東海道新幹線の新型車両「N700S」を初公開
JR東海は1日、2020年度に運行開始する東海道新幹線の新型車両「N700S」を愛知県豊川市で初公開した。先頭車両と客室の座席・内装を公開し、先頭形状の改善で環境性能が向上したことや客室の快適さを説明した。18年3月に確認試験車を完成させ、営業運転に向けた走行試験を実施する。
N700Sを製造する子会社、日本車両製造の豊川製作所で公開した。古屋政嗣JR東海新幹線鉄道事業本部車両部担当部長は「現時点で盛り込める技術を盛り込んだ」と自信を示した。
先頭車両は左右両サイドにエッジを立てた形状により、走行時の風の流れを整え、騒音や抵抗を低減できる。塗装前の状態で公開し、今後は確認試験車として使用する。
客室はグリーン車と普通車の座席・内装を配置したモックアップを公開。座席は現行車両「N700A」よりも沈み込みやすくしたほか、荷棚の照明が停車駅に近づくと明るくなり、荷物の置き忘れを防ぐ。
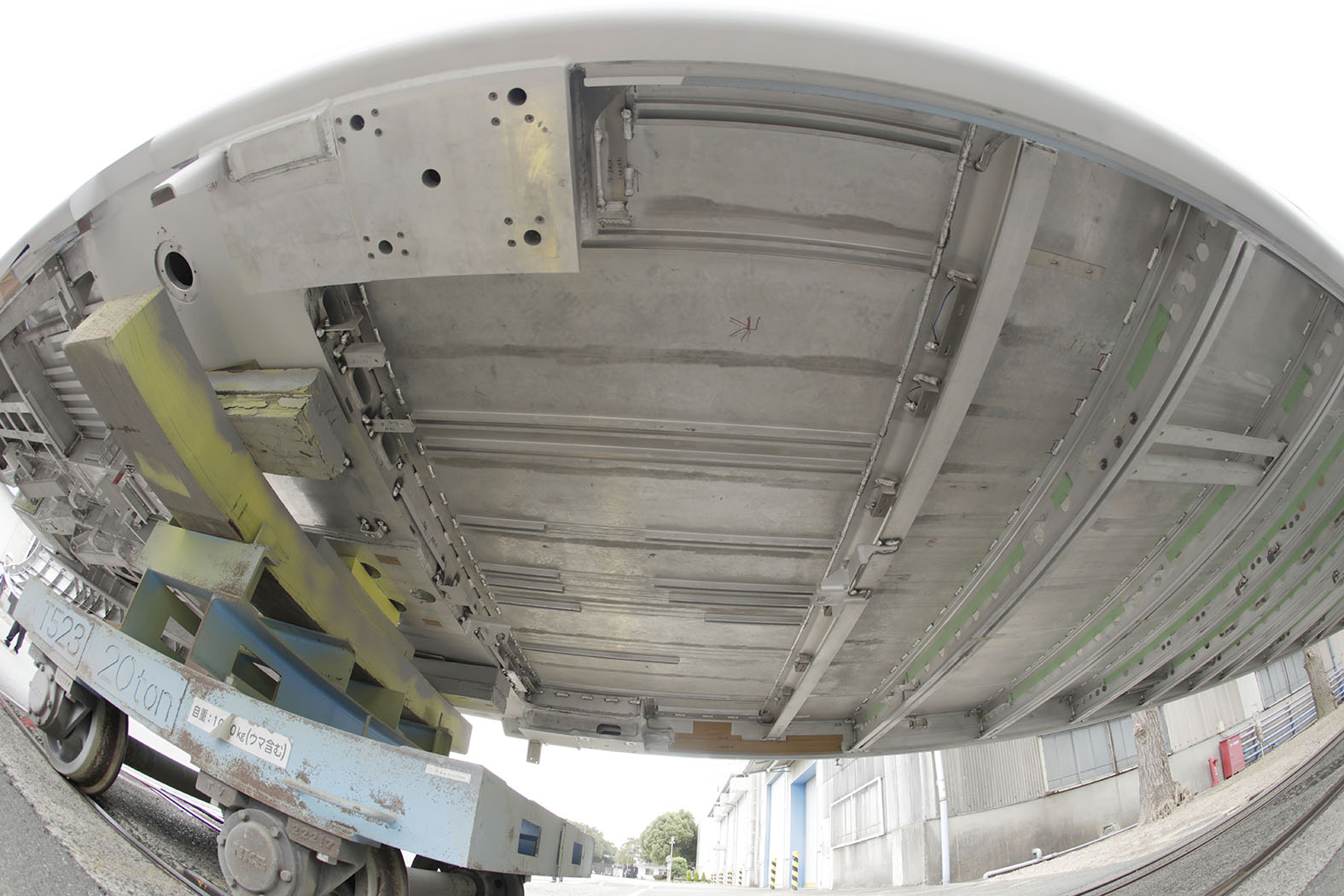
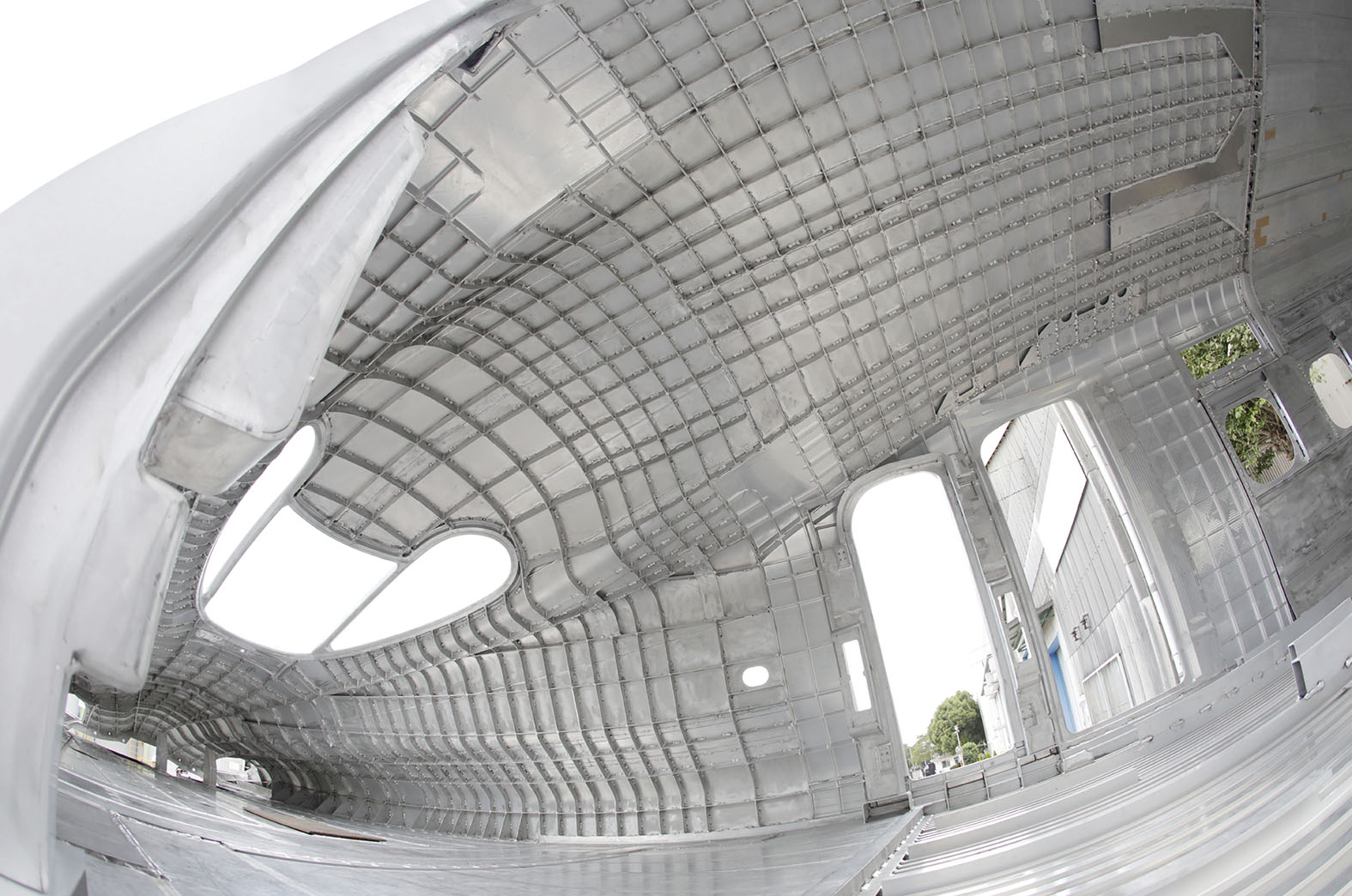
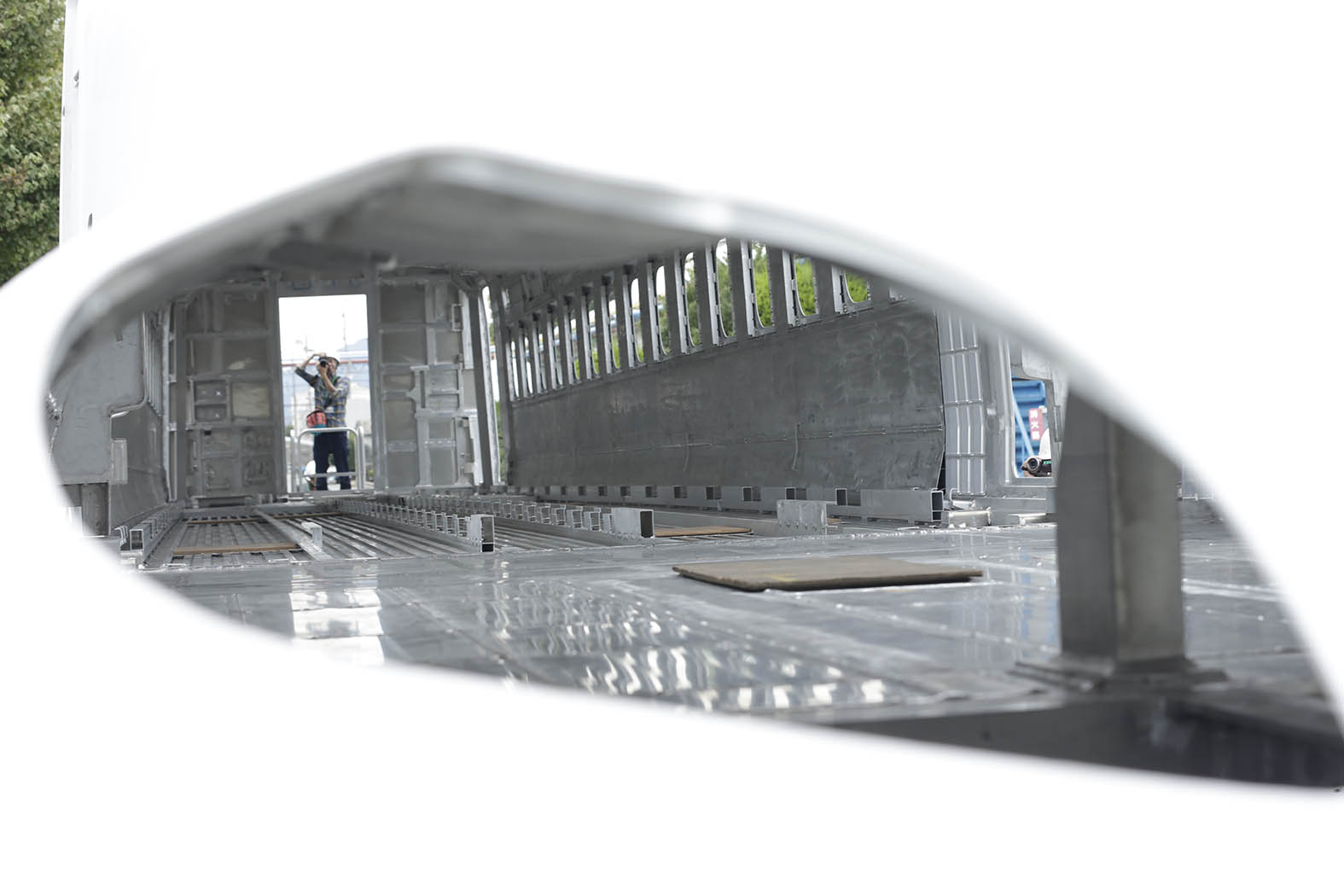
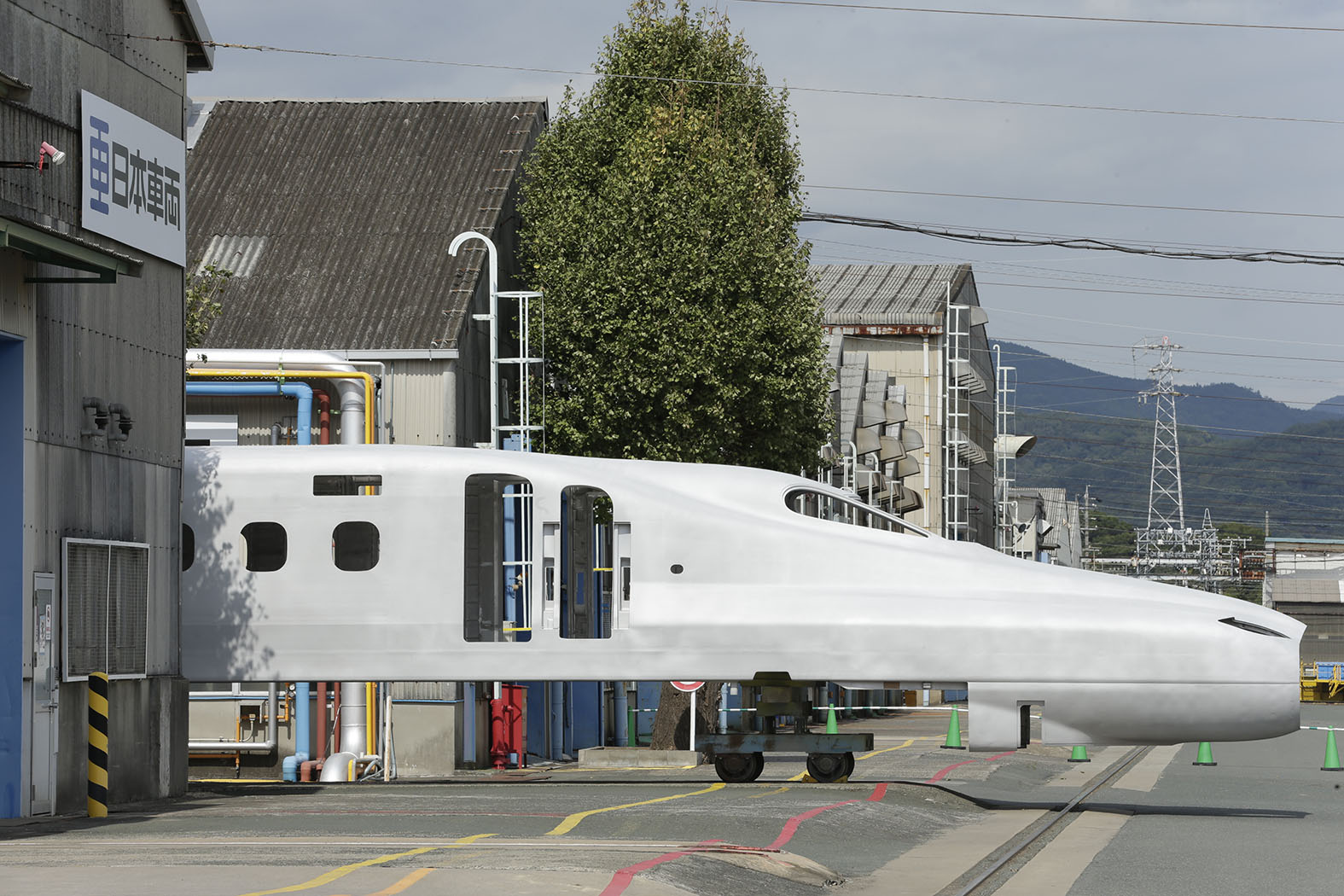
JR東海は2020年度に東海道新幹線に投入する新型車両「N700S」の開発を進める。床下の駆動システムのコンバーター、インバーターに炭化ケイ素(SiC)素子のパワー半導体を採用し、小型・軽量化する。