自動車の軽量化を考える(5)高い耐熱性、PEEKに熱視線
耐熱性が最高水準のスーパーエンジニアリングプラスチック。高級素材にもスポットライト当たる
自動車用軽量部材として浸透している樹脂。熱可塑性樹脂の中で耐熱性などが最高水準にあるスーパーエンジニアリングプラスチックと呼ばれる高級素材にもスポットライトが当たる。スーパーエンプラの一種、ポリエーテルエーテルケトン(PEEK)は価格面や成形加工の難しさから採用を敬遠されていたこともあったが、車体軽量化を追い風に自動車用途を開拓しようと英国やドイツの化学メーカーが日本市場に熱視線を送る。
樹脂の強みは軽量であるほか、部分的に厚みを持たせるなど多様な形状にできることだ。樹脂はポリプロピレンや塩化ビニール樹脂など汎用樹脂、ポリアミドなど耐熱性や機械強度に優れるエンジニアリングプラスチック、そして耐熱性や機械強度、耐薬品性がさらに高いスーパーエンプラに分けられている。
【万能性素材】
PEEKの魅力の一つはグレード(品種)によっては300度C超の環境で使えるという耐熱性の高さだ。最大手の英ビクトレックスの日本法人ビクトレックスジャパン(東京都港区)の神成貴晴代表取締役は「PEEKはまんべんなく優れている」のも強みと話す。耐熱性に優れた樹脂はほかにもあるが、摺(しゅう)動性や耐薬品性など全体の特性で見ても欠点があまりなく、万能性の高い素材だという。
【課題を解決】
同社は日本の自動車メーカーが世界に先行して開発しているハイブリッド車や電気自動車、燃料電池車に注目する。これらの車では多く搭載される電気系部品の軽量化が課題。モーターの高出力化などに伴って耐熱性をはじめとして各種の要求が厳しくなるにつれ、「金属の特性とギャップが小さいPEEKが受け入れられやすくなる」と神成氏は期待する。
同じくPEEKの製造販売を手がける独エボニック。日本の合弁会社ダイセル・エボニック(東京都新宿区)の沢田克己氏は、「トランスミッションは宝の山」と注目する。ハイブリッド車のモーター走行時は静かなため、従来は気にならなかったトランスミッションの摩擦音などを抑える必要が生じた。剛性は高いが表面は硬すぎず、摺動性も高いPEEKをギア部品などに使えば静音性が改善される。加えて吸音材を削減できるため、コストを抑えつつ軽量化も果たせる。
【採用広がる】
とはいえ高級素材のPEEKは航空機や半導体製造装置といった用途の採用が中心。自動車での採用実績は継ぎ手部品やシール材、ブレーキシステムのピンといった小型部品が大半だ。同じスーパーエンプラでもポリフェニレンサルファイド(PPS)は価格がこなれてきたことや流動性が高くて成形しやすいといった特徴から、エンジン周辺や電装品の筐(きょう)体として既に採用が広がっている。またポリアミドなどエンプラでも耐熱性や耐薬品性を高めたものが相次いで開発されている。
価格面でのハンディとどう向き合うか。その答えの一つとして各社は成形技術の開発に力を入れる。ビクトレックスは金属とPEEKの異材接合技術、金属や他の樹脂にPEEKを塗工する技術の開発を進めている。ダイセル・エボニックも「さまざまな加工法に挑戦する」(沢田氏)方針で、日本の装置メーカーや成形加工業と連携して複合成形やフィルム化などの加工法を開発している。これらの加工法を使うことで、例えば部品同士が接触するギアの歯の表面などに限定してPEEKを採用すれば、使用量を減らしてコストの増加を抑えられる。コストにひときわ敏感な自動車業界から受け入れられるため、素材メーカー自らが成形加工技術の確立に精を出す。
