コロナ禍にロボット業界は進化する! 産学で開発と人材育成 基盤を整える機会に
新型コロナウイルスがロボットの開発や人材育成基盤を揺るがしている。大学や高等専門学校での研究が停滞し、実際に手を動かして学ぶ活動が難しくなっている。ロボットはハードとソフトのすり合わせが技術の難しさであり、この蓄積が技術者の強みだ。開発も人材育成も現場や現物に縛られていたが、シミュレーションや遠隔技術を活用し知見を共有する動きが始まっている。産学連携で取り組めば、開発や人材育成の新潮流になるかもしれない。
(取材・小寺貴之)現場で悩み、その経験が強みに
「シミュレーションだけではできることが限られる。すり合わせや調整は実機が前提」と神戸大学の横小路泰義教授は説明する。ソフトウエアは自宅でも開発できるが、機体開発やハードウエアとのインテグレーションは従来、研究室に集まって行われてきた。だが、コロナ禍が一旦落ち着き、大学の研究が再開された後も、できる限り接触頻度を抑えるなど、長期間制約を受けることが避けられそうにない。
そのため2020年度はシミュレーションや人工知能(AI)処理の情報技術や、センサーやアクチュエーターなどの要素技術を研究する学生が増えると想定される。シミュレーションで実機を再現する「デジタルツイン」や、デジタルツインなどを利用して開発と運用を高度化する「サイバーフィジカルシステム(CPS)」が研究のトレンドになっている。
ただ技術のインテグレーションこそがロボット開発の難しさであり、技術者としての強みになる。実機でのすり合わせは不可欠。そこでできるだけ現場での作業を減らし、遠隔で効率的に開発する工夫が模索されている。
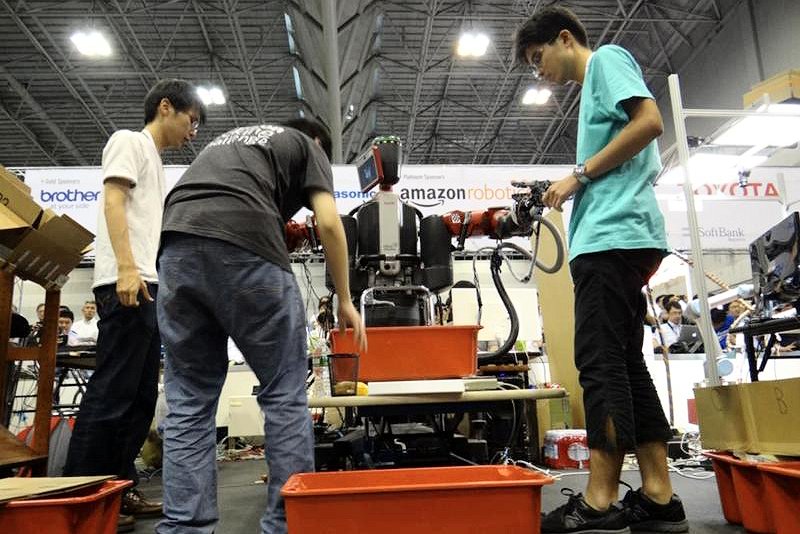
サイバーコンテスト、人材育成を継続させる国際連携
例えばロボカップ日本委員会(岡田浩之会長=玉川大学教授)は遠隔で参加する技術競技会を立ち上げる。ソフトを競うシミュレーション競技に加えて、遠隔の実機競技も計画中だ。標準プラットフォームとなる機体に、各大学が開発したソフトをダウンロードして技を競う。競技者が会場に集まらないため、大会の運営体制を最小限に抑えられる。同委員会の岡田会長は「日本で機体が動かせない場合はフランスの機体を使うなど、競技会場を世界に分散させて補い合える」と説明する。