顔である先頭車両の形状はシミュレーションと風洞実験により、風切り音などの騒音を数%減らす。
13年に投入した「N700A」以来の新型車両で、SiC素子は大手電機メーカー4社と共同開発した。SiC素子は発熱量が少なく、冷却機構を簡素化できるため、小型・軽量化が可能になる。
走行中の床下の風を取り込む冷却方式との組み合わせにより、1編成当たりの駆動システムの重量は、N700系の2割減の約47トンにできる。総合技術本部技術開発部の佐藤賢司車両制御チームマネージャーは「さらに軽量化できる」と限界まで挑戦する考えだ。
コンバーター、インバーターの小型・軽量化で、変圧器とひとまとめにするなど、床下機器の配置を現在よりコンパクトにできる。8種類ある配置パターンを4種類に集約できるため、さまざまな新幹線に適用できる標準車両が実現する。
16両の東海道新幹線以外にも、8両や12両の新幹線にも適用できるため、海外の新幹線方式の高速鉄道に車両を売り込みやすい。
先頭車両の形状は、N700Aに改良を加えた最終形状が既に決定。車両に沿って左右に直線の隆起を設けるなどして、空気抵抗を減らす。
形状の決定には4年間かけた。前半の2年間は制約なしに自由に考え、後半の2年間は実際の条件を基に考えた。シミュレーションソフトを用いて形状を考案し、15年2月には模型に強風を当てる風洞実験を開始し、データを取得・分析していった。
技術開発部の阿彦雄一高速技術チームマネージャーは「シミュレーションは手段でしかない」と説く。技術者のアイデアや工夫があってこそ、最終形状が生まれたと言える。