樹脂の強みは軽量であるほか、部分的に厚みを持たせるなど多様な形状にできることだ。樹脂はポリプロピレンや塩化ビニール樹脂など汎用樹脂、ポリアミドなど耐熱性や機械強度に優れるエンジニアリングプラスチック、そして耐熱性や機械強度、耐薬品性がさらに高いスーパーエンプラに分けられている。
【万能性素材】
PEEKの魅力の一つはグレード(品種)によっては300度C超の環境で使えるという耐熱性の高さだ。最大手の英ビクトレックスの日本法人ビクトレックスジャパン(東京都港区)の神成貴晴代表取締役は「PEEKはまんべんなく優れている」のも強みと話す。耐熱性に優れた樹脂はほかにもあるが、摺(しゅう)動性や耐薬品性など全体の特性で見ても欠点があまりなく、万能性の高い素材だという。
【課題を解決】
同社は日本の自動車メーカーが世界に先行して開発しているハイブリッド車や電気自動車、燃料電池車に注目する。これらの車では多く搭載される電気系部品の軽量化が課題。モーターの高出力化などに伴って耐熱性をはじめとして各種の要求が厳しくなるにつれ、「金属の特性とギャップが小さいPEEKが受け入れられやすくなる」と神成氏は期待する。
同じくPEEKの製造販売を手がける独エボニック。日本の合弁会社ダイセル・エボニック(東京都新宿区)の沢田克己氏は、「トランスミッションは宝の山」と注目する。ハイブリッド車のモーター走行時は静かなため、従来は気にならなかったトランスミッションの摩擦音などを抑える必要が生じた。剛性は高いが表面は硬すぎず、摺動性も高いPEEKをギア部品などに使えば静音性が改善される。加えて吸音材を削減できるため、コストを抑えつつ軽量化も果たせる。
【採用広がる】
とはいえ高級素材のPEEKは航空機や半導体製造装置といった用途の採用が中心。自動車での採用実績は継ぎ手部品やシール材、ブレーキシステムのピンといった小型部品が大半だ。同じスーパーエンプラでもポリフェニレンサルファイド(PPS)は価格がこなれてきたことや流動性が高くて成形しやすいといった特徴から、エンジン周辺や電装品の筐(きょう)体として既に採用が広がっている。またポリアミドなどエンプラでも耐熱性や耐薬品性を高めたものが相次いで開発されている。
価格面でのハンディとどう向き合うか。その答えの一つとして各社は成形技術の開発に力を入れる。ビクトレックスは金属とPEEKの異材接合技術、金属や他の樹脂にPEEKを塗工する技術の開発を進めている。ダイセル・エボニックも「さまざまな加工法に挑戦する」(沢田氏)方針で、日本の装置メーカーや成形加工業と連携して複合成形やフィルム化などの加工法を開発している。これらの加工法を使うことで、例えば部品同士が接触するギアの歯の表面などに限定してPEEKを採用すれば、使用量を減らしてコストの増加を抑えられる。コストにひときわ敏感な自動車業界から受け入れられるため、素材メーカー自らが成形加工技術の確立に精を出す。
日刊工業新聞2014年09月22日 モノづくり面
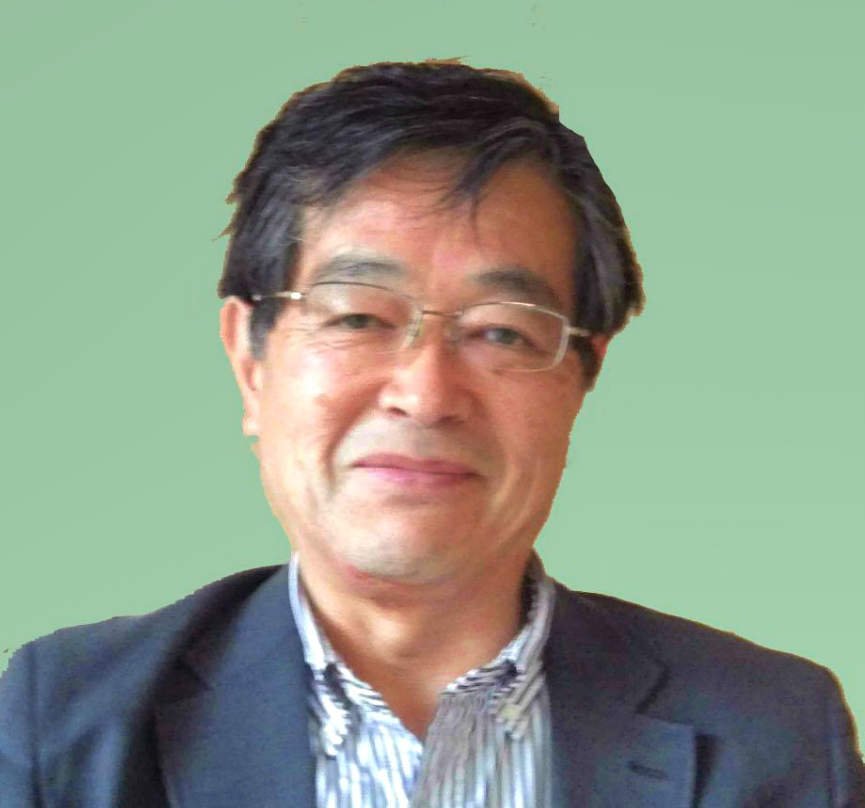