世界に450あるGEの“デジタル工場”の頂点が東京・日野にあった!
日本のヘルスケアの拠点、「ブリリアント・ファクトリー」の全貌
生産現場のデジタル化は自社の変革を推進してくれるだろう。上層部からも“現場にIoTを取り入れよ”とプレッシャーがかかりはじめた。でも、いざ自分ゴトとなると、具体的な導入イメージが持てない―。
産業向けIoTの重要性への認知が拡がる一方、昨年ガートナーが実施した調査では4割が『いまだにどこから手をつけるべきか分からない』と回答している。
米ゼネラル・エレクトリック(GE)はいま、「ブリリアント・ファクトリー」という考え方を掲げ、世界中に構える自社工場のすべてを進化させる取り組みを進めている。
目指すのは、最新のデジタル・テクノロジーを用いてリアルタイムでデータを活用し、製造オペレーションからサプライチェーンまで全体を『最適化』すること。
この取り組みの先端を走るのが、GEヘルスケアの東京・日野工場。世界に450ある自社工場の頂点、「ベスト・ブリリアント・ファクトリー(2016)」の称号も得たこの工場を取材すると、現場のマネージャー達が「ここはいま毎週、いや毎日、進化してますよ!」という。
今回は、たっぷりの取材写真と共に、GEにおける“工場デジタル化の実際”を紹介する。
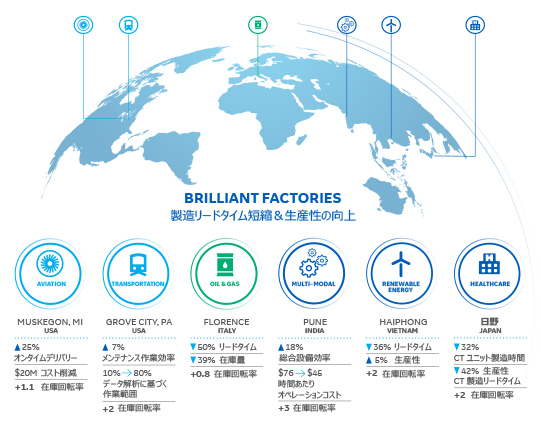
GEヘルスケア・ジャパン 日野本社工場 (東京都日野市)世界に450あるGEの自社工場の頂点「ベスト・ブリリアント・ファクトリー」の称号を持つ。ここで開催する「リーン・アカデミー」には、GEの事業部門を問わず国内外から毎年100名以上の受講者が。
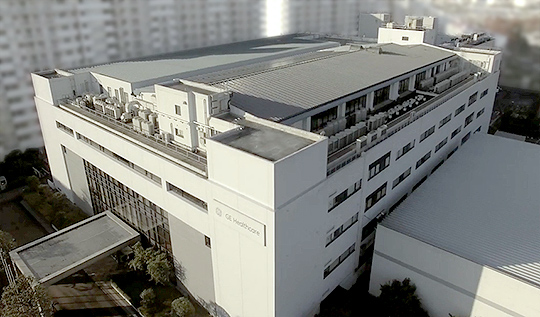
日野工場は、全世界に製造拠点を持つGEヘルスケアにあって、生産管理やカイゼンのモデル工場と位置づけられている。製造の効率化は日本チームの得意領域。
古くは「5S」や「VM(見える管理)」、90年代後半には「シックスシグマ」を、2002年からはそこにトヨタ生産方式を範とするリーンを組み合わせた「リーン・シックスシグマ」を導入し、絶えず品質と生産効率の向上を続けてきた。
最新のデジタル・ソリューションにどんなに投資しても、実際の現場に、ムダがなく洗練された生産方式が根付いていなければ十分な成果は得られない。
一方で、すでにカイゼンし尽くしたかに見える生産現場であっても、デジタル化によって従来は見えなかったカイゼン・ポイントを発見し、さらなる最適化を図ることが可能である。
デジタルとリーン(トヨタ生産方式を範とする、製造工程のムダを排除する生産方式)は相互にプラスの作用をもたらし、投資効果を最大化してくれる。
日野工場の森本淳工場長は「IoTとかデジタル・ツールを導入する前に、仕事のやり方を“標準化”しておくことが大切。全員が常に同じやり方をしているからこそ、数字の変化がどの工程に起因しているかを特定できる。だから対策が的確に進むし、 “Predix”のような世界共通のプラットフォームを通じてベストな方法をグローバル展開する、ということにも繋げることができる」と話す。
