「全固体電池」実用化方針にサプライズ、トヨタの電池戦略はEV時代に競争優位を保つか
欧米の自動車メーカーを中心に世界中で車載電池への投資が過熱する中、トヨタ自動車が満を持して自社戦略を公表した。20年以上にわたる電池の内製で培ってきた生産・開発ノウハウと、車両タイプに合わせた全方位の電池ラインアップが、主なポイントだ。投資単位の圧縮や地道な技術改善など、地に足のついた“トヨタらしい”やり方で、今後本格的に到来する電気自動車(EV)時代の競争力を確保する構えだ。(名古屋・政年佐貴恵)
車両と電池、一体開発
「車両と電池の両輪がトヨタの強みだ」―。9月7日に開いた電池戦略の説明会で、技術開発を統括する前田昌彦執行役員は強調した。EVにとって電池は車両性能を左右する重要部品だが、現状では複数の課題を抱える。航続距離や充電時間、EV車両の3―4割を占め高価格の要因となっているコスト、安全性の確保などだ。これらの性能は車両の使用年数や走行履歴などで変わると同時に、技術的には背反する要素が多い。トヨタは1997年に発売したハイブリッド車(HV)の初代「プリウス」以降、電池を内製してきた。前田執行役員は「内製ノウハウやデータを生かして車両と電池を一体開発すれば、これらの性能を高次元でバランスできる」と、優位性を訴える。
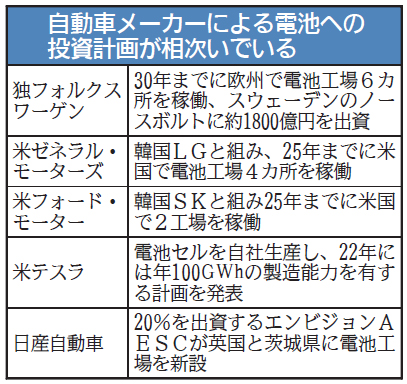
低コスト・高性能・長寿命化へ
トヨタの電池戦略の軸は、技術革新や生産単位の最小化による低コストな電池の実現と、電池における“全方位戦略”だ。コスト面では1キロメートル走行するのに必要な電力である電費を、2022年半ば頃に投入予定のEV「bZ4X」に比べさらに30%改善することで電池容量を削減し、30%のコスト低減を目指す。同時にニッケルやコバルトといった高コスト材料の使用を減らすほか、車両一体構造の電池開発などで、電池単体のコストも30%以上低減させる計画だ。これらを合わせて、20年代後半までにEV1台当たりのコスト半減を目指す。
また30年までに計70本程度の生産ラインを立ち上げ、容量で現状比約33倍の200ギガワット時以上の供給量を目指す製造面では、1ライン当たりの生産量や作業人員の数を抑制。ライン立ち上げまでのリードタイムも短くすることで投資単位を引き下げる。生産を統括する岡田政道執行役員は「必要な投資を小刻みにするのが我々の特徴で持ち味だ」と説明する。市場ニーズに細かく対応できるようにして、量の変動があっても競争力を確保できるラインにする。投資単位の小さなラインを実現すべく、他社との連携も視野に設備開発から手がけていく。「これまでガソリンエンジンでも小さなラインの思想でやってきた。これを(次世代駆動部品の)電池でも引き継ぐ」(トヨタ幹部)。
