日米の先進工場から見えてきたホンダの新潮流
寄居=輸出モデル増加で自動化に逆行。オハイオ=「NSX」生産でミグ溶接を完全自動化
国内最新鋭の完成車工場として3年前に稼働したホンダの寄居工場(埼玉県寄居町)が変化している。生産技術の発信拠点として自動化を着々と広げる一方で、輸出拡大への戦略転換を受けて、海外モデルにしかないサンルーフの取り付け装置を導入するなどの対応にも追われている。
「新たな生産技術を生み出して海外に展開し、世界の工場の競争力を底上げする」。河野丈洋寄居工場長は国内工場の役割をこう強調する。中でも寄居工場は国内では23年ぶりの新規工場とあって、新技術を試すには格好の場。実際多くの新技術を導入している。
例えば、ドアの内側と外側のパネルの縁をローラーで押しつけて張り合わせる技術「ローラーヘム」や、インストルメントパネル(インパネ)を車内に自動で組み付けるロボットは稼働当初から取り入れた最新技術だ。
特にロボットによる手作業の自動化は、人材不足に悩まされる日本の生産現場にとって大きな課題。「ホンダの世界の工場の中で最も自動化が進んでいる」(同)寄居工場だが、昨年も「パワードライブユニット」という電装品を取り付ける作業と、工程上空けざるをえない穴を「グロメット」というゴム状の部品で最後にふたをする作業を自動化。さらに自動化を進める方針だ。
一方、寄居工場はホンダの世界生産戦略の変化のまっただ中にいる。小型車「フィット」、スポーツ多目的車(SUV)「ヴェゼル」など小型車を生産しているが、かつては国内向けがすべてだった。ホンダは国内生産のほぼすべてを国内販売に振り向けて輸出を減らす戦略をとっていた。
だが市場環境が厳しくなり、度重なるリコールによる品質問題も重なって国内販売が低迷。輸出を減らす戦略が裏目に出て国内工場の稼働率が落ち込み、輸出モデルの生産を増やす方針に転換した。
寄居工場ではこれまでの日本モデルに加え、15年から欧州と北米向けのフィットの生産を始めた。国内も海外も基本的には同じ車種だから大きな変更はないが、わずかな仕様の差で生産現場が対応に追われる。
例えば、日本モデルにはないサンルーフ付きの仕様に対応するために、新たに取り付け装置を導入した。ガソリンタンクの大きさが日本と米国で異なるため、従来から使っていた自動取り付け機にタンクが収まらず、応急措置として手作業で対応。自動化に逆行する事例も起きている。
現在は輸出向けが日産500台、国内向けが日産500台のペースで生産しておりフル稼働状態だ。世界をリードする役回りだけに、戦略転換の中にあっても高稼働を維持しつつ生産技術を生み出し続けることが求められている。
一方、新型高級スポーツカー「NSX」の生産を米国オハイオ州の専用工場で4月下旬から始める。骨格の接合には業界初となる100%自動化したミグ溶接を取り入れるなど最新の生産技術と職人技の調和を実現したという。米国では2月に受注を始めている。日本でも売り出すが発売時期は未定。
オハイオ州メアリズビルに新設した専用工場は、100人の従業員が各工程で先進のロボット技術と協調しながら、高度な品質と職人技を実現できるようにしたという。
骨格の接合にはボディーを360度回転させることができる治具を導入し、ロボット溶接アームをアクセスしやすくして100%自動化した。
砂型を使って急冷する「アブレーション鋳造」という技術を骨格の接合部品の生産に導入した。同技術を自動車に応用するのは世界で初めてという。NSXに搭載する3・5リットルV6ターボエンジンを生産する同州のアンナ工場に導入した。