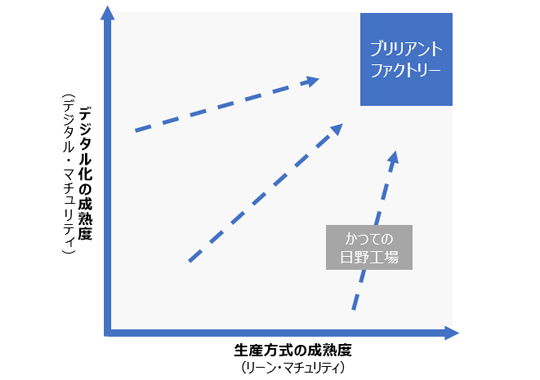
ムダの無い(=リーン)生産方式を実践しているか、どれだけデジタル化が進んでいるか。両方の成熟度が高いのがGEにおける「ブリリアント・ファクトリー」
生産方式が成熟した工場としてすでに高い評価を得ていた日野工場が、さらにデジタル化に取り組む意義とは何か。「何のためにカイゼンを進めるかといえば、我々が製造部門としてお客様に提供する価値、すなわち“品質・納期・コスト低減“を最大化するため。したがって、デジタル化によってカイゼンを加速させようという考えは、誰の腹にもストンと落ちるものだった」(森本氏)
これまでは手間がかかりすぎていた、生産工程のデータ収集と分析。それがデジタル・ツールによって自動化できるようになった結果、本来のフォーカスであるカイゼンに、時間を使えるようになったと言う。実際、ある主力製品ではIoT技術の活用によって製造リードタイムを65%も短縮することに成功している。
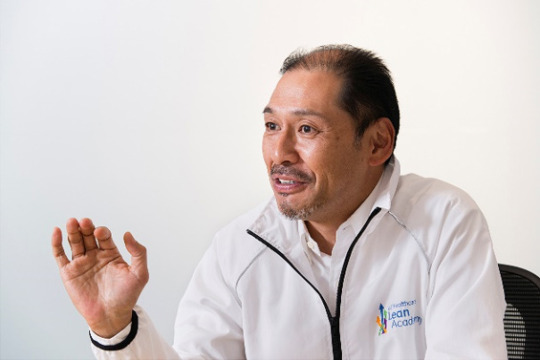
森本淳( GEヘルスケア・ジャパン 執行役員・製造本部長 日野工場長)
「いま思えば、リーン・シックスシグマはそれまでのカイゼンの延長線上。でも、ブリリアント・ファクトリーは全く次元の違う変革だと実感している。カルチャーチェンジが起こる」と強調する森本氏。
誰でも課題や効果が見えるので、現場の人が主体となってカイゼンのボトムアップが進み、それにより、誰でも、いつでも、どこでもカイゼンが起こるようになる。
「デジタル化によって、ひとりひとりがエンパワーされていると感じます。それぞれが能力を発揮し、活躍しやすくなる」と森本氏。
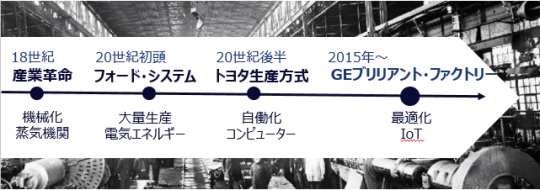
「第4次産業革命」という言葉がそのインパクトの大きさを示すように、これまでと異次元の変革が始動。GEは「ブリリアント・ファクトリー」と呼ぶ考え方のもと、これを推進する。
大型装置も小型の精密機器も製造する日野工場。製品によって製造技法やペインポイント(=お困りごと)が異なるため、デジタル化の目的や期待効果もさまざま。ここからは、製品ラインごとに、日野工場の取り組みの様子を紹介する。
【CTスキャナ用 “ガントリ” 製造ライン】
CTスキャナのX線チューブや検出器などを収めるドーナツ状の「ガントリ」。その大きさからも想像できるとおり、取り付ける部品点数が多いのが特徴。
会社設立の1982年当時は5日かかっていた製造リードタイムも、継続的なカイゼンの努力で、いまやわずか数時間にまで短縮。高品質を守りながらさらなる効率化を図るべく、デジタル化の焦点を「価値作業比率の向上」に置いた。
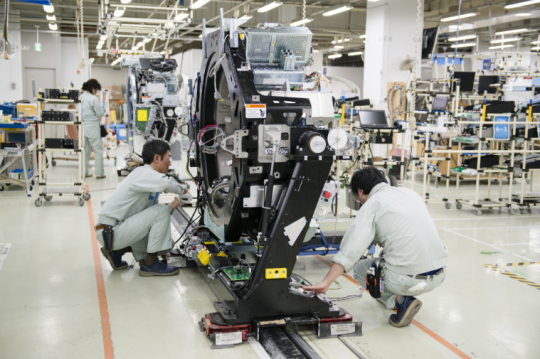
部品点数が多いため「部品を組み付けるときのムダ」をいかに省くかが効率化の鍵。
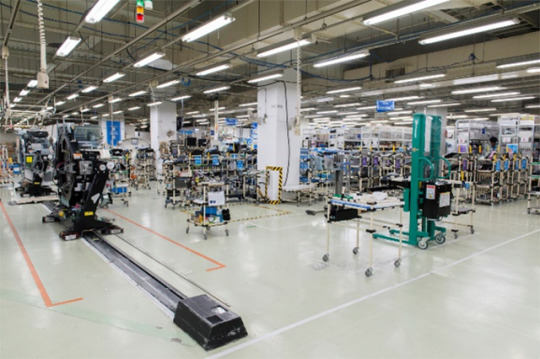