(文=名古屋・戸村智幸)
N700Sを製造する子会社、日本車両製造の豊川製作所で公開した。古屋政嗣JR東海新幹線鉄道事業本部車両部担当部長は「現時点で盛り込める技術を盛り込んだ」と自信を示した。
先頭車両は左右両サイドにエッジを立てた形状により、走行時の風の流れを整え、騒音や抵抗を低減できる。塗装前の状態で公開し、今後は確認試験車として使用する。
客室はグリーン車と普通車の座席・内装を配置したモックアップを公開。座席は現行車両「N700A」よりも沈み込みやすくしたほか、荷棚の照明が停車駅に近づくと明るくなり、荷物の置き忘れを防ぐ。
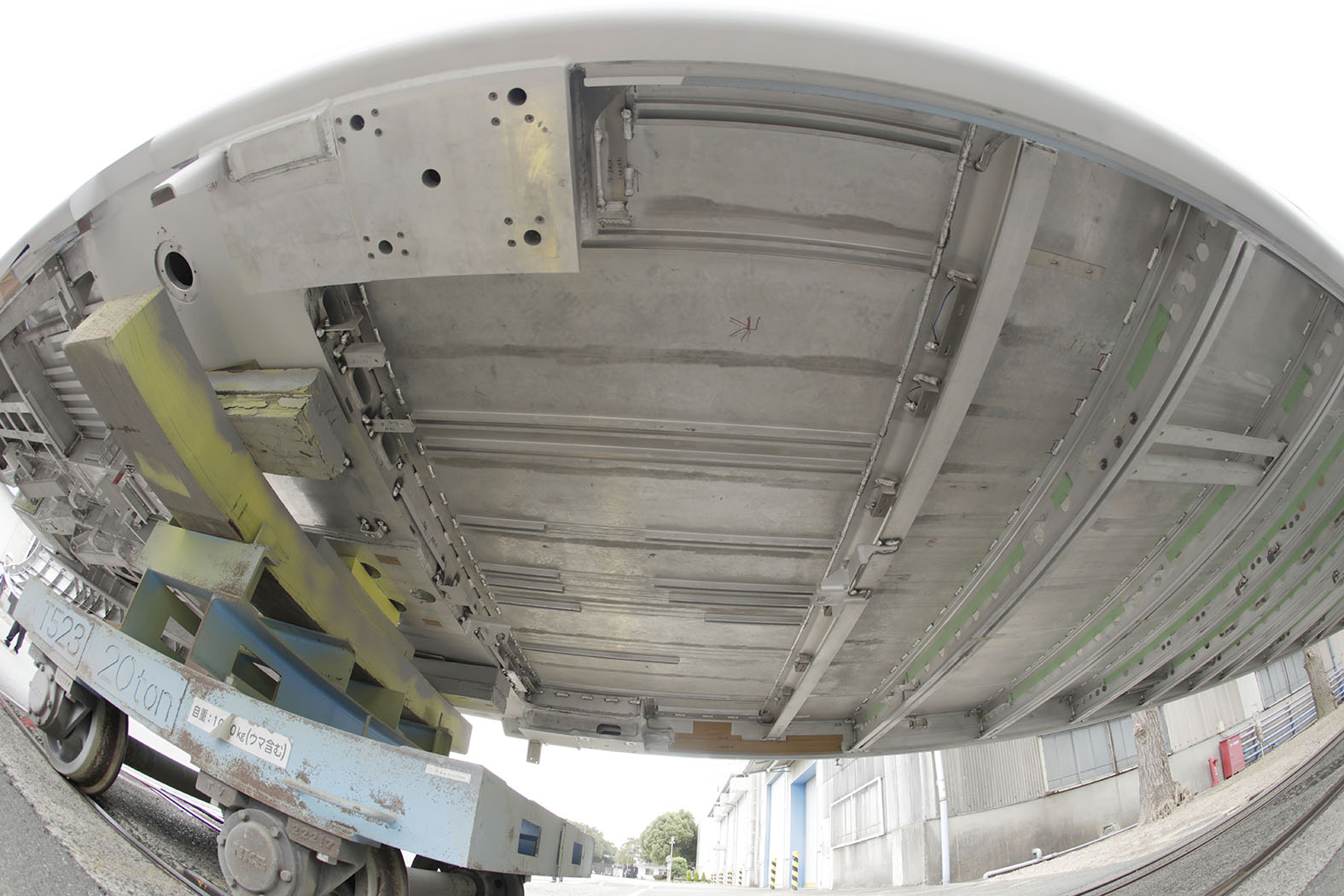