先代NSXは日本で生産していたが2005年に終了。世界的な金融危機で次期モデルの開発を一時凍結したが、復活を機に米国生産に移した。
(文=池田勝敏)
ロボットなどの新技術を試す場
「新たな生産技術を生み出して海外に展開し、世界の工場の競争力を底上げする」。河野丈洋寄居工場長は国内工場の役割をこう強調する。中でも寄居工場は国内では23年ぶりの新規工場とあって、新技術を試すには格好の場。実際多くの新技術を導入している。
例えば、ドアの内側と外側のパネルの縁をローラーで押しつけて張り合わせる技術「ローラーヘム」や、インストルメントパネル(インパネ)を車内に自動で組み付けるロボットは稼働当初から取り入れた最新技術だ。
特にロボットによる手作業の自動化は、人材不足に悩まされる日本の生産現場にとって大きな課題。「ホンダの世界の工場の中で最も自動化が進んでいる」(同)寄居工場だが、昨年も「パワードライブユニット」という電装品を取り付ける作業と、工程上空けざるをえない穴を「グロメット」というゴム状の部品で最後にふたをする作業を自動化。さらに自動化を進める方針だ。
変わる世界戦略の中心地
一方、寄居工場はホンダの世界生産戦略の変化のまっただ中にいる。小型車「フィット」、スポーツ多目的車(SUV)「ヴェゼル」など小型車を生産しているが、かつては国内向けがすべてだった。ホンダは国内生産のほぼすべてを国内販売に振り向けて輸出を減らす戦略をとっていた。
だが市場環境が厳しくなり、度重なるリコールによる品質問題も重なって国内販売が低迷。輸出を減らす戦略が裏目に出て国内工場の稼働率が落ち込み、輸出モデルの生産を増やす方針に転換した。
寄居工場ではこれまでの日本モデルに加え、15年から欧州と北米向けのフィットの生産を始めた。国内も海外も基本的には同じ車種だから大きな変更はないが、わずかな仕様の差で生産現場が対応に追われる。
例えば、日本モデルにはないサンルーフ付きの仕様に対応するために、新たに取り付け装置を導入した。ガソリンタンクの大きさが日本と米国で異なるため、従来から使っていた自動取り付け機にタンクが収まらず、応急措置として手作業で対応。自動化に逆行する事例も起きている。
現在は輸出向けが日産500台、国内向けが日産500台のペースで生産しておりフル稼働状態だ。世界をリードする役回りだけに、戦略転換の中にあっても高稼働を維持しつつ生産技術を生み出し続けることが求められている。
米国の職人がロボットと協調しスポーツカーづくり
一方、新型高級スポーツカー「NSX」の生産を米国オハイオ州の専用工場で4月下旬から始める。骨格の接合には業界初となる100%自動化したミグ溶接を取り入れるなど最新の生産技術と職人技の調和を実現したという。米国では2月に受注を始めている。日本でも売り出すが発売時期は未定。
オハイオ州メアリズビルに新設した専用工場は、100人の従業員が各工程で先進のロボット技術と協調しながら、高度な品質と職人技を実現できるようにしたという。
骨格の接合にはボディーを360度回転させることができる治具を導入し、ロボット溶接アームをアクセスしやすくして100%自動化した。
砂型を使って急冷する「アブレーション鋳造」という技術を骨格の接合部品の生産に導入した。同技術を自動車に応用するのは世界で初めてという。NSXに搭載する3・5リットルV6ターボエンジンを生産する同州のアンナ工場に導入した。
先代NSXは日本で生産していたが2005年に終了。世界的な金融危機で次期モデルの開発を一時凍結したが、復活を機に米国生産に移した。
(文=池田勝敏)
2016年3月21日 自動車
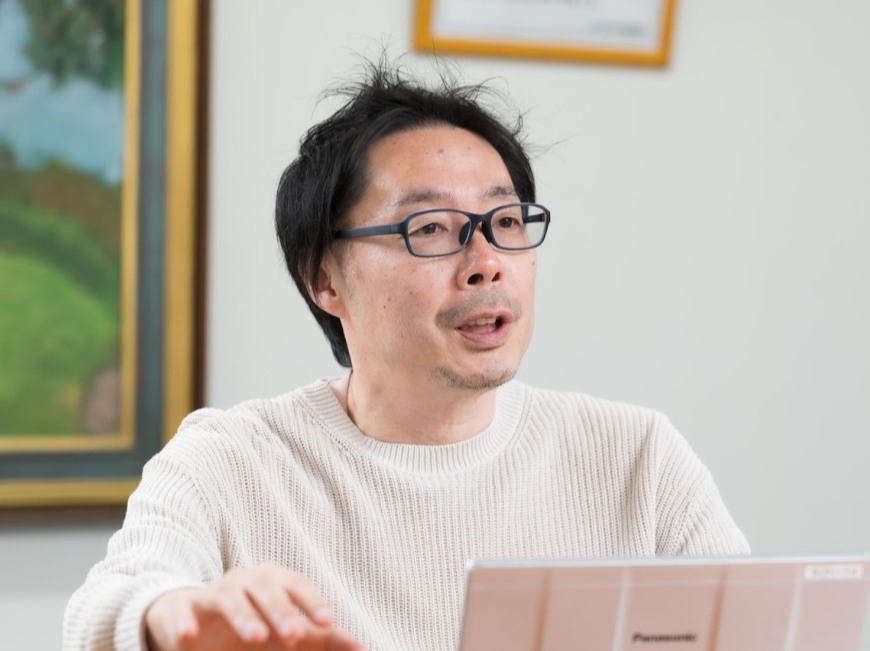