「車両別」で全方位戦略
車両タイプに合わせた電池ラインアップも拡充する。既存の液系リチウムイオン電池やバイポーラ型ニッケル水素電池、開発中の全固体電池に加え、20年代後半には新構造の液系リチウムイオン電池の実用化を目指す。さらに低コストが見込めるリン酸鉄リチウムイオンバッテリーも視野に入れる。「使用条件など実際の利便性を見て使う電池を見極める」(前田執行役員)考えだ。こうした全方位戦略について、野村証券の桾本将隆アナリストは「次世代電池も複数開発し、今後の進展に機動的に対応できる」と評価する。
投資では30年までに生産に約1兆円、研究開発で約5000億円の、計1兆5000億円を投じると表明した。兆円単位の投資規模だが、東海東京調査センターの杉浦誠司シニアアナリストは「毎年1500億円のペースで、決して大きくはない」と指摘。「欧州メーカーはEV投資も含めて大風呂敷を広げているが、トヨタは真面目にやっている印象だ」と述べる。
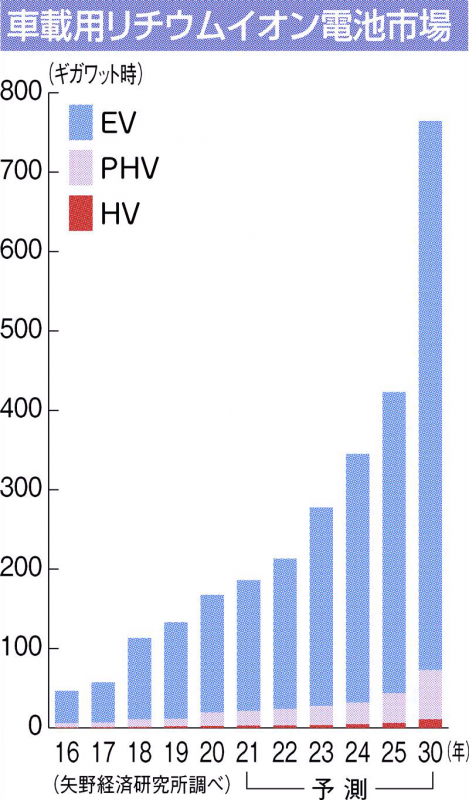
トヨタは電池製造でパナソニックと共同出資する子会社や、豊田自動織機といったグループ企業を活用するほか、中国・寧徳時代新能源科技(CATL)などの提携先では設備投資を負担し、トヨタ向けの専用ラインを構えることも想定する。一方、一部では「トヨタグループ内で電池技術が分散し、それぞれの役割が見えない」(車関連メーカー首脳)との声も挙がる。トヨタ幹部は「今はそれぞれで競争力を高める段階」とするが、経営リスクの大きい電池事業をより効率よく運営するには、将来の事業再編も選択肢に入れる必要がありそうだ。
全固体電池は「HVから」
トヨタの電池戦略でサプライズの一つとして受け止められたのが、全固体電池の実用化方針だ。全固体は発火リスク低減や小型・高容量などを実現しEV向けの次世代電池として注目が高まっているが、トヨタは最初にHVで実用化を目指す考えを示した。東海東京調査センターの杉浦シニアアナリストは「投資家は全固体による(EV市場の)ゲームチェンジを期待していた」と明かす。
20年8月に実車搭載して走行試験を実施したが、足元では劣化を抑える材料開発など、技術課題の解決に時間がかかるという。前田執行役員は「現状では寿命が短い課題があるが、全固体は高出力化が期待できる。HVが一番特徴を生かせるのではないか」と説明する。