トヨタ自動車の生活支援ロボット「HSR」などの標準機は、シミュレーションなどの開発環境も提供している。開発した技術はチーム間で共有しやすい。標準機は開発の効率を上げるための方策だが、競技会運営や人材育成にも有効だ
。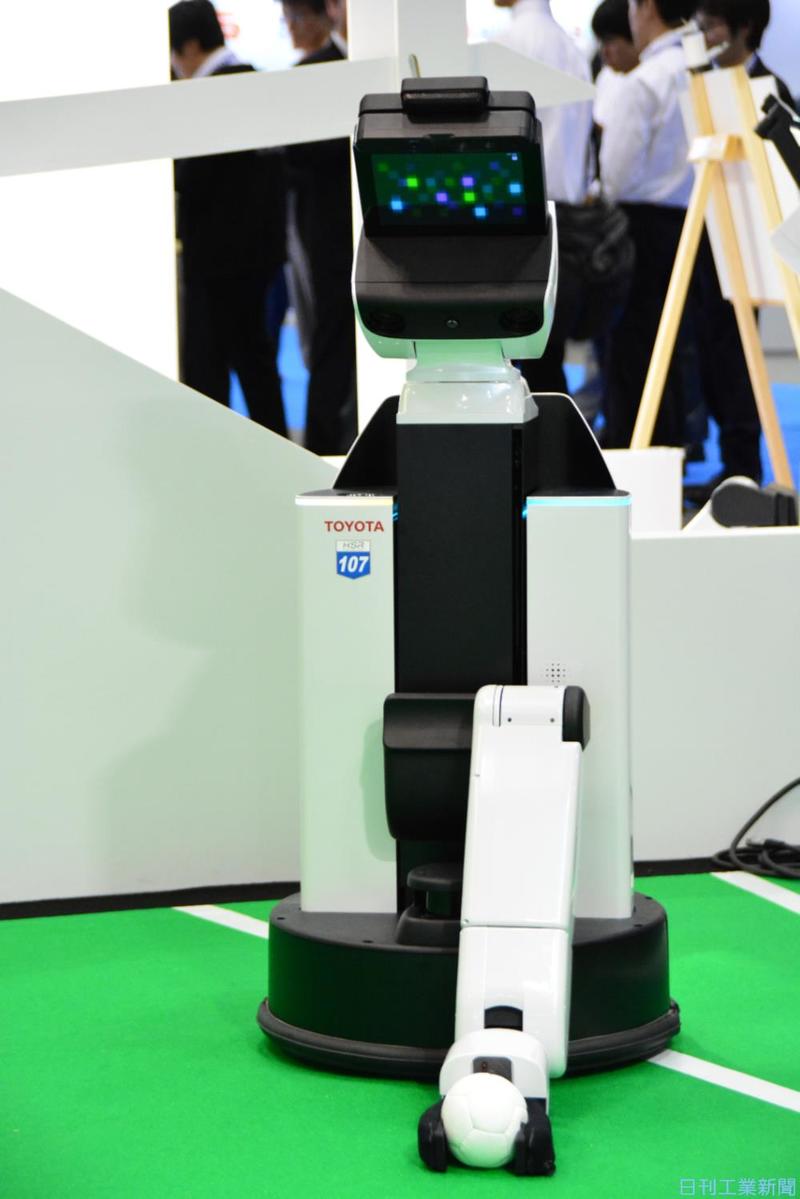
生活支援やサービス分野のロボット研究は、人との対話や高度な認識などの知能化に主眼を置いている背景もある。スマートフォンとスマホ用アプリケーション(応用ソフト)のように、ハードの開発負荷を抑えつつ多様なアプリを実現する上でシミュレーションなどの開発環境は有効だ。
今後はロボット本体に限らず、室内に配置したカメラなどIoT(モノのインターネット)機器にも標準プラットフォームが拡張されていくと期待される。現場に配置したセンサーからロボットを確認して動作の修正や、シンプルに遠隔から稼働状況の監視などもできる。
岡田会長は「学生は家でソフトを開発し、研究室の機体を動かして遠隔で検証する。ただ不具合があると機体のリセットボタンを誰かが押す必要がある」という。遠隔再起動など、遠隔を前提とした環境整備が進めば、研究室に集まらなくても研究を続けられる。
産業界 現場・現物の制約課題 体制構築急ぐ
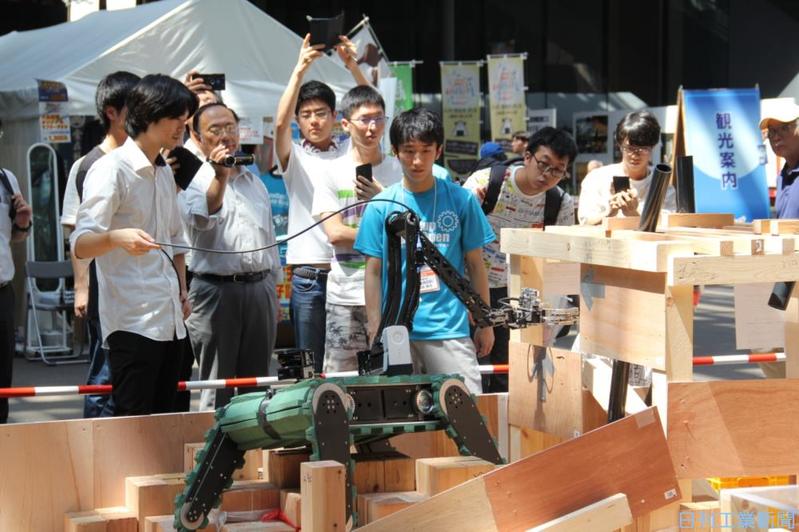
産業界からは大学での人材育成が停滞し、研究分野が従来よりも偏るのではないかと懸念する声も出ている。もともと広範な技術のインテグレーションを経験させられる研究室はそう多くない。仮に遠隔で知見を共有し、得意分野を補い合う環境が整うと技術の底上げが期待できる。
産業界にとっても現場・現物の制約は課題の一つだ。コロナ禍以前も設計や据え付け、保守など、ロボットメーカーやシステムインテグレーター(SIer)の技術者は顧客の現場に事あるごとに駆けつけていた。深刻な人手不足に加え、コロナ禍で人との接触頻度を極力減らす働き方が求められるようになった。
コロナ禍が長引くなら、接触頻度を減らしてでも事業を続けられる体制の検討も必要になる。遠隔だけですべてが完結することはないが、業界の構造的な問題に向き合うチャンスともいえる。