作業の進行とともに、レール上をゆっくりと進むガントリ。奥には個別工程ごとに必要な部品だけが載せられた、キットカートが並ぶ。
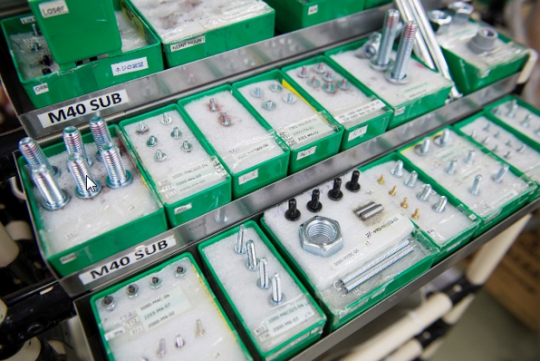
工程ごとに必要な部品だけが作業順にセットされたキットカートは、従来からの文化とも言える「リーン生産方式」のアプローチ。部品を取り出すムダな動作を省くだけでなく、付け忘れを防ぎ品質を担保する。
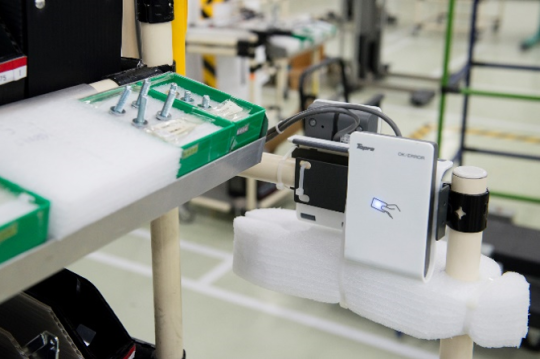
キットカートを引き出したり、工程を終えて返却位置に戻すと、センサーが反応して時間を記録。CTのブリリアントファクトリープロジェクトを担当する寺田有汰曰く「かつてカイゼンはストップウォッチ片手に進められていました。データ収集と解析をするには膨大な労力が必要で、手を出せない領域があった。でも、センサーやソフトウェアを活用できる今は違います」
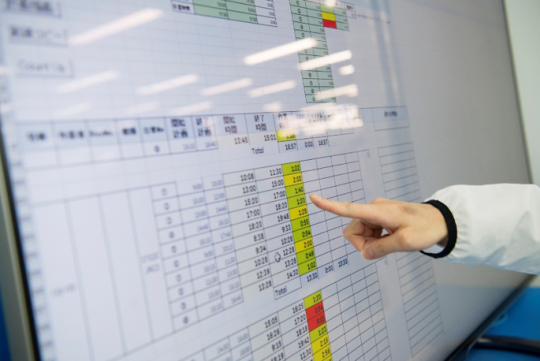
製造工程は、1工程=1時間で進捗を管理。緑はオンタイム、黄色は10分以内の遅れ、赤は10分以上の遅れを表す。
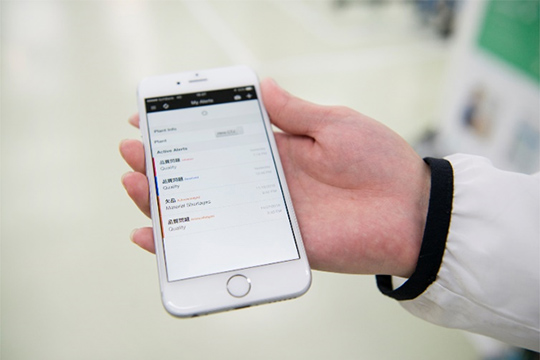
ラインでトラブルが発生した際、チームリーダーにアラートをとばすeAndonシステム。不具合が発生した場所や時間、内容が記録される。作業者は、QRコードやプルダウンメニューを使って簡単にアラート入力できる。
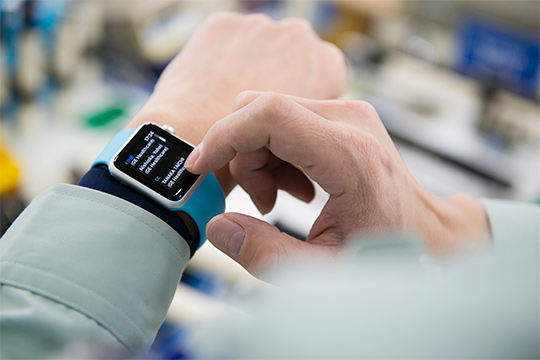
eAndonのアラートは、ウェアラブル端末でも確認可能。

品質検査の工程でも、リアルタイムでオペレーション状況をモニタリング。作業開始から終了までを点で表す“ボックスプロット”で作業時間のばらつきが出やすい工程やオペレーターごとの作業時間の差も一目瞭然。どこに改善ポイントがあるかを的確に把握でき、コツやノウハウの横展開を成果につなげやすい。
【超音波診断機用 “プローブ”製造ライン】
プローブとは、超音波診断の際に身体の表面に当てるマウスのような装置のこと。非常に精密な装置ゆえ高い技術力が求められ、世界中で使われるGE製プローブの約25%は、この日野工場から送り出されている。製造技法上、失敗してもやり直せずスクラップ(廃棄)せざるを得ないため、至上命題は「品質重視」。
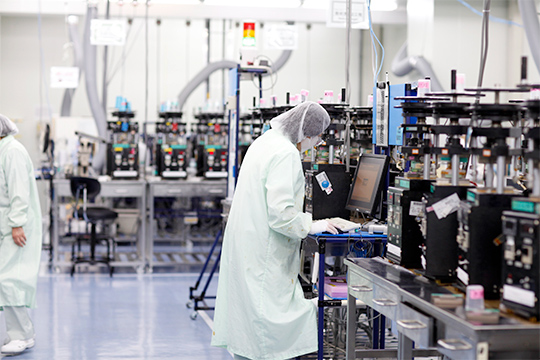
部品サイズがミクロン単位と小さく、かつ、生産個数が多いプローブの製造ライン。
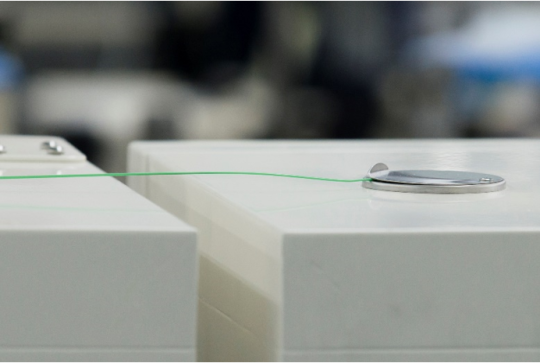
既存の機器に取り付けられた温度センサーから伸びる緑色のケーブル。大げさに新しい機器を導入しなくても、既存設備にセンサーを取り付けるだけで意味のある“見える化”が実現できる。
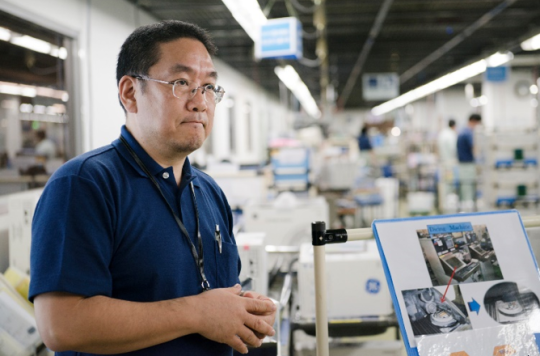
重要なのは、不具合や異常を検知することだけじゃない。「安定している=大丈夫だ、ということがわかることが大事」と語るのは、プローブ生産技術グループマネージャーの奥山栄太郎氏。何が「よい状態」であるかを理解することで不具合を発見しやすくなり、あるべき姿と次のゴール決められる。