トヨタは当初掲げていた20年代前半の実用化目標は据え置いた。HVへの導入により、早期の実用化に重きを置いた格好だ。グローバルで全固体の開発競争は激化している。実用化で先行して走行性能などのメリットを打ち出し、優位性を築くことを狙う。
調達力=生産・販売力
グローバルでも自動車各社が車載電池の投資を強化する方針を相次ぎ打ち出している。独フォルクスワーゲン(VW)は30年までに欧州で6工場を稼働させると発表したほか、出資するスウェーデンのノースボルトでは23年にVW向けの生産を始める計画だ。生産能力を容量ベースで年40ギガワット時まで段階的に引き上げる。米ゼネラル・モーターズ(GM)は韓国LG化学との合弁工場で25年までに4工場を立ち上げる。EVと自動運転で、25年までに350億ドル(約4兆円)を投じる構えだ。米フォード・モーターも韓国SKイノベーションと組み、25年までに計約1兆円を投じる。
投資合戦が相次ぐ理由は、電池の調達力がEVの生産・販売力に直結するからだ。「とてつもない量が必要になるので、各社には確保しなければならない危機感がある」(トヨタ幹部)。一般的には電池生産量が増えることで電池価格の低下が期待される。一方、投資の過熱はリチウムやニッケルといった資源の獲得競争に陥り価格が下がらず、EV普及速度が鈍化し大規模な初期投資を回収ができないリスクもはらむ。
矢野経済研究所は政策や自動車各社の電動化目標を基にした高成長モデルの電池市場予測を出しており、その場合、30年の市場規模は容量ベースで1809・2ギガワット時になると試算する。しかし「ガソリンエンジン車よりも利幅が少ないプラグインハイブリッド車(PHV)、EVの展開が想定よりも困難となれば、当初の見込みほどには至らない」と指摘する。
オンラインセミナーのご案内
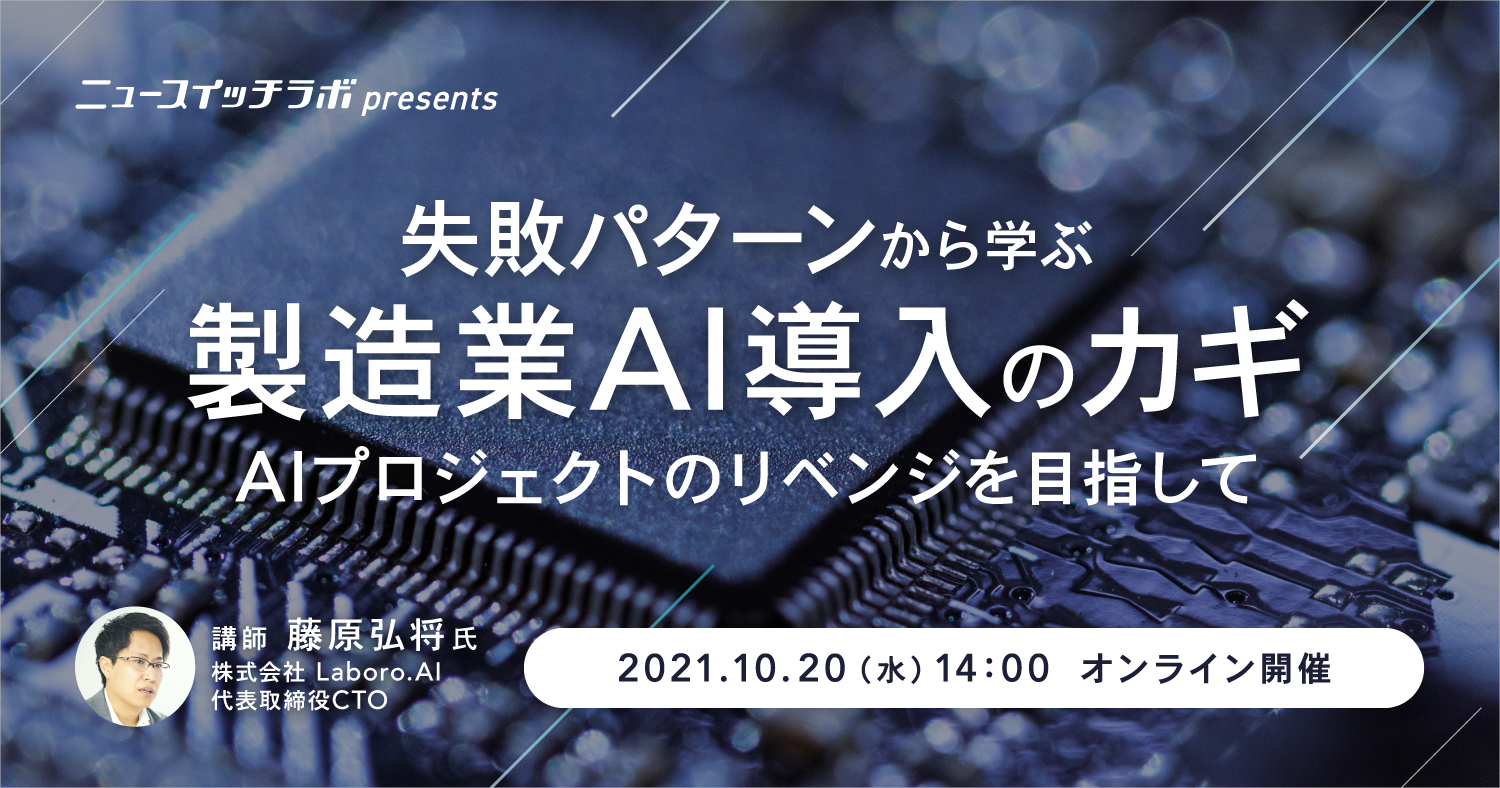
ニュースイッチでは、オンラインイベント「失敗パターンから学ぶ 製造業AI導入のカギ 〜AIプロジェクトのリベンジを目指して〜」を開催します。
本セミナーでは、特集「AIは幻想かー導入現場のリアル」の執筆を手がけた、AI開発スタートアップLaboro.AIの代表取締役CTO 藤原弘将氏が、製造業の代表的なAI導入ケースである異常検出、需要予測、故障予知、安全管理、工程スケジューリングをテーマに取り上げ、それぞれのアンチパターンを紹介し、AI導入プロジェクトを成功に導くためのヒントを提供します。
2021/10/20(水) 14:00 ~ 15:30
<<申し込みはこちらから>>
参加料:¥7,700(税込)
申し込み締切 2021年10月19日(火)12:00
【連載】AIは幻想か―導入現場のリアル