ギガキャスト、自走式組み立てライン…トヨタが公開した新生産技術の全容
積み上げてきた力、次世代に
トヨタ自動車がモノづくり革新に挑んでいる。このほど、大物部品を一体成形するギガキャストや、自走式の車両組み立てライン、次世代電池の試作ラインといった新たな生産技術を初公開した。キーワードは投資や生産準備期間などを半減する生産方式「BEVハーフ」と、デジタル技術を活用した「技能の継承」だ。新興の電気自動車(EV)メーカーが常識にとらわれない生産を実現する中、積み上げてきたモノづくり力を次世代でも強みにできるか。現場の取り組みが本格化している。(編集委員・政年佐貴恵)
投資・生産準備期間半減
溶けたアルミニウムが流し込まれた、高さ6メートル、長さ15メートルほどのダイカスト装置。3分ほどで、両側に開いた型から厚さ4ミリメートルのリアフェンダー部の一体成形部品が取り出された。トヨタが明知工場(愛知県みよし市)で実証を進めているギガキャストの試作品だ。
特徴は、金型を分割して汎用部と専用部に分け、部品に応じて必要な型だけを交換する方式だ。少ない型の数で幅広い部品の成形に対応できると同時に、従来は24時間かかっていた型交換の時間を20分に短縮。担当者は「高度な寸法管理や設計技術が必要で、ほかにやっているところはない」と自負する。現状の装置の型締め力は4000トンだが、さらなる大型化や薄肉化も検討している。
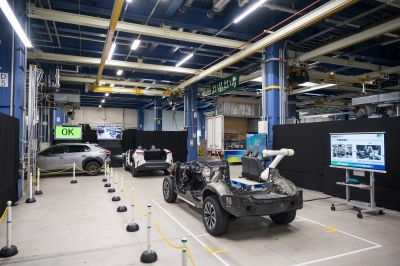
このほか元町工場(同豊田市)では、工場内に設置した6台のカメラで周辺を認識し自動走行するプラットフォーム(車台)に、シートなどを組み付ける様子を公開。完成した車を車両保管場所に自動で運ぶ新型ロボット「VLR」も披露した。9月から運用しており、2024年にはロボット台数を現状の1台から10台に増やし、同工場の全完成車両の運搬に広げる計画だ。
貞宝工場(同)では、全固体電池の電極材料を「からくり」の原理を使って高精度に積層する治具や、バイポーラ型リン酸鉄リチウムイオン(LFP)電池の電極塗布工程を公開。製造領域を統括する新郷和晃執行役員は、全固体電池開発の進捗(しんちょく)について「成分開発のめどはついている。量産化には安定して安価に作るなど課題は多いが、5合目くらいには来ているのではないか」との認識を示す。
デジタル技術・TPS活用
「生産部門のやり方を大きく変えることもいとわない」。新郷執行役員は力を込める。危機感の背景には、新興自動車メーカーの参入による競争激化がある。特にコストが高く収益化に課題のあるEVを中心に、より効率良く開発・生産し、スピーディーに良い製品を投入する必要性が高まっている。「我々は当たり前のように既存の設備で車を作るが、EV専業メーカーが驚くような作り方をしてきている」(新郷執行役員)。対抗するには、生産技術革新を速める必要がある。その土台として重視するのが、デジタル技術とトヨタ生産方式(TPS)の活用だ。
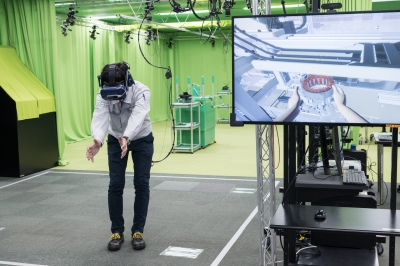
例えば貞宝工場で生産設備の製作を手がける部隊では、デジタル空間上に設備の3次元モデルを再現し、設計や製造、設備を使う作業者らが同時に確認できる仕組みを構築。ギガキャストでは型に流したアルミニウムの挙動や固まり方などを解析する、独自開発のソフトを活用している。30年来の鋳造ノウハウを注ぎ込んだ「秘伝のタレ」(担当者)だ。
こうしたデジタル技術を活用して作ったリアルの設備や製品のデータを、再びデジタルにフィードバックし、さらなる改良につなげる。近藤禎人モノづくり開発センター長は「現場のノウハウをデジタルに落とし込み、それをさらに改善して現場に落とし込む繰り返しが重要だ」と説く。これはまさに改善で技能を高めるTPSのやり方。また、高い技能者でなければデジタルへの反映もできないという。こうした理由から人材育成にも重きを置いており、高技能者の技術を伝承するためのデジタルツールの導入も始めた。
新郷執行役員は「トヨタの技でモノづくりの未来を変える」と意気込む。今回公開された生産技術の多くは、26年に投入予定の次世代EVで導入される見通し。生産現場の風景がどこまで変わり、競争力を発揮するかが注目される。