったという。今後は振動以外にも、放射温度計を用い工具寿命に関わる工具の温度データの取得なども検討する。
今回開発した金型加工で最適な加工条件に自動制御する仕組みは、機械が変わっても使える。次は1チャックで、さまざまな角度から加工ができる5軸MCでの実証を進める。ただし、機械が変わると、それぞれ最適な加工条件を出す実験は必要になる。山崎主査は「材料の材質や工具の直径が変わった場合、新たに閾値を設けるときに、今は人が実験している。今後はAIで推論して条件を出せれば」と話す。
ロボットの予兆管理でチョコ停防止
オムロンの綾部事業所(京都府綾部市)では、近接スイッチモジュールの組立工程がある。近接スイッチは、非接触で近傍の物体の有無を検出するセンサだ。使用している組立装置は15年以上稼働しているが、国内の製造業では、同様に老朽化した設備を使っている工場も多く典型的な例だという。ここでは、ロボットを使い製品の組立を行っているが、不定期に発生するチョコ停の予兆を把握する仕組みを構築し生産性向上に取り組んでいる。
たとえば、ロボットを使い部品を上から下の部品に挿入し組み合わせる工程では、作業を行っている間にロボットにずれが発生し組付に失敗し、チョコ停が発生する。
調べていくと、ロボットの先端部分のずれが0.4mm以上になると、設備トラブルとなってしまう。人間の目では正常だが、ハイスピードカメラで捉えると、軸がわずかにずれていることがわかる(図1)。そこで、ずれの予兆を捉えるために、レーザー変位センサを用いて、3つの生産ラインでロボットの先端位置を測定している。
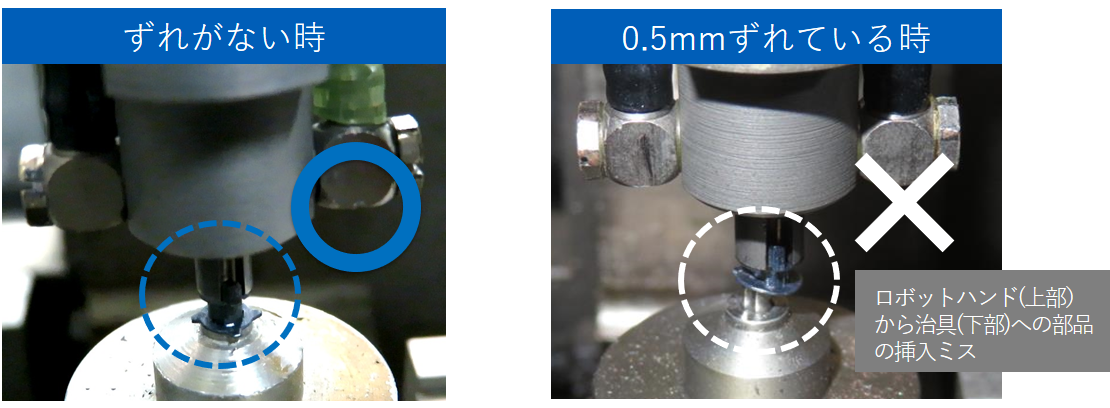
ロボットの先端位置の2ミリ秒ごとの波形データを収集し、任意に設定できるサイクルで、波形の中からずれたときに出る数値である特徴量をトレンドグラフとして表示する。ロボットの先端位置がずれて設定した閾値を超えると、生産ラインの状態を一覧できるオーバービューの画面上で「正常」から「予報」「警報」へと切り替わる仕組みだ(図2)。
たとえば予報の段階では、すぐに対応しなければならないレベルではないが、チョコ停が発生する前に、段取り替えのときに、ずれを調整するなど事前の準備ができる。突発的なトラブルで設備が止まってしまうと、すぐに対応しなければならないが、作業者の心理的な負担も減り、生産性の向上にもつながる。
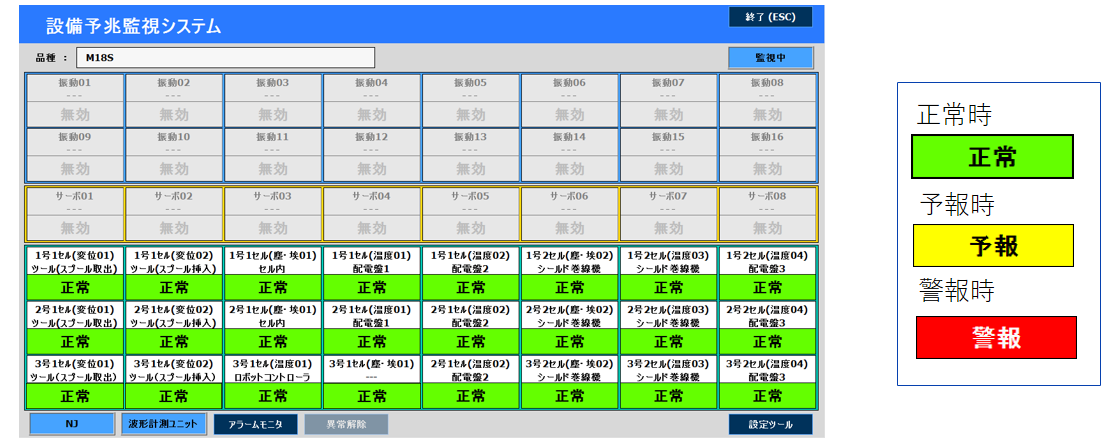
予兆保全システムの実証実験はオフラインで17年4月から始め、9月からは実際の生産ラインで活用を始めた。チョコ停の低減の効果はまとまっていないが、1ライン当たりチョコ停は月4.5時間の低減、チョコ停に伴い発生する部品ロスが月1万3,000円低減すると見込んでいる。
従来の保全は、定期保全の考え方だが、予兆保全はムダな交換をやめて、設備をムダなく使いたいという考え方だ。大切なことは、予兆保全システムを使い最適な管理基準を決めるための知見を現場で蓄積していくことだ。
IoT活用のヒント
オムロンの製造現場においてIoT導入、得られたビッグデータをどのように活用していくのか、AIをデータ解析に役立てるのかという取組みは、まだ始まったばかり。草津事業所には年間2,000人以上の見学者が訪れるが、「身の丈にあったIoTは、どこから始めたら良いのか」という経営者や担当者が多いのも実情だ。
金型加工、ロボットを使った組立などオムロンの製造現場で行った生産性向上や設備の変化を捉える設備の予兆監視の取組みは、非常にベーシックだ。製造現場にIoTをどう活用すればいいのかと考える企業にとっては、導入費用、効果検討する上で示唆に富む実例になりそうだ。
「工場管理」2018年1月号