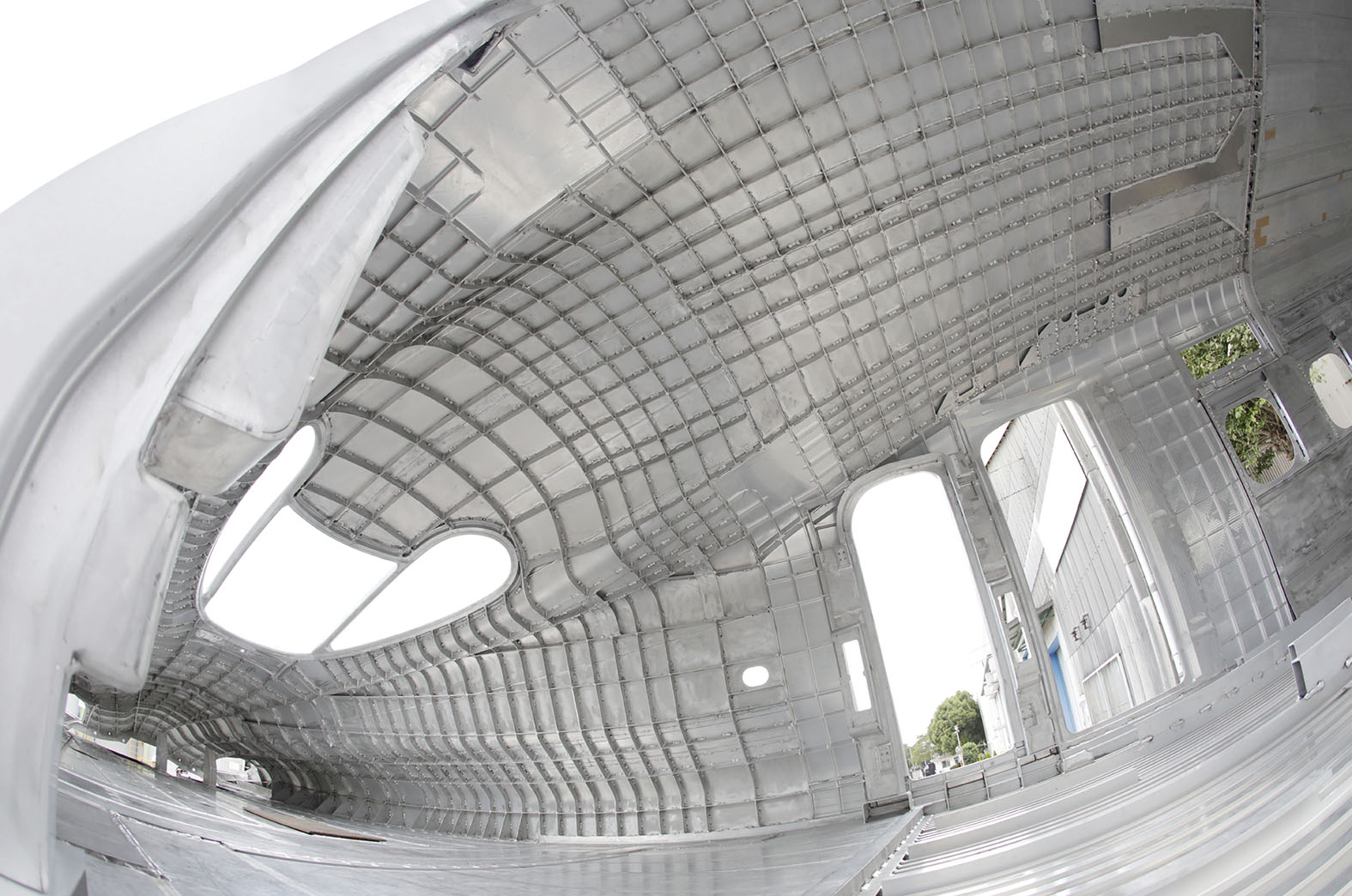
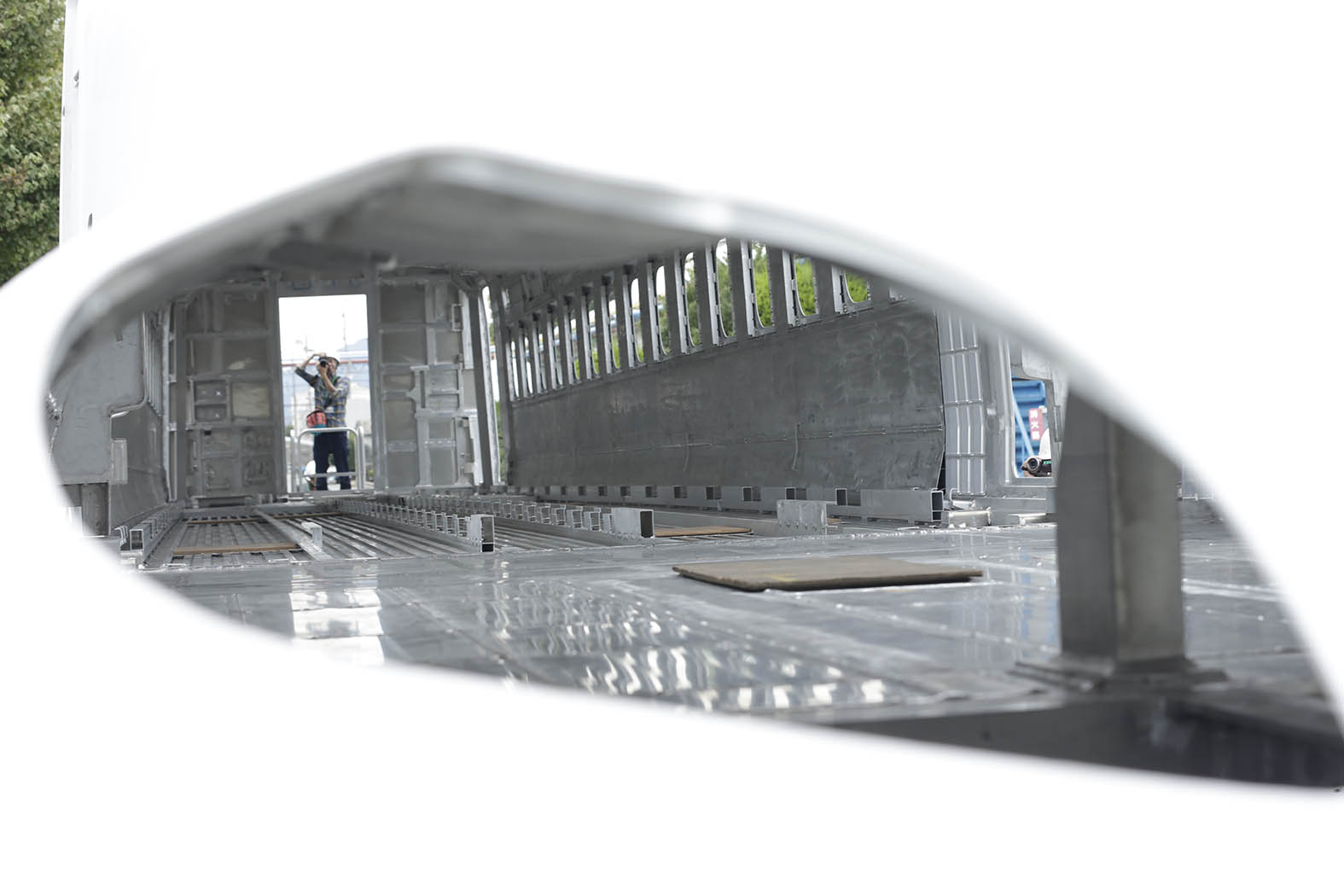
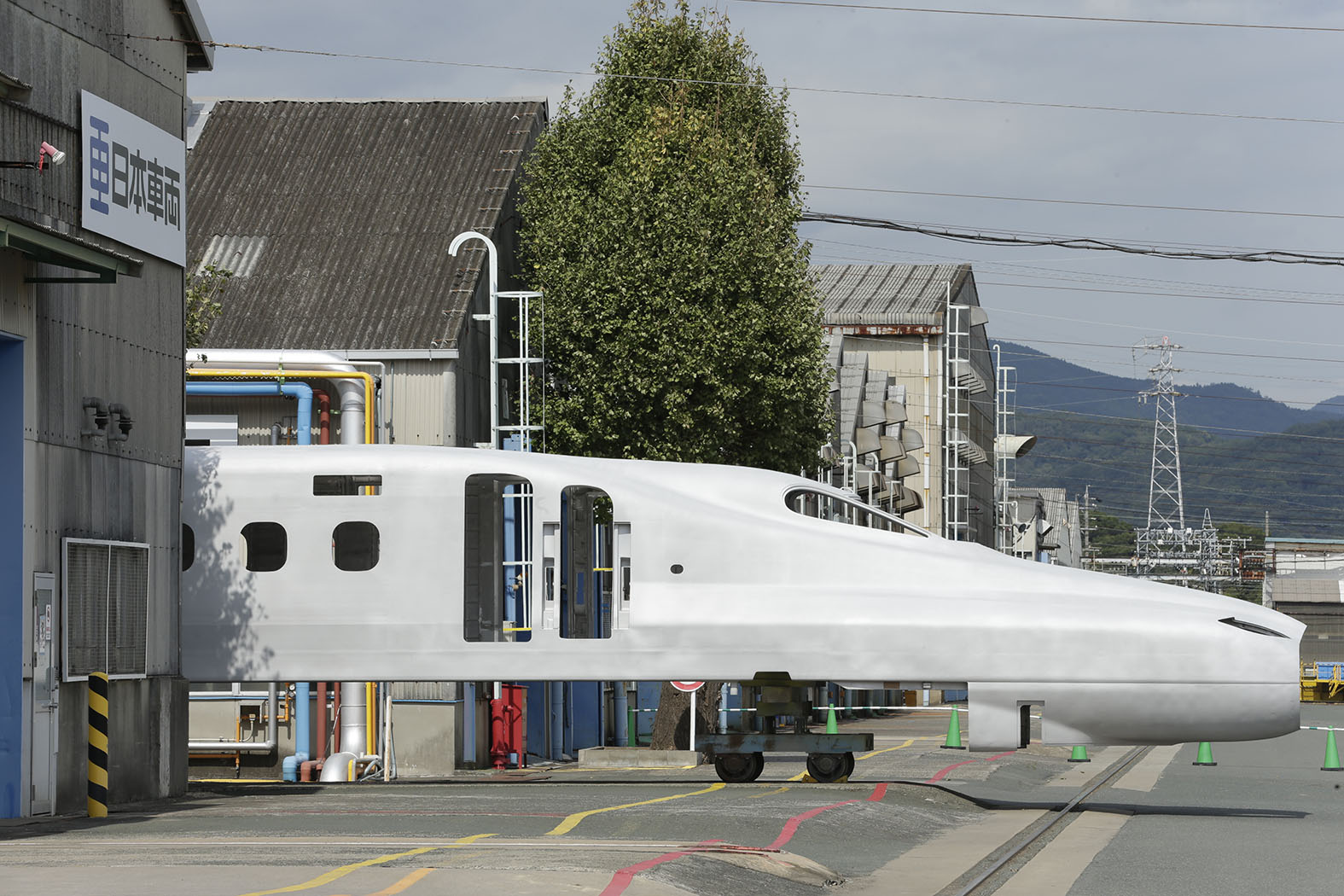
日刊工業新聞2017年10月2日
床下のヒミツ
JR東海は2020年度に東海道新幹線に投入する新型車両「N700S」の開発を進める。床下の駆動システムのコンバーター、インバーターに炭化ケイ素(SiC)素子のパワー半導体を採用し、小型・軽量化する。顔である先頭車両の形状はシミュレーションと風洞実験により、風切り音などの騒音を数%減らす。