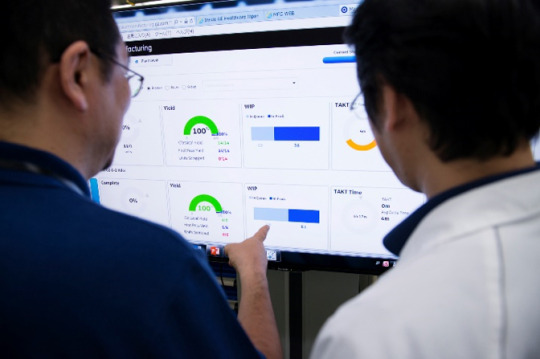
産業用IoTのクラウド・プラットフォーム「Predix」上で稼動する「Plant Pulse Optimizer(PPO)」なら在庫と工程、進捗(仕掛り品:WIP)のリアルタイムな状況が一目でわかる。以前は、不具合が発生すると膨大な量の完成品・仕掛り品の個数を手で数えて対策を考えていた。
【CTスキャナ用 “ディテクタ/コリメーター” 製造ライン】
ディテクタ/コリメーターとは、CTスキャナ内部のX線を検出し、電気信号へと変換する装置。これもまた精密で手作業やリワーク作業が多いうえ、このラインでは1000を超える工具や測定具の管理・点検を行う必要。情報入力の作業時間は全製造プロセスの10%に及ぶほど。そこで、デジタル化の成果目標は「手作業と煩雑な設備管理の簡略化」としました。
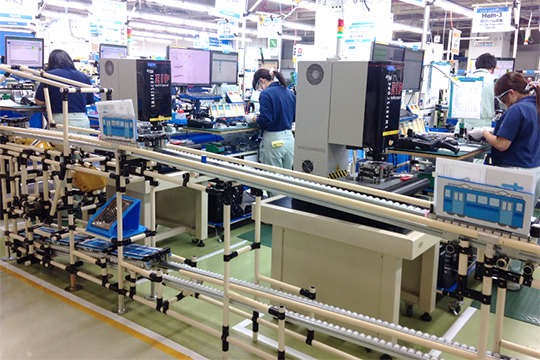
複雑で繊細な作業に緊張感を張り巡らしている製造担当者たち。
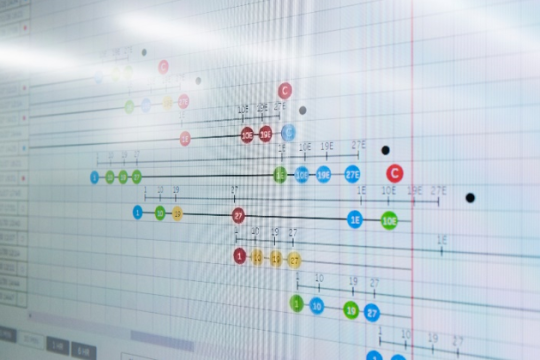
生産進捗管理と1000以上の工具・測定具の点検スケジュールや点検作業進捗はデジタル管理に切り替えた。「以前は壁一面に張り出していましたが、Webアプリ化した今では、いつでも、どこでもリアルタイムな状況がわかります」とディテクタのブリリアント・ファクトリーリーダーの吉田大氏。
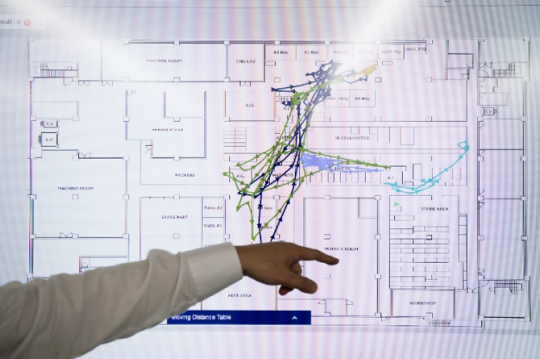
ビーコンを活用して、オペレーターの動線をチェック。スパゲティーチャートで無駄な動きが発生していないかを把握し、
ライン組み替え時などの配置の最適化を図る。
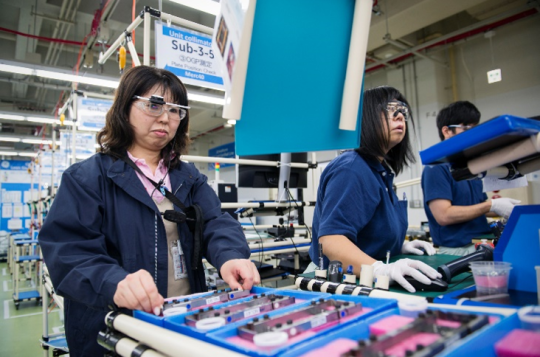
試験導入中のWearable Glass。PCなどのデバイスや資料を持ち歩く必要がなくなる。遠隔指示や新人教育などへの活用も検討中。
ブリリアント・ファクトリー化には3段階のステップがある。それは、Get connected(センサーなどの設置とネットワーク接続)、Get Insights(解析によるインサイト=洞察の獲得)、Get Optimized(最適化)。
しかし、最終ステップに到達しないと成果が得られないわけではない。「IoT」のようなバズワードに踊らされる必要もなければ、IoT導入が目的でもない。
「改善すべきことは何で、実現しやすいものは何か。小さく始めればいい。必要なデータはすでに身近にあり、カイゼン・ポイントは目の前にたくさん広がっているもの。小さな成功が得られれば、自然と次の道がひらけてくる」と森本工場長。
昨年、日野工場では現場から2500もの改善アイデアが挙がった。取材時に目にしたのも、若手からベテランまで口々にアイデアを披露して盛り上がる製造現場の定例ミーティングの様子。