FA・ロボットシステムインテグレータ協会の久保田和雄会長(三明機工〈静岡市清水区〉社長)は「人口減少で自動化の需要は大きい。協会としてコロナ禍で会社をたたむ状況は防ぎたい」という。同協会の調べでは会員企業の8割以上にマイナスの影響があった。営業や装置の据え付けなどの現場作業が停滞し、開発済み装置の売上代金が回収できていない事例が目立つ。
光る先行事例、現場の知恵をインテグレーション
三明機工では仮想現実(VR)で生産ラインやロボットシステムを確認するシステムを持つ。ヘッド・マウント・ディスプレー(HMD)を装着すれば実寸大の現場に入って、ロボットの動作や人の作業性を検証できる。 企画や保守、改善の際に3次元(3D)モデルに改良を反映させて差分を確認できる。何度も通って現場で試行錯誤するよりも、構想から設置まで垂直的にシステムを立ち上げるための仕組みだ。西田真幸部長は「現場の熱や照度の変化を撮る技術があれば設計に生かせる」と指摘する。
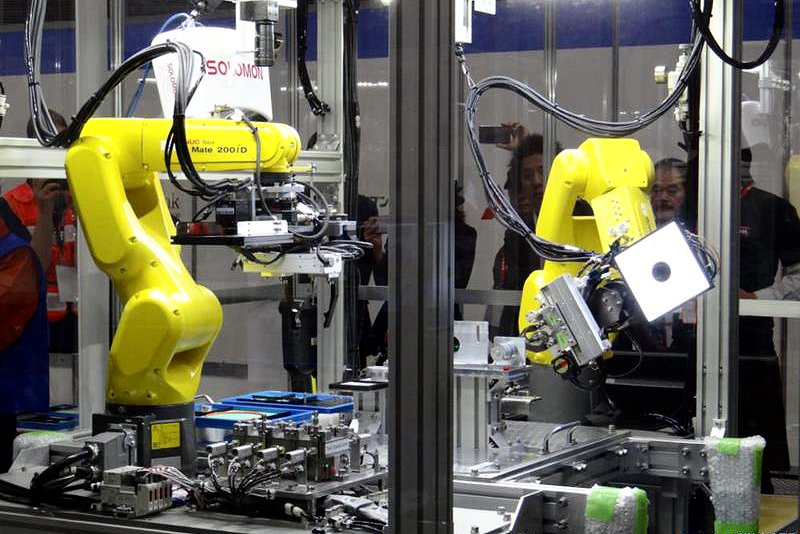
現場確認の遠隔化も進む。オフィスエフエイ・コム(栃木県小山市)は、18年にFA.Regalo(同)を立ち上げ、ビデオ会議システムで現場のスペースや前後工程の状況、作業者の動作フローなどを確認し、見積もり提案するサービスを展開している。青木伸輔代表は「システムインテグレーターのノウハウで商社の営業マンをサポートする」と説明する。
開発の遠隔化には3D図面やシミュレーション技術、製造技術の知見を統合する必要がある。従来はそれぞれがバラバラに存在し、技術者が実機を触りながらインテグレーションしてきた。例えば生産装置の改善や故障履歴は、装置担当者の改善実績として保存され、新ラインの設計時に参照されないこともある。図面も製造ノウハウもデータになっていても、それぞれがひも付いていない。
オフィスエフエイ・コムの飯野英城社長は「複数人で設計し開発するプラットフォームが必要」と指摘する。開発時は各技術者の設計物がシミュレーション上で動き、同時並行して改良を加える。運用時はセンサーで稼働状態のデータを取り、シミュレーションに反映させて改善策を練る。
まだ大手製造業でも模索している段階だ。仮にこうした開発基盤を産学で共有できれば、開発と人材育成の高度化を進める機会になる。コロナ禍で顕在化した課題の先には、業界がより強くなるヒントがあるのかもしれない。
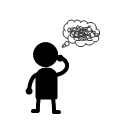