13年に投入した「N700A」以来の新型車両で、SiC素子は大手電機メーカー4社と共同開発した。SiC素子は発熱量が少なく、冷却機構を簡素化できるため、小型・軽量化が可能になる。
走行中の床下の風を取り込む冷却方式との組み合わせにより、1編成当たりの駆動システムの重量は、N700系の2割減の約47トンにできる。総合技術本部技術開発部の佐藤賢司車両制御チームマネージャーは「さらに軽量化できる」と限界まで挑戦する考えだ。
コンバーター、インバーターの小型・軽量化で、変圧器とひとまとめにするなど、床下機器の配置を現在よりコンパクトにできる。8種類ある配置パターンを4種類に集約できるため、さまざまな新幹線に適用できる標準車両が実現する。
16両の東海道新幹線以外にも、8両や12両の新幹線にも適用できるため、海外の新幹線方式の高速鉄道に車両を売り込みやすい。
先頭車両の形状は、N700Aに改良を加えた最終形状が既に決定。車両に沿って左右に直線の隆起を設けるなどして、空気抵抗を減らす。
形状の決定には4年間かけた。前半の2年間は制約なしに自由に考え、後半の2年間は実際の条件を基に考えた。シミュレーションソフトを用いて形状を考案し、15年2月には模型に強風を当てる風洞実験を開始し、データを取得・分析していった。
技術開発部の阿彦雄一高速技術チームマネージャーは「シミュレーションは手段でしかない」と説く。技術者のアイデアや工夫があってこそ、最終形状が生まれたと言える。
(文=名古屋・戸村智幸)
日刊工業新聞2016年12月6日
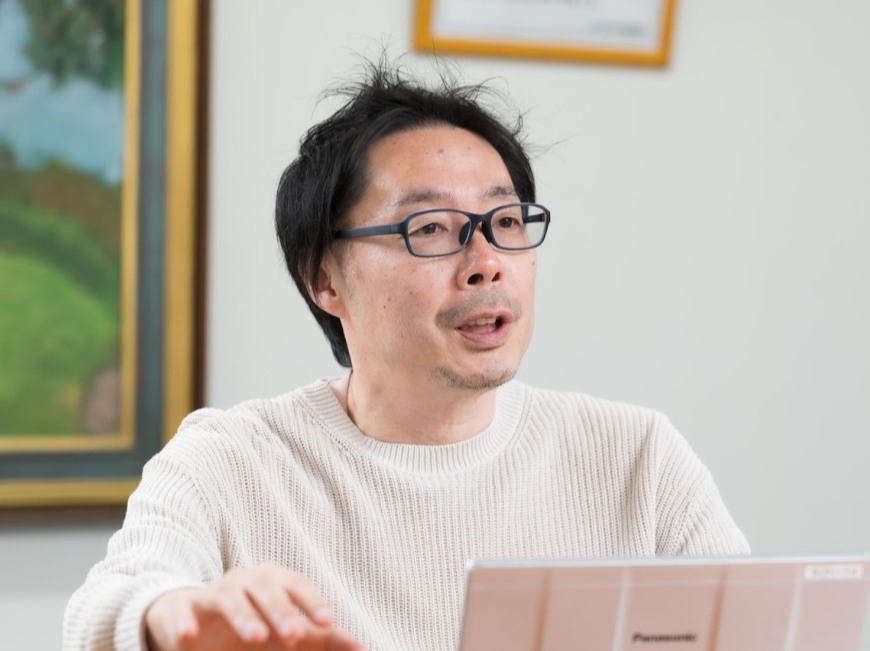