「日々、現場のみんなと話すなかで確信しましたよ。あぁ、IoTはカイゼンを倍速にしてくれるツールなんだな、ってね」
(全写真:GEジャパン株式会社、GEヘルスケア・ジャパン株式会社)
産業向けIoTの重要性への認知が拡がる一方、昨年ガートナーが実施した調査では4割が『いまだにどこから手をつけるべきか分からない』と回答している。
米ゼネラル・エレクトリック(GE)はいま、「ブリリアント・ファクトリー」という考え方を掲げ、世界中に構える自社工場のすべてを進化させる取り組みを進めている。
目指すのは、最新のデジタル・テクノロジーを用いてリアルタイムでデータを活用し、製造オペレーションからサプライチェーンまで全体を『最適化』すること。
この取り組みの先端を走るのが、GEヘルスケアの東京・日野工場。世界に450ある自社工場の頂点、「ベスト・ブリリアント・ファクトリー(2016)」の称号も得たこの工場を取材すると、現場のマネージャー達が「ここはいま毎週、いや毎日、進化してますよ!」という。
今回は、たっぷりの取材写真と共に、GEにおける“工場デジタル化の実際”を紹介する。
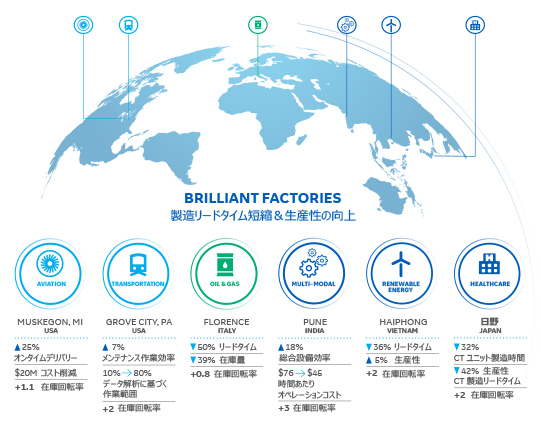
GEヘルスケア・ジャパン 日野本社工場 (東京都日野市)世界に450あるGEの自社工場の頂点「ベスト・ブリリアント・ファクトリー」の称号を持つ。ここで開催する「リーン・アカデミー」には、GEの事業部門を問わず国内外から毎年100名以上の受講者が。
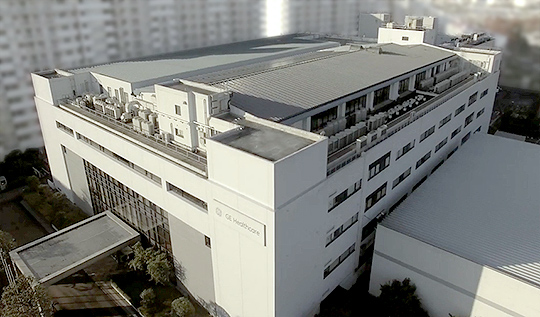
日野工場は、全世界に製造拠点を持つGEヘルスケアにあって、生産管理やカイゼンのモデル工場と位置づけられている。製造の効率化は日本チームの得意領域。
古くは「5S」や「VM(見える管理)」、90年代後半には「シックスシグマ」を、2002年からはそこにトヨタ生産方式を範とするリーンを組み合わせた「リーン・シックスシグマ」を導入し、絶えず品質と生産効率の向上を続けてきた。
成功のための掟
最新のデジタル・ソリューションにどんなに投資しても、実際の現場に、ムダがなく洗練された生産方式が根付いていなければ十分な成果は得られない。
一方で、すでにカイゼンし尽くしたかに見える生産現場であっても、デジタル化によって従来は見えなかったカイゼン・ポイントを発見し、さらなる最適化を図ることが可能である。
デジタルとリーン(トヨタ生産方式を範とする、製造工程のムダを排除する生産方式)は相互にプラスの作用をもたらし、投資効果を最大化してくれる。
日野工場の森本淳工場長は「IoTとかデジタル・ツールを導入する前に、仕事のやり方を“標準化”しておくことが大切。全員が常に同じやり方をしているからこそ、数字の変化がどの工程に起因しているかを特定できる。だから対策が的確に進むし、 “Predix”のような世界共通のプラットフォームを通じてベストな方法をグローバル展開する、ということにも繋げることができる」と話す。
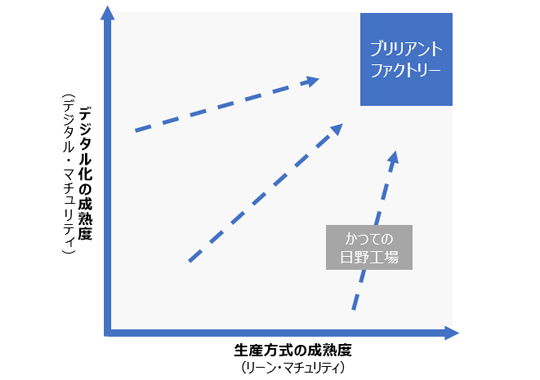
