強度が1・5倍、航空機向けアルミ合金を開発した実力企業
コイワイが九大など連携。積層造形で大手に売り込みへ
コイワイ(神奈川県小田原市、小岩井豊己社長)は、九州大学などと連携し「高強度アルミニウム合金積層体」を開発した。既存のアルミより約1・5倍の強度を持つ。1年後をめどに強度を6000系・7000系のアルミ材(ジュラルミン)に近づける。強度が高く、積層造形でき、航空機の複雑な構造体などへの活用が期待できる。
金属積層工法で使うアルミ合金は、ケイ素やマグネシウムを添加しており、引っ張り強度は300メガパスカル程度にとどまる。また、3Dプリンターによる金属粉末積層工法では現在、ジュラルミンの造形はきわめて難しい。
新アルミ合金は既存のアルミ合金に使うケイ素などとは異なる元素を添加する。引っ張り強度は、400メガ―500メガパスカル。元素の添加はジュラルミンより少なく、安価に製造が可能という。
新アルミ合金は、東洋アルミニウム、九大、千葉工業大学との産学連携で実現した。九大、千葉工大などの知見を基に東洋アルミが素材を開発、その材料をコイワイが成形・製造した。特許も出願済み。今秋に軽金属学会で詳細を報告する。
海外では、米ゼネラル・エレクトリック(GE)や独シーメンスなどが金属粉末積層工法を試作・研究開発から量産品へと広げつつある。
コイワイは3月に宇宙航空分野の規格「JISQ9100認証」を取得。航空機部品の量産体制を構築している。
コイワイ(神奈川県小田原市、小岩井豊己社長)は、3Dプリンターを活用した積層砂型工法と金属粉末積層工法を不特定多数の顧客に提供した国内初のサービスビューローだ。船舶エンジンのマニホールドや自動車エンジン用ターボチャージャー(過給器)の試作開発を手がけている。
同社は2007年に3Dプリンターによる積層砂型工法の研究を開始。それ以前は自動車向け鋳物部品を試作していたが、顧客の求める高精度・高速のニーズに対応できず悩んでいた。若手人材も不足しており、「モノづくり革新と人材確保を満たすのが3Dプリンターだった」と小岩井社長は振り返る。
08年から砂型による試作提供を開始したが、当初は「3Dプリンターの砂型は採用できない」と理解が得られなかった。機械的性質の調査や従来製品と遜色ない品質証明などを一つ一つ検証していった。
3Dプリンターは木型をつくる工程を省くため短納期の試作が可能で、従来工法の3分の1―10分の1の価格で製作でき、顧客の評価も徐々に向上した。
12年には3次元データからダイレクトに金属部品をつくる金属粉末積層工法を開始し、より複雑な形状の部品を短時間で試作できるようになった。
小岩井社長は「鋳物と金属積層プリンター製品は全くの別物。砂型の進化形が金属積層ではない」と強調する。金属粉末ではチタンやコバルトクロムなどの硬い金属で、1ミリメートル以下の細くメッシュ形状などの精密な試作に対応できる。一方、砂型ではより大型製品が製作でき、少量の量産も可能だ。
金属積層工法で使うアルミ合金は、ケイ素やマグネシウムを添加しており、引っ張り強度は300メガパスカル程度にとどまる。また、3Dプリンターによる金属粉末積層工法では現在、ジュラルミンの造形はきわめて難しい。
新アルミ合金は既存のアルミ合金に使うケイ素などとは異なる元素を添加する。引っ張り強度は、400メガ―500メガパスカル。元素の添加はジュラルミンより少なく、安価に製造が可能という。
新アルミ合金は、東洋アルミニウム、九大、千葉工業大学との産学連携で実現した。九大、千葉工大などの知見を基に東洋アルミが素材を開発、その材料をコイワイが成形・製造した。特許も出願済み。今秋に軽金属学会で詳細を報告する。
海外では、米ゼネラル・エレクトリック(GE)や独シーメンスなどが金属粉末積層工法を試作・研究開発から量産品へと広げつつある。
コイワイは3月に宇宙航空分野の規格「JISQ9100認証」を取得。航空機部品の量産体制を構築している。
日刊工業新聞2017年6月30日
なぜ3Dプリンターに向き合ったのか
コイワイ(神奈川県小田原市、小岩井豊己社長)は、3Dプリンターを活用した積層砂型工法と金属粉末積層工法を不特定多数の顧客に提供した国内初のサービスビューローだ。船舶エンジンのマニホールドや自動車エンジン用ターボチャージャー(過給器)の試作開発を手がけている。
同社は2007年に3Dプリンターによる積層砂型工法の研究を開始。それ以前は自動車向け鋳物部品を試作していたが、顧客の求める高精度・高速のニーズに対応できず悩んでいた。若手人材も不足しており、「モノづくり革新と人材確保を満たすのが3Dプリンターだった」と小岩井社長は振り返る。
08年から砂型による試作提供を開始したが、当初は「3Dプリンターの砂型は採用できない」と理解が得られなかった。機械的性質の調査や従来製品と遜色ない品質証明などを一つ一つ検証していった。
3Dプリンターは木型をつくる工程を省くため短納期の試作が可能で、従来工法の3分の1―10分の1の価格で製作でき、顧客の評価も徐々に向上した。
12年には3次元データからダイレクトに金属部品をつくる金属粉末積層工法を開始し、より複雑な形状の部品を短時間で試作できるようになった。
小岩井社長は「鋳物と金属積層プリンター製品は全くの別物。砂型の進化形が金属積層ではない」と強調する。金属粉末ではチタンやコバルトクロムなどの硬い金属で、1ミリメートル以下の細くメッシュ形状などの精密な試作に対応できる。一方、砂型ではより大型製品が製作でき、少量の量産も可能だ。
日刊工業新聞2017年3月23日
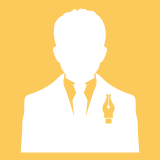