ムダの無い(=リーン)生産方式を実践しているか、どれだけデジタル化が進んでいるか。両方の成熟度が高いのがGEにおける「ブリリアント・ファクトリー」
スローガンは「カイゼンを倍速に!」
生産方式が成熟した工場としてすでに高い評価を得ていた日野工場が、さらにデジタル化に取り組む意義とは何か。「何のためにカイゼンを進めるかといえば、我々が製造部門としてお客様に提供する価値、すなわち“品質・納期・コスト低減“を最大化するため。したがって、デジタル化によってカイゼンを加速させようという考えは、誰の腹にもストンと落ちるものだった」(森本氏)
これまでは手間がかかりすぎていた、生産工程のデータ収集と分析。それがデジタル・ツールによって自動化できるようになった結果、本来のフォーカスであるカイゼンに、時間を使えるようになったと言う。実際、ある主力製品ではIoT技術の活用によって製造リードタイムを65%も短縮することに成功している。
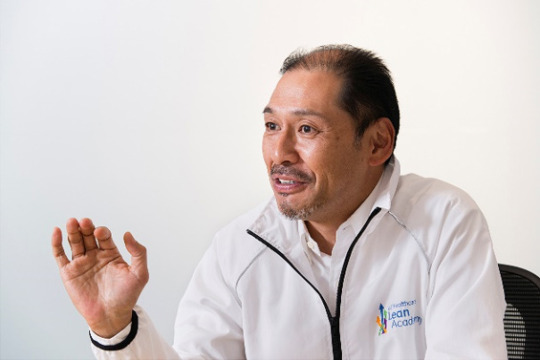
「いま思えば、リーン・シックスシグマはそれまでのカイゼンの延長線上。でも、ブリリアント・ファクトリーは全く次元の違う変革だと実感している。カルチャーチェンジが起こる」と強調する森本氏。
誰でも課題や効果が見えるので、現場の人が主体となってカイゼンのボトムアップが進み、それにより、誰でも、いつでも、どこでもカイゼンが起こるようになる。
「デジタル化によって、ひとりひとりがエンパワーされていると感じます。それぞれが能力を発揮し、活躍しやすくなる」と森本氏。
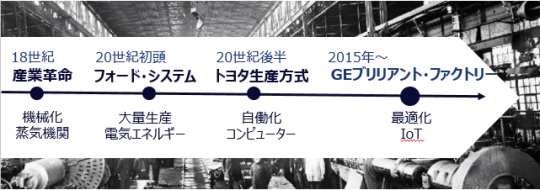
「第4次産業革命」という言葉がそのインパクトの大きさを示すように、これまでと異次元の変革が始動。GEは「ブリリアント・ファクトリー」と呼ぶ考え方のもと、これを推進する。
初公開!日野工場のリアルな「工場デジタル化」
大型装置も小型の精密機器も製造する日野工場。製品によって製造技法やペインポイント(=お困りごと)が異なるため、デジタル化の目的や期待効果もさまざま。ここからは、製品ラインごとに、日野工場の取り組みの様子を紹介する。
【CTスキャナ用 “ガントリ” 製造ライン】
CTスキャナのX線チューブや検出器などを収めるドーナツ状の「ガントリ」。その大きさからも想像できるとおり、取り付ける部品点数が多いのが特徴。
会社設立の1982年当時は5日かかっていた製造リードタイムも、継続的なカイゼンの努力で、いまやわずか数時間にまで短縮。高品質を守りながらさらなる効率化を図るべく、デジタル化の焦点を「価値作業比率の向上」に置いた。
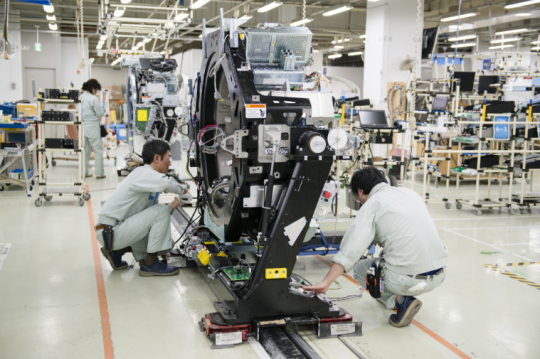
部品点数が多いため「部品を組み付けるときのムダ」をいかに省くかが効率化の鍵。
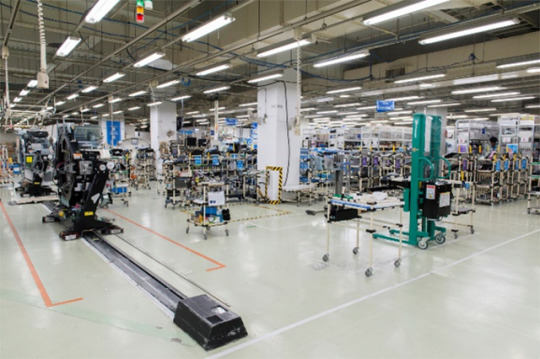
作業の進行とともに、レール上をゆっくりと進むガントリ。奥には個別工程ごとに必要な部品だけが載せられた、キットカートが並ぶ。
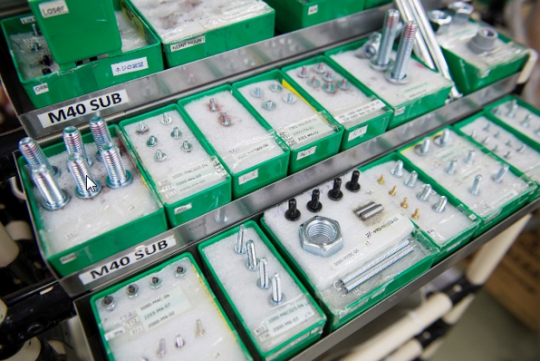
工程ごとに必要な部品だけが作業順にセットされたキットカートは、従来からの文化とも言える「リーン生産方式」のアプローチ。部品を取り出すムダな動作を省くだけでなく、付け忘れを防ぎ品質を担保する。
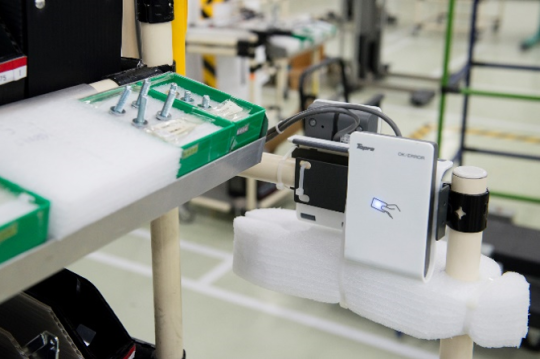
キットカートを引き出したり、工程を終えて返却位置に戻すと、センサーが反応して時間を記録。CTのブリリアントファクトリープロジェクトを担当する寺田有汰曰く「かつてカイゼンはストップウォッチ片手に進められていました。データ収集と解析をするには膨大な労力が必要で、手を出せない領域があった。でも、センサーやソフトウェアを活用できる今は違います」
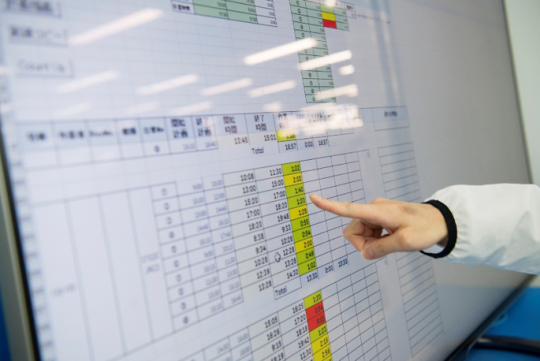
製造工程は、1工程=1時間で進捗を管理。緑はオンタイム、黄色は10分以内の遅れ、赤は10分以上の遅れを表す。
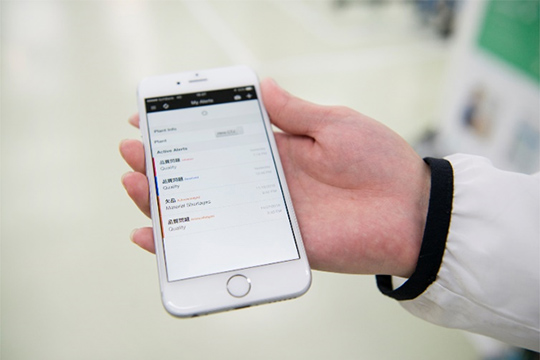
ラインでトラブルが発生した際、チームリーダーにアラートをとばすeAndonシステム。不具合が発生した場所や時間、内容が記録される。作業者は、QRコードやプルダウンメニューを使って簡単にアラート入力できる。
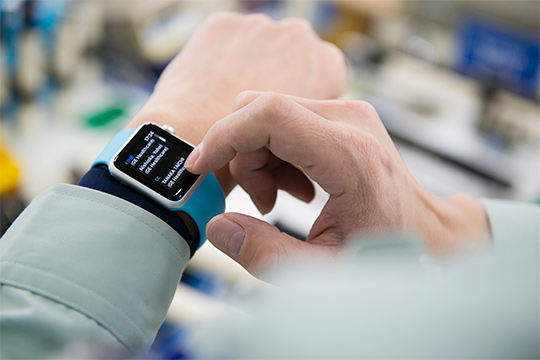
eAndonのアラートは、ウェアラブル端末でも確認可能。

品質検査の工程でも、リアルタイムでオペレーション状況をモニタリング。作業開始から終了までを点で表す“ボックスプロット”で作業時間のばらつきが出やすい工程やオペレーターごとの作業時間の差も一目瞭然。どこに改善ポイントがあるかを的確に把握でき、コツやノウハウの横展開を成果につなげやすい。
【超音波診断機用 “プローブ”製造ライン】
プローブとは、超音波診断の際に身体の表面に当てるマウスのような装置のこと。非常に精密な装置ゆえ高い技術力が求められ、世界中で使われるGE製プローブの約25%は、この日野工場から送り出されている。製造技法上、失敗してもやり直せずスクラップ(廃棄)せざるを得ないため、至上命題は「品質重視」。
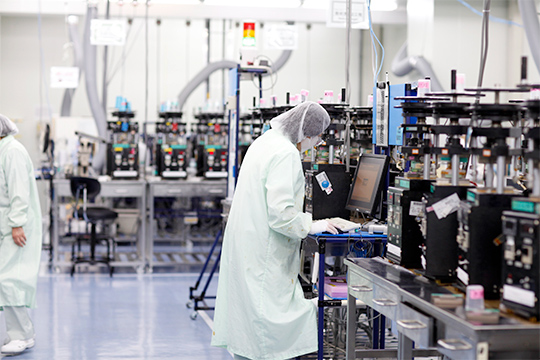
部品サイズがミクロン単位と小さく、かつ、生産個数が多いプローブの製造ライン。
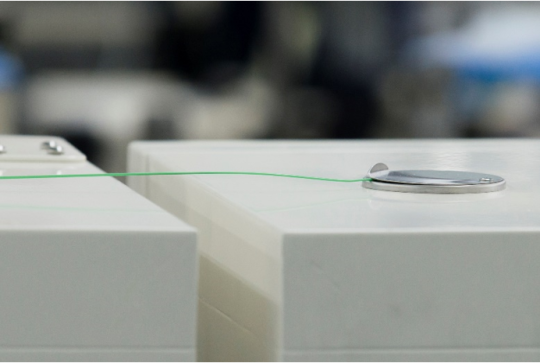
既存の機器に取り付けられた温度センサーから伸びる緑色のケーブル。大げさに新しい機器を導入しなくても、既存設備にセンサーを取り付けるだけで意味のある“見える化”が実現できる。
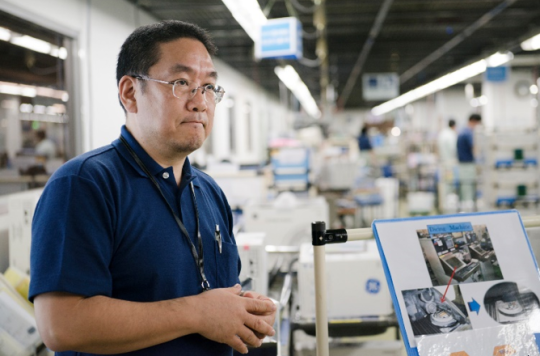
重要なのは、不具合や異常を検知することだけじゃない。「安定している=大丈夫だ、ということがわかることが大事」と語るのは、プローブ生産技術グループマネージャーの奥山栄太郎氏。何が「よい状態」であるかを理解することで不具合を発見しやすくなり、あるべき姿と次のゴール決められる。
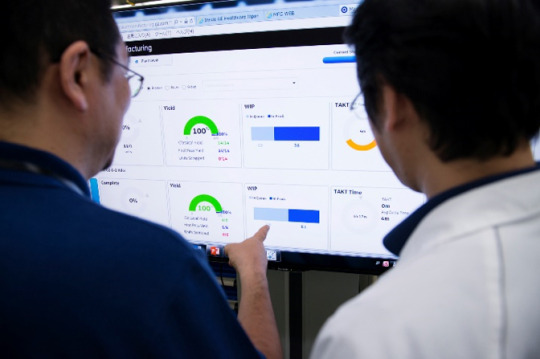
産業用IoTのクラウド・プラットフォーム「Predix」上で稼動する「Plant Pulse Optimizer(PPO)」なら在庫と工程、進捗(仕掛り品:WIP)のリアルタイムな状況が一目でわかる。以前は、不具合が発生すると膨大な量の完成品・仕掛り品の個数を手で数えて対策を考えていた。
【CTスキャナ用 “ディテクタ/コリメーター” 製造ライン】
ディテクタ/コリメーターとは、CTスキャナ内部のX線を検出し、電気信号へと変換する装置。これもまた精密で手作業やリワーク作業が多いうえ、このラインでは1000を超える工具や測定具の管理・点検を行う必要。情報入力の作業時間は全製造プロセスの10%に及ぶほど。そこで、デジタル化の成果目標は「手作業と煩雑な設備管理の簡略化」としました。
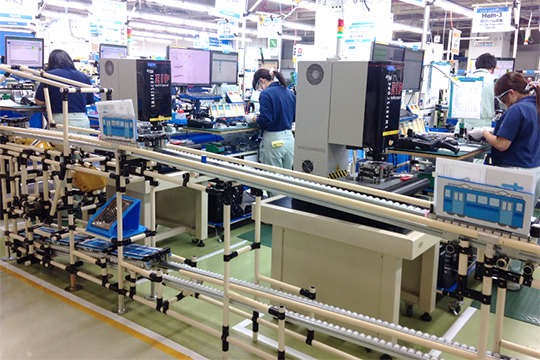
複雑で繊細な作業に緊張感を張り巡らしている製造担当者たち。
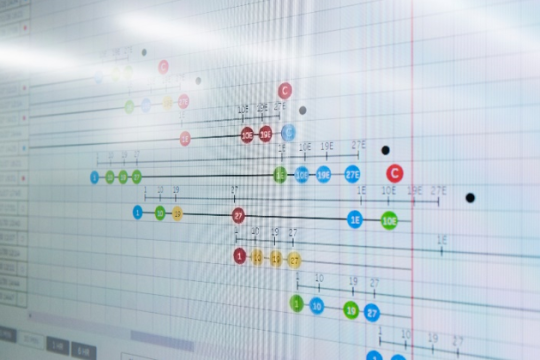
生産進捗管理と1000以上の工具・測定具の点検スケジュールや点検作業進捗はデジタル管理に切り替えた。「以前は壁一面に張り出していましたが、Webアプリ化した今では、いつでも、どこでもリアルタイムな状況がわかります」とディテクタのブリリアント・ファクトリーリーダーの吉田大氏。
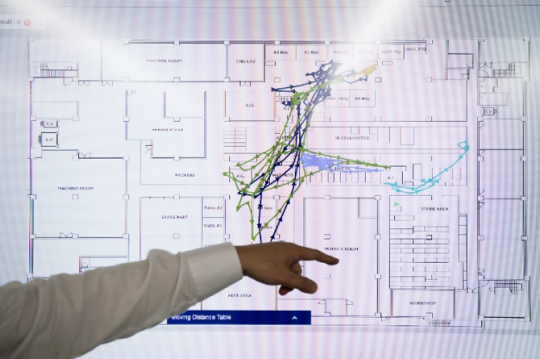
ビーコンを活用して、オペレーターの動線をチェック。スパゲティーチャートで無駄な動きが発生していないかを把握し、
ライン組み替え時などの配置の最適化を図る。
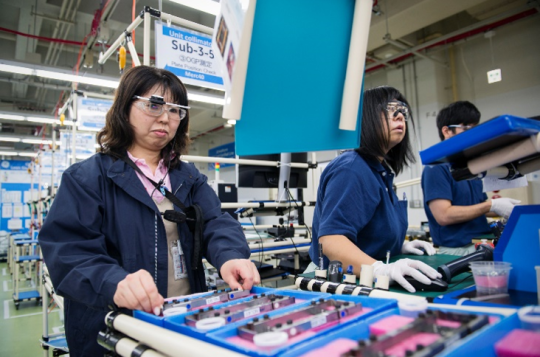
試験導入中のWearable Glass。PCなどのデバイスや資料を持ち歩く必要がなくなる。遠隔指示や新人教育などへの活用も検討中。
答えは現場にある!
ブリリアント・ファクトリー化には3段階のステップがある。それは、Get connected(センサーなどの設置とネットワーク接続)、Get Insights(解析によるインサイト=洞察の獲得)、Get Optimized(最適化)。
しかし、最終ステップに到達しないと成果が得られないわけではない。「IoT」のようなバズワードに踊らされる必要もなければ、IoT導入が目的でもない。
「改善すべきことは何で、実現しやすいものは何か。小さく始めればいい。必要なデータはすでに身近にあり、カイゼン・ポイントは目の前にたくさん広がっているもの。小さな成功が得られれば、自然と次の道がひらけてくる」と森本工場長。
昨年、日野工場では現場から2500もの改善アイデアが挙がった。取材時に目にしたのも、若手からベテランまで口々にアイデアを披露して盛り上がる製造現場の定例ミーティングの様子。
「日々、現場のみんなと話すなかで確信しましたよ。あぁ、IoTはカイゼンを倍速にしてくれるツールなんだな、ってね」
(全写真:GEジャパン株式会社、GEヘルスケア・ジャパン